- Home
- Blog
- Mineral Solution
- Vibrating Screen Design Demystified: Types and Benefits
What is a Vibrating Screen?
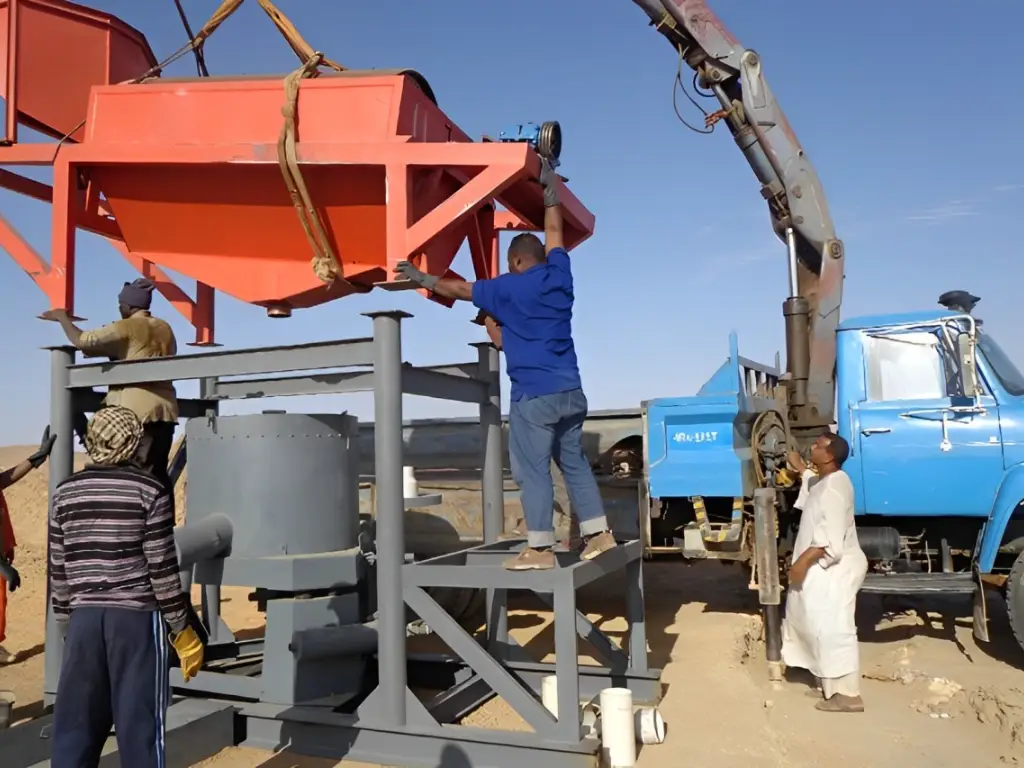
Application of Vibrating Screen
Vibrating screens are utilized in a multitude of industries due to their adaptability and efficiency. They play a crucial role in material processing and classification.
Vibrating Screen Design for Different Industries
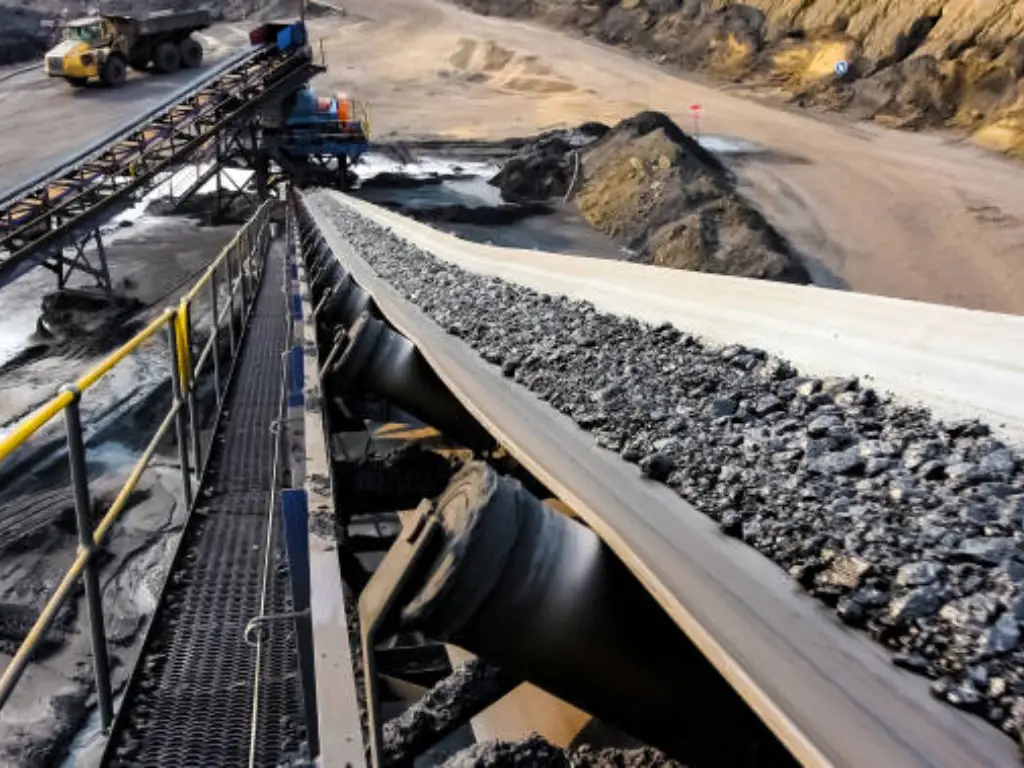
Optimizing Vibrating Screen Efficiency
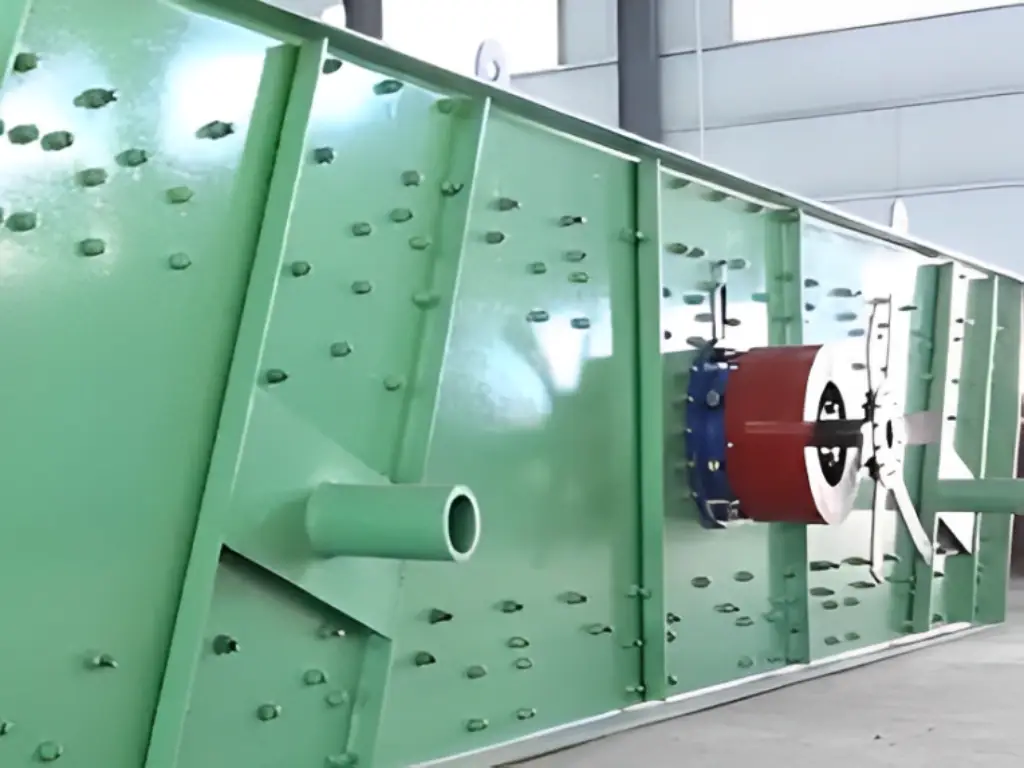
There are several options that can be adjusted in order to achieve the highest efficiency of vibrating screens. These options enable the screen to be optimized for the material and operational needs of the process. To optimize performance, it is crucial to familiarize yourself with the Essential Guide to Vibrating Screen Parts.
How does the Vibrating Screen Machine Work?
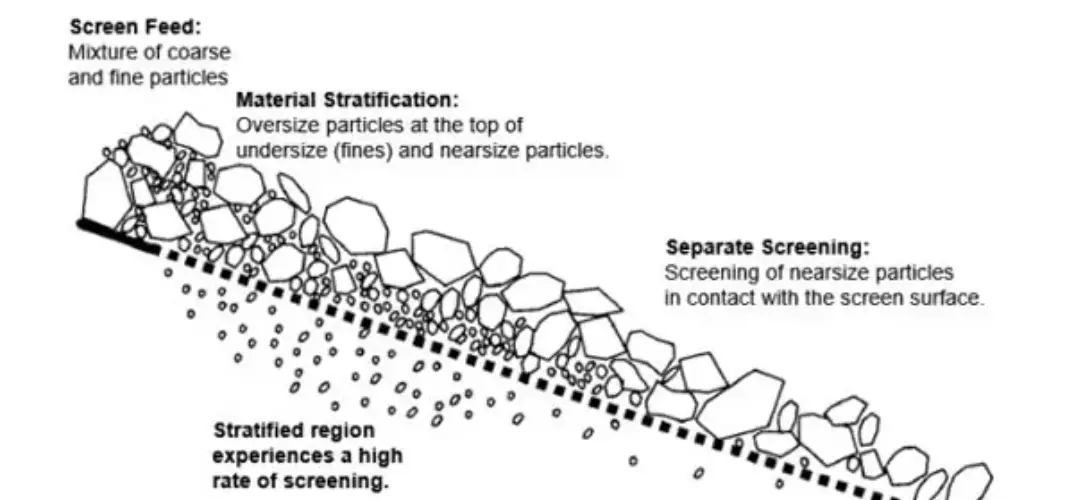
Factors Affecting Vibrating Screen Performance
JXSC can customize vibrating screens based on your material, feed size, screen size, and the number of screen decks. For tailored design solutions, visit JXSC Vibrating Screens.
Different Types of Vibrating Screens
Types | Dsecription | Pros and Cons | Applications |
---|---|---|---|
Inclined Screens | Inclined screens are designed with an angle to help material flow. They use gravity to move materials over the screen, improving efficiency and throughput. These screens are common in the aggregate and mining industries for sorting large particles. | They are efficient for large particles and high throughput. However, they may not be suitable for fine screening and can take up more space. They are durable and easy to maintain, but material can build up at the bottom. | Best for aggregate and mining industries where large particles need sorting. Ideal for primary screening and high-capacity uses. |
Horizontal Screens | Horizontal screens provide precise separation with a flat surface. They offer better control over the screening process, ensuring accurate results. These screens are ideal for fine material separation and high-precision tasks. | These screens are precise and accurate for fine materials. However, they have lower throughput compared to inclined screens and can be more complex to maintain. They require less space but may need more frequent cleaning to avoid clogging. | Used in pharmaceuticals and food processing where precision is critical. Ideal for fine material separation and quality control. |
Banana Screens | Named for their curved shape, banana screens offer multiple angles in a single unit. This design increases capacity and efficiency by processing more material at once. They are effective for handling high volumes. | Banana screens offer high capacity and efficiency, suitable for large-scale operations. Their complex design can be harder to maintain and repair. They handle high volumes well but may not be as precise for fine materials. | Common in mining and heavy-duty applications where large volumes need processing quickly. Suitable for high-capacity operations. |
Dewatering Screens | These screens are designed for dewatering. They use high-frequency vibration to remove moisture from materials, making them ideal for wet material processing. Dewatering screens ensure materials are dry after screening. | Dewatering screens are effective at removing moisture, improving material handling and reducing drying times. However, they are specialized and may not be versatile for other tasks. They are efficient but can have higher operational costs. | Used in mining, wastewater treatment, and any industry where moisture removal is crucial. Ideal for dewatering and drying tasks. |
Grizzly Screens | Grizzly screens have large openings to handle coarse materials. They are often used in primary screening to remove large rocks and debris before secondary processing. These screens are robust and durable. | Grizzly screens are durable and handle large materials well, reducing the load on secondary crushers. However, they are not suitable for fine screening and can be noisy. They need minimal maintenance but may need cleaning to prevent clogging. | Best for mining and heavy-duty uses where large rocks and debris need to be screened out. Used as a primary screening tool. |
Rotary Screens | Rotary screens feature a cylindrical drum that rotates to screen materials. They provide gentle handling and are effective for separating materials based on size. These screens are versatile and can be used for various materials. | Rotary screens offer gentle handling and versatility, suitable for a wide range of materials. They have lower throughput compared to vibrating screens and can be more complex to maintain. Their rotating design reduces noise but may require more space. | Common in food processing, pharmaceuticals, and recycling where gentle handling and versatility are needed. Suitable for separating different material sizes. |
How to Choose the Right Vibrating Screen for Your Needs?
To find the best vibrating screen manufacturers, explore the Top 5 Vibrating Screen Manufacturers: Boost Your Mining Efficiency guide.
Maintenance Tips for Vibrating Screens
Conclusion
FAQs
The price of vibrating screens depends on the design, material used, and other features that may be incorporated in the design. Mining applications screens are generally costlier than food processing applications due to their construction and capacity. Other attributes like energy consumption, ease of maintenance, and durability also affect the cost and should be taken into account when comparing the designs.
Vibrating screens can be easily incorporated into the existing production lines by making them conform to size, shape and installation interfaces. One must also take into account the screen size and its position in the feed and discharge area and any changes that may be required in the production line to incorporate the new equipment. The integration process can be made easier and the efficiency of the production process improved if the planning and layout design are well done.