- Home
- Blog
- Equipment Info
- Uncover The Solutions To Common Thickener Problems
- jxsc
Thickeners are often used in the beneficiation process to help tailings dehydration or concentration processes. It is also widely used in the concentration and purification of liquids containing solid particles in the chemical industry, building materials, and water and sewage treatment industries. However, despite their widespread use, they can sometimes cause problems that must be addressed. Concentration is a critical stage in separating solids from liquids, and any problems in this process can lead to inefficiencies and loss of valuable resources. In this article, we will discuss some common problems in the use of thickeners, and develop different solutions based on potential problems to help you improve the performance of their equipment.
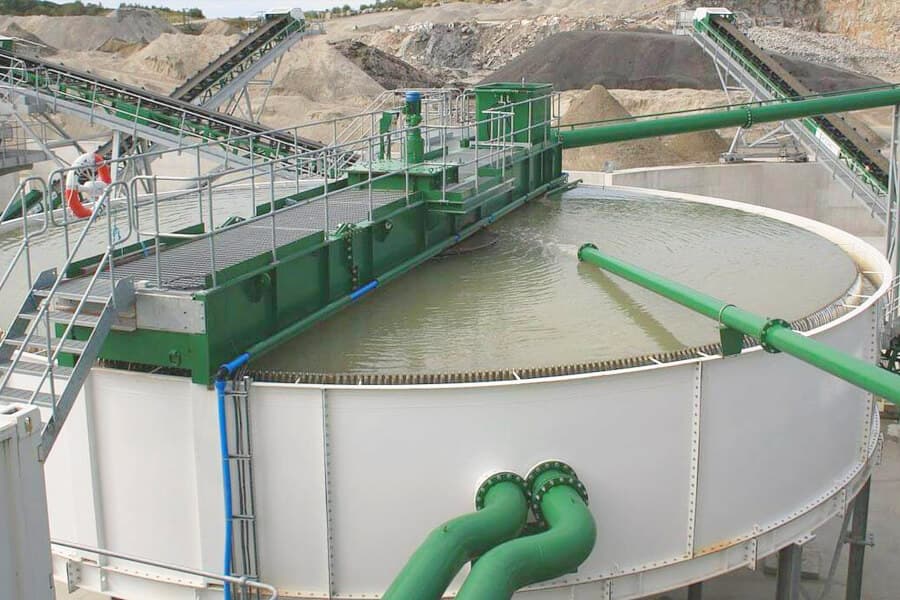
Thickener is a continuous settling equipment used for solid-liquid separation of finely ground pulp in concentrate or tailings. The common problems of thickeners are common headaches in many industries. To ensure your process runs as efficiently and safely as possible, we should try to identify potential thickener problems before they become major problems.
1. Thickener overflow water running muddy
The main reason for muddying is that the raw ore contains a lot of slimes, the processing capacity is too large, and the amount of washing water is increased. The mud seal of the mud seal tank is damaged, and there is too much sand in a certain layer, etc.
Solution: Adjust the mass fraction of flocculant and the amount of dilution water, and change the position of adding dilution water;
2. Thickener harrowing accident
Torque high-pressure rake accidents often occur in the actual application of rake thickeners. This will not only lead to a lot of waste of material and manpower but also stop production accidents.
Solution: Weld reinforcement ribs on the flange of the main shaft of the rake machine to improve the strength level of the connecting bolts.
3. The base of the thickener cycloidal reducer is broken
The main reason for the breakage of the bottom of the cycloidal reducer of the thickener is that the thickener runs under heavy load for a long time, which makes the safety protection device fail. The bottom disconnection of the cycloidal reducer is very harmful during applying the thickener. Once the base of the reducer breaks, every component will fail from the motor to the entire drive chain of the rake.
Solution: Add safety protection device
During the thickener’s working process, the cycloid reducer’s bearing capacity must be considered. Set the maximum torque, and add a mechanical safety protection device for destroying components and a transmission mode with safety protection for the thickener.
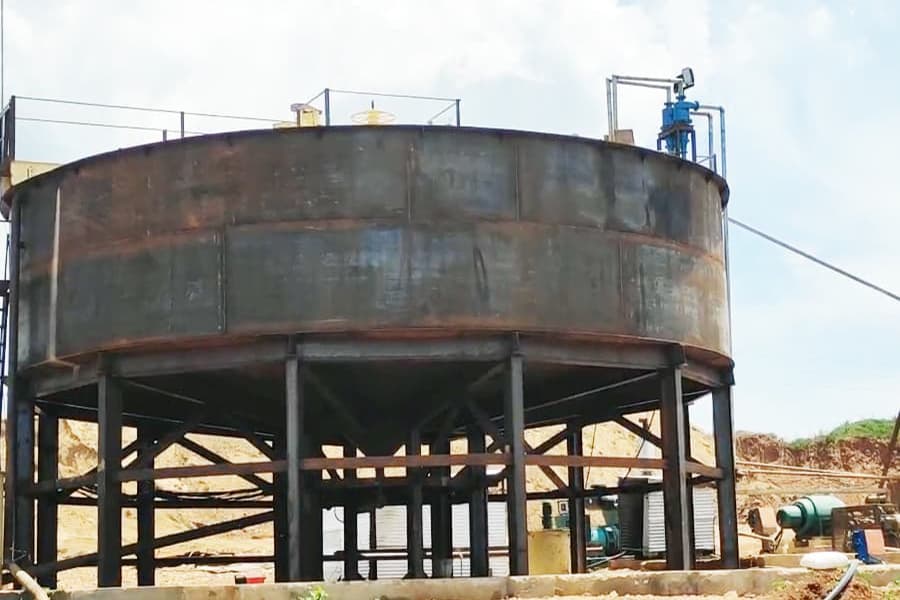
4. Thickener lifting device failure
The failure state of the hoisting device of the thickener is that the rake needs to be lifted during operation, but the rake cannot be lifted. There are two main reasons:
(1). The matching clearance between the main shaft and the worm gear hole is too small. During operation, there is a large friction force between the two, and there is no sufficient supply and lubrication, so the ability to lift the rake is getting weaker and weaker. If the rake is not lifted for a long time, it will also cause it to rust and die.
(2). The stress-bearing surface of the long key connected to the shaft is uneven, and only part of the force-bearing surface is stressed.
Solutions:
(1) Increase the lifting gap
The fit clearance for bore shaft is too small. According to the actual situation, without changing the lifting device’s structure and the sleeve’s positioning, a 3 mm thick metal pad can be installed at the lower end of the sleeve.
(2) Improve the lubrication method
Due to the long lubricating pipeline of the thikener, the resistance is relatively large. After friction occurs between the main shaft and the worm gear, the lubrication cannot be replenished in time. Therefore, a high-pressure oil gun can be used for pressure lubrication, and the oil supply pipeline can be modified according to the pressure pipeline.
- Improve the production and purchase requirements of spare parts
When the thickener rake is manufactured, it should be processed and manufactured according to the requirements stipulated in the original design drawings. In addition, when purchasing equipment, try to choose pressed channel steel, as welded steel channels are easily deformed.
5. Fracture of volute of Thickener hoisting device
The thickener operates due to a lack of lubricant and overload during the working process. There will be fractures of the volute, increasing the loss between the turbine and the rod.
Solutions:
During the operation of the thickener, it is necessary to control the distance between the main body of the hoisting device of the thickener and the shaft center, to prevent the shaft center from moving up and causing damage to the cover on the upper part of the turbine. In addition, it is necessary to strengthen daily maintenance and overhaul operations to achieve daily lubrication inspection and replenishment.
In summary, common problems with thickeners are caused by various factors and are common in industrial and beneficiation processes. But it should be addressed as soon as possible to prevent further costly damage. The causes and solutions discussed in this article can give you a starting point. It is important to have regular inspections and maintain a vigilant maintenance program to avoid such problems. Additionally, it is important to consider the specific needs of each structure when making repair or replacement decisions. With the proper diagnosis and solutions, many common thickener problems can be easily resolved.
To ensure the normal operation of the mineral processing plant, JXSC can customize high-efficiency thickeners according to the production environment, process conditions, investment costs and other factors to avoid economic losses.