- Accueil
- Blog
- Solution minérale
- L'extraction du minerai de fer : Le processus essentiel pour la production d'acier
Qu'est-ce que le minerai de fer ?
Le minerai de fer est une substance minérale contenant des métaux et capable de produire du fer métallique (Fe) lorsqu'elle est chauffée avec un réducteur. C'est le principal matériau utilisé pour produire de l'acier, et 98% de minerai de fer sont utilisées à cette fin. La magnétite (Fe3O4), l'hématite (Fe2O3), la goethite, la limonite ou la sidérite sont les minerais de fer que l'on trouve habituellement, et l'hématite et le cuivre sont les minerais les plus couramment exploités. Les météorites de fer contiennent généralement du nickel et on pense qu'elles proviennent de corps accrétés de 1 000 km de diamètre ou plus. Ces dernières années, la production mondiale de minerai de fer a augmenté régulièrement pour répondre à la demande croissante d'acier, la société minière brésilienne Vale étant le plus grand producteur mondial. Selon l'United States Geological Survey (USGS), la production mondiale de minerai de fer en 2021 sera d'environ 2,3 milliards de tonnes, avec Vale en tête.
Le minerai de fer est obtenu par extraction à ciel ouvert ou souterraine et passe ensuite au traitement, qui comprend le concassage, le criblage et l'enrichissement afin d'augmenter sa teneur en fer. Le minerai est mélangé et homogénéisé avant d'être transporté pour l'exportation.
Où trouver du minerai de fer ?
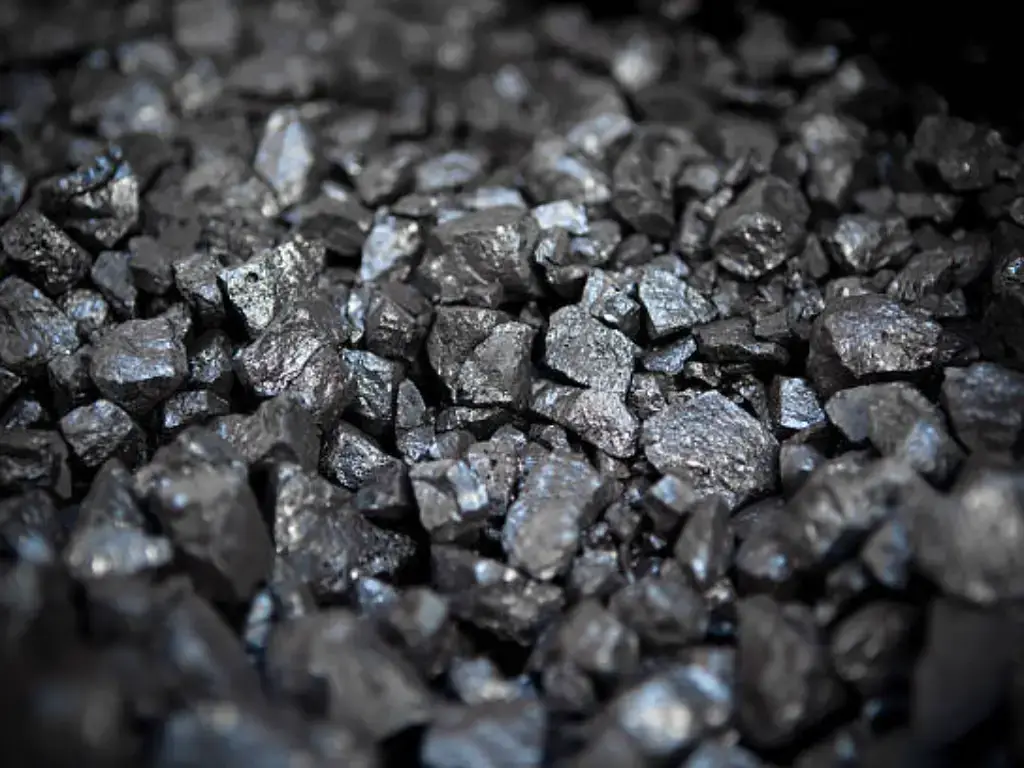
Les gisements de minerai de fer se trouvent dans diverses régions du monde, les plus grands producteurs étant l'Australie, le Brésil, la Chine et l'Inde. D'importantes mines de fer sont également situées aux États-Unis, au Canada, en Russie et en Afrique du Sud. Aux États-Unis, la majeure partie de l'exploitation du minerai de fer a lieu dans la chaîne de Mesabi, située dans le Minnesota et le Michigan, près des Grands Lacs.
L'Australie est le premier producteur mondial de minerai de fer, l'Australie occidentale représentant plus de 90% de la production du pays. La région de Pilbara, en Australie occidentale, abrite certaines des plus grandes mines de fer du monde, exploitées par de grandes sociétés telles que Rio Tinto, BHP et Fortescue Metals Group. Le Brésil, deuxième producteur mondial, possède ses principales mines de fer dans la région de Carajás, dans l'État de Pará.
Types de minerai de fer
L'hématite, la magnétite et la limonite sont les trois principaux types de minerai de fer, chacun ayant des propriétés uniques et un rôle propre dans les processus de fabrication de l'acier.
Hématite
L'hématite est le minerai de fer le plus courant et le plus largement exploité en raison de sa teneur élevée en fer (60-70%) qui le rend facile à traiter. De couleur rouge-noir, ce minerai se trouve dans les roches sédimentaires et a une texture relativement molle, ce qui facilite son broyage et son concassage. L'hématite est le minerai le plus apprécié pour la production d'acier car, lorsqu'il est réduit en fer métallique, il nécessite moins d'énergie que les autres minerais. La teneur élevée en fer et le faible taux d'impuretés de l'hématite contribuent certainement à des opérations plus douces et de meilleure qualité dans les hauts fourneaux et, par conséquent, à des produits sidérurgiques de meilleure qualité.
Magnétite
La magnétite, bien que moins courante que l'hématite, contient le pourcentage de fer le plus élevé, avec jusqu'à 72% de fer. Ce minéral noir et magnétique se forme dans les roches métamorphiques et ignées ; il est donc difficile à extraire et à traiter. Néanmoins, les propriétés magnétiques de la magnétite conviennent mieux à la séparation des minéraux de la gangue, ce qui est facilité par les méthodes de séparation magnétique. La magnétite est plus riche en fer que les autres minéraux. Elle donne donc un concentré de qualité supérieure qui est important pour la production d'acier. La densité plus élevée de la magnétite permet de l'utiliser dans la séparation en milieu lourd, l'une des méthodes utilisées pour améliorer les minerais de fer à faible teneur.
Limonite
La limonite, également appelée "minerai de fer de tourbière", est un minerai de faible qualité dont la couleur brun-jaune est due à ses impuretés. Elle est le sous-produit de l'altération d'autres minéraux riches en fer et contient environ 20-30% de fer. Néanmoins, la limonite a une valeur économique inférieure à celle de l'hématite et de la magnétite en raison de sa moindre teneur en fer et de la présence d'impuretés telles que la silice et l'alumine ; cependant, elle est utilisée depuis longtemps dans la production d'acier. La limonite est valorisée par des techniques d'enrichissement telles que le lavage, le jigging et le processus de frittage avant d'être utilisée comme matière première dans les hauts fourneaux. En fait, la limonite peut être utilisée comme minerai secondaire à mélanger aux minerais principaux pour obtenir la teneur en fer et les niveaux d'impuretés requis.
La sélection du minerai de fer pour la production d'acier repose sur différents aspects, notamment la teneur en fer, les niveaux d'impureté, les exigences en matière de traitement et la rentabilité. L'hématite est la forme la plus utilisée car elle est relativement courante, contient une forte teneur en fer et n'est pas difficile à traiter. La magnétite est peut-être plus dure dans la nature, mais elle est de plus en plus utilisée comme matière première dans la production d'acier pour produire des concentrés de qualité supérieure en raison de sa teneur en fer plus élevée. La limonite n'est peut-être pas le minerai le plus désirable, mais elle peut être utilisée dans la production d'acier lorsque c'est économiquement possible ou pour fournir un minerai de mélange pour les fours afin d'améliorer les performances et la qualité du produit.
Le processus d'extraction du minerai de fer
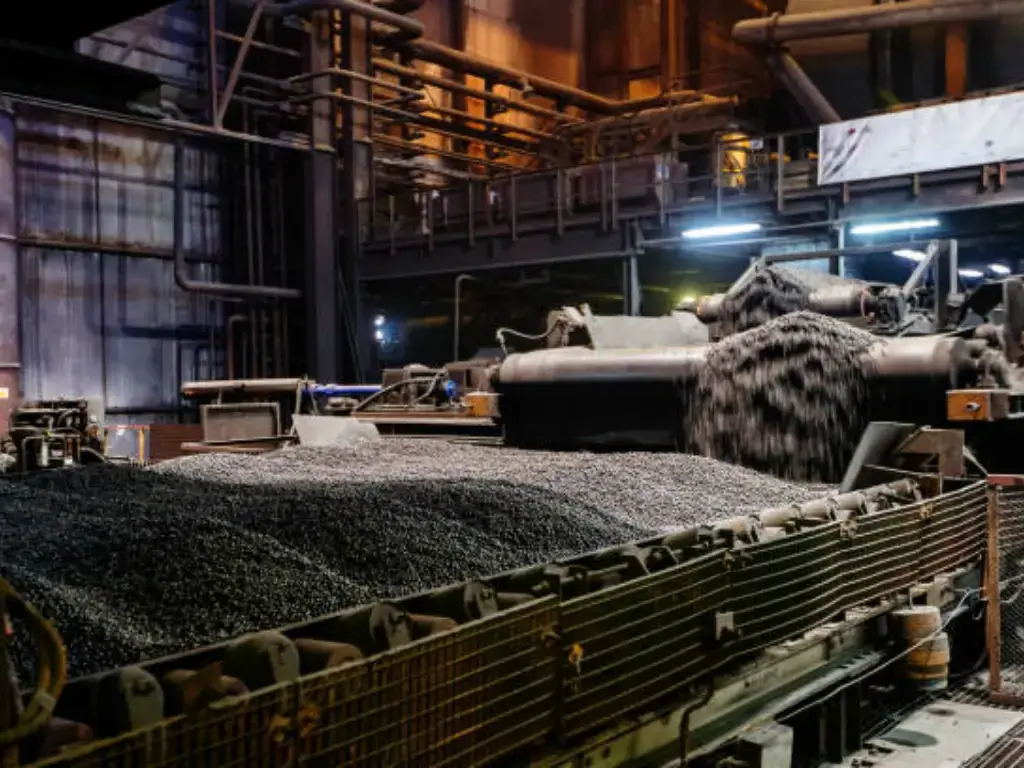
Étape 1:Exploration et sélection du site - Trouver de bons gisements
L'extraction du minerai de fer commence par le processus d'exploration et de sélection des sites. Les géologues et les ingénieurs miniers appliquent différentes techniques pour identifier les emplacements probables des gisements de minerai de fer, telles que les levés géophysiques, les levés aériens et les forages exploratoires. L'étude initiale prouve qu'un site est prometteur, avec des gisements potentiels dans des zones telles que la région des Grands Lacs. L'étape suivante consiste en une étude détaillée et en un échantillonnage visant à déterminer le volume et la qualité du gisement de minerai de fer.
Étape 2:Forage et dynamitage : Extraction du minerai de la terre
Une fois que le gisement de minerai de fer est exploitable, le processus minier consiste à extraire le minerai de la terre. La technique la plus utilisée est l'exploitation à ciel ouvert, qui consiste à forer et à dynamiter la roche et le sol en surface pour atteindre le gisement de minerai situé en dessous, dans des États comme le Minnesota et le Michigan, autour de la région du lac Supérieur. Une fois les morts-terrains enlevés, le minerai de fer est foré et dynamité pour en faire des morceaux plus petits qui peuvent être facilement transportés hors des mines.
Étape 3 : Transport - Expédition du minerai vers l'usine de traitement
Ensuite, le minerai est détaché par le dynamitage et les véhicules géants ou les bandes transporteuses l'amènent hors de la mine. Le minerai est transporté jusqu'à l'usine de traitement. Celle-ci peut être proche ou éloignée. Le minerai est transporté par camion, par train ou par bateau, le choix du mode de transport étant déterminé par la distance et l'emplacement. Le minerai doit être acheminé vers l'usine de manière efficace pour que le processus d'extraction du minerai de fer puisse être mené à bien.
Étape 4 : Concassage et broyage - Préparation du minerai pour la séparation
À l'usine, des machines appelées concasseurs réduisent le minerai en petits morceaux. Les premiers concasseurs sont concasseurs à mâchoires qui permettent de briser les plus gros morceaux. Ensuite, les broyeurs à cône le décomposer davantage. Enfin, les morceaux de minerai sont placés dans broyeurs à billes ou broyeurs à barres. Il s'agit de grands tambours en rotation contenant des billes ou des tiges d'acier. En tournant, ils broient le minerai en une fine poudre. Cette étape augmente la surface du minerai, ce qui permet de séparer plus facilement le fer lors de l'étape suivante.
Étape 5 : Séparation magnétique - Extraire le fer
Les aimants puissants attirent la fine poudre de minerai de fer. Les particules de fer sont attirées et prises par les aimants. Cette technique de séparation magnétique est efficace pour les minerais de haute qualité, tels que la magnétite. Un aimant est utilisé pour attirer les particules de fer magnétiques et les stériles sont éliminés. Ce processus permet d'obtenir une poudre de minerai de fer concentrée. Améliorez votre processus d'extraction du fer grâce à nos séparateur magnétique détaillée ici.
Étape 6 : Pelletisation - Le processus de production de boulettes de minerai de fer
Le minerai de fer concentré est ensuite mélangé à des liants, tels que l'argile bentonite, et transformé en petites boulettes de la taille d'une bille à l'aide d'un disque ou d'un tambour de granulation. Les boulettes sont ensuite durcies par cuisson dans un four à haute température (1 200-1 300°C). La granulation du minerai de fer permet un transport et une manutention plus efficaces, ainsi qu'une meilleure performance dans le haut fourneau pendant le processus de fabrication de l'acier.
Équipement pour l'extraction du fer
Equipement | Caractéristiques | Applications | Avantages |
---|---|---|---|
Appareils de forage | 1. forage rotatif ou à percussion - forage jusqu'à 60 mètres de profondeur 2. énergie hydraulique ou électrique 3. fonctionnement automatisé ou manuel | 1. Création de trous de mine dans les morts-terrains et le minerai de fer 2. convient aux mines de surface et aux mines souterraines 3. utilisé dans les forages d'exploration et de production | 1. forage efficace et précis 2. polyvalent pour différentes conditions d'exploitation minière 3. une productivité élevée et des coûts d'exploitation réduits |
Explosifs | 1.- ANFO (fuel-oil à base de nitrate d'ammonium) 2. les explosifs à émulsion 3. détonateurs électroniques ou non électriques 4. les techniques de dynamitage contrôlé | 1. Briser les morts-terrains et le minerai de fer 2. applicable dans les mines à ciel ouvert et souterraines 3. fragmentation de la roche pour faciliter l'excavation | 1) Explosion optimisée pour une meilleure fragmentation 2. sécurité accrue grâce à la détonation contrôlée 3. des solutions de dynamitage rentables et fiables |
Camions de transport | 1. camions à châssis rigide ou articulés 2. capacité de charge de 40 à 400 tonnes 3. options diesel ou électrique 4. fonctionnement autonome ou avec équipage | 1. transport du minerai de fer de la mine à l'usine de traitement 2. convient aux mines à ciel ouvert et aux mines à grande échelle .3.Opérations de transport en continu | 1. Capacité de charge élevée pour un transport efficace 2. conception robuste pour des conditions d'exploitation difficiles 3. des dispositifs de sécurité avancés et le confort de l'opérateur |
Concasseurs | 1. concasseurs à mâchoires, à cônes, giratoires ou à percussion 2. étapes de broyage primaire et secondaire 3. capacité et taux de réduction élevés 4. matériaux résistants à l'usure | 1.Réduction de la taille du minerai de fer pour traitement ultérieur 2. applicable à différents types de minerais de fer et à différentes duretés 3. intégration dans les circuits de broyage | 1. réduction efficace de la taille pour un traitement optimisé 2. composants durables pour une longue durée de vie 3. des conceptions personnalisables pour des propriétés de minerai spécifiques |
Broyeurs | 1. Broyeurs à boulets, à barres ou autogènes 2. procédés de broyage par voie humide ou sèche <br.3. classificateurs à haut rendement 4. systèmes de contrôle automatique | 1. broyage du minerai de fer en fines particules 2. Convient à l'hématite, à la magnétite et à d'autres minerais. 3 Préparation à la séparation magnétique ou à la granulation | 1. distribution cohérente et uniforme de la taille des particules 2. débit élevé et efficacité énergétique 3. réduction des coûts d'entretien et d'usure |
Séparateurs magnétiques | 1. séparateurs magnétiques à basse ou haute intensité 2. procédés de séparation par voie sèche ou humide 3. conception permanente ou électromagnétique 4. plusieurs étapes pour une meilleure récupération | 1. séparation des particules magnétiques de minerai de fer de la gangue 2. applicable aux minerais de magnétite et d'hématite 3. concentration et purification du minerai de fer | 1. des taux de récupération et des teneurs en concentrés élevés 2. élimination efficace des impuretés 3. s'adapter aux différentes caractéristiques du minerai et à la configuration de l'usine |
Machines de granulation | 1. granulateurs à disque ou à tambour 2. les processus de balisage et d'induration 3. systèmes d'ajout de liant 4. Contrôle des processus et automatisation | 1) Agglomération de fines de minerai de fer en boulettes 2. convient aux concentrés issus de la séparation magnétique 3. préparation au haut fourneau ou à la réduction directe | 1. taille et qualité constantes des granulés 2.Amélioration des propriétés de transport et de manutention 3. Amélioration de la performance et de l'efficacité des hauts-fourneaux |
Traitement du minerai de fer pour la production d'acier
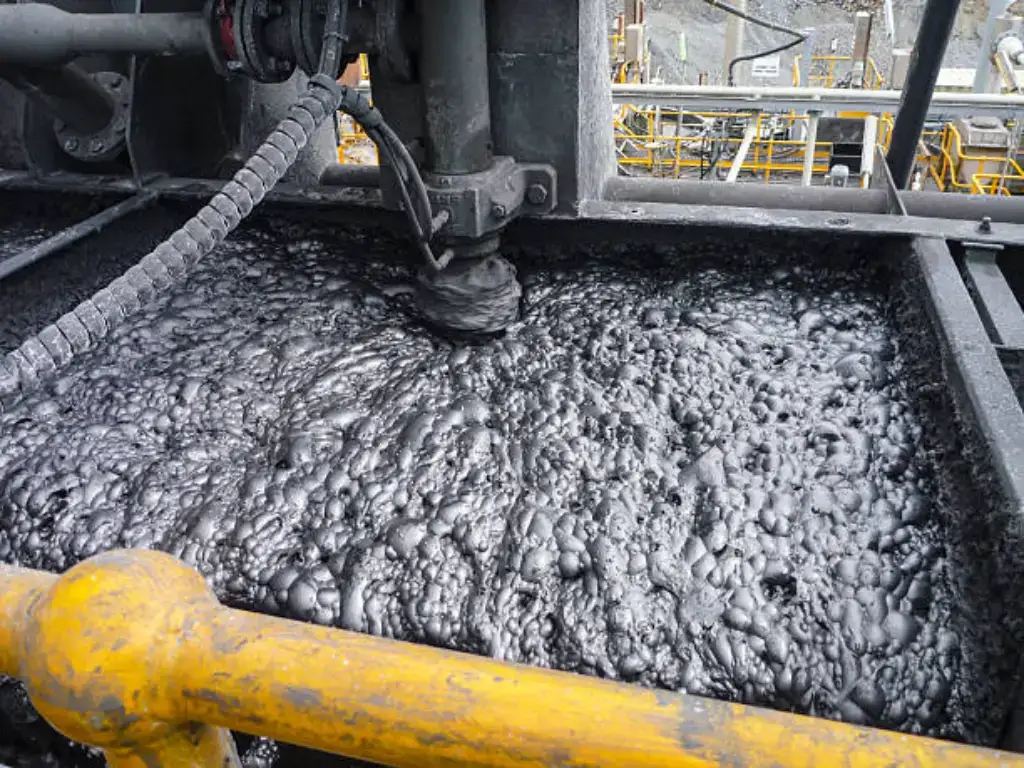
Les données sous-jacentes montrent que le minerai de fer extrait est principalement utilisé pour fabriquer de l'acier. Le minerai de fer est la principale matière première des usines sidérurgiques ; des tonnes de minerai de fer sont donc utilisées dans les usines de nombreux pays comme la Chine et le Canada. La première étape du processus est la production de fonte brute, à partir de laquelle le minerai de fer est converti dans le haut fourneau et se présente généralement sous la forme d'oxydes de fer. L'air chauffé est soufflé dans le bas du fourneau, ce qui contribue à la cokéfaction et à l'obtention de températures élevées (environ 1 500 °C). La production d'acier dépend entièrement des ressources naturelles. Par exemple, le minerai de fer, le charbon et le calcaire, qui sont utilisés pour fabriquer de l'acier employé dans divers secteurs.
C'est un mélange de minerai de fer, de coke et de calcaire dans le haut fourneau qui subit le changement et est réduit à l'état liquide, tombant au fond du four sous forme de fonte brute. Le calcaire agit comme un fondant, il purifie la fonte des impuretés. La fonte brute est prélevée au fond du haut fourneau et est soit coulée en lingots, soit transférée à l'état fondu dans le convertisseur basique à oxygène pour être transformée en acier.
Dans un four à oxygène de base, la fonte brute est combinée à de la ferraille et à d'autres additifs tels que le manganèse, le silicium et l'aluminium dans les proportions adéquates pour obtenir les propriétés souhaitées du produit sidérurgique. Un flux d'oxygène d'une grande pureté est insufflé dans le four. Par oxydation, les impuretés de la fonte brute sont transformées en laitier, qui est ensuite séparé de l'acier en fusion. L'acier est ensuite extrait du four, dans son état raffiné, et peut être coulé dans un certain nombre de formes telles que les brames, les blooms ou les billettes, qui sont les produits finaux.
Conclusion
L'extraction du minerai de fer a été identifiée comme un processus crucial qui fournit les matières premières nécessaires à la fabrication de l'acier, élément essentiel de l'infrastructure et de la technologie du monde moderne. Le processus d'extraction du minerai de fer comporte un certain nombre d'étapes, depuis la recherche de gisements propices à l'exploitation jusqu'au traitement du minerai sous une forme utilisable dans un haut-fourneau, ce qui nécessite des équipements et des connaissances spécialisés.
La demande mondiale d'acier étant toujours en hausse, l'importance de l'extraction du minerai de fer continuera à devenir plus évidente. Le développement de la technologie minière et de méthodes durables sera essentiel pour créer un approvisionnement régulier et consciencieux en minerai de fer afin de pouvoir répondre à la demande mondiale. En prenant conscience du processus d'extraction du minerai de fer et de son importance, nous pourrons prendre en considération le rôle important que joue ce produit fondamental dans le façonnement du monde.