- Inicio
- Blog
- Información sobre el equipo
- Anatomía de un molino de bolas: Diagrama detallado de un molino de bolas
Introducción a los molinos de bolas
Los molinos de bolas son una parte importante del engranaje de la industria minera y de tratamiento de minerales, donde se utilizan en la fase de trituración del proceso de machaqueo. La conminución consiste en reducir el tamaño de los materiales sólidos, y consta de dos etapas principales: la trituración y la molienda. La trituración es la fase primaria en la que las partículas grandes se reducen a otras más pequeñas que pueden introducirse en los molinos, incluidos los de bolas. La molienda, que es la segunda y última etapa, reduce el tamaño de las partículas en partículas aún más finas con la ayuda de fuerzas de impacto y atrición.
Junto a la industria minera, los molinos de bolas también se utilizan en distintos sectores, como la producción de cemento, para moler clinker y otras materias primas; la fabricación de cerámica, para moler y mezclar polvos cerámicos, y la producción de pintura, para dispersar y homogeneizar pigmentos y otros ingredientes. Los múltiples usos de los molinos de bolas son la principal razón por la que son tan importantes en muchas industrias. Para una explicación detallada de los molinos de bolas, haga clic en ¿Qué es un molino de bolas y cómo funciona? Explicación detallada.
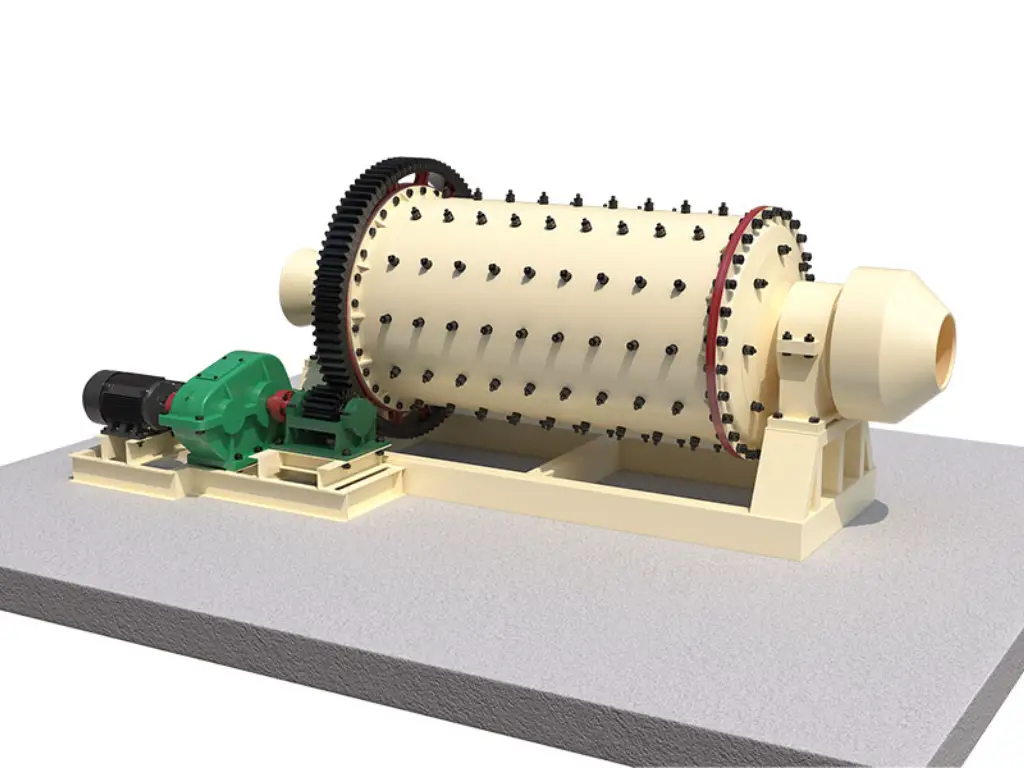
Principio de funcionamiento de los molinos de bolas
Mecanismos de fragmentación: impacto y desgaste
La acción de moler en un molino de bolas se consigue mediante dos mecanismos primarios de fragmentación: la atrición y el impacto. La atrición se produce cuando los medios de molienda (bolas o guijarros duros) chocan entre sí y con el material que se está moliendo. Esto conduce a la fragmentación de la sustancia en trozos de menor tamaño. Por el contrario, la atrición es un proceso que resulta del rozamiento y el cizallamiento de las partículas entre sí y con la carcasa del molino, lo que provoca una mayor reducción de tamaño.
Niveles de energía de los medios de molienda
Los niveles de energía de las bolas de molienda son muy importantes en el funcionamiento del molino de bolas. Durante la rotación de la carcasa, las bolas se elevan por los laterales del molino hasta un punto en el que vuelven a caer al fondo del molino. Cuanto más se elevan las bolas y con más fuerza vuelven a caer sobre el material molido, más energía se transmite al material. Hay parámetros como el diámetro, el volumen y la velocidad de las bolas que afectan al nivel de energía.
Rotación de la carcasa y la placa base
La rotación de la carcasa del molino de bolas es un elemento muy importante para el proceso de molienda. La carcasa suele estar montada sobre un eje horizontal y gira a una velocidad determinada denominada velocidad crítica. La velocidad crítica es la velocidad de rotación a la que la fuerza centrífuga iguala a la fuerza gravitatoria, haciendo que los medios de molienda se adhieran a la carcasa del molino en lugar de caer. Por lo general, los molinos de bolas funcionan a una velocidad crítica del orden de 50-90% para obtener los mejores resultados de molienda posibles.
Funcionamiento en molinos de bolas
Funcionamiento en cascada a distintas velocidades
El funcionamiento de un molino de bolas puede clasificarse en tres modos distintos en función de la velocidad de rotación:
Baja velocidad: bolas de molienda rodantes sin vuelo
A bajas velocidades, las bolas de molienda ruedan por el fondo del molino sin ser levantadas por los laterales. Este modo se caracteriza por fuerzas de bajo impacto y es ideal para aplicaciones de molienda ligera o mezclado.
Modo mixto (Cascade modo de movimiento): balanceo parcial y vuelo parcial
Al aumentar la velocidad de rotación, las bolas se elevan por las paredes del molino y alcanzan cierta altura antes de caer. Este modo de movimiento mixto, también conocido como cascada, es el más utilizado en los molinos de bolas, ya que proporciona un equilibrio entre las fuerzas de impacto y atrición.
Alta velocidad: movimiento circular de las bolas sin caída
A velocidades muy elevadas, las bolas se desplazan por la circunferencia del molino sin caer. Este método, comúnmente llamado centrifugado, no es aplicable a la molienda, ya que no se produce impacto ni atrición.
Importancia de la velocidad de rotación
La velocidad de rotación del molino de bolas es un parámetro crítico que determina la eficacia de la molienda y la calidad del producto final. La velocidad óptima varía en función del diámetro del molino, el tamaño y la densidad de las bolas y el material molido. Funcionar a la velocidad adecuada garantiza que las bolas de molienda transfieran la máxima cantidad de energía al material y no provoquen un desgaste excesivo de los componentes del molino.
Alimentación y descarga de material
Los molinos de bolas pueden funcionar en modo discontinuo o continuo. En el modo discontinuo, se carga una cantidad determinada de material en el molino, se muele durante un periodo específico y luego se descarga. En el modo continuo, el material se introduce continuamente en un extremo del molino y se descarga por el otro. Los mecanismos de alimentación y descarga, que incluyen canaletas, tolvas y rejillas, son el componente más importante para tener un flujo constante y controlado del material a través del molino.
Velocidad óptima para la máxima reducción de tamaño
Para obtener la máxima reducción del tamaño de las partículas, los molinos de bolas deben funcionar a su velocidad óptima. Esta velocidad se sitúa normalmente entre 50-90% de la velocidad crítica, que depende de la aplicación y del material que se vaya a moler. A la velocidad óptima, los medios de molienda caen por la carcasa del molino en el punto más alto, generando así la máxima fuerza de impacto y el proceso de molienda se vuelve eficiente.
Construcción de molinos de bolas
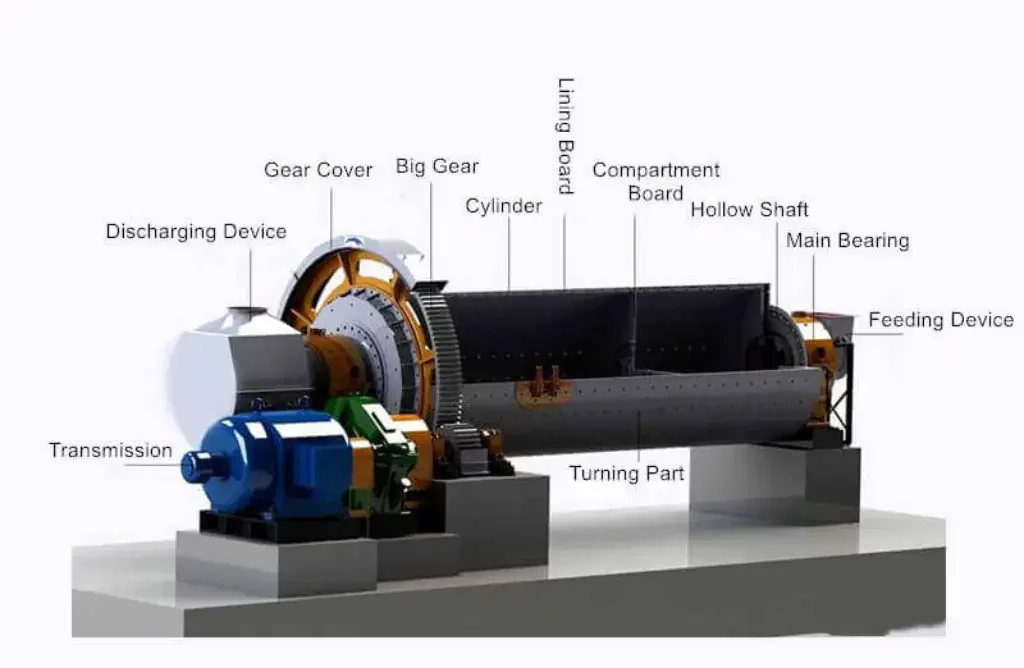
Un molino de bolas consta de tres componentes principales: la carcasa, los medios de molienda (bolas o guijarros) y el motor. El armazón es un tubo metálico hueco por dentro y está revestido de materiales resistentes al desgaste, como acero al manganeso o caucho. Los medios de molienda pueden ser de acero de alto contenido en cromo, cerámica o caucho, pero la elección depende de la aplicación. Las bolas de acero son el tipo más común de bolas de molienda y pueden adquirirse en distintos tamaños, desde 10 mm hasta 150 mm de diámetro. El tamaño de las bolas se basa en el tamaño de la materia prima y el tamaño deseado del producto final. Las bolas de cerámica y caucho se utilizan en procesos en los que las bolas de acero son inadecuadas para la contaminación, por ejemplo, en la producción de materias primas cerámicas y pintura.
El revestimiento de la carcasa es una pieza necesaria que se encarga de proteger la carcasa del molino del desgaste inducido por el impacto y la abrasión de los medios de molienda. Los materiales de revestimiento más utilizados son el acero al manganeso, el caucho y la cerámica. El acero al manganeso es famoso por su alta resistencia al desgaste debido a su amplia aplicación en minería y procesamiento de minerales. El revestimiento de caucho se utiliza para la molienda en húmedo y es capaz de reducir el nivel de ruido. Los revestimientos cerámicos se utilizan en aplicaciones de alta temperatura o cuando la contaminación de los revestimientos metálicos es un problema. La rotación del molino es accionada por el motor, cuya potencia viene determinada por el tamaño del molino y la capacidad de molienda.
Los molinos de bolas pueden ser tan pequeños como los de laboratorio o tan grandes como los industriales, con un diámetro de hasta 8 m. La capacidad del molino viene dictada por su volumen. El volumen depende tanto del diámetro como de la longitud. Por lo general, la relación longitud-diámetro del molino, conocida como relación L/D, se sitúa entre 0,5 y 3. Los molinos más cortos se utilizan para triturar materiales gruesos, mientras que los más largos se emplean para moler materiales finos. Las dimensiones y la capacidad del molino de bolas se determinan en función de la aplicación y el rendimiento requerido.
Descubra el funcionamiento de estas piezas en Dominar el método de fresado con bolas: Su guía completa.
Factores determinantes de la eficiencia de los molinos de bolas
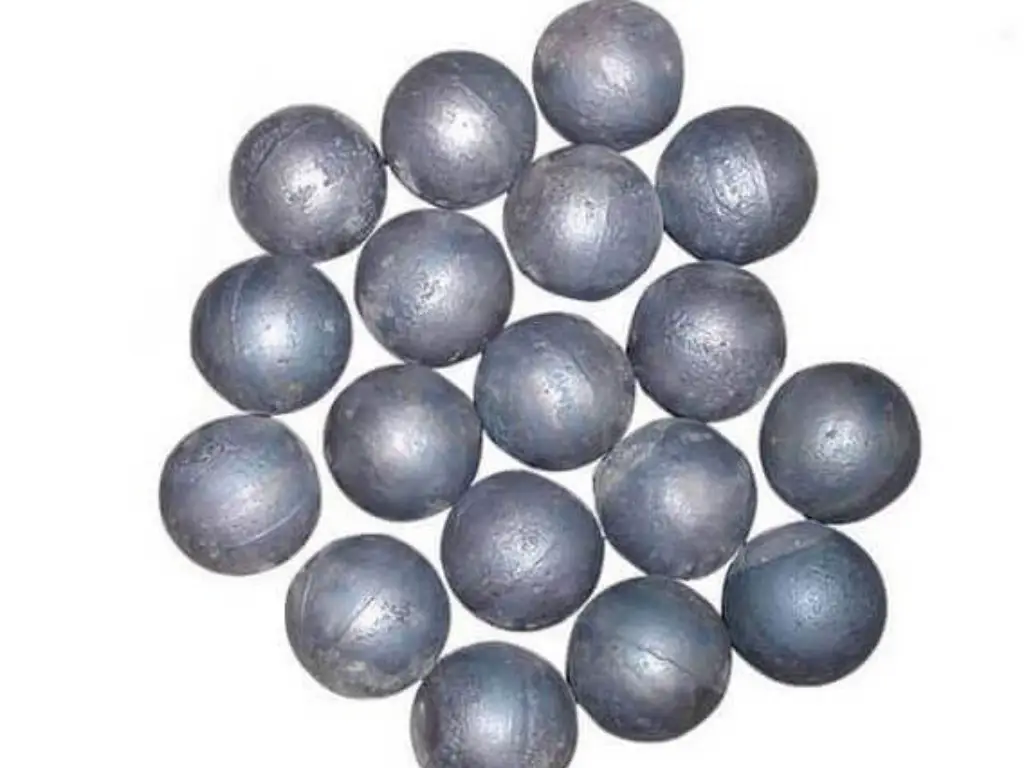
Tiempo de residencia del material
El tiempo de residencia, que es el periodo de tiempo que el material permanece dentro del molino, es el principal parámetro que influye en la eficacia del molino. Un periodo de funcionamiento más largo permite una mayor interacción entre las bolas de molienda y el material, lo que se traduce en una molienda del material en partículas más finas. Sin embargo, la prolongación del tiempo de permanencia puede provocar un exceso de molienda y la reducción de la capacidad, así como un consumo extra de energía.
Tamaño, densidad y número de bolas
La eficacia de la molienda depende de factores como el tamaño, la densidad y el número de bolas del molino. Cuanto más grandes y densas sean las bolas, mayor será el aporte de energía y se conseguirá una molienda más rápida. Sin embargo, emplear bolas demasiado grandes puede reducir la molienda y aumentar el desgaste del revestimiento interior del molino. El número de bolas debe ajustarse para garantizar que no se pierda el objetivo ni sean demasiado densas.
Dureza de las bolas y del material
La selección de la dureza de las bolas de molienda del molino, así como el tipo de material que se muele, influyen mucho en la eficacia del molino de bolas. La dureza de las bolas de molienda debe ser superior a la del material a moler para obtener un buen dimensionamiento. Emplear bolas de la dureza adecuada es la clave para regular el desgaste del molino y el consumo de energía, así como para proteger el revestimiento del molino.
Velocidad y nivel de alimentación
La velocidad de alimentación, que es la velocidad a la que se introduce el material en el molino, y el nivel de alimentación, que es el nivel de material dentro del molino, son los dos factores principales que influyen en la eficacia del molino de bolas. Que la velocidad de alimentación esté en el nivel óptimo y bajo control garantiza que el molino esté en su mejor nivel de funcionamiento sin sobrecargarse. El nivel de alimentación debe mantenerse en torno al 30-50% del volumen del molino de bolas para crear espacio suficiente para que las bolas de molienda se muevan e impacten contra el material.
Velocidad de rotación del cilindro
Como ya se ha mencionado, la velocidad de rotación del cilindro del molino de bolas es un elemento clave para la eficacia del proceso de molienda. Los componentes del molino están sometidos a un desgaste mínimo a medida que se optimiza la velocidad del molino para conseguir la máxima energía impartida por los medios de molienda. La velocidad óptima puede variar en función del diámetro del molino, el tamaño y la densidad de las bolas y el material molido.
Proceso de trabajo de los molinos de bolas
Fase inicial: partículas aplanamiento y cambio de forma
Durante la etapa inicial del proceso de molienda, las partículas del material de alimentación se aplastan y su forma cambia debido a la fuerza de impacto de los medios de molienda. Esta es la etapa en la que la mayoría de las partículas de gran tamaño se convierten en trozos más pequeños.
Etapa intermedia: cambios significativos en comparación con la etapa inicial
Las partículas sufren cambios considerables a medida que avanza el proceso de molienda, lo que contrasta con la fase inicial. Las partículas adquieren una forma más esférica y uniforme, y el ritmo de reducción de tamaño es más lento. Esta etapa se produce por las fuerzas de impacto y atrición, lo que da lugar a un tamaño de partícula más fino.
Etapa final: partículas reducción de tamaño y microestructura homogénea
En la fase final del proceso de molienda, las partículas se reducen a su tamaño final y se obtiene una microestructura homogénea. Las partículas son ahora muy finas y uniformes, con una estrecha distribución de tamaños. En esta etapa predominan las fuerzas de atrición, ya que las partículas son demasiado pequeñas para ser descompuestas eficazmente por impacto propiamente dicho.
Etapa de finalización: estructura metaestable extremadamente deformada.
Las partículas han sufrido mucha deformación y han alcanzado un estado metaestable al final del proceso. Esta etapa se conoce como etapa de alta deformación y defectos reticulares en las partículas, y puede asociarse a una mayor reactividad y propiedades únicas. Esta última etapa suele ser necesaria en aplicaciones como la aleación mecánica, donde el objetivo es obtener microestructuras y propiedades únicas del material.
Ventajas de los molinos de bolas
1. Puede tratar materiales difíciles como minerales duros y arcillas blandas.
2. Para obtener partículas de pequeño tamaño, el proceso de molturación puede producir partículas submicrónicas.
3. Este equipo funciona continuamente, lo que garantiza un alto rendimiento y bajos tiempos de inactividad.
4. La capacidad de controlar el tamaño final del producto simplemente ajustando los parámetros de funcionamiento es la característica destacable de esta técnica.
5. Asegurar una mezcla y homogeneización adecuadas para un resultado final uniformemente disperso.
6. Sus ventajas son un diseño sencillo y un mantenimiento mínimo con sustitución de las piezas desgastadas.
Desventajas de los molinos de bolas
1. 2. Alto consumo de energía, con una gran cantidad de calor y ruido como resultado del desperdicio de energía.
2. Posibilidad de contaminación de los medios de molienda y los materiales de revestimiento.
3. El riesgo de sobremolienda en ausencia de control, que da lugar a partículas ultrafinas indeseables.
4. Incapacidad de elegir para controlar un único tamaño de partícula, lo que da lugar a una gama de distribución de tamaños.
5. Funcionamiento ruidoso de las trituradoras, sobre todo a velocidades más altas o con bolas de trituración más grandes.
Conclusión
Para terminar, la anatomía de una industria molino de bolas y su intrincado diagrama son vitales para el rendimiento óptimo del molino y el buen funcionamiento de los procesos de molienda. Mediante una cuidadosa evaluación de los principios de funcionamiento, la construcción, el funcionamiento y los factores determinantes de la eficiencia del molino, los operarios e ingenieros pueden tomar decisiones bien fundadas para garantizar la máxima eficiencia de molienda y la obtención de productos de alta calidad en muchos campos, como la minería, el procesamiento de minerales, la cerámica y las pinturas.