- Home
- Blog
- Equipment Info
- What is Secondary Crushing? Basic Knowledge Should Know
How Secondary Crushing Works?
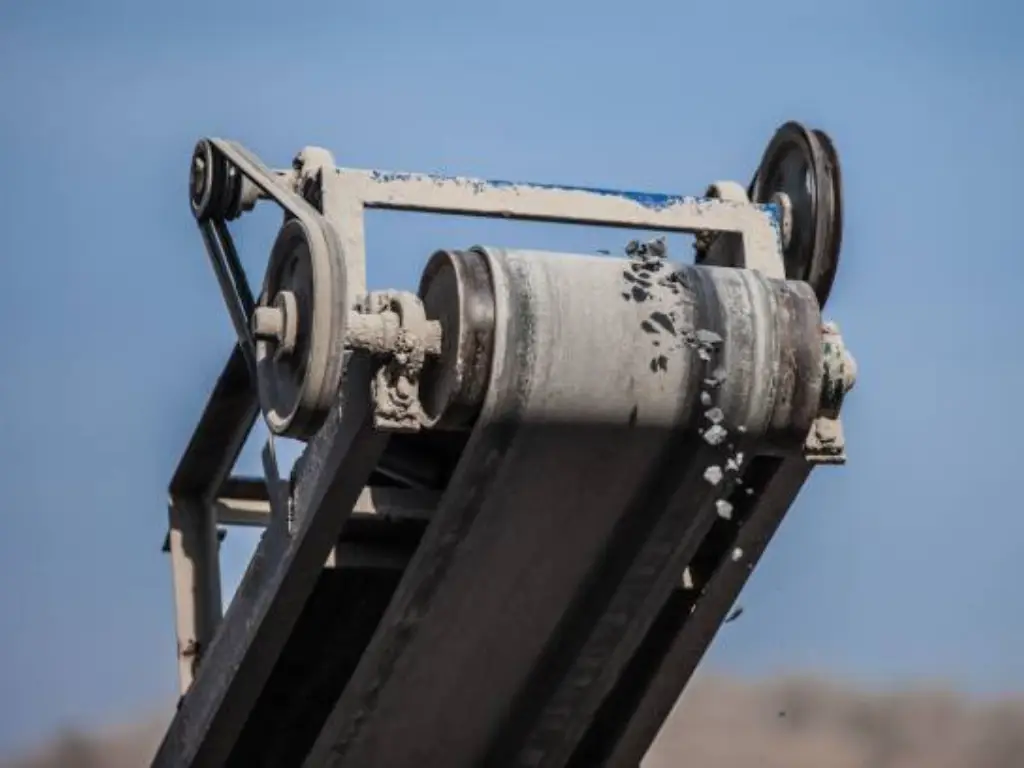
When material enters a crusher, it’s the crusher’s design—compression, impact, or shear—that decides how it’s reduced. Cone and gyratory crushers compress materials to break them into the needed size. Impact crushers, meanwhile, use force to break materials into smaller bits. This step is vital. It not only decides how well the size is reduced but also affects the shape and quality of the final product.
The crushing process is carefully managed. Settings for feeding and discharging are adjusted precisely. The aim is to make material smaller and uniform, ideally between 10 and 50 mm. The target reduction ratio is usually between 3:1 and 7:1. Adjusting these settings right helps produce a finer output. This step is key for making the next stages more efficient.
The whole process relies on balancing the size of the crusher, the material reduction ratio, and the crusher type. This balance is crucial. It ensures secondary crushing prepares materials perfectly for the next steps. This phase is essential, whether for mining, making construction materials, or building roads. It shows how important careful planning is to achieve the right final product.
Comparing Primary, Secondary and Tertiary Crushing
Feature | Primary Crushing Stage | Secondary Crushing Stage | Tertiary Crushing Stage |
---|---|---|---|
Material Size Before | Up to 2 meters | 100-200 mm | 10-50 mm |
Material Size After | 100-200 mm | 10-50 mm | Less than 12 mm, often finer |
Reduction Ratio | 3:1 to 6:1 | 6:1 to 8:1 | Up to 10:1 or more |
Equipment Used | Primary Crusher: Jaw crushers, Gyratory crushers | Secondary Crusher: Cone crushers, Impact crushers, Gyratory crushers | Tertiary Crusher: Cone crushers, Roll crushers, Impact mills |
Purpose | Initial size reduction, handling of the largest rocks | Further size refinement, improvement in shape | Final refinement, precise sizing and shaping |
Types of Secondary Crushing Equipment
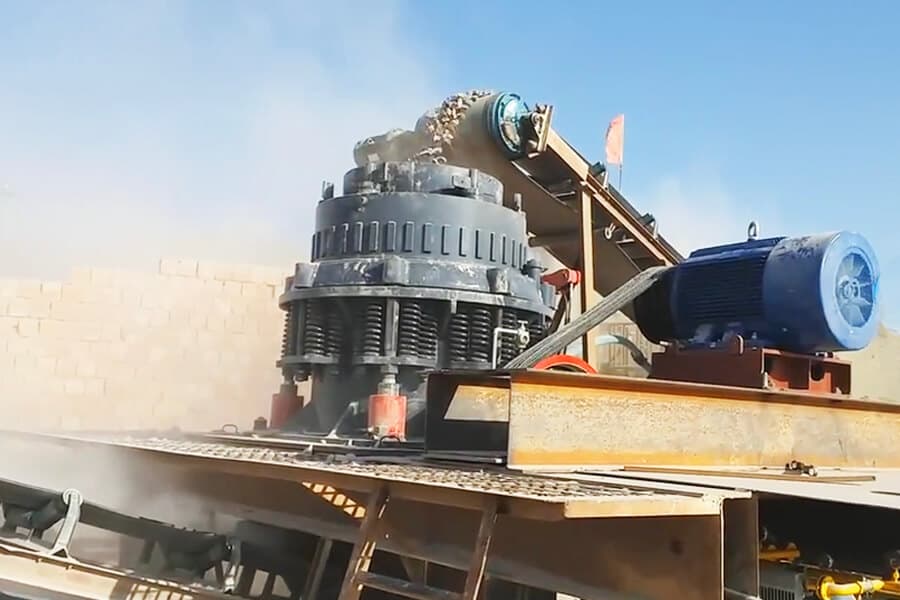
In the realm of secondary stage, several types of crushers stand out for their efficiency, versatility, and the quality of product they produce. Here’s a closer look at each:
1. Cone Crushers: These crushers stand out as one of the foremost conventional and favored choices for secondary crushing. Idealize for handling hard materials, they exceed expectations in making medium to fine molecule sizes.The process involves a dynamic cone and a static bowl working together. As the cone moves, it smashes the material between it and the bowl with compressive drive. Known for conveying reliable molecule sizes and shapes, cone crushers are favored for making totals utilized in making aggregates used in road construction and concrete.Discover detailed cone crusher visuals in Cone Crusher Diagram: A Simple Explanation.
2. Impact Crushers: These crushers use a strong force to break materials into pieces. They push materials against fast-spinning rotors, then the materials crash into metal blocks or plates. This action crushes the materials. Impact crushers work really well for softer stuff, like limestone, because of their ability to generate a more cubical or rounded end product. This is great for making things like asphalt or concrete, where you really care about the shape and size of the pieces.
3. Gyratory Crushers: Sharing similitudes with cone crushers, gyratory crushers moreover smash materials utilizing compression. What sets them separated is their steeper chamber and more forceful smashing activity, empowering them to handle exceptionally hard materials productively. These crushers are a go-to in secondary crushing scenarios that request tall throughput.
4. Horizontal Shaft Impact (HSI) Crushers: These crushers have a rotor that lies horizontally. They push materials to hit hard surfaces inside the crushing area. This makes the materials much smaller. HSIs are great for crushing softer to somewhat hard materials and are often used to recycle stuff.
What Should Consider When Choosing Secondary Crushers?
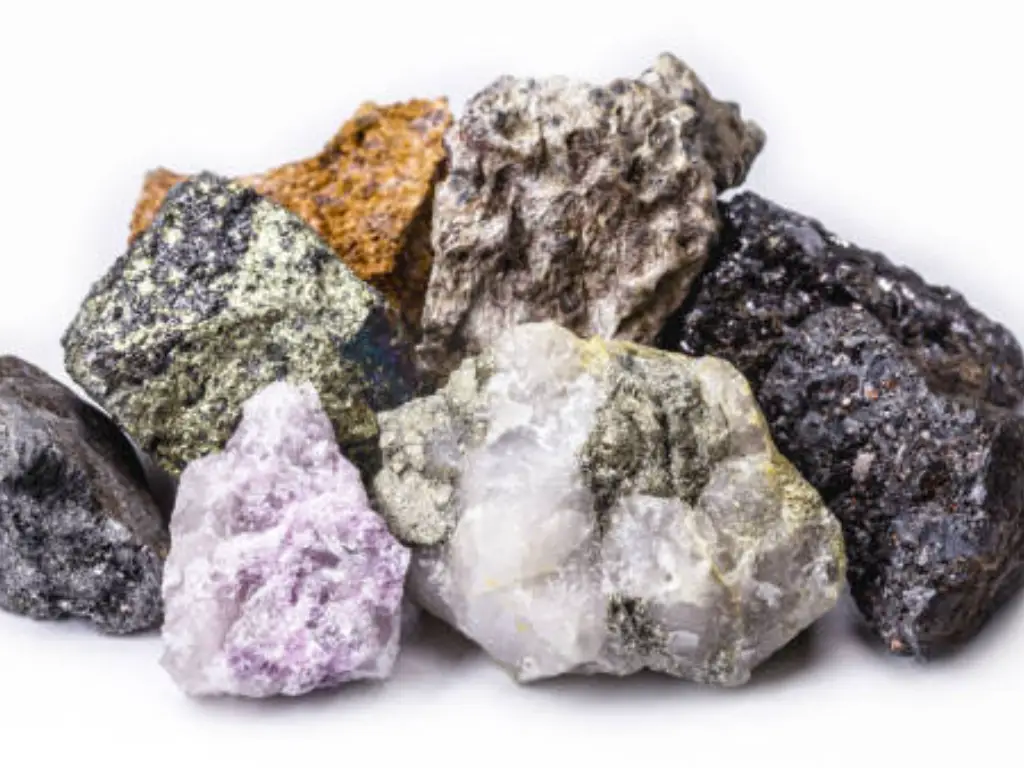