- Home
- Blog
- Mineral Solution
- Unlocking the Secrets of Screening in Mineral Processing
- mmldigi
What is Screening in Mineral Processing?
Screening in mineral processing is a very important process that sort particles based on size and shape. This process not only helps to improve the efficiency of the subsequent operations such as crushing and grinding but also to increase the recovery of valuable minerals. Through the application of different screening techniques, the operators are able to sort out all the undesirable materials from the product so that only the required size of particles is passed through the plant. Screening is a critical step in the mineral processing cycle, and anyone involved in the operations needs to have an understanding of the concept to maximize efficiency and profitability.
Screening, therefore, cannot be overemphasized. It acts as the preliminary barrier against unwanted material and thus enables better management of the feed material particle size. This in turn improves screening efficiency and adds value to the overall downstream processing activities. Also, the screening technology has improved in such a way that it is now possible to get the highest efficiency with the least amount of time that the mineral processing plant will be out of order.
Screening vs. Other Separation Methods
When discussing screening in mineral processing, it’s essential to compare it with other separation methods. This comparison helps to highlight the strengths and weaknesses of screening relative to other techniques. Below is a table summarizing the differences between screening and other common separation methods:
Separation Method | Description | Advantages | Disadvantages |
---|---|---|---|
Screening | Separates particles based on size using screens. | Efficient for particle size control- Simple operation- Low energy consumption | Limited to size-based separation- Not effective for very fine particles |
Cycloning | Utilizes centrifugal force to separate particles | Effective for fine particles- Can handle large volumes of material | Higher operational costs- More complex equipment |
Gravity Separation | Uses the difference in density to separate materials | Cost-effective for certain materials- Simple technology | Limited to specific materials- Less effective for small particles |
Flotation | Separates minerals based on surface chemistry | Highly selective for valuable minerals- Can recover very fine particles | Requires chemicals- More complex process |
Applications of Screening in the Mining Industry
Screening in mineral processing finds a wide range of applications across various industries. Here are some notable examples:
● Mining: Used to separate valuable minerals like iron ore from unwanted materials.
● Aggregates: Helps in producing high-quality gravel and sand by removing fine particles.
● Coal Industry: Utilizes screening to ensure consistent particle size in coal processing.
● Recycling: Separates metals and plastics from waste materials to improve recycling efficiency.
● Construction: Assists in producing aggregate materials for concrete and road construction.
Types of Screening Equipment Used in Mineral Processing
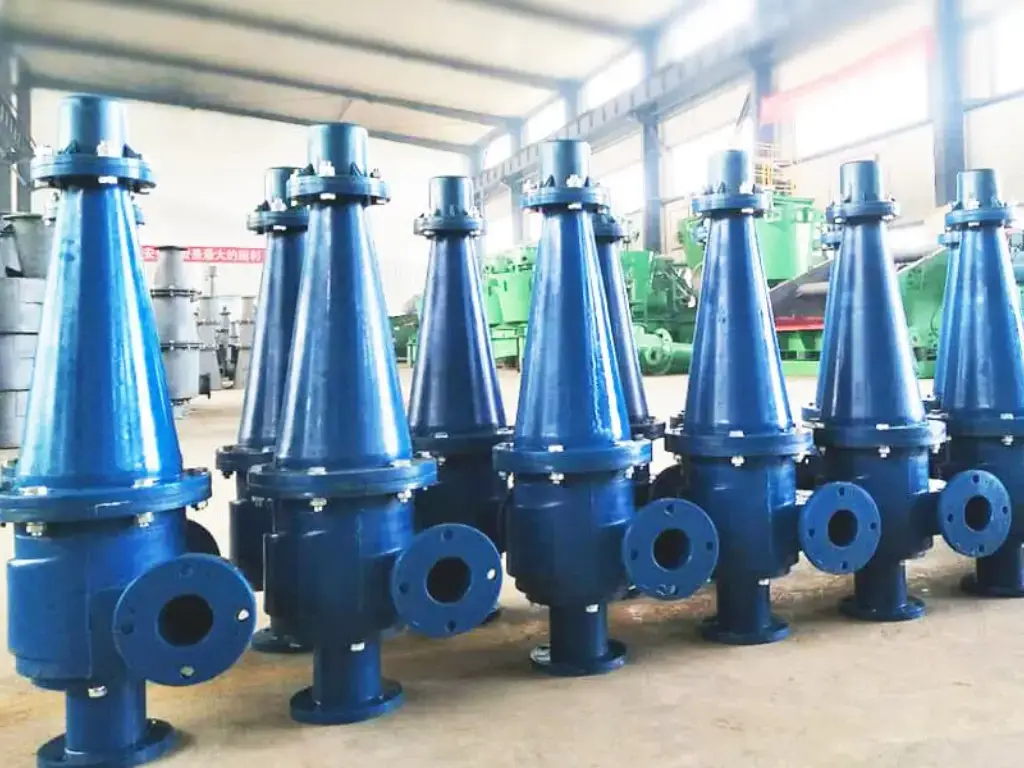
In mineral processing, a variety of screening equipment is employed to achieve efficient particle separation. The most commonly used types include:
Trommel Screens
Trommel screens are cylindrical screening equipment that is used by rotating to sort materials according to size. They are most suitable for large particle sizes and are widely employed in handling of aggregates, composts and ores. The rotation also causes the material to tumble and this aids in the layering of the material and also enables the removal of the fine particles through the screen openings. Trommel screens are particularly useful in the separation of materials such as gravel, coal, and even gold ore because they can manage large throughputs while achieving high levels of separation. Due to their longevity and ease of use, they are used in big and small businesses alike.
Vibrating Screens
Vibrating screens are one of the most popular types of screening equipment in the mineral processing industry that provides more efficient screening. They work through employing a vibrating motion to transport materials across the screen surface and as a result, separate them according to size. The screens are available in different types; inclined and horizontal types and they can process materials ranging from fine powder to coarse aggregate. Vibrating screens are most useful in the separation of materials such as iron ores, copper, and gold, and hence are a vital tool in mining. Their high capacity and flexibility in the characteristics of the material being screened improve total screening effectiveness.
Spiral Classifiers
Spiral classifiers are used in the classification of materials by size and density. The equipment includes a spiral screw that is mounted in a trough containing water and on which lighter particles float while the heavier ones settle at the bottom of the trough. This process is highly efficient in sorting fine and coarse particles, and therefore can be used in mineral processing operations such as sorting of sand and slurry. Spiral classifiers are especially useful when working with silica, coal, and heavy metal ores because they offer a stable way of achieving the right particle size. The versatility, which allows them to work in tandem with other pieces of equipment, including ball mills, further improves the efficiency of the process.
Hydrocyclones
Hydrocyclones are very efficient tools for the separation of materials according to their density and size using the force of centrifu gation. When slurry is fed into the hydrocyclone the denser particles move to the periphery due to the centrifugal force while the lighter particles move towards the center and are discharged through the overflow. This method is widely used in the field of mineral processing where it is used in the separation of fine particles of iron ore and copper. These are among the reasons why hydrocyclones are compact in design, high throughput and low energy intensity which makes them a vital tool in the current mining processes. This they achieve by providing a well sorted particle size distribution which in turn improves the efficiency of the processing plant.
Gold Trommel Scrubbers
Gold trommel scrubbers are screening equipment used specifically in washing and sorting of gold containing materials. These machines consist of the functions of a trommel screen and a scrubber that washes clay and other impurities out of the ore. The rotating drum stirs the materials and this makes it easy to separate gold particles from the rest of the materials. Applicable for alluvial gold washing, these scrubbers are usually used in combination with other equipment to enhance the yield of gold. They are built to last and have large carrying capacities and are ideal for both small scale mining companies and large mining companies that require high capacity mineral processing equipment.
Looking for screening machine manufacturers? Click on industrial screening equipment to explore JXSC’s premium screening machines designed to boost your operational efficiency and enhance mineral recovery.
What Factors Affect the Efficiency of a Screening Process?
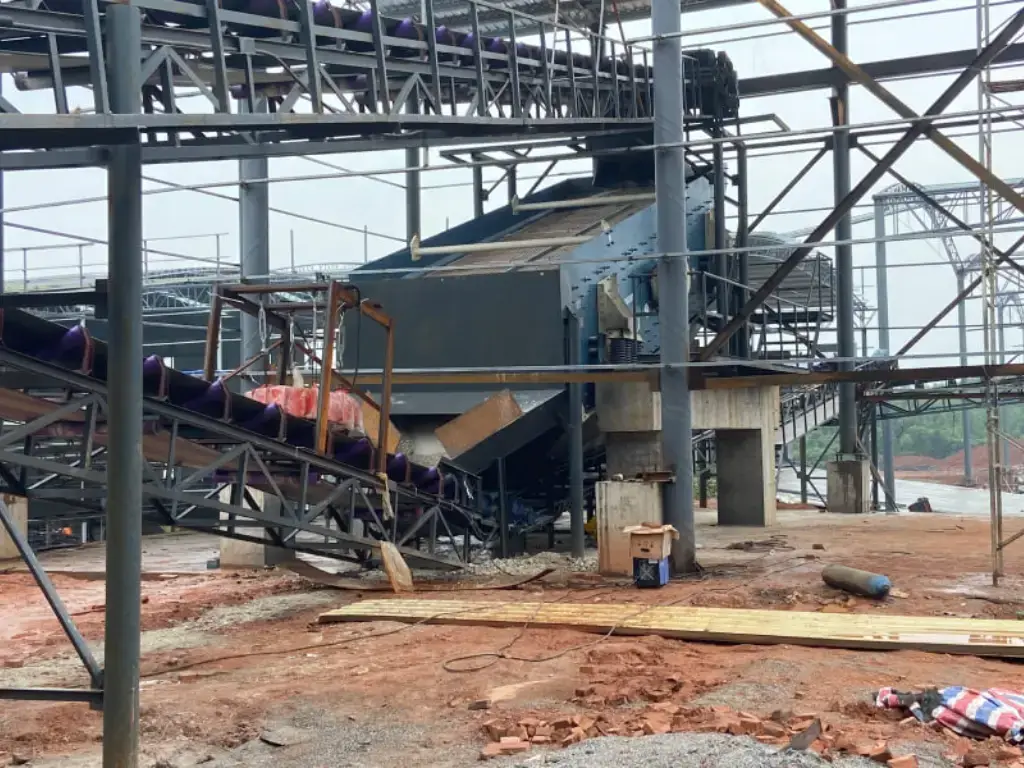
The efficiency of a screening process can be influenced by several factors, including:
● Type of Screening: The kind of screening used which may be mechanical screening, wet screening or dry screening has a great effect on the method. All of the methods described above have their peculiarities and are suitable for particular materials. For instance, wet screening is the most appropriate method for use in separating fine particles from slurries while dry screening is most appropriate for coarse materials.
● Screen Mesh and Aperture Size: The size of the screen mesh and the aperture openings are the two important factors that define the efficiency of particle separation. A large opening permits the passage of large particles while a small one retains the finer materials within a given system. In general, it is important that the screen mesh chosen should be best suited to the particle size distribution of the material that is being screened.
● Flow of Material and Screen Capacity: The size of the material and the width of the rate at which it passes through the screen determines the general capacity and productivity of the screen. High flow rates may result in the accumulation of material which may block the screen opening and thus low efficiency. For effective screening, operators have to ensure that there is right proportion between the amount of the material to be screened and the screen capacity.
● Screen Deck Configuration: The tilt of the screen deck and the number of screen openings can affect the particle stratification. Screen decks should therefore be well designed to allow for efficient separation whereby the finer particles get to the discharge end, ensuring there is enough open area for optimal performance. Recent developments in screen deck design including the double deck designs improve the screening of minerals by offering more than one size classification in one run.
● Material Characteristics: Screening of materials depends on the type of material to be screened, its moisture content, density, and shape. For instance, wet particles stick together and are likely to block the screen openings than dry particles which are more likely to flow. Knowledge of the properties of the material assists in the choice of the screening equipment and techniques, which results in enhanced efficiency.
● Uptime and Maintenance: The effectiveness of a screening process can be greatly enhanced if the screening equipment undergoes routine maintenance and if there are few interruptions in the screening operation. The efficiency of the screening equipment and the degree of separation obtained are dependent on the performance of the screening equipment. If the screening machine is well maintained, with special emphasis on screen mesh and the mechanical systems, then the best way to improve throughput can be achieved.
● Vibration and Circular Motion: Vibration is very important and used widely especially in vibrating screens to enable the movement of particles across the incline screen. Circular motion enables the particles to stratify and achieve efficient sizing and also eliminates blockage at the discharge end. The amplitude of vibration should be set correctly in order to enhance the efficiency of screening, as well as to increase the ability of particles to pass through the screen mesh.
Common Challenges and Solutions in Screening Processes
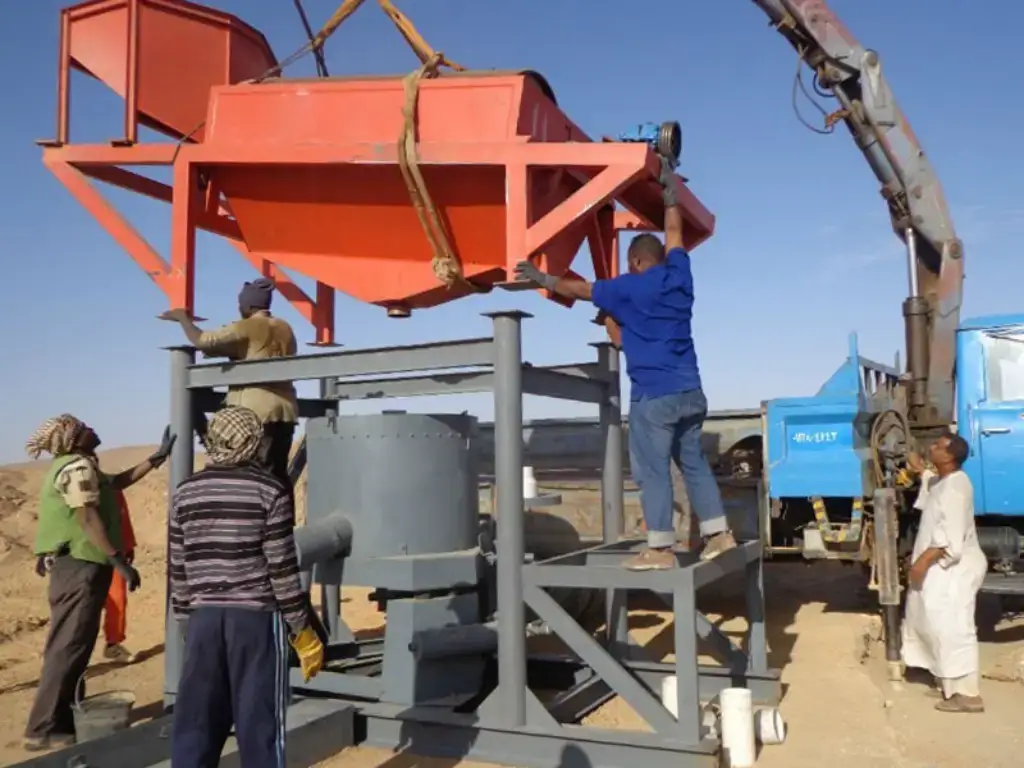
One common problem is screen blinding where fine particles block the screen openings thus causing reduced flow and time wastage. In response to this, operators can use anti-blinding devices or screen cleaning systems that assist in preserving clear apertures. Another challenge is the deterioration of the screen media which causes a decline in screening efficiency of the machine. This is why it is important to carry out routine checks on the machines and replace any worn out part as soon as possible. Furthermore, there is a problem of the differences in the amount of moisture in materials since it causes agglomeration which in turn influences the flow of materials. Appropriate use of moisture control measures including drying of materials before screening go a long way in enhancing the results. If these challenges are managed effectively, operators can optimize the screening processes and therefore increase the overall recovery of minerals.
The Role of Screening in Environmental Sustainability
Screening is also an important tool in enhancing environmentalism in the mineral processing industry. Screening makes it possible to minimize the amount of waste produced during the extraction process and to increase the general yield of valuable minerals. This not only helps to save natural resources but also reduce the negative effects of mining on the environment.
Moreover, improved screening processes contribute to the minimization of energy use and greenhouse emissions that are common in mineral processing. In the context of the growing focus on sustainability, the function of screening in achieving the highest levels of resource utilization and the lowest levels of waste production is critical.
Conclusion
In conclusion, screening in mineral processing is one of the essential operations that have a direct influence on the performance of the mining industry. As the technology in screening continues to improve, the industry can look forward to even better screening in the future. It will not only increase the revenue of mineral processing plants but will also lead to more responsible mining.
Looking to the future, it will be essential for mining professionals to grasp the principles of screening and to choose the right equipment. In this way, it is possible to maintain the efficiency of screening in the future of the development of mineral processing, making it economically and environmentally profitable.
Experience Superior Performance with JXSC's Screening Machines
At JXSC, we pride ourselves on delivering high-quality screening machines designed to enhance the efficiency of mineral processing operations. Our commitment to excellence is evident in our extensive range of products, including trommel screens for sale, vibrating screens for sale, and crushing and screening equipment for sale. Each piece of equipment is engineered with cutting-edge technology and built from robust materials to ensure durability and longevity. This reliability makes JXSC a trusted name in the mining industry, as our screening machines are specifically designed to optimize performance while minimizing downtime.
Our screening machines are not only high-performing but also engineered for low maintenance, reducing overall operational costs for our customers. The vibrating screening machines we offer are particularly renowned for their precise sorting capabilities, allowing for efficient classifying of ores based on size and density. By integrating advanced design features, JXSC ensures that each screener for sale maximizes throughput and accelerates return on investment (ROI). Experience the superior performance of JXSC’s screening equipment and elevate your mineral processing operations today!
FAQs
How does the size of particles affect the screening process?
The size of particles directly influences the screening efficiency; smaller particles tend to pass through the screen openings more readily, while larger particles may be retained longer.
How do different materials (like coal, gold, and copper) affect screening methods?
Different materials have unique properties, such as density and moisture content, which can impact the choice of screening methods. For instance, fine particles in coal require different techniques compared to heavier materials like gold or copper.
What maintenance practices are essential for screening equipment?
Regular inspection and maintenance of screen panels, monitoring for wear and tear, and cleaning mechanisms to prevent blinding are crucial for maintaining the efficiency of screening equipment.