- Inicio
- Blog
- Solución mineral
- Guía definitiva de 101 pasos para procesar oro
Introducción
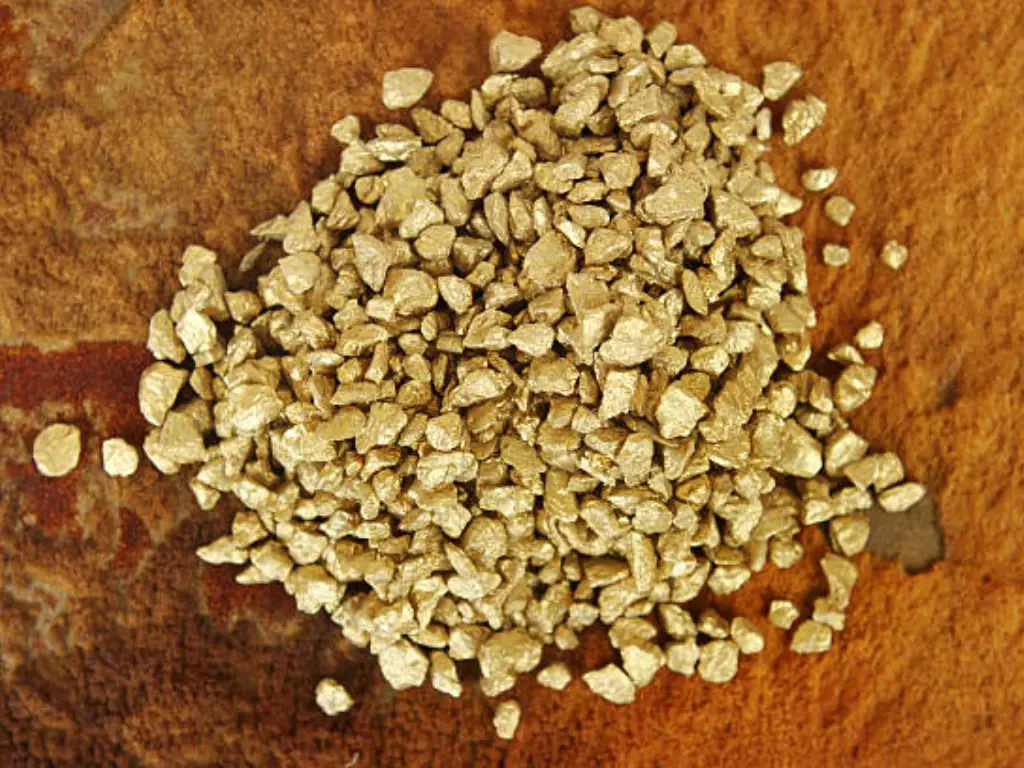
La minería del oro puede ser una industria colosal, con unas 3.500 toneladas de oro extraídas cada año. El valor de la publicidad del oro supera los 1.200 billones de dólares, y la demanda sigue creciendo. Las personas necesitan oro para adornos, especulaciones e innovación. La minería del oro da trabajo a millones de personas en todo el mundo. Además, contribuye al desarrollo financiero de numerosos países, especialmente en África, América Latina y Asia.
Este artículo le guiará a través de las últimas etapas del procesamiento del oro, desde la prospección y la minería hasta el refinado y la creación de lingotes de oro. Obtendrá una comprensión más profunda de la innovación progresiva y la habilidad necesarias para extraer el oro de la tierra y convertirlo en oro inmaculado y brillante. ¡Prepárate para descubrir el interesante mundo de la preparación del oro!
Países con abundantes recursos de oro
Descubrirás oro en lugares totalmente diferentes de todo el mundo, pero algunos países tienen más que otros. La Cámara Mundial del Oro dice que en 2020, las naciones que entregaron la mayor cantidad de oro fueron China, Rusia, Australia, Estados Unidos y Canadá. Estas naciones tienen una parte de los almacenes de oro y han sido la minería de oro durante mucho tiempo, lo que hace una diferencia sus economías se desarrollan e incluye la suma de oro accesible en todo el mundo.
Prospección y minería
Para encontrar oro se utilizan métodos como la cartografía geológica, el muestreo geoquímico y los estudios geofísicos. Cuando se encuentra un posible yacimiento de oro, se realizan perforaciones de exploración para determinar si es económicamente viable explotarlo.
El método de extracción utilizado depende de las características del yacimiento de oro, como la profundidad, la forma y la ley. Las técnicas de minería de superficie, como la minería a cielo abierto y la minería de aluvión, se utilizan para yacimientos poco profundos. Las técnicas de minería subterránea, como la minería de roca dura y la minería de tajo largo, se utilizan para yacimientos profundos.
El tipo de yacimiento de oro también influye en el método de extracción elegido. El oro puede presentarse en diferentes formas:
1. Oro nativo: Oro puro encontrado en forma de pepitas o escamas.
2. Vetas auríferas: Depósitos de oro delgados, en forma de láminas, en grietas o fisuras de la roca.
3. Oro diseminado: Oro disperso por una formación rocosa, a menudo en partículas microscópicas.
Trituración y molienda
El mineral de oro, directamente de la mina, se introduce primero en una trituradora de mandíbulas. Esta gran máquina rompe las enormes rocas en trozos más pequeños, normalmente de unos 100-200 mm de tamaño. Después, el mineral triturado pasa a la trituradora secundaria, que suele ser una trituradora de cono. Aquí se tritura aún más, hasta unos 10-50 mm. A veces, se utiliza una tercera fase de trituración con un rodillo triturador de alta presión (HPGR). Esto puede hacer que el mineral sea muy fino, hasta 5-20 mm antes de pasar a la planta de procesamiento.
El siguiente paso es el circuito de molienda. El mineral triturado se mezcla con agua para formar una pasta, que es una mezcla líquida espesa. A continuación, se muele hasta obtener un polvo fino en molinos de bolas o de barras. Estos molinos tienen bolas o barras de acero en su interior que giran y muelen el mineral hasta que los trozos son de 75 micras o menos. Esto es muy importante porque separa las partículas de oro de la roca circundante. Los mineros vigilan de cerca el proceso de molienda para asegurarse de que las partículas tengan el tamaño perfecto para los siguientes pasos de extracción del oro.
Clasificación y concentración por gravedad
Tras la trituración y la molienda, los lodos de mineral se clasifican mediante hidrociclones. Estas máquinas separan las partículas en función de su tamaño y densidad. Las partículas mayores de 75 micras, que suelen ser más pesadas y contener más oro, se envían al circuito de concentración por gravedad. Las partículas menores de 75 micras, normalmente más ligeras y con menos oro, pasan a la siguiente fase de procesamiento.
En el circuito de gravedad, los lodos se vierten en una mesa de agitación ligeramente inclinada entre 3 y 5 grados. Se agita rápidamente unas 300-400 veces por minuto. Como el oro es mucho más denso que la roca huésped (19,3 g/cm³ frente a 2,5-3,0 g/cm³), las partículas de oro pesadas se hunden en las crestas de la mesa mientras que los residuos más ligeros se lavan. Otros métodos gravimétricos, como las espirales y los concentradores centrífugos, también aprovechan esta diferencia de densidad entre el oro (19,3 g/cm³) y la roca (2,5-3,0 g/cm³) para separar eficazmente las partículas de oro del material de desecho.
Espesamiento y preoxidación
Tras el circuito de gravedad, la pasta de mineral pasa a un tanque espesador. Este tanque separa los sólidos del líquido. Al sedimentarse, los sólidos más pesados se hunden en el fondo. El agua limpia se retira de la parte superior. El lodo espesado tiene ahora un mayor porcentaje de sólidos, normalmente 50-60% en peso. Se bombea desde el fondo para su posterior procesamiento.
Algunos minerales de oro son refractarios. Son difíciles de procesar con la lixiviación normal con cianuro. Esto se debe a que los minerales sulfurosos encapsulan las partículas de oro. Para solucionar este problema, es necesaria una etapa de preoxidación. Ésta descompone los minerales de sulfuro y expone las partículas de oro a la etapa de lixiviación. Existen varios métodos de preoxidación:
* Oxidación a presión: El lodo espesado se bombea al autoclave. Se enfrenta a alta presión (20-50 bares) y alta temperatura (180-225°C) con oxígeno. Esto acelera la oxidación de los minerales de sulfuro, liberando el oro encapsulado.
* Biooxidación: Bacterias como Thiobacillus ferrooxidans oxidan los minerales sulfurosos. Las bacterias se añaden al lodo espesado. Metabolizan los sulfuros, liberando partículas de oro. Se produce a 40-45°C y pH 1,5-2,5.
* Asado: El lodo espesado se seca y se calienta a 500-700°C con aire presente. El calor hace que los sulfuros se oxiden y liberen oro. Sin embargo, la tostación es menos habitual por motivos medioambientales y de coste energético.
La elección del método de preoxidación depende de las características del mineral, de la tecnología disponible y de factores económicos. Tras la preoxidación, el mineral está listo para la lixiviación con cianuro.
Lixiviación con cianuro
La lixiviación con cianuro es el método más utilizado para extraer oro del mineral. En esta etapa, el lodo de mineral preoxidado se mezcla con una solución débil de cianuro de sodio (alrededor de 0,01-0,05% NaCN) en grandes tanques llamados tanques de lixiviación. El cianuro reacciona con las partículas de oro expuestas para formar un complejo oro-cianuro estable y soluble en agua. La reacción es la siguiente
4Au + 8NaCN + O2 + 2H2O → 4Na[Au(CN)2] + 4NaOH.
Hay varios factores que influyen en la eficacia de la lixiviación:
Tamaño de las partículas: Las partículas de oro más pequeñas tienen más superficie. La lixiviación es más rápida.
Concentración de cianuro: Más cianuro puede acelerar la lixiviación. Pero una cantidad excesiva es costosa y perjudicial para el medio ambiente.
Nivel de pH: El intervalo ideal es 10,5-11,5. Se añade cal para mantener los purines alcalinos.
Temperatura: Temperaturas más altas, en torno a 20-30°C, favorecen la lixiviación. Pero el calor excesivo utiliza más cianuro y provoca pérdidas de oro.
Oxígeno: Es fundamental que haya mucho oxígeno. Se añade agitando el lodo o inyectando aire/peróxido.
El proceso de lixiviación puede durar entre 24 y 72 horas. Depende de factores como el tamaño de las partículas, la concentración de cianuro, el nivel de pH, la temperatura y la disponibilidad de oxígeno, así como de las características específicas del propio mineral. Una vez finalizada la lixiviación, la solución preñada que contiene el oro se separa del material sólido de desecho (llamado estéril). Esto se hace mediante decantación o filtración en contracorriente. La solución preñada pasa a la fase de recuperación del oro. Los residuos se almacenan en una instalación especial o se tratan para eliminar los restos de cianuro antes de eliminarlos adecuadamente.
Adsorción y elución
La solución preñada del proceso de lixiviación con cianuro que contiene el complejo oro-cianuro disuelto se hace pasar por columnas rellenas de carbón activado. El carbón activado es muy bueno para adsorber selectivamente el complejo oro-cianuro de la solución. A medida que la solución preñada fluye a través de las columnas, el oro se adhiere progresivamente a la superficie del carbón activado, mientras que la solución que sale por el otro extremo es ahora estéril (sin oro).
Una vez que el carbón activado está cargado de oro, se retira de las columnas de adsorción y se somete a un proceso denominado elución para eliminar el oro. El carbón cargado se trata con una solución cáustica caliente (90-120°C) que contiene 1-2% de hidróxido de sodio (NaOH) y 0,1-0,2% de cianuro (NaCN). Esta solución de eluato elimina eficazmente el oro del carbón activado, produciendo una solución de oro de alto grado. A continuación, el carbón despojado se reactiva calentándolo en un horno a 600-800°C antes de enviarlo de nuevo al circuito de adsorción para su reutilización.
Electroobtención y fundición
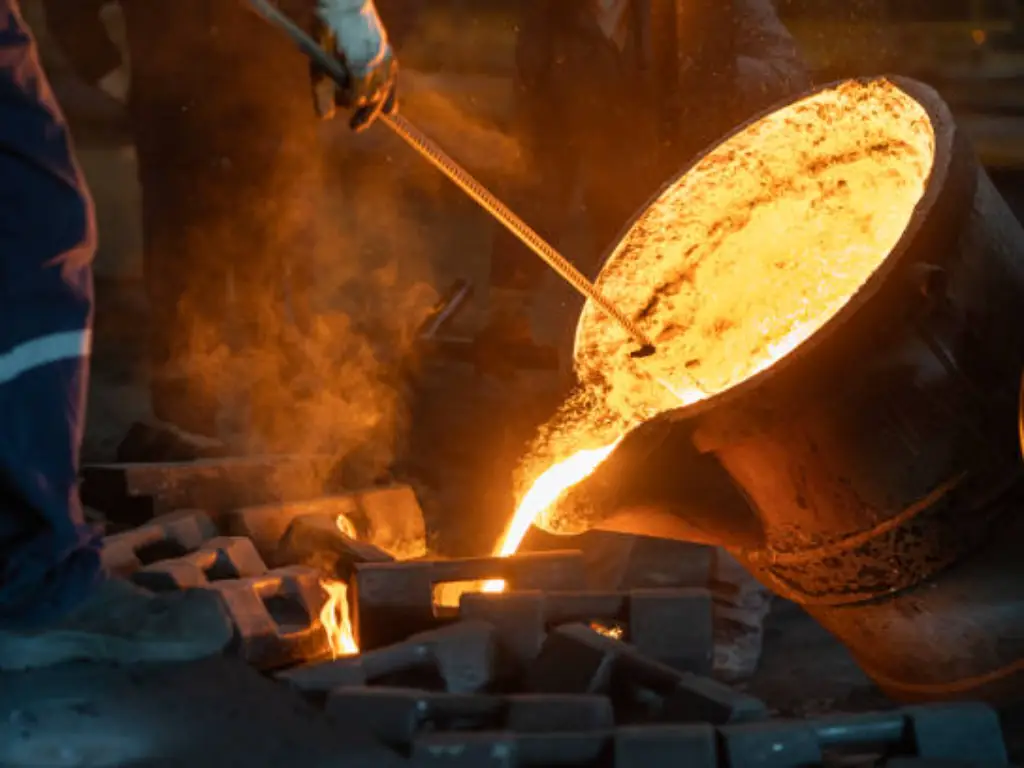
La solución de oro de alta ley procedente de la elución pasa a las celdas de electroobtención. Se trata de contenedores especiales en los que una corriente eléctrica hace que el oro se adhiera a cátodos hechos de lana de acero o malla de acero inoxidable. Los iones de oro se convierten en oro metálico y se depositan en los cátodos.
Cada cierto tiempo, los cátodos bañados en oro se extraen de las celdas de electroobtención y el lodo aurífero se raspa, se filtra y se seca.
A continuación, el lodo de oro seco se introduce en un horno de fundición calentado a más de 1.064 °C, el punto de fusión del oro. Cuando está tan caliente, el oro se funde y se separa de las impurezas que puedan quedar, como la plata o el cobre. El oro fundido se vierte en moldes para fabricar lingotes doré con una pureza aproximada de 90-95%.
A continuación, estos lingotes doré se envían a una refinería. Allí, se purificarán aún más hasta alcanzar el nivel deseado, normalmente 99,99% o una pureza superior. Después, el oro está listo para venderse o transformarse en productos.
Refinado
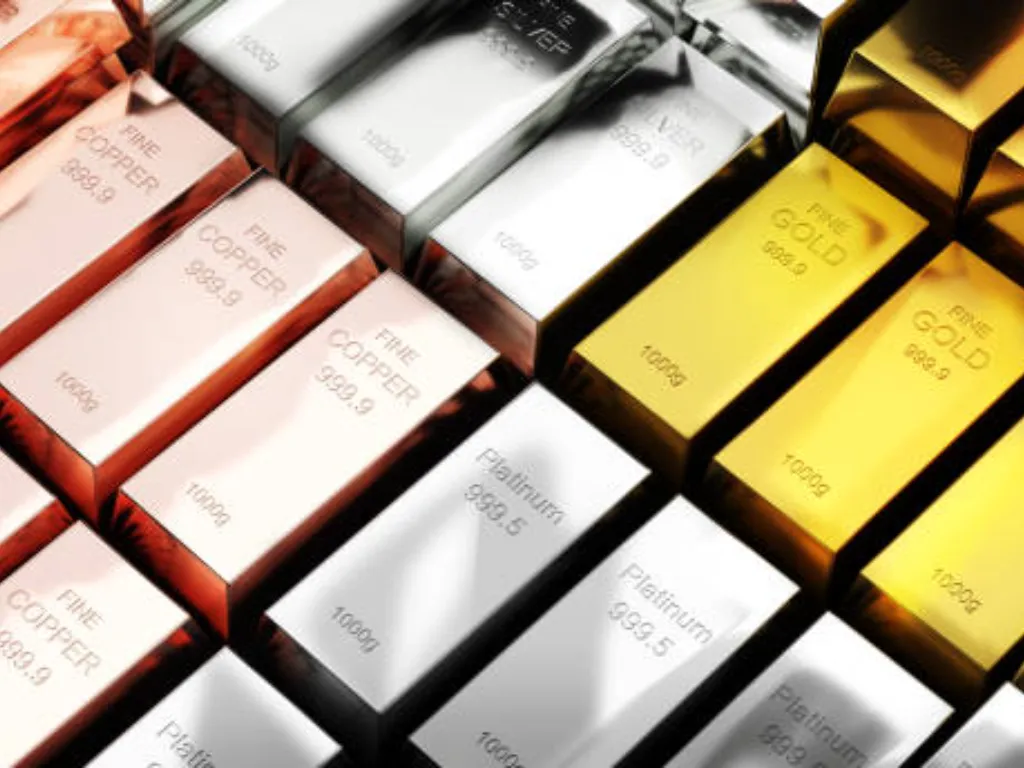
Los lingotes de oro doré de la etapa de fundición se someten a un proceso de refinado para alcanzar el nivel de pureza deseado, normalmente 99,99% o superior. Un método de refinado habitual es la cloración, en la que se funden las barras doré y se hace burbujear gas cloro a través del metal fundido. El cloro reacciona con impurezas como la plata, formando compuestos de cloruro que flotan en la superficie y se eliminan. A continuación, el oro purificado se vierte en moldes para producir barras de gran pureza.
Otro método popular es la electrólisis, también conocida como proceso Wohlwill. En este caso, el doré de oro se disuelve en una solución de cloruro y se aplica una corriente eléctrica para depositar el oro puro en un cátodo. Las impurezas permanecen en la solución o forman un lodo en el fondo de la célula electrolítica. La electrólisis puede producir oro con una pureza de hasta 99,99%. Tras el refinado, estos lingotes de oro de gran pureza están listos para la venta o para su transformación en diversos productos de oro.
Gestión de residuos
Los estériles son los trozos de roca finamente molidos y los restos químicos del proceso de extracción de oro, y deben manipularse adecuadamente para minimizar los daños al medio ambiente. Estos materiales suelen guardarse en presas o balsas de estériles, que son estructuras especialmente diseñadas para impedir que el agua y los sedimentos contaminados salgan a los alrededores. Las empresas productoras de oro que se preocupan por ser responsables utilizan diferentes estrategias para asegurarse de que gestionan los residuos de forma segura y eficaz.
Una estrategia importante consiste en utilizar diques de estériles con un revestimiento especial para evitar que el agua contaminada se filtre en el sistema de aguas subterráneas. También se utilizan sistemas de tratamiento del agua para eliminar los contaminantes de las aguas residuales antes de verterlas o reciclarlas en el circuito de tratamiento. Otro método consiste en eliminar los estériles en pilas secas, donde los estériles se secan y se compactan para darles una forma estable. Esto reduce el riesgo de rotura de presas y ocupa menos espacio para la instalación de almacenamiento de estériles. La recuperación y rehabilitación de las instalaciones de almacenamiento de estériles son también partes muy importantes de la gestión responsable de estériles. Esto significa asegurarse de que el terreno vuelve a un estado estable y productivo una vez finalizadas las operaciones mineras.
Equipos necesarios para el tratamiento del oro
El procesamiento del oro requiere un montón de equipos especializados para garantizar que la extracción y el refinado de este metal precioso se realicen de forma eficiente y eficaz. Estos son algunos de los principales equipos utilizados en el procesamiento del oro:
* Trituradoras y molinos: Se trata de trituradoras de mandíbulas, trituradoras de cono, trituradoras de impacto, molinos de bolas y molinos de barras. Sirven para triturar y moler el mineral de oro hasta el tamaño que queramos.
* Equipos de concentración por gravedad: Se trata de mesas vibratorias, plantillas, espirales y concentradores centrífugos. Se utilizan para separar las partículas de oro del mineral en función de su densidad en comparación con el resto del material.
* Espesantes y clarificantes: Se utilizan para separar los trozos sólidos del líquido de la pasta y para aumentar la densidad de la pulpa (que es la cantidad de material sólido que hay en el líquido).
* Tanques de lixiviación: Se trata de grandes cubas donde el mineral triturado y molido se mezcla con la solución de cianuro para disolver el oro.
* Columnas de adsorción y elución: Se utilizan para extraer el oro de la solución preñada (el líquido con el oro disuelto) mediante carbón activado y, a continuación, para eliminar el oro del carbón cargado.
* Células de electroobtención: Utilizan una corriente eléctrica para hacer que el oro se deposite en los cátodos.
* Hornos de fundición: Se utilizan para fundir el lodo aurífero y producir barras de oro doré.
* Equipos de refinado: Dependiendo de cómo se refine el oro, se pueden utilizar reactores de cloración, celdas electrolíticas u hornos de proceso Miller para producir lingotes de oro de gran pureza.
Otros métodos de beneficio del oro
Además de los pasos habituales para procesar el oro, existen otras formas de extraer oro de los minerales, dependiendo de las características específicas del mineral y de si el proceso tiene sentido desde el punto de vista económico. Estos métodos incluyen:
Oro CIL (carbono en lixiviación):
La CIL de oro es un proceso que lixivia y adsorbe el oro del mineral al mismo tiempo en una serie de tanques agitados que contienen solución de cianuro y carbón activado.
Oro PIC (Carbono en pulpa):
El CIP del oro es bastante similar al proceso CIL, pero el oro se adsorbe después de la etapa de lixiviación. En este método, la solución con el oro se traslada a tanques que contienen carbón activado.
Oro Pila Lixiviación:
La lixiviación en pilas es un proceso que funciona bien para los minerales de oro de baja ley. En este método, el mineral se apila en una plataforma que no gotee y, a continuación, se rocía una solución de lixiviación sobre la pila para disolver el oro.
Flotación:
La flotación es un proceso utilizado para tratar minerales auríferos que tienen muchos sulfuros que flotan fácilmente. En este método, los minerales que contienen oro se separan de la roca estéril (ganga) adhiriéndose a las burbujas de aire y flotando en la superficie.
Estos métodos alternativos de beneficio del oro pueden utilizarse en casos específicos en los que las características del mineral y los factores económicos los convierten en una mejor opción que las fases convencionales de tratamiento del oro.
Conclusión
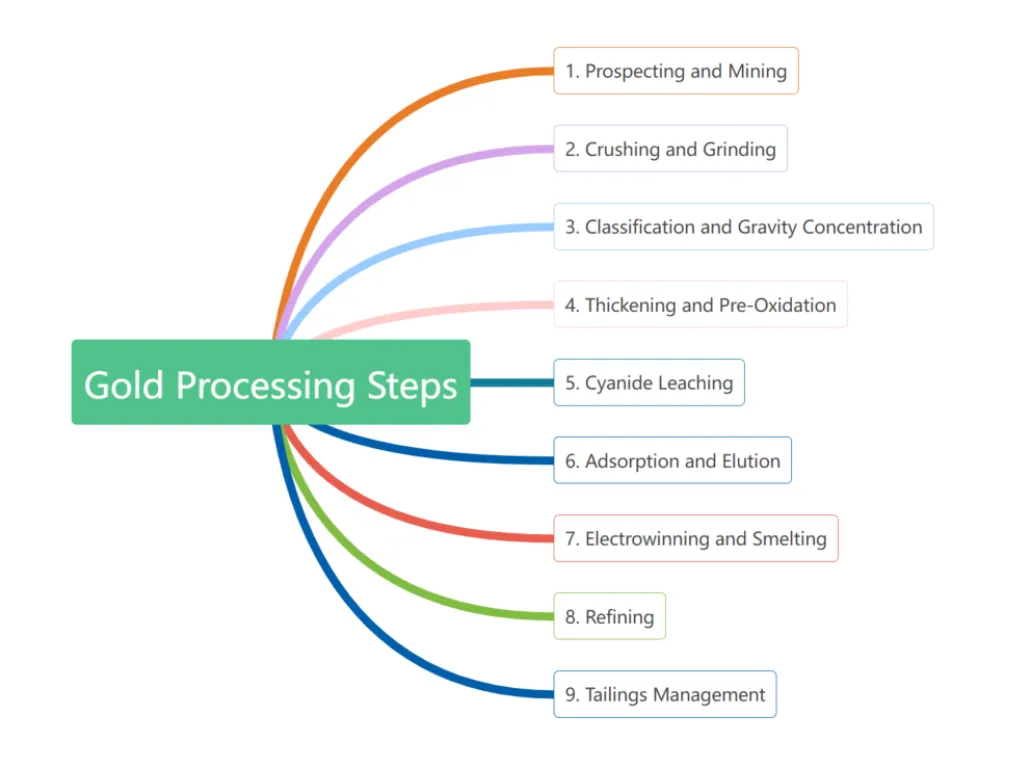
De principio a fin, tratamiento del oro incluye una serie de pasos y operaciones que requieren conocimientos, equipos y procedimientos extraordinarios. Todo comienza con la prospección y la minería, en ese momento se mueve a la refinación y la gestión de los relaves (los materiales adicionales). En el caso de que usted está dentro de la industria de la minería de oro, es super imprescindible para conseguir que todos estos pasos. ¿Por qué? Porque marca la diferencia, optimizas las formas de extracción y refinado, minimizas el efecto sobre el medio ambiente y aseguras sin lugar a dudas que estás creando este valioso metal de forma capaz.
Más información sobre JXSC
En el caso de que usted es agudo para memorizar más aproximadamente oro procesamiento de pasos y quiere descubrir los arreglos más excelentes para sus operaciones mineras, que sin duda debe comprobar hacia fuera JXSC. Son un pionero de confianza dentro de la industria, con más de 35 mucho tiempo de experiencia y una proximidad en todo el mundo. JXSC ofrece una amplia gama de productos y servicios, incluyendo equipos de última generación, planes de gestión y asistencia especializada. Conocen a la perfección todos los aspectos de la preparación del oro, desde la trituración y el machaqueo hasta la separación por gravedad, la flotación y el refinado. Al asociarse con JXSC, optimizará sus operaciones de preparación de oroAumente la eficacia y maximice sus beneficios.