- Accueil
- Blog
- Solution minérale
- Le guide ultime des étapes du traitement de l'or
Introduction
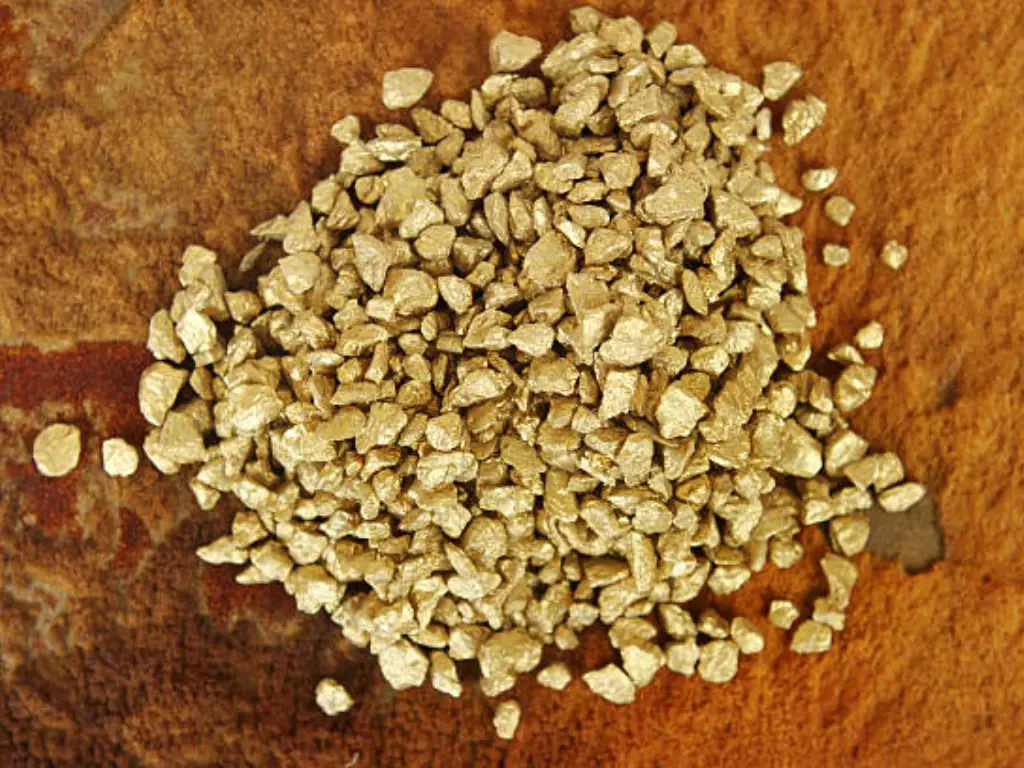
L'extraction de l'or peut être une industrie colossale, avec environ 3 500 tonnes d'or extraites chaque année. La publicité pour l'or représente plus de $200 milliards d'euros, et la demande ne cesse de croître. Les particuliers ont besoin d'or pour les parures, les spéculations et l'innovation. L'extraction de l'or donne du travail à des millions de personnes dans le monde. Elle contribue en outre au développement financier de nombreuses nations, en particulier en Afrique, en Amérique latine et en Asie.
Ce billet vous guidera à travers les étapes de pointe du traitement de l'or, de la prospection et de l'exploitation minière à l'affinage et à la création de lingots d'or. Vous comprendrez mieux les progrès de l'innovation et des capacités nécessaires pour extraire l'or du sol et le transformer en or immaculé et étincelant. Préparez-vous à découvrir le monde intéressant de la préparation de l'or !
Pays disposant d'abondantes ressources en or
Vous trouverez de l'or dans différents endroits du monde, mais certains pays en possèdent beaucoup plus que d'autres. La Chambre mondiale de l'or indique qu'en 2020, les pays qui ont livré le plus d'or sont la Chine, la Russie, l'Australie, les États-Unis et le Canada. Ces pays possèdent une partie des réserves d'or et exploitent l'or depuis longtemps, ce qui fait que leurs économies se développent et que la quantité d'or accessible dans le monde entier augmente.
Prospection et exploitation minière
Pour trouver de l'or, on utilise des méthodes telles que la cartographie géologique, l'échantillonnage géochimique et les études géophysiques. Lorsqu'un gisement d'or potentiel est découvert, des forages d'exploration sont effectués pour déterminer si l'exploitation est économiquement viable.
La méthode d'extraction utilisée dépend des caractéristiques du gisement d'or, telles que la profondeur, la forme et la teneur. Les techniques d'extraction à ciel ouvert, comme l'exploitation à ciel ouvert et l'exploitation des placers, sont utilisées pour les gisements peu profonds. Les techniques d'extraction souterraine, telles que l'extraction en roche dure et l'extraction par longue taille, sont utilisées pour les gisements profonds.
Le type de gisement d'or influe également sur la méthode d'extraction choisie. L'or peut se présenter sous différentes formes :
1. Or natif : L'or pur trouvé sous forme de pépites ou de paillettes.
2. Veines aurifères : Dépôts d'or minces, en forme de feuillets, dans les fissures de la roche.
3. Or disséminé : L'or dispersé dans une formation rocheuse, souvent sous forme de particules microscopiques.
Concassage et broyage
Le minerai d'or provenant directement de la mine est d'abord introduit dans un concasseur à mâchoires. Cette grosse machine réduit les énormes roches en morceaux plus petits, d'une taille d'environ 100 à 200 mm. Le minerai broyé passe ensuite dans le concasseur secondaire, qui est généralement un concasseur à cône. Là, il est encore plus concassé, jusqu'à une taille d'environ 10 à 50 mm. Parfois, ils utilisent une troisième étape de broyage avec un rouleau de broyage à haute pression (HPGR). Cela permet de rendre le minerai très fin, jusqu'à 5-20 mm, avant qu'il ne soit acheminé vers l'usine de traitement.
Vient ensuite le circuit de broyage. Le minerai concassé est mélangé à de l'eau pour former une boue, qui est un mélange liquide épais. La boue est ensuite broyée en une fine poudre à l'aide de broyeurs à boulets ou à barres. Ces broyeurs contiennent des billes ou des tiges en acier qui tournent autour du minerai et le broient jusqu'à ce que les morceaux aient une taille de 75 microns ou moins. Cette opération est très importante car elle permet de séparer les particules d'or de la roche environnante. Ils surveillent de près le processus de broyage pour s'assurer que les particules atteignent la taille parfaite pour les étapes suivantes de l'extraction de l'or.
Classification et concentration par gravité
Après le concassage et le broyage, la boue de minerai est classée à l'aide d'hydrocyclones. Ces machines séparent les particules en fonction de leur taille et de leur densité. Les particules de plus de 75 microns, qui ont tendance à être plus lourdes et à contenir plus d'or, sont envoyées dans le circuit de concentration par gravité. Les particules plus petites, inférieures à 75 microns, généralement plus légères et contenant moins d'or, passent à l'étape de traitement suivante.
Dans le circuit gravitaire, la boue est versée sur une table à secousses légèrement inclinée entre 3 et 5 degrés. Elle est secouée rapidement, environ 300 à 400 fois par minute. L'or étant beaucoup plus dense que la roche hôte (19,3 g/cm³ contre 2,5-3,0 g/cm³), les particules d'or lourdes s'enfoncent dans les crêtes de la table tandis que les déchets plus légers sont emportés. D'autres méthodes gravimétriques telles que les spirales et les concentrateurs centrifuges exploitent également cette différence de densité entre l'or (19,3 g/cm³) et la roche (2,5-3,0 g/cm³) pour séparer efficacement les particules d'or des déchets.
Épaississement et pré-oxydation
Après le circuit gravitaire, la boue de minerai est acheminée vers un réservoir épaississeur. Ce réservoir sépare les solides du liquide. Au fur et à mesure que la boue se dépose, les solides les plus lourds tombent au fond. L'eau claire est éliminée par le haut. La boue épaissie a maintenant un pourcentage plus élevé de solides, généralement de 50 à 60% en poids. Elle est pompée par le bas en vue d'un traitement ultérieur.
Certains minerais d'or sont des minerais réfractaires. Ils sont difficiles à traiter par une lixiviation classique au cyanure. Cela est dû au fait que les minéraux sulfurés encapsulent les particules d'or. Pour résoudre ce problème, une étape de pré-oxydation est nécessaire. Elle décompose les minéraux sulfurés et expose les particules d'or à l'étape de la lixiviation. Il existe plusieurs méthodes de pré-oxydation :
* Oxydation sous pression: La boue épaissie est pompée dans l'autoclave. Il est soumis à une pression élevée (20-50 bars) et à une température élevée (180-225°C) avec de l'oxygène. Cela accélère l'oxydation des minéraux sulfurés, libérant ainsi l'or encapsulé.
* Bio-oxydation: Des bactéries comme Thiobacillus ferrooxidans oxydent les minéraux sulfurés. Les bactéries sont ajoutées à une boue épaissie. Elles métabolisent les sulfures et libèrent des particules d'or. Se produit à 40-45°C et à un pH de 1,5-2,5.
* Torréfaction: La boue épaissie est séchée et chauffée à 500-700°C en présence d'air. La chaleur élevée provoque l'oxydation des sulfures, ce qui libère l'or. Mais le grillage est moins courant en raison des préoccupations liées à l'environnement et au coût de l'énergie.
Le choix de la méthode de préoxydation dépend des caractéristiques du minerai, de la technologie disponible et de facteurs économiques. Après la pré-oxydation, le minerai est prêt pour la lixiviation au cyanure.
Lixiviation au cyanure
La lixiviation au cyanure est le meilleur moyen d'extraire l'or du minerai. Au cours de cette étape, la boue de minerai pré-oxydée est mélangée à une faible solution de cyanure de sodium (environ 0,01-0,05% NaCN) dans de grandes cuves appelées cuves de lixiviation. Le cyanure réagit avec les particules d'or exposées pour former un complexe or-cyanure stable et soluble dans l'eau. La réaction se déroule comme suit :
4Au + 8NaCN + O2 + 2H2O → 4Na[Au(CN)2] + 4NaOH
Quelques facteurs influencent l'efficacité de la lixiviation :
Taille des particules: Les petites particules d'or ont une plus grande surface. La lixiviation est plus rapide.
Concentration de cyanure: Une plus grande quantité de cyanure peut accélérer la lixiviation. Mais une trop grande quantité de cyanure est coûteuse et néfaste pour l'environnement.
Niveau de pH: La fourchette idéale se situe entre 10,5 et 11,5. De la chaux est ajoutée pour maintenir le lisier alcalin.
Température: Des températures plus élevées, de l'ordre de 20 à 30°C, favorisent la lixiviation. Mais une chaleur excessive utilise plus de cyanure et entraîne des pertes d'or.
Oxygène: Il est essentiel de disposer d'une grande quantité d'oxygène. Il est ajouté en remuant la boue ou en injectant de l'air/du peroxyde.
L'ensemble du processus de lixiviation peut durer de 24 à 72 heures. Il dépend d'éléments tels que la taille des particules, la concentration de cyanure, le niveau de pH, la température et la disponibilité de l'oxygène, ainsi que des caractéristiques spécifiques du minerai lui-même. Une fois la lixiviation achevée, la solution de départ contenant de l'or est séparée des déchets solides (appelés résidus). Cela se fait par décantation ou filtration à contre-courant. La solution prégnante passe ensuite à l'étape de récupération de l'or. Quant aux résidus, ils sont soit stockés dans une installation spéciale, soit traités pour éliminer les restes de cyanure avant d'être éliminés de manière appropriée.
Adsorption et élution
La solution de lixiviation au cyanure contenant le complexe or-cyanure dissous passe dans des colonnes remplies de charbon actif. Le charbon actif est très efficace pour adsorber sélectivement le complexe or-cyanure de la solution. Au fur et à mesure que la solution prête traverse les colonnes, l'or se colle progressivement à la surface du charbon actif, tandis que la solution qui sort de l'autre côté est maintenant stérile (sans or).
Une fois que le charbon actif est chargé d'or, il est retiré des colonnes d'adsorption et subit un processus appelé élution pour éliminer l'or. Le charbon chargé est traité avec une solution caustique chaude (90-120°C) contenant 1-2% d'hydroxyde de sodium (NaOH) et 0,1-0,2% de cyanure (NaCN). Cette solution d'éluat élimine efficacement l'or du charbon actif, produisant une solution d'or de haute qualité. Le charbon décapé est ensuite réactivé en le chauffant dans un four à 600-800°C avant d'être renvoyé dans le circuit d'adsorption pour être réutilisé.
L'électro-extraction et la fusion
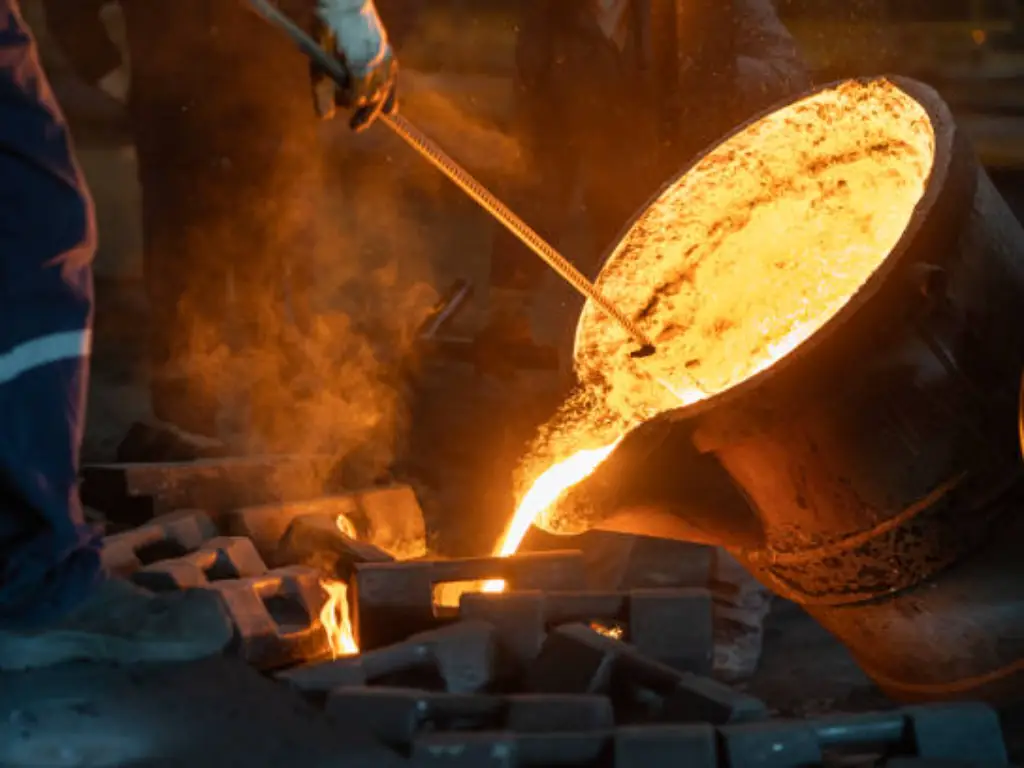
La solution d'or de haute qualité issue de l'élution est acheminée vers les cellules d'extraction électrolytique. Il s'agit de conteneurs spéciaux dans lesquels un courant électrique fait adhérer l'or à des cathodes faites de laine d'acier ou de mailles d'acier inoxydable. Les ions d'or se transforment en or métallique et se déposent sur les cathodes.
De temps en temps, les cathodes plaquées or sont retirées des cellules d'électrolyse et la boue aurifère est raclée, filtrée et séchée.
Ensuite, la boue d'or séchée est introduite dans un four de fusion chauffé à plus de 1 064 °C - le point de fusion de l'or. À cette température, l'or fond et se sépare des impuretés restantes, comme l'argent ou le cuivre. L'or fondu est coulé dans des moules pour fabriquer des barres de doré d'une pureté d'environ 90-95%.
Ces barres d'or sont ensuite envoyées dans une raffinerie. Elles y seront encore purifiées jusqu'à ce qu'elles atteignent le niveau de pureté souhaité, généralement 99,99% ou plus. L'or est alors prêt à être vendu ou transformé en produits.
Raffinage
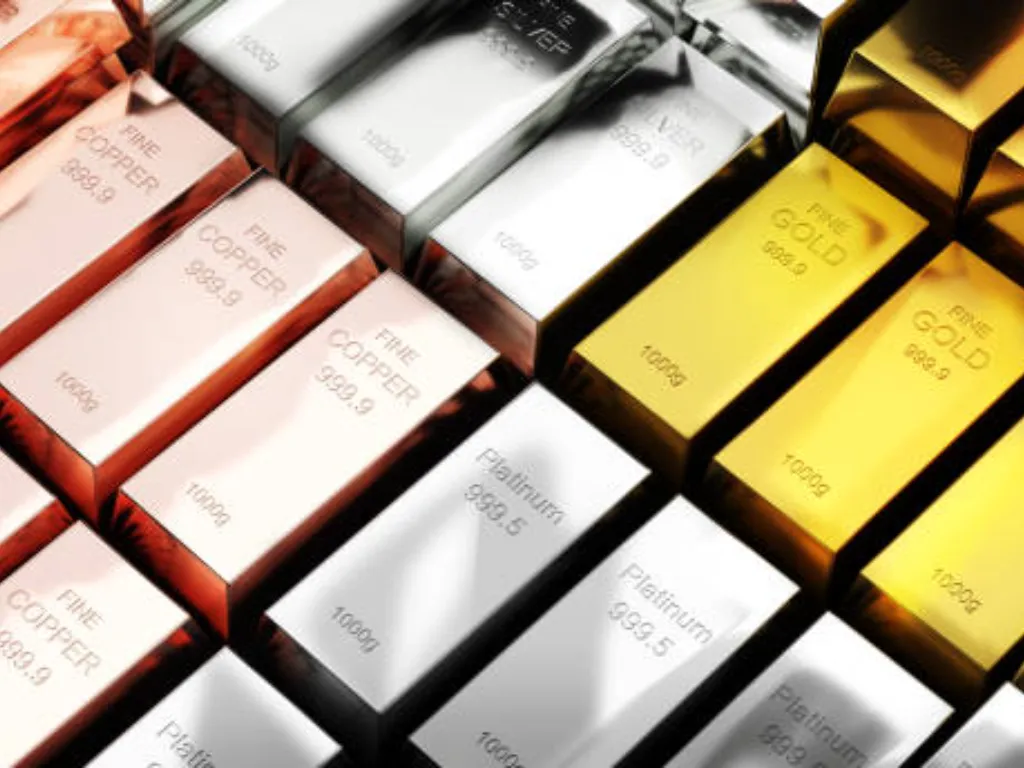
Les barres d'or doré issues de l'étape de fusion subissent un affinage supplémentaire pour atteindre le niveau de pureté souhaité, généralement 99,99% ou plus. Une méthode d'affinage courante est la chloration, qui consiste à faire fondre les barres d'or doré et à faire barboter du chlore gazeux dans le métal en fusion. Le chlore réagit avec les impuretés telles que l'argent, formant des composés chlorés qui flottent à la surface et sont éliminés. L'or purifié est ensuite coulé dans des moules pour produire des barres de haute pureté.
L'électrolyse, également connue sous le nom de procédé Wohlwill, est une autre méthode très répandue. Le doré est dissous dans une solution de chlorure et un courant électrique est appliqué pour déposer de l'or pur sur une cathode. Les impuretés restent dans la solution ou forment une boue au fond de la cellule d'électrolyse. L'électrolyse peut produire de l'or d'une pureté allant jusqu'à 99,99%. Après affinage, ces lingots d'or de haute pureté sont prêts à être vendus ou transformés en divers produits en or.
Gestion des résidus
Les résidus sont les morceaux de roche finement broyés et les restes de produits chimiques issus du processus d'extraction de l'or, et ils doivent être traités correctement afin de minimiser les dommages causés à l'environnement. Ces matériaux sont généralement conservés dans des barrages ou des bassins de résidus, qui sont des structures spécialement conçues pour empêcher l'eau et les sédiments contaminés de s'écouler dans la zone environnante. Les sociétés de production d'or soucieuses d'agir de manière responsable utilisent différentes stratégies pour s'assurer qu'elles gèrent les résidus de manière sûre et efficace.
Une stratégie importante consiste à utiliser des digues à résidus dotées d'un revêtement spécial pour empêcher l'eau contaminée de s'infiltrer dans le système d'eaux souterraines. Des systèmes de traitement de l'eau sont également utilisés pour éliminer les contaminants de l'eau des résidus avant qu'elle ne soit rejetée ou recyclée dans le circuit de traitement. Une autre approche consiste à éliminer les résidus à sec, c'est-à-dire à les assécher et à les compacter pour leur donner une forme stable. Cette méthode réduit le risque de rupture de barrage et occupe moins d'espace dans l'installation de stockage des résidus. La remise en état et la réhabilitation des installations de stockage des résidus sont également des éléments très importants d'une gestion responsable des résidus. Il s'agit de s'assurer que le terrain est remis dans un état stable et productif une fois les opérations minières terminées.
Équipement nécessaire au traitement de l'or
Le traitement de l'or nécessite un grand nombre d'équipements spécialisés afin de garantir que l'extraction et le raffinage de ce métal précieux soient effectués de manière efficace et efficiente. Voici quelques-uns des principaux équipements utilisés dans le traitement de l'or :
* Concasseurs et broyeurs: Il s'agit de concasseurs à mâchoires, de concasseurs à cônes, de concasseurs à percussion, de broyeurs à boulets et de broyeurs à barres. Ils sont utilisés pour concasser et broyer le minerai d'or jusqu'à la taille souhaitée.
* Équipement de concentration par gravité: Il s'agit des tables à secousses, des jigs, des spirales et des concentrateurs centrifuges. Ils sont utilisés pour séparer les particules d'or du minerai en fonction de leur densité par rapport au reste du matériau.
* Épaississants et clarificateurs: Ils sont utilisés pour séparer les éléments solides du liquide dans la boue et pour augmenter la densité de la pâte (qui correspond à la quantité de matière solide dans le liquide).
* Réservoirs de lixiviation: Il s'agit de grandes cuves dans lesquelles le minerai concassé et broyé est mélangé à la solution de cyanure pour dissoudre l'or.
* Colonnes d'adsorption et d'élution: Ils sont utilisés pour extraire l'or de la solution prégnante (le liquide contenant l'or dissous) à l'aide de charbon actif, puis pour retirer l'or du charbon chargé.
* Cellules d'électrolyse: Ils utilisent un courant électrique pour que l'or se dépose sur les cathodes.
* Fours de fusion: Ils sont utilisés pour fondre les boues d'or et produire des barres d'or doré.
* Équipement de raffinage: Selon le mode de raffinage de l'or, vous pouvez utiliser des réacteurs de chloration, des cellules électrolytiques ou des fours Miller pour produire des lingots d'or de grande pureté.
Autres méthodes de traitement de l'or
Outre les étapes habituelles de traitement de l'or, il existe quelques autres méthodes pour extraire l'or des minerais, en fonction des caractéristiques spécifiques du minerai et de l'intérêt économique du procédé. Ces méthodes sont les suivantes
L'or CIL (Carbone en lixiviation):
Le CIL de l'or est un procédé qui lixivie et adsorbe l'or du minerai en même temps dans une série de cuves agitées qui contiennent une solution de cyanure et du charbon actif.
L'or CIP (Carbone en pâte):
Le procédé CIP pour l'or est assez similaire au procédé CIL, mais l'or est adsorbé après l'étape de lixiviation. Dans cette méthode, la solution contenant l'or est transférée dans des cuves contenant du charbon actif.
L'or Tas Lixiviation:
La lixiviation en tas est un procédé qui fonctionne bien pour les minerais d'or à faible teneur. Dans cette méthode, le minerai est empilé sur un support étanche, puis une solution de lixiviation est pulvérisée sur le tas pour dissoudre l'or.
Flottation:
La flottation est un procédé utilisé pour traiter les minerais d'or contenant beaucoup de minéraux sulfurés qui flottent facilement. Dans cette méthode, les minéraux contenant de l'or sont séparés de la roche stérile (gangue) en adhérant aux bulles d'air et en flottant à la surface.
Ces méthodes alternatives d'enrichissement de l'or peuvent être utilisées dans des cas spécifiques où les caractéristiques du minerai et les facteurs économiques en font un meilleur choix que les étapes conventionnelles de traitement de l'or.
Conclusion
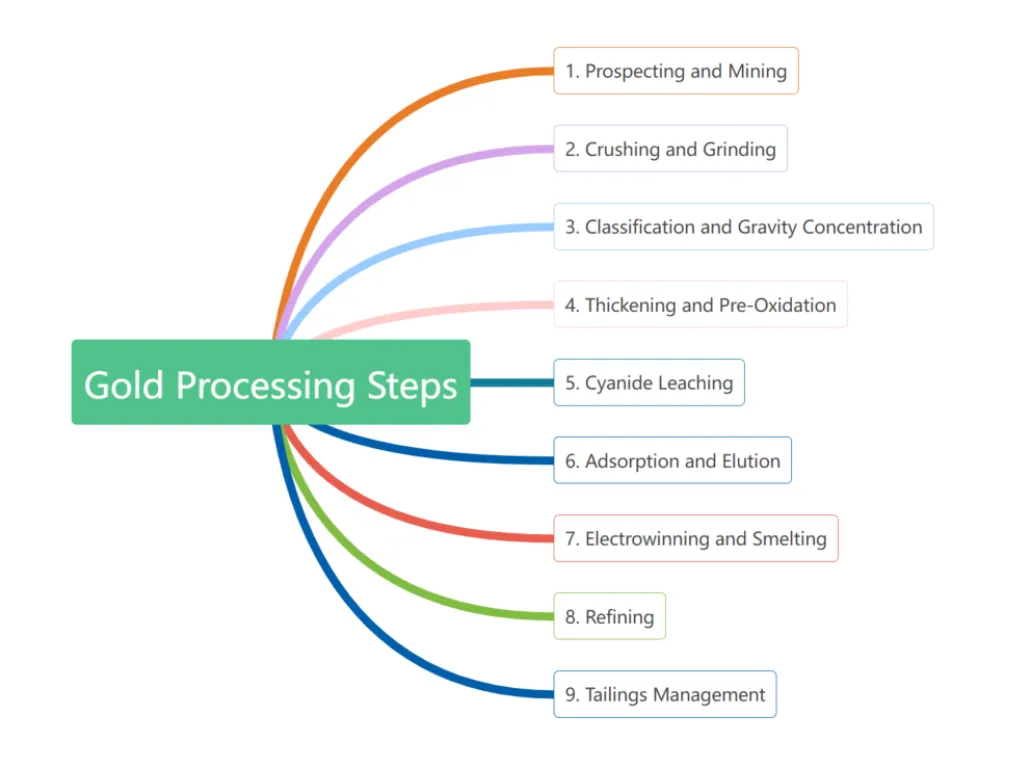
Du début à la fin, traitement de l'or comprend une série d'étapes et d'opérations diverses qui requièrent un savoir-faire, un équipement et des procédures extraordinaires. Tout commence par la prospection et l'exploitation minière, puis vient le raffinage et la gestion des résidus (les matériaux supplémentaires). Si vous travaillez dans le secteur de l'extraction de l'or, il est impératif de connaître toutes ces étapes. Pourquoi ? Parce que cela permet d'optimiser les formes d'extraction et de raffinage, de minimiser l'impact sur l'environnement et de s'assurer que l'on crée ce métal précieux de manière efficace.
En savoir plus sur JXSC
Si vous souhaitez en savoir plus sur les étapes du traitement de l'or et découvrir les meilleurs arrangements pour vos opérations minières, vous devriez certainement consulter JXSC. Il s'agit d'un pionnier de confiance dans l'industrie, avec plus de 35 ans d'expérience et une proximité dans le monde entier. JXSC propose une large gamme d'articles et d'administrations, notamment des équipements de pointe, des plans de manutention et un soutien spécialisé. JXSC connaît parfaitement tous les aspects de la préparation de l'or, du concassage au pilonnage, en passant par la séparation par gravité, la flottaison et le raffinage. En vous associant à JXSC, vous optimiserez vos opérations de préparation de l'orLes avantages de l'assurance maladie sont nombreux, ce qui permet d'accroître l'efficacité et de maximiser les bénéfices.