- Inicio
- Blog
- Solución mineral
- Extracción de mineral de hierro: El proceso esencial para la producción de acero
¿Qué es el mineral de hierro?
El mineral de hierro es una sustancia mineral metálica capaz de producir hierro metálico (Fe) cuando se calienta con un reductor. Es el principal material utilizado como insumo para producir acero, y para ello se utiliza 98% de mineral de hierro. La magnetita (Fe3O4), la hematita (Fe2O3), la goethita, la limonita o la siderita son los minerales de hierro que suelen encontrarse, y los que más se extraen son la hematita y el cobre. Los meteoritos de hierro, por lo general, contienen níquel y se cree que proceden de cuerpos acrecionados de 1.000 km (621 mi) de diámetro o mayores. En los últimos años, la producción mundial de tmpa de mineral de hierro no ha dejado de crecer para satisfacer la creciente demanda de acero, siendo la empresa minera brasileña Vale el mayor productor mundial. Según el Servicio Geológico de Estados Unidos (USGS), la producción mundial de mineral de hierro en 2021 será de aproximadamente 2.300 millones de toneladas, con Vale a la cabeza.
El mineral de hierro se obtiene mediante minería a cielo abierto o subterránea y luego se somete a un proceso de trituración, cribado y beneficio para elevar su nivel de contenido de hierro. El mineral se mezcla hasta alcanzar un grado homogéneo y se transporta para su exportación.
¿Dónde encontrar mineral de hierro?
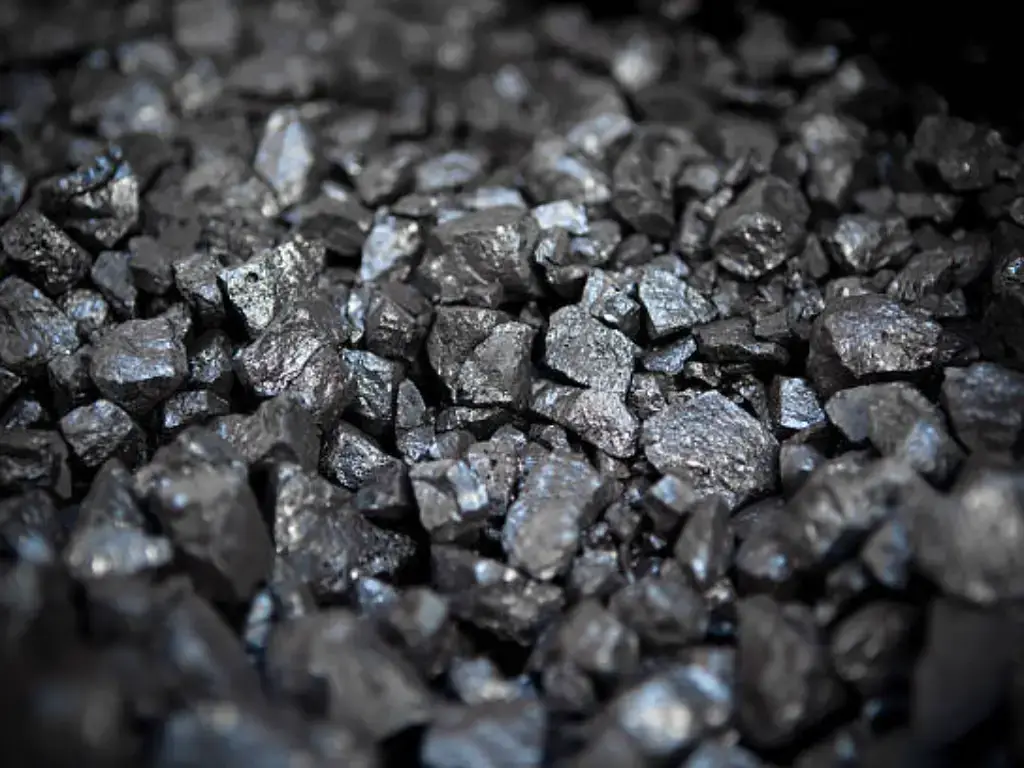
Los yacimientos de mineral de hierro se encuentran en varias regiones de todo el mundo. Los mayores productores son Australia, Brasil, China e India. También hay importantes minas de hierro en Estados Unidos, Canadá, Rusia y Sudáfrica. En Estados Unidos, la mayor parte del mineral de hierro se extrae en la cordillera Mesabi, situada en Minnesota y Michigan, cerca de los Grandes Lagos.
Australia es el mayor productor mundial de mineral de hierro, y Australia Occidental representa más de 90% de la producción del país. La región de Pilbara, en Australia Occidental, alberga algunas de las mayores minas de mineral de hierro del mundo, explotadas por grandes empresas como Rio Tinto, BHP y Fortescue Metals Group. Brasil, segundo productor mundial, tiene sus principales minas de hierro en la región de Carajás, en el estado de Pará.
Tipos de mineral de hierro
La hematita, la magnetita y la limonita son los tres tipos básicos de mineral de hierro, cada uno con propiedades únicas y su propio papel en los procesos de fabricación del acero.
Hematites
La hematites es la mena de hierro más común y más explotada debido a su alto contenido en hierro (60-70%), que facilita su transformación. De color rojizo-negro, este mineral se encuentra en rocas sedimentarias y tiene una textura relativamente blanda, lo que facilita su molienda y trituración. La hematites es la mena preferida para la producción de acero porque, al reducirse a hierro metálico, requiere menos energía que otras menas. El alto contenido en hierro y las menores impurezas de la hematites contribuyen sin duda a que las operaciones en los altos hornos sean más suaves y mejores y, en consecuencia, a que los productos siderúrgicos sean de mejor calidad.
Magnetita
La magnetita, aunque menos común que la hematites, contiene el mayor porcentaje de hierro, con hasta 72% de hierro. Este mineral negro y magnético se forma en las rocas metamórficas e ígneas, por lo que es difícil de extraer y procesar. Sin embargo, las propiedades magnéticas de la magnetita son más adecuadas para separarla de los minerales de ganga, lo que se facilita con los métodos de separación magnética. La magnetita es más rica en hierro que los demás minerales. Por lo tanto, da un concentrado de mayor calidad que es importante en la producción de acero. La mayor densidad de la magnetita la hace adecuada para su uso en la separación de medios pesados, uno de los métodos utilizados para mejorar los minerales de hierro de menor calidad.
Limonita
La limonita, también llamada "mineral de hierro de pantano", es un mineral de baja calidad con un color marrón amarillento debido a sus impurezas. Es el subproducto de la meteorización de otros minerales ricos en hierro y contiene alrededor de 20-30% de hierro. No obstante, la limonita tiene un valor económico inferior al de la hematites y la magnetita debido a su menor contenido en hierro combinado con la presencia de impurezas como sílice y alúmina; sin embargo, se ha utilizado en la producción de acero durante mucho tiempo. La limonita se mejora mediante técnicas de beneficio como el lavado, el jigging y el proceso de sinterización antes de utilizarla como materia prima en los altos hornos. De hecho, la limonita puede utilizarse como mineral secundario que se mezcla con los minerales principales para alcanzar el contenido de hierro y los niveles de impurezas requeridos.
La selección del mineral de hierro para la producción de acero depende de varios aspectos, como el contenido de hierro, los niveles de impurezas, los requisitos de procesamiento y la rentabilidad. La hematites es la forma más utilizada, ya que es bastante común, contiene un alto contenido de hierro y no es difícil de procesar. La magnetita puede ser más dura en la naturaleza, pero se utiliza cada vez más como materia prima en la producción de acero para producir concentrados de mayor calidad debido a su mayor contenido en hierro. La limonita puede no ser la mena más deseable, pero puede utilizarse en la producción de acero cuando sea económicamente viable o para proporcionar una mena de mezcla a los hornos con el fin de mejorar el rendimiento y la calidad del producto.
El proceso de extracción del mineral de hierro
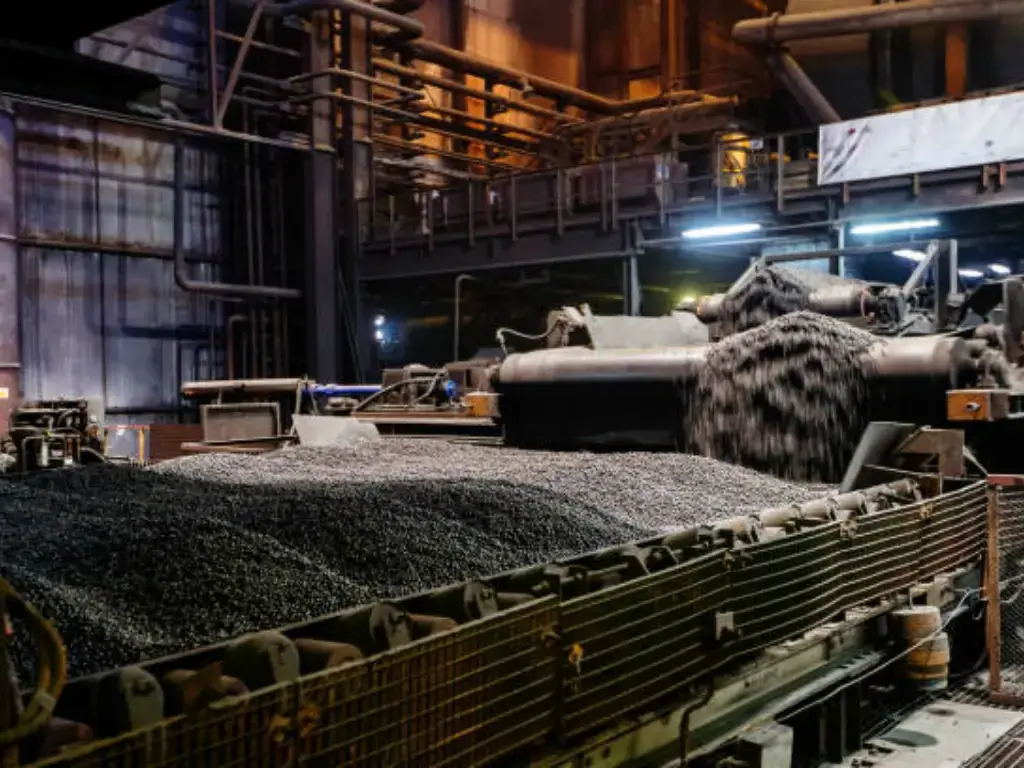
Paso 1:Exploración y selección de yacimientos: encontrar buenos yacimientos.
La extracción de mineral de hierro comienza con el proceso de exploración y selección del emplazamiento. Los geólogos y los ingenieros de minas aplican distintas técnicas para identificar las ubicaciones probables de los yacimientos de mineral de hierro, como estudios geofísicos, reconocimientos aéreos y perforaciones exploratorias. El estudio inicial demuestra que un yacimiento es prospectivo, con depósitos potenciales en zonas como la región de los Grandes Lagos. La siguiente etapa consiste en un estudio detallado y la toma de muestras para determinar el volumen y la calidad del yacimiento de mineral de hierro.
Paso 2: Perforación y voladura: Extracción de mineral de la tierra
Una vez que el yacimiento de mineral de hierro es factible, el proceso de extracción pasa a excavar el mineral de la tierra. La técnica más utilizada es la minería a cielo abierto, que consiste en perforar y volar la roca y el suelo de la superficie para llegar al yacimiento de mineral que hay debajo en estados como Minnesota y Michigan, alrededor de la zona del Lago Superior. Una vez retirada la sobrecarga, el mineral de hierro se perfora y se dinamita para convertirlo en trozos más pequeños que puedan transportarse fácilmente desde las minas.
Etapa 3: Transporte - Envío del mineral a la planta de transformación
A continuación, el mineral se desprende mediante la voladura y los vehículos gigantes o cintas transportadoras lo sacan de la mina. El mineral se transporta a la planta de procesamiento. Puede estar cerca o en un lugar lejano. El mineral viaja en camión, tren o barco; la elección del modo de transporte depende de la distancia y la ubicación. Para que el proceso de extracción del mineral de hierro se lleve a cabo con eficacia, es necesario que el mineral llegue a la planta de manera eficiente.
Etapa 4: Trituración y molienda - Preparación del mineral para la separación
En la planta, unas máquinas llamadas trituradoras desmenuzan el mineral. Las primeras trituradoras son trituradoras de mandíbula que rompen los trozos más grandes. A continuación, trituradoras de cono descomponerlo más. Por último, los trozos de mineral pasan a molinos de bolas o molinos de barras. Se trata de grandes tambores giratorios con bolas o barras de acero en su interior. Al girar, muelen el mineral hasta convertirlo en un polvo fino. Este paso aumenta la superficie, de modo que el hierro puede separarse más fácilmente en el siguiente paso.
Paso 5: Separación magnética - Extracción del hierro
Los fuertes imanes atraerán el fino polvo de mineral de hierro. Las partículas de hierro son atraídas y captadas por los imanes. Esta técnica de separación magnética es eficaz para los minerales de alta calidad, como la magnetita. Se utiliza un imán para atraer las partículas magnéticas de hierro y se desecha la roca residual. Mediante este proceso, se obtiene polvo de mineral de hierro concentrado. Mejore su proceso de extracción de hierro con nuestros avanzados separador magnético tecnología, detallada aquí.
Etapa 6: Peletización - El proceso de producción de pellets de mineral de hierro
A continuación, el mineral de hierro concentrado se mezcla con agentes aglutinantes, como arcilla bentonítica, y se forma en pequeños gránulos del tamaño de una canica utilizando un disco o tambor de granulación. A continuación, los gránulos se endurecen en un horno a altas temperaturas (1.200-1.300°C). La peletización del mineral de hierro permite un transporte y una manipulación más eficaces, así como un mejor rendimiento en el alto horno durante el proceso de fabricación del acero.
Equipos de extracción de hierro
Equipamiento | Características | Aplicaciones | Beneficios |
---|---|---|---|
Equipos de perforación | 1.Perforación rotatoria o por percusión- Profundidades de perforación de hasta 60 metros 2.Energía hidráulica o eléctrica 3.Funcionamiento automatizado o manual | 1. Creación de agujeros de voladura en la sobrecarga y el mineral de hierro 2.Apto para minas de superficie y subterráneas 3.Utilizado en perforación de exploración y producción | 1.Perforación eficaz y precisa 2.Versátil para diferentes condiciones de mina 3.Alta productividad y costes de explotación reducidos |
Explosivos | 1.- ANFO (Fuel Oil de Nitrato de Amonio) 2.Explosivos de emulsión 3.Detonadores electrónicos o no eléctricos 4.Técnicas de voladura controlada | 1. Romper la sobrecarga y el mineral de hierro 2.Aplicable en minas a cielo abierto y subterráneas 3.Fragmentación de la roca para facilitar la excavación | 1.Voladura optimizada para mejorar la fragmentación 2.Mayor seguridad con detonación controlada 3.Soluciones de voladura rentables y fiables |
Camiones de transporte | 1.Camiones de bastidor rígido o articulados 2.Capacidad de carga de 40 a 400 toneladas 3.Opciones de propulsión diésel o eléctrica 4.Funcionamiento autónomo o tripulado | 1.Transporte del mineral de hierro de la mina a la planta de transformación 2.Adecuado para minas a cielo abierto y a gran escala .3.Operaciones de transporte continuas | 1. Alta capacidad de carga útil para un transporte eficiente 2.Diseño robusto para las duras condiciones de la minería 3.Funciones avanzadas de seguridad y comodidad para el operador |
Trituradoras | 1.Trituradoras de mandíbulas, de cono, giratorias o de impacto 2.Etapas de trituración primaria y secundaria 3.Alta capacidad y ratios de reducción 4.Materiales resistentes al desgaste | 1.Reducción del tamaño del mineral de hierro para su posterior procesamiento 2.Aplicable a varios tipos y durezas de mineral de hierro 3.Integración con circuitos de molienda | 1.Reducción eficaz del tamaño para un procesamiento optimizado 2.Componentes duraderos para una larga vida útil 3.Diseños personalizables para propiedades específicas del mineral |
Molinos | 1. Molinos de bolas, de barras o autógenos 2.Procesos de molienda en húmedo o en seco <br.3.Clasificadores de alto rendimiento 4.Sistemas de control automático | 1.Molienda de mineral de hierro en partículas finas 2. Adecuado para hematita, magnetita y otros minerales. 3.Preparación para la separación magnética o la granulación | 1.Distribución homogénea y uniforme del tamaño de las partículas 2.Alto rendimiento y eficiencia energética 3.Reducción de los costes de mantenimiento y desgaste |
Separadores magnéticos | 1.Separadores magnéticos de baja o alta intensidad 2.Procesos de separación en seco o en húmedo 3.Diseños permanentes o electromagnéticos 4.Etapas múltiples para mejorar la recuperación | 1.Separación magnética de las partículas de mineral de hierro de la ganga 2.Aplicable a minerales de magnetita y hematita 3.Concentración y purificación del mineral de hierro | 1.Altos índices de recuperación y grados de concentrado 2.Eliminación eficaz de impurezas 3.Adaptable a diversas características del mineral y disposiciones de la planta |
Granuladoras | 1.Granuladoras de disco o tambor 2.Procesos de formación de bolas e induración 3.Sistemas de adición de ligante 4. Control y automatización de procesos | 1.Aglomeración de finos de mineral de hierro en pellets 2.Adecuado para concentrado de separación magnética 3.Preparación para el alto horno o la reducción directa | 1.Tamaño y calidad constantes del granulado 2.Mejores propiedades de transporte y manipulación 3.Mejora del rendimiento y la eficiencia de los altos hornos |
Procesamiento del mineral de hierro para la producción de acero
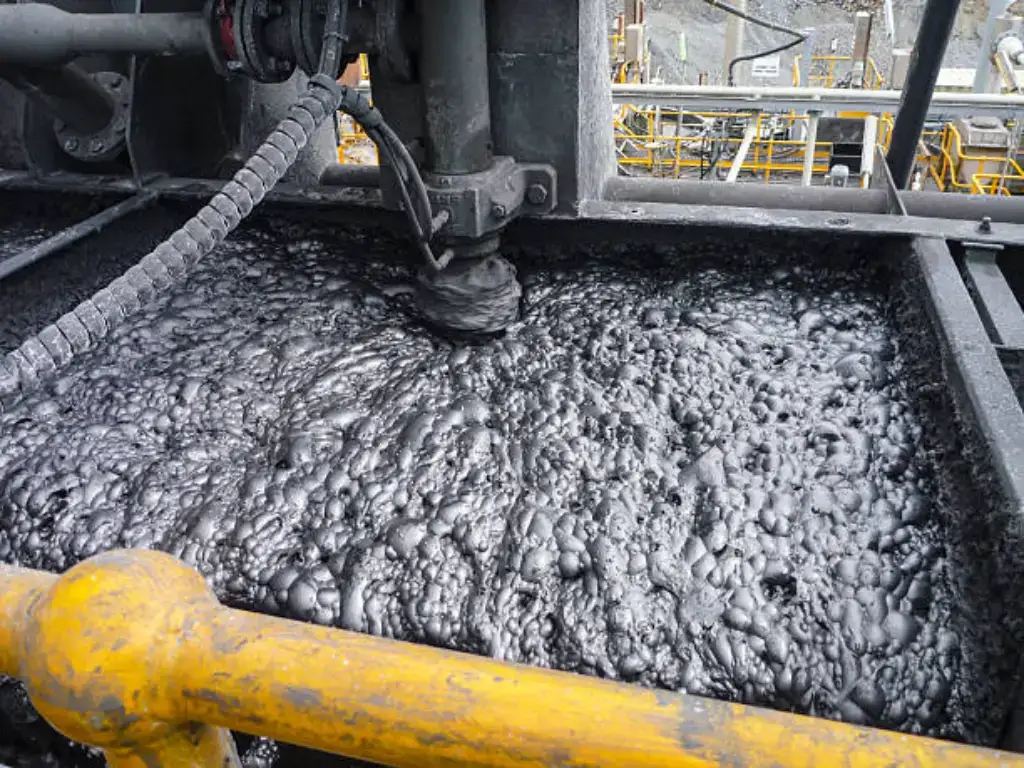
Los datos subyacentes muestran que el principal uso del mineral de hierro extraído es su procesamiento para fabricar acero. La materia prima clave para las plantas siderúrgicas es el mineral de hierro de mina, por lo que en las fábricas de muchos países como China,Canadá se utilizan toneladas de mineral de hierro. El primer paso del proceso es la producción de arrabio, a partir del cual el mineral de hierro se convierte en el alto horno y suele presentarse en forma de óxidos de hierro. El aire caliente se insufla en el horno por la parte inferior, lo que ayuda a que la coquización se queme y se produzcan altas temperaturas (unos 1.500°C). La producción de acero depende totalmente de los recursos naturales. Por ejemplo, el mineral de hierro, el carbón y la piedra caliza, que se utilizan para fabricar acero que se emplea en diversos sectores.
Es una mezcla del mineral de hierro, el coque y la piedra caliza en el alto horno que sufre el cambio y se reduce para formar el estado líquido, hundiéndose al fondo del horno como arrabio. La piedra caliza funciona como fundente , purifica el arrabio de las impurezas. El arrabio fundido se extrae del fondo del alto horno y se funde en lingotes o se transfiere en estado fundido al horno básico de oxígeno para su posterior transformación en acero.
En un horno de oxígeno básico, el arrabio se combina con chatarra de acero y otros aditivos como manganeso, silicio y aluminio en las proporciones adecuadas para obtener las propiedades deseadas del producto de acero. Se introduce en el horno una corriente de oxígeno de gran pureza. Mediante la oxidación, las impurezas del arrabio se convierten en escoria, que se separa del acero fundido. El acero se extrae del horno, ya refinado, y puede moldearse en diversas formas, como desbastes, palanquillas o tochos, que son los productos finales.
Conclusión
La extracción de mineral de hierro se ha identificado como un proceso crucial que suministra las materias primas necesarias para la fabricación de acero, que es un elemento esencial para la infraestructura y la tecnología del mundo moderno. El proceso de extracción del mineral de hierro consta de varias fases, desde la búsqueda de yacimientos adecuados hasta su transformación en un alto horno, lo que requiere equipos y conocimientos especializados.
Dado que la demanda mundial de acero sigue aumentando, la importancia de la extracción de mineral de hierro seguirá haciéndose más patente. El desarrollo de la tecnología minera y de métodos sostenibles será fundamental para crear un suministro constante y consciente de mineral de hierro que permita cubrir la demanda mundial. Conociendo el proceso de extracción del mineral de hierro y su importancia, podremos tener en cuenta el importante papel que desempeña este producto fundamental en la configuración del mundo.