- Accueil
- Blog
- Informations sur l'équipement
- Anatomie d'un broyeur à boulets : Schéma détaillé d'un broyeur à boulets
Introduction aux broyeurs à billes
Les broyeurs à boulets constituent un élément important de l'engrenage dans l'industrie minière et le traitement des minerais, où ils sont utilisés dans l'étape de broyage du processus de concassage. La fragmentation consiste à réduire la taille des matériaux solides et se compose de deux étapes principales : le broyage et le concassage. Le concassage est la phase primaire au cours de laquelle les grosses particules sont réduites en particules plus petites qui peuvent être introduites dans les broyeurs, y compris les broyeurs à boulets. Le broyage, qui est la deuxième et dernière étape, réduit la taille des particules en particules encore plus fines à l'aide de forces d'impact et d'attrition.
Outre l'industrie minière, les broyeurs à billes sont également utilisés dans différents secteurs, tels que la production de ciment, pour le broyage du clinker et d'autres matières premières, la fabrication de céramiques, pour le broyage et le mélange de poudres céramiques, et la production de peintures, pour la dispersion et l'homogénéisation des pigments et d'autres ingrédients. Les multiples utilisations des broyeurs à boulets sont la principale raison pour laquelle ils sont si importants dans de nombreuses industries. Pour une explication détaillée des broyeurs à billes, cliquez sur Qu'est-ce qu'un broyeur à billes et comment fonctionne-t-il ? Une explication approfondie.
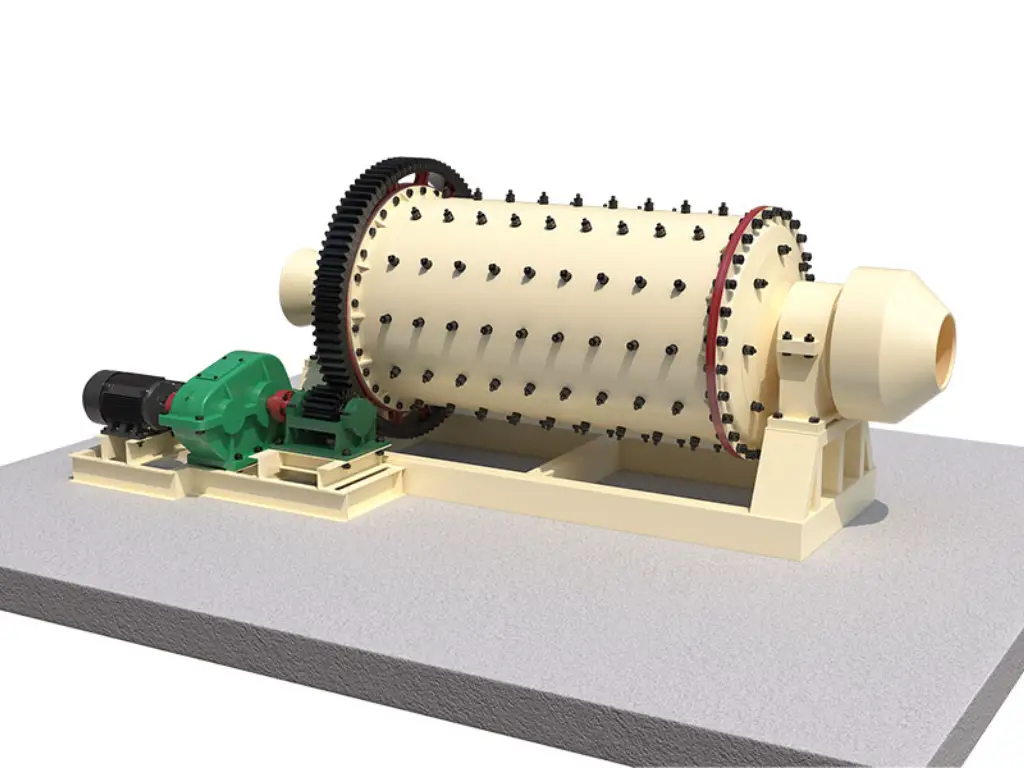
Principe de fonctionnement des broyeurs à billes
Mécanismes de fragmentation : impact et attrition
L'action de broyage dans un broyeur à boulets est obtenue grâce à deux mécanismes de fragmentation principaux : l'attrition et l'impact. L'impaction se produit lorsque les éléments broyants (billes ou galets durs) se heurtent les uns aux autres et à la matière à broyer. Cela entraîne la fragmentation de la substance en morceaux de plus petite taille. Au contraire, l'attrition est un processus qui résulte du frottement et du cisaillement des particules les unes contre les autres ainsi que contre la coquille du broyeur, ce qui entraîne une réduction supplémentaire de la taille.
Niveaux d'énergie des agents de broyage
Les niveaux d'énergie des éléments broyants sont très importants pour le fonctionnement du broyeur à boulets. Pendant la rotation de la coquille, les éléments broyants sont soulevés sur les côtés du broyeur jusqu'à ce qu'ils retombent au fond du broyeur. Plus les éléments sont soulevés et plus ils retombent violemment sur la matière à broyer, plus l'énergie transmise à la matière est importante. Certains paramètres tels que le diamètre, le volume et la vitesse de l'élément broyeur influencent le niveau d'énergie.
Rotation de la coque et de la plaque de base
La rotation de la virole du broyeur à boulets est un élément très important pour le processus de broyage. La virole est généralement montée sur un axe horizontal et tourne à une certaine vitesse appelée vitesse critique. La vitesse critique est la vitesse de rotation à laquelle la force centrifuge est égale à la force gravitationnelle, ce qui fait que les éléments broyants restent collés à la virole du broyeur au lieu de tomber. En général, les broyeurs à boulets fonctionnent à une vitesse critique comprise entre 50 et 90% afin d'obtenir les meilleurs résultats de broyage possibles.
Fonctionnement des broyeurs à boulets
Fonctionnement en cascade à différentes vitesses
Le fonctionnement d'un broyeur à boulets peut être classé en trois modes distincts en fonction de la vitesse de rotation :
Faible vitesse : roulement des billes de broyage sans volée
À faible vitesse, les éléments broyants roulent au fond du broyeur sans être soulevés par les parois. Ce mode se caractérise par des forces d'impact faibles et est idéal pour les applications de broyage ou de mélange légères.
Mode mixte (Cascade mouvement de mode) : roulis partiel et vol partiel
Avec l'augmentation de la vitesse de rotation, les éléments broyants sont soulevés le long des parois du broyeur et atteignent une certaine hauteur avant de retomber. Ce mode de mouvement mixte, également appelé cascade, est le plus couramment utilisé pour les broyeurs à boulets, car il permet d'équilibrer les forces d'impact et d'attrition.
Vitesse élevée : mouvement circulaire des billes sans chute
À des vitesses très élevées, le matériau à broyer est transporté autour de la circonférence du broyeur sans tomber. Cette méthode, communément appelée centrifugation, n'est pas applicable au broyage car il n'y a pas d'impact ou d'attrition.
Importance de la vitesse de rotation
La vitesse de rotation du broyeur à boulets est un paramètre critique qui détermine l'efficacité du broyage et la qualité du produit final. La vitesse optimale varie en fonction du diamètre du broyeur, de la taille et de la densité des éléments broyants et du matériau à broyer. Le fait de fonctionner à la bonne vitesse garantit que les éléments broyants transfèrent le maximum d'énergie au matériau et n'entraînent pas une usure excessive des composants du broyeur.
Alimentation et déchargement du matériel
Les broyeurs à boulets peuvent fonctionner soit en mode discontinu, soit en mode continu. En mode discontinu, une quantité donnée de matériau est chargée dans le broyeur et broyée pendant une période spécifique, puis déchargée. En mode continu, la matière est alimentée en continu à une extrémité du broyeur et déchargée à l'autre. Les mécanismes d'alimentation et de décharge, qui comprennent les goulottes, les trémies et les grilles, sont les éléments les plus importants pour assurer un flux cohérent et contrôlé de la matière dans le broyeur.
Vitesse optimale pour une réduction maximale de la taille
Pour obtenir une réduction maximale de la taille des particules, les broyeurs à boulets doivent fonctionner à leur vitesse optimale. Cette vitesse se situe normalement entre 50 et 90% de la vitesse critique, qui dépend de l'application et du matériau à broyer. À la vitesse optimale, le matériau de broyage tombe le long de la coquille du broyeur au point le plus élevé, générant ainsi une force d'impact maximale, et le processus de broyage devient efficace.
Construction des broyeurs à boulets
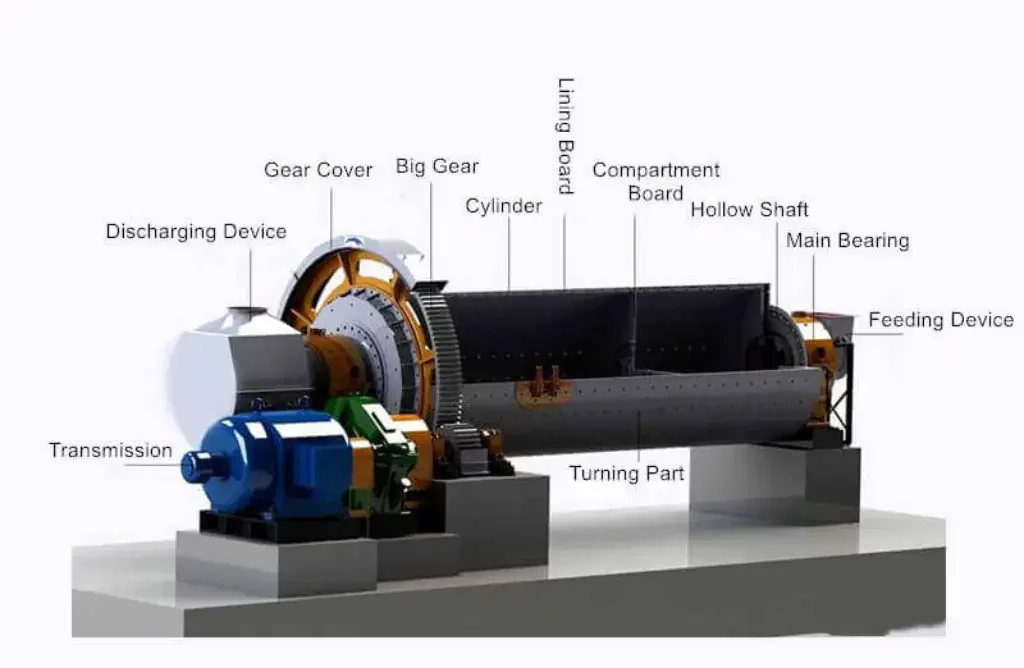
Un broyeur à boulets se compose de trois éléments principaux : la virole, le matériau de broyage (boulets ou cailloux) et le moteur. La coquille est constituée d'un tube métallique creux à l'intérieur, revêtu de matériaux résistants à l'usure tels que l'acier au manganèse ou le caoutchouc. Les éléments de broyage peuvent être en acier chromé, en céramique ou en caoutchouc, mais le choix dépend de l'application. Les billes d'acier sont le type le plus courant d'agent de broyage et peuvent être obtenues dans une variété de tailles allant de 10 mm à 150 mm de diamètre. La taille des billes dépend de la taille de la matière première et de la taille souhaitée pour le produit final. Les billes en céramique et en caoutchouc sont utilisées dans les processus où les billes en acier ne conviennent pas pour la contamination, par exemple dans la production de matières premières céramiques et de peinture.
Le revêtement de la virole est une partie nécessaire qui est chargée de protéger la virole du broyeur contre l'usure induite par l'impact et l'abrasion de l'agent de broyage. L'acier au manganèse, le caoutchouc et la céramique sont les types de matériaux de revêtement les plus couramment utilisés. L'acier au manganèse est réputé pour sa grande résistance à l'usure en raison de sa large application dans l'exploitation minière et le traitement des minerais. Le revêtement en caoutchouc est utilisé pour le broyage humide et permet de réduire le niveau de bruit. Les revêtements en céramique sont utilisés dans les applications à haute température ou lorsque la contamination par les revêtements métalliques pose problème. La rotation du broyeur est entraînée par le moteur, dont la puissance est déterminée par la taille du broyeur et la capacité de broyage.
Les broyeurs à boulets peuvent être aussi petits que les broyeurs de laboratoire ou aussi grands que les broyeurs industriels, avec un diamètre pouvant atteindre 8 m. La capacité du broyeur est dictée par son volume. Le volume dépend à la fois du diamètre et de la longueur. En général, le rapport longueur/diamètre du broyeur, appelé rapport L/D, est compris entre 0,5 et 3. Les broyeurs plus courts sont utilisés pour écraser les matériaux grossiers, tandis que les broyeurs plus longs sont utilisés pour broyer les matériaux fins. Les dimensions et la capacité du broyeur à boulets sont déterminées en fonction de l'application et du débit requis.
Découvrez le fonctionnement de ces pièces à l'adresse suivante Maîtriser la méthode de broyage à billes : Votre guide complet.
Facteurs déterminant l'efficacité des broyeurs à boulets
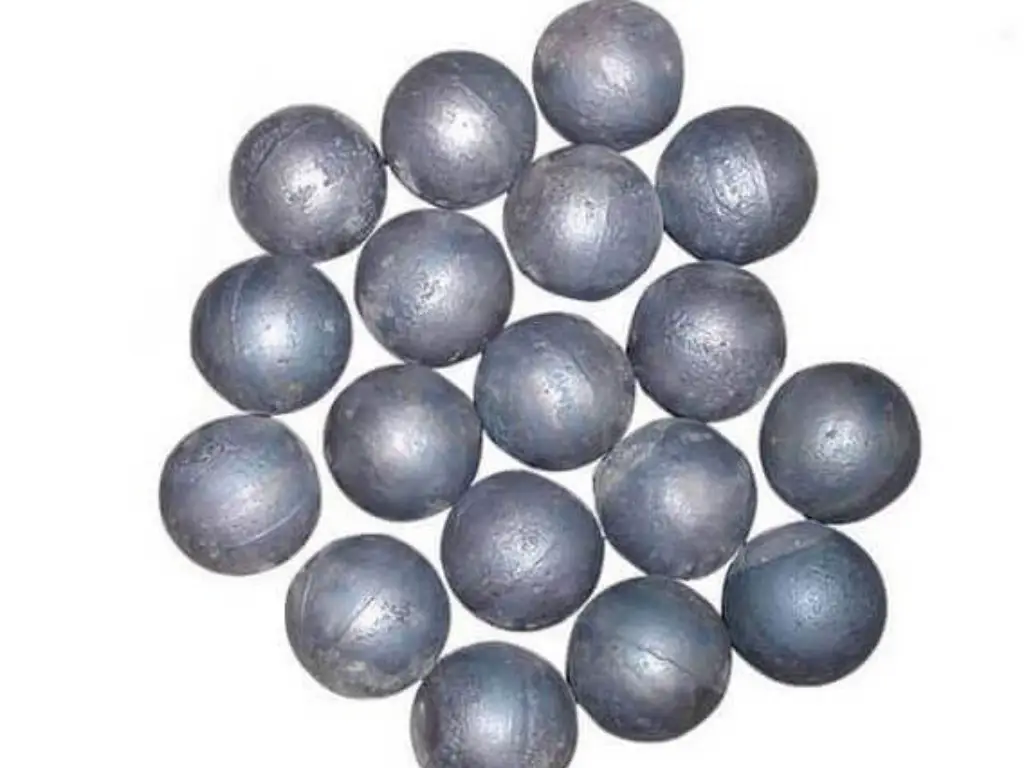
Temps de séjour du matériau
Le temps de séjour, c'est-à-dire la période pendant laquelle le matériau reste à l'intérieur du broyeur, est le principal paramètre qui influe sur l'efficacité du broyeur. Une période de fonctionnement plus longue permet une plus grande interaction entre le support de broyage et le matériau, ce qui permet de broyer le matériau en particules plus fines. Toutefois, le temps de séjour prolongé peut entraîner un surbroyage et une réduction de la capacité, ainsi qu'une consommation d'énergie supplémentaire.
Taille, densité et nombre de billes
L'efficacité du broyage dépend de facteurs tels que la taille, la densité et le nombre de billes dans le broyeur. Plus les billes sont grosses et denses, plus l'apport d'énergie est important et plus le broyage est rapide. Toutefois, l'utilisation de billes beaucoup trop grosses peut entraîner un broyage plus faible et une usure accrue du revêtement intérieur du broyeur. Le nombre de billes doit être ajusté afin de s'assurer que les billes ne manquent pas la cible et qu'elles ne sont pas trop denses.
Dureté des billes et du matériau
Le choix de la dureté du support de broyage du broyeur à boulets, ainsi que le type de matériau à broyer, influencent fortement l'efficacité du broyeur à boulets. La dureté du support de broyage doit être supérieure à celle du matériau à broyer pour assurer un bon calibrage. L'utilisation de billes d'une dureté appropriée est essentielle pour réguler l'usure du broyeur et la consommation d'énergie, ainsi que pour protéger le revêtement du broyeur.
Vitesse et niveau d'alimentation
Le taux d'alimentation, qui est la vitesse à laquelle le matériau est introduit dans le broyeur, et le niveau d'alimentation, qui est le niveau de matériau à l'intérieur du broyeur, sont les deux principaux facteurs qui influencent l'efficacité du broyeur à boulets. Une vitesse d'alimentation optimale et contrôlée garantit que le broyeur fonctionne au mieux sans être surchargé. Le niveau d'alimentation doit être maintenu à environ 30-50% du volume du broyeur à boulets afin de créer suffisamment d'espace pour que les éléments broyants puissent se déplacer et percuter le matériau.
Vitesse de rotation du cylindre
Comme indiqué plus haut, la vitesse de rotation du cylindre du broyeur à boulets est un élément clé de l'efficacité du processus de broyage. Les composants du broyeur sont soumis à une usure minimale, car la vitesse de rotation du broyeur est optimisée pour obtenir l'énergie maximale transmise par le matériau de broyage. La vitesse optimale peut varier en fonction du diamètre du broyeur, de la taille et de la densité des éléments broyants et du matériau à broyer.
Processus de fonctionnement des broyeurs à billes
Phase initiale : particule aplatissement et changement de forme
Au cours de la phase initiale du processus de broyage, les particules du matériau d'alimentation sont aplaties et leur forme est modifiée en raison de la force d'impact de l'agent de broyage. C'est à ce stade que la plupart des particules de grande taille sont transformées en morceaux plus petits.
Stade intermédiaire : changements significatifs par rapport au stade initial
Les particules sont soumises à des changements considérables au fur et à mesure que le processus de broyage progresse, contrairement à la phase initiale. Les particules deviennent plus sphériques et plus uniformes, et la réduction de la taille est plus lente. Cette étape est provoquée par des forces d'impact et d'attrition, ce qui se traduit par une taille de particule plus fine.
Phase finale : particule réduction de la taille et microstructure homogène
Dans la phase finale du processus de broyage, les particules sont réduites à leur taille finale et une microstructure homogène est obtenue. Les particules sont maintenant très fines et uniformes, avec une distribution de taille étroite. Cette étape est principalement constituée de forces d'attrition, car les particules sont trop petites pour être brisées efficacement par l'impact lui-même.
Stade d'achèvement : structure métastable extrêmement déformée
Les particules ont subi de nombreuses déformations et ont atteint un état métastable à la fin du processus. Ce stade est appelé stade de haute déformation et de défauts de réseau dans les particules, et il peut être associé à une réactivité accrue et à des propriétés uniques. La dernière étape est souvent requise dans des applications telles que l'alliage mécanique, où l'objectif est d'obtenir des microstructures et des propriétés uniques du matériau.
Avantages des broyeurs à billes
1. Peut traiter des matériaux difficiles comme les minerais durs et les argiles molles.
2. Pour obtenir des particules de petite taille, le processus de broyage peut produire des particules submicroniques.
3. Cet équipement fonctionne en continu, ce qui garantit un débit élevé et des temps d'arrêt réduits.
4. La capacité de contrôler la taille du produit final en ajustant simplement les paramètres de fonctionnement est la caractéristique remarquable de cette technique.
5. Assurer un mélange et une homogénéisation adéquats pour un résultat final uniformément dispersé.
6. La conception simple et l'entretien minimal avec le remplacement des pièces d'usure sont ses avantages.
Inconvénients des broyeurs à boulets
1. Consommation d'énergie élevée, avec une grande quantité de chaleur et de bruit résultant du gaspillage d'énergie.
2. Possibilité de contamination des matériaux de broyage et de revêtement.
3. Le risque de surbroyage en l'absence de contrôle, qui se traduit par des particules ultrafines indésirables.
4. Impossibilité de choisir de contrôler une taille de particule unique, ce qui conduit à une gamme de distribution de taille.
5. Fonctionnement bruyant dans les concasseurs, en particulier à des vitesses plus élevées ou avec des médias de broyage plus grands.
Conclusion
En conclusion, l'anatomie d'une entreprise industrielle broyeur à boulets et son diagramme complexe sont essentiels à la performance optimale du broyeur et au bon déroulement des processus de broyage. Grâce à une évaluation minutieuse des principes de fonctionnement, de la construction, de l'exploitation et des facteurs déterminants de l'efficacité du broyeur, les opérateurs et les ingénieurs peuvent prendre des décisions éclairées pour garantir une efficacité de broyage maximale et la production de produits de haute qualité dans de nombreux domaines, tels que l'exploitation minière, le traitement des minerais, les céramiques et les peintures.