- Home
- Blog
- Equipment Info
- What is a Ball Mill and How Does It Work? An In-Depth Explanation
- mmldigi
What is a Ball Mill?
A ball mill is a kind of grinder that grinds and blends materials for the purpose of mineral processing, paint production, pyrotechnics, ceramics, and selective laser sintering. It works on the principle of impact and attrition: the balls are released from the top of the shell and then crush and grind the material to fine powders. The main secret of the desired product size is keeping control over critical speed, media loading, material characteristics, mill speed, liners and grinding media type of mill, circulating load, use of closed system, and operating conditions.
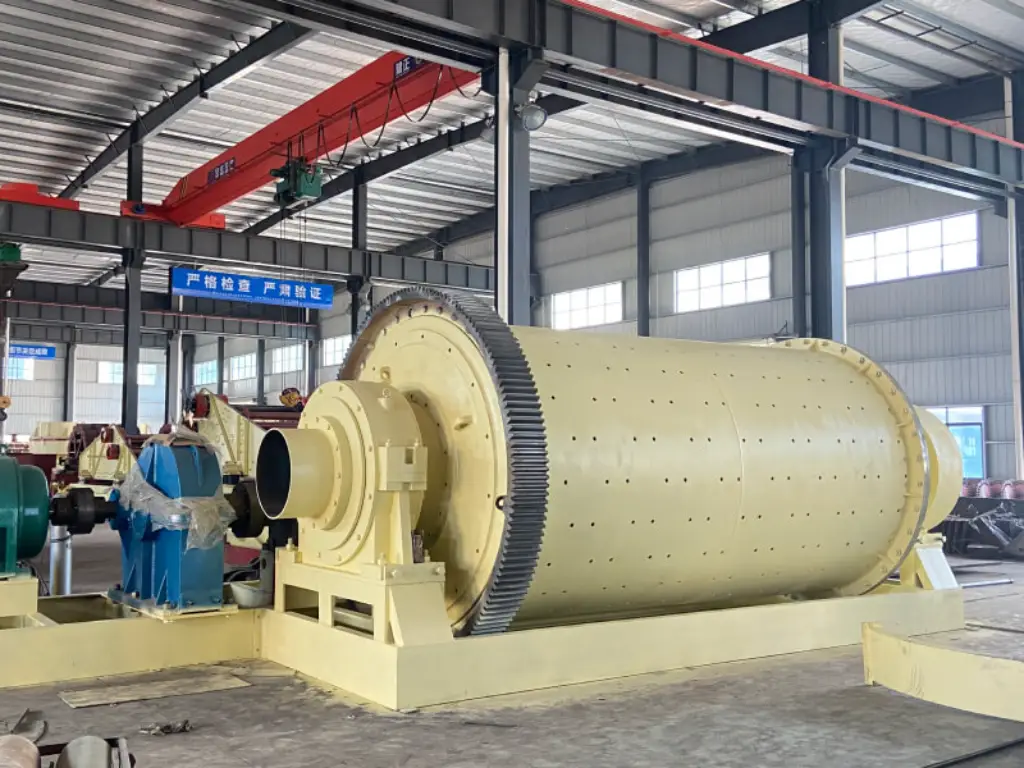
Components of a Ball Mill
A typical ball mill has a number of main components that function in unison to obtain the best performance of the ball mill. The cylindrical shell, which is typically made of steel or is lined with abrasion-resistant materials such as manganese steel, rotates on the horizontal axis. The drum diameter is partly filled with grinding media, such as steel balls, ceramic balls, or natural rocks, depending on the process and your specific needs. When the shell rotates, the grinding media falls and tumbles, thus combining the impact forces and attrition forces that are responsible for the fragmentation of the feed material.
Other essential components include feed inlet, discharge outlet, and trunnion bearings which support the shell on both ends. The drive system, which usually consists of an electric motor with gears or a belt drive, generates the desired rotation speed. Liner, e.g. lifter bar or wave liner, are put inside the shell to lift the grinding media and increase the grinding efficiency. Moreover, the control system supervises and controls different parameters, including the speed, feed rate, and power consumption, to ensure the ball mill works perfectly.
How Does Ball Mill Work?
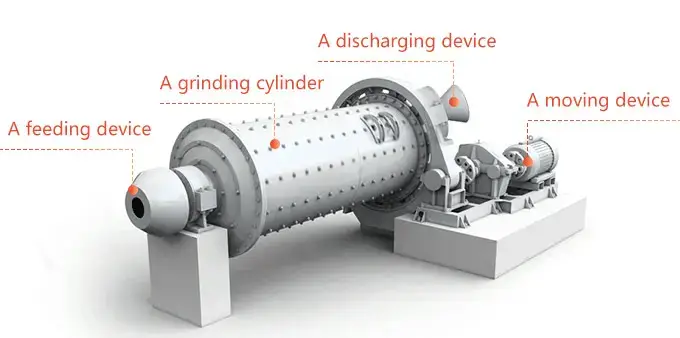
The working principle of a ball mill is based on the premise of impact and attrition. The rotation of the shell lifts the grinding media and then releases it to impact the feed material. This results in smaller particles of the ore particles. On the other hand, this process continues until the size of the ore particles reaches the desired size. The critical speed of a ball mill, which is the speed at which the centrifugal force equals the gravitational force, is directly related to the efficiency of fine grinding.
In a normal ball milling process, the material being milled is fed into the mill through the mill inlet. The turning shell lifts the grinding media and the material with it, and then drops them back down, which generates a cascading effect. The forces of impact and attrition created by the balls as they fall down, lead to the splitting of the material into finer particles. The material inside the mill is then discharged through the outlet with the aim to either refine it or to continue the process. The size reduction process continues until the particles get to the distribution of sizes that are desired.
For a detailed diagram and better understanding, see Anatomy of a Ball Mill: A Detailed Ball Mill Diagram.
Applications of Ball Mills

Ball mills are widely used in various industries due to their flexibility and their ability to treat a wide range of materials. Some of the key applications include:
● Mineral processing: Ball mills are one of the most common type of grinder in the mining industry, and their purpose is to grind ores, such as gold, copper, iron, and zinc, to the point where they are ready for further processing and extraction.
● Cement production: Ball mills are key equipment in the cement industry where clinker and other raw materials are ground to produce cement powder of the required fineness.
● Paints and pigments: The ball mill is a mechanical device used for blending and grinding pigments, fillers, and other additives to produce homogeneous paint formulations with the desired properties.
● Ceramics: In the ceramic industry, ball mills are utilized to grind and mix raw materials, i.e. clays, feldspar, and quartz to prepare them for shaping and firing.
● Pyrotechnics: In pyrotechnics, the ball mills are used for the mixing and grinding of chemicals, which are then used to make fireworks, flares, and other pyrotechnic devices.
● Selective laser sintering: In the additive manufacturing field, ball mills are employed for the purpose of preparing metal powders with the required particle size distribution for the selective laser sintering technique.
These are just a few of the numerous operations that can be done by grinding mills. They are an invaluable equipment that guarantees the correct grinding and blending of materials in different industrial settings.
Factors Affecting Ball Mill Grinding Efficiency
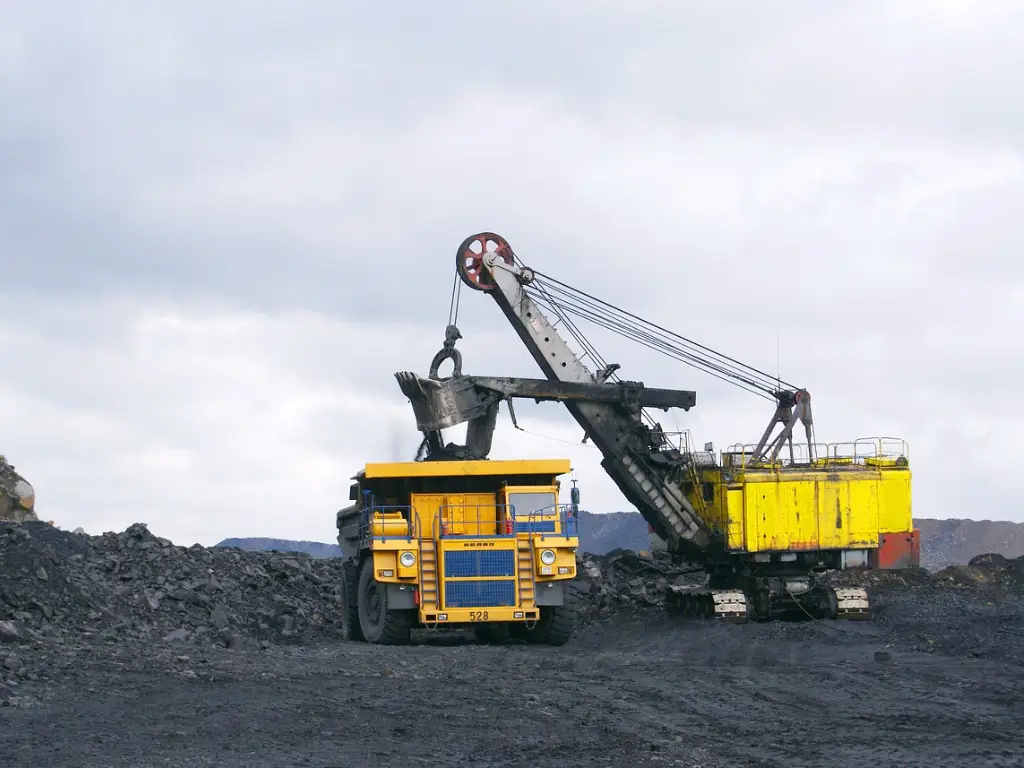
The ball mill grinding efficiency and effectiveness are all influenced by several factors. Recognizing and improving these factors is essential for attaining the required product quality and ensuring the high productivity of the mill. Let’s discuss some of the key factors:
● Critical Speed: Critical speed is the hypothetical speed at which the centrifugal force is equal to the gravitational force, and the grinding media starts sticking to the inner shell of the equipment instead of falling freely. Grinding at or close to critical speed of the mill yields a poorer grinding efficiency. The ball mills are mostly operated at 65-75% of the critical speed to attain the best outcomes.
● Media Loading: The type of media and its size as well as the amount of media are the other factors that affect the grinding efficiency. In this case, the media charge is estimated to be 30-50% of the mill volume. Using a greater number of small balls increases the surface area of grinding, hence speeding up the process. The media, however, will be in the mill and that will slow down the cascading and will not be productive.
● Material Characteristics: The features of the different materials like hardness, toughness, and abrasiveness determine the grinding process. The harder material take more energy and time to grind as compared to the softer material which is prone to over-grinding. The grinding efficiency is influenced by feed size and moisture content, which are the main factors as well.
● Liners and Grinding Media Type: The selection of right liners and grinding media that is one of the most important factors which affect the performance of grinding process. The selection of liners with the required profiles including for example wave liners or lifter bars, will result in the media being lifted and therefore will improve the cascading action. The type and size of the grinding media should be selected in order to be in agreement with the feed material properties and the target output particle size.
● Circulating Load: In the closed-circuit grinding systems, circulation load is the proportion of mill discharge that is returned to the mill for further grinding. In this case, the optimum circulating load is a prerequisite for achieving the required product size distribution and maximum grinding efficiency.
● Use of Closed System: The closed-circuit grinding, which means that the mill discharge is classified and the oversize particles are sent back to the mill, provides for a better control of the product size distribution and for reducing the over-grinding. Moreover, it allows higher output with the same or less energy consumption compared with open-circuit grinding.
● Operating Conditions: Such factors as the feed rate, pulp density, and grinding aids could be among the reasons for the grinding efficacy. The most critical factors in achieving stable mill operation and grinding performance are the rate of feed and pulp density, so their constancy and improvement should be ensured. The addition of grinding aids such as chemical substances can lower particle aggregation and therefore, enhance the grinding effectiveness.
By the means of the targeted assessment and improvement of these factors, you can reach the highest level of productivity and performance in grinding in your ball mill. It is mandatory to control and readjust these values on a regular basis to keep up the quality of the product and maximize the output of the mill. Learn about top ball mill manufacturers at Top 5 Ball Mill Manufacturers to Power Your Manufacturing Needs.
Wet vs. Dry Grinding: Which Method to Choose?
Factor | Wet Grinding | Dry Grinding |
---|---|---|
Material Properties | Suitable for sticky, high moisture content, or agglomerating materials | Preferred for moisture-sensitive materials or those requiring a dry final product |
Product Requirements | Produces finer and more uniform particles | Sufficient for coarser or less critical applications |
Downstream Processing | Suitable when the product can be easily dewatered or when a slurry is required | Preferred when the material needs to be dry for further processing |
Energy Efficiency | Consumes more energy due to additional requirements for pumping and classification | Generally more energy-efficient, as it eliminates the need for drying the product |
Environmental Considerations | Generates wastewater that needs treatment or disposal | Produces dust that requires effective collection and filtration systems |
Equipment Requirements | Requires additional equipment, such as pumps and classifiers | Can be simpler in terms of equipment setup |
Temperature Control | Liquid helps dissipate heat generated during the grinding process | May require additional cooling systems for temperature-sensitive materials |
Grinding Efficiency | Can be more efficient in terms of particle size reduction and throughput | May be less efficient for agglomerating or high-moisture materials |
Maintenance | Requires regular maintenance of additional equipment, such as pumps and classifiers | Simpler maintenance, focusing mainly on the mill and dust collection system |
Cost | Higher initial investment and operating costs due to additional equipment and energy consumption | Generally lower capital and operating costs compared to wet grinding |
Conclusion
By the end of this section, you will have the know-how of the intricacies of ball mills, their make-up parts, and factors that are related to their efficiency. This will be very useful to your grinding process. Introducing the elements such as critical speed, grinding media loading, properties of the material, and grinding methods along with the experience of the manufacturers, you will be able to optimize the ball mill’s operation. Our group of pros can always help you with the selection of the ball mill suitable for your grinding process and they are ready to assist you at every step of the process.