- Home
- Blog
- Mineral Solution
- SAG Mill vs Ball Mill: Choosing the Right Grinding Mill
Preface
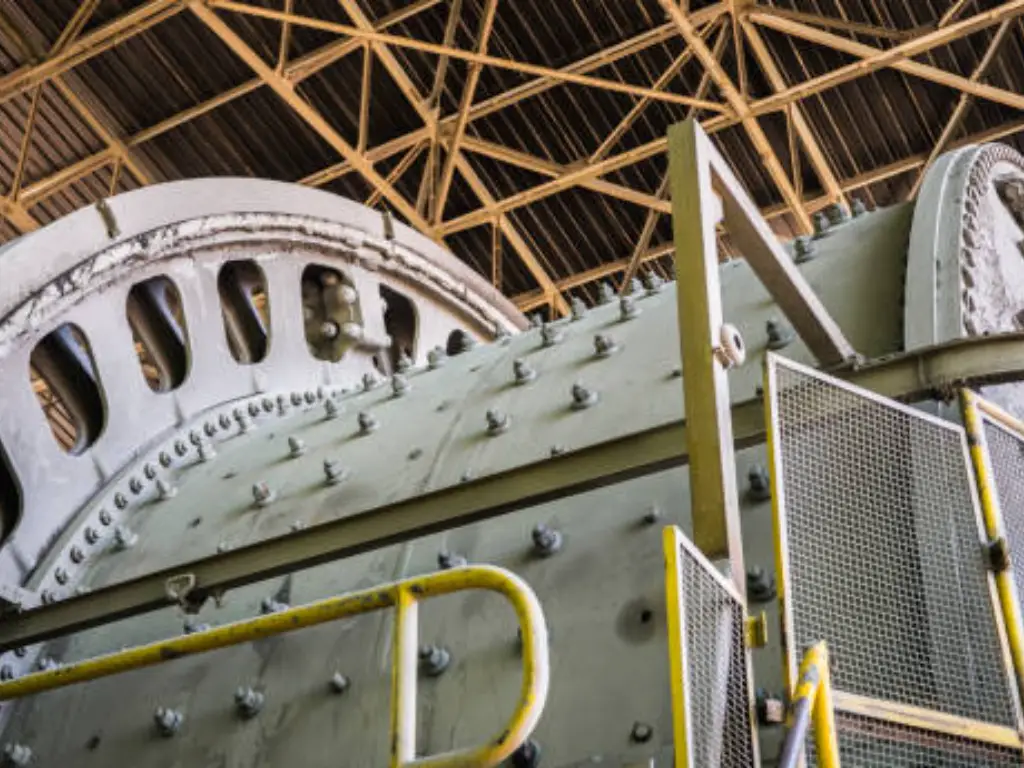
Grinding equipment is essential in mineral processing operations to help reduce particle size to enhance the extraction process.In the field of mineral processing, the selection of the grinding mill has a significant impact on the performance and the cost. In addition to the pebble mill, Two types of these are the SAG mill and the ball mill and they have respective advantages. SAG mills deal with larger rocks with a blend of rock particles and steel balls suitable for primary grinding though they consume more power. Ball mills employ steel balls or stainless steel rods with varying diameters for producing the final particle size for precious metals. Both types of mills may also have different motor types and gearing systems, making it important to understand the design and components of each. This blog will introduce their knowledge of material size, length ratios, and the amount of ore to help you make informed decision to purchase right mill for particular application .
What is Sag Mill?
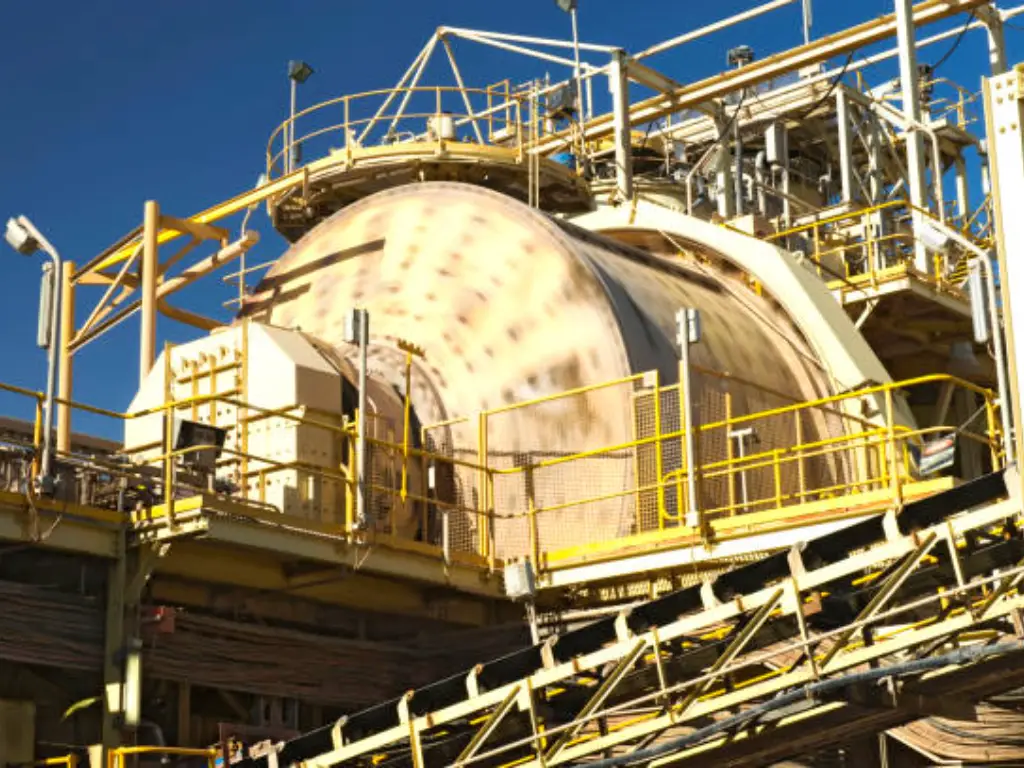
Sag Mill is a kind of heavy duty equipment used in the ore crushing and grinding industry. Its working principle is to utilize the impact and grinding effect of a small amount of steel balls and the material itself to crush the ore Through the rotation of the cylinder, large pieces of ore are gradually broken into smaller particles in the collision between the steel balls and the ore SAG Mill is widely used in the primary grinding process of mines and can effectively handle large and hard ores.
Compared with the traditional ball mills, the semi-autogenous mills have higher energy-saving effect because they partially depend on the energy of the materials themselves for grinding, thus less dependence on the steel balls and the electrical energy. SAG Mill has been adopted in large mines and high throughput lines and is well suited for large ore chunks, enhancing productivity and minimizing energy consumption.
What is Ball Mill?
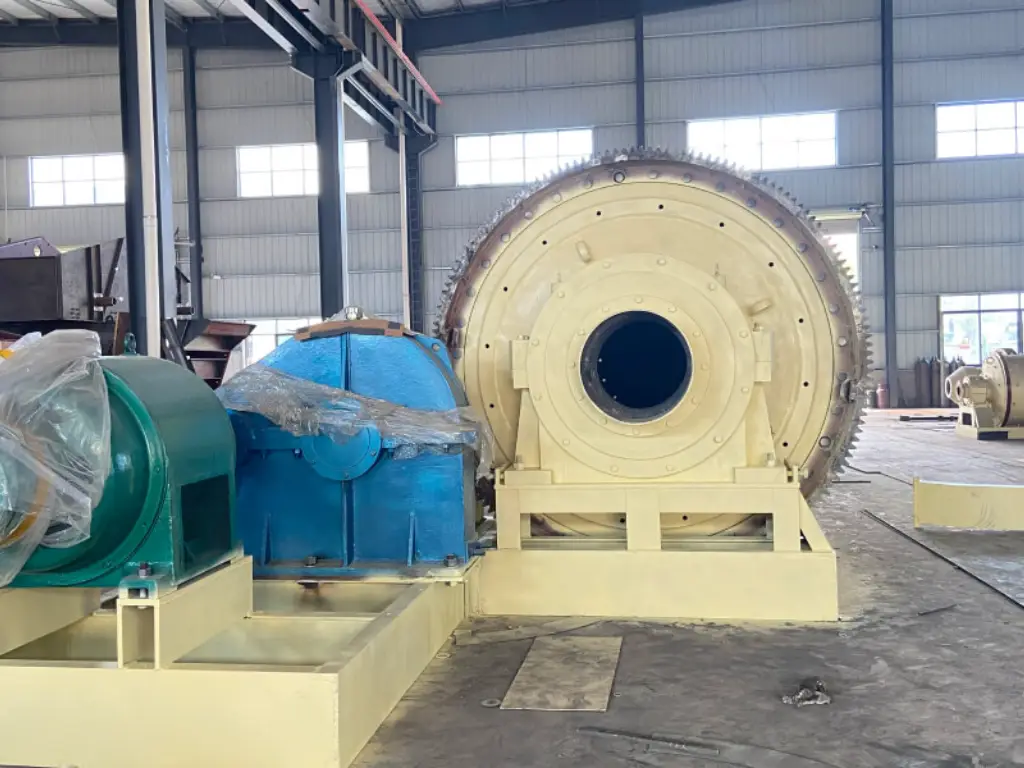
Ball mills are used in various industries including the mining industry, chemical industry, building materials industry and the metallurgy industry to crush raw materials. When the cylinder rotates, the steel balls inside it move and grind against the materials, and thus large portions of materials can be broken into smaller portions. Ball mills can be used for both primary and secondary grinding of materials with different hardness and it can also be used in the process of fine grinding.
The structure of the ball mill is simple, easy to operate, and has strong adaptability. It is mainly used to grind secondary or tertiary materials and it especially demonstrates excellent performance when fine-grained materials are needed. Some of the parameters that will influence the efficiency of the ball mill and the extent of ore breakage include the size of the steel balls, the speed of the cylinder and the nature of the material. Despite the high power consumption of sag, it has excellent performance in fine grinding and is widely used in various industrial sectors.
Discover the full details of ball milling by exploring A Comprehensive Guide to the Ball Milling Process.
Main Differences Between Sag Mills and Ball Mills
Feature | Gold | Silver |
---|---|---|
Working Principle | Rotating drum with steel balls and rock particles, creating impact and attrition forces | Rotating drum half-filled with steel balls, creating a systematic and rhythmic grinding action |
Grinding Media | Combination of steel balls and rock particles | Only steel balls, with a lack of rock particles |
Application Stage | Primarily used in the first stage of grinding, handling large feed sizes and varying ore hardness | Used in later stages of grinding for fine particle size distribution, meeting specific process requirements |
Processing Capacity | High processing capacity, suitable for large-scale operations due to larger diameter and larger mill shell | Lower capacity, ideal for smaller scale operations |
Energy Consumption | Higher power consumption due to the need to crush large rocks and manage diverse media | Lower power consumption as only a fraction of the energy is needed for the uniform grinding motion |
Grinding Efficiency | Higher levels of impact reduction, effective for larger and harder ores | More uniform grinding process, producing smaller and consistent particle sizes |
Equipment Cost | Higher initial costs due to larger size and complex design | Lower initial costs due to simpler design and use of steel balls |
Operation and Maintenance | More complex operation and higher maintenance costs due to wear and tear on diverse media | Simpler operation and lower maintenance costs due to fewer components |
Applicable Ore Types | Capable of handling a wide range of ores, including large and hard particles | Best for softer ores and materials needing fine grinding |
Process Flow | Often used in an open circuit, allowing for high throughput and handling of larger feed sizes | Typically used in a closed circuit system to maintain consistent particle size and material homogeneity |
How to Choose Between Ball mill and Sag mill?
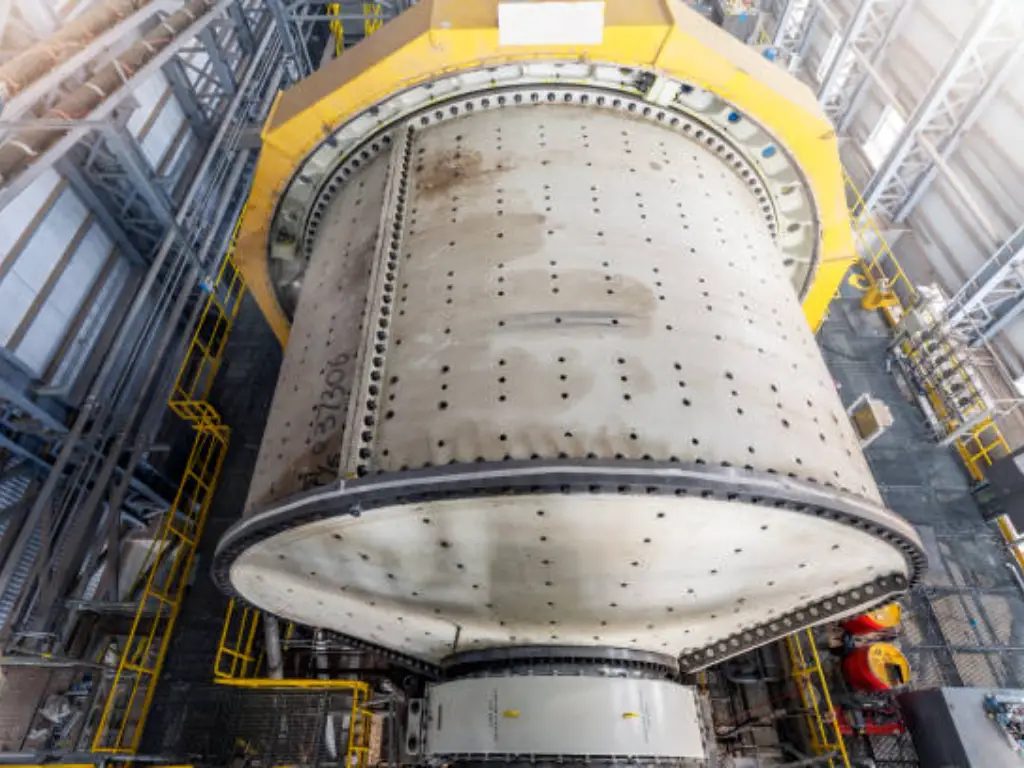
By careful consideration of several factors, it will help you make the right decision.
Grinding Media and Motion
● SAG Mill: In the milling process, the SAG mill employs steel balls and rock particles as the grinding media in the milling process. These two features, which are addition of rock particles, allow the mill to handle large feed sizes and different movements of the charge load. The presence of the rock particles also assists in offering the variety of grinding motion, which makes SAG mills appropriate for various ore characteristics. But it should be noted that the application of rock particles can also cause wear of mill liners and a decrease in their performance. This type of mill is particularly useful in the first stage of comminution since it assists in the achievement of the goal of breaking large chunks of the ore.
● Ball Mill: In ball mills, only steel balls are used as the grinding media. The balls are of equal size and of the same material and this results to a more controlled grinding. The particles formed are of a smaller size and of a narrow size distribution. This makes ball mills ideal for use in applications where a high amount of fines are required and a certain type of motio
Energy Consumption
● SAG Mill: SAG mills are generally more energy consuming because of the need to crush larger rocks and to handle both media. However, SAG mills are useful in the handling of large amounts of ore and are not affected by the characteristics of the material. The higher energy demand, because of the required high level of power, is another crucial aspect that has to be considered when evaluating the costs of the operation.
● Ball Mill: Ball mills are less energy intensive than SAG mills. Since the rock particles are not present in the mill, it only requires a small amount of energy to run and thus is more economical for fine grinding. This lower power requirement is very crucial in reducing operating expenses, especially for small-scale businesses.
Processing Capacity
● SAG Mill: SAG mills are employed for the purpose of size reduction of the feed materials and possess a high capacity of through put. The larger balls of steel and rocks used in the process of grinding also help in grinding large and hard ores in the process. This, coupled with their smaller diameter and length ratios, make SAG mills ideal for large mining operations where large throughputs are needed.
● Ball Mill: While ball mills have a lower throughput compared to SAG mills, they are very efficient in producing fine products. This makes them suitable for small scale applications where the particle size is critical and has to be uniform.
Maintenance and Operation
● SAG Mill: The operation and maintenance of SAG mills are slightly more complex due to the fact that the mill has to handle both steel balls and rock particles. The contents of the mill are exposed to a lot of stress and hence require frequent replacement. The various charge load actions and components of each mill have to be managed properly to get the best results in terms of the material characteristics, cost, and maintenance.
● Ball Mill: Ball mills are also easy to operate and maintain as compared to other mills. The absence of rock particles and the employment of only steel balls mean that there are fewer components to regulate, which in turn means that there is less need for maintenance. This makes ball mills a practical choice for operations that need to have constant and simple maintenance procedures.
Innovations and Future Trends in Grinding Technology
The mining industry is always evolving and so is the grinding technology since it is still being advanced. Innovations in the construction, the type of materials employed and the methods of fabrication of grinding mills are slowly improving the efficiency of mineral processing facilities. For example, new types of the grinding media are ceramic and polymer-based balls to improve the grinding performance and reduce the wear. The amount of ore and the ratio of steel balls are some of the factors that have to be well managed in order to improve the performance of each type of mill. Further, new technologies in automation and control systems are allowing better control and uniformity in the grinding process and hence enhancing the performance of the mills by controlling the charge load actions and other parts of the mills.
For the future development, there will be more advancement in the grinding technology that will enhance the operations of SAG and ball mills. These innovations will help the mining operations to improve productivity, reduce energy consumption and the effect on the environment. For instance, mill speed control and the knowledge of material properties will be improved to increase the response to the ore hardness and the content of the mill. It is necessary to be informed about these trends to be able to choose the right grinding equipment for your processes and to control each specific case to the maximum.
Conclusion
Some of important factors that need to be put into consideration when selecting the right mill for your mining business include the type of ore and material, the size of the particle that is desired and the power consumption. SAG mills are for larger feed sizes with both rock and steel balls and are more general use but use more energy. Ball mills are used for fine grinding and the product obtained is of small particle size, low energy consumption and narrow particle size distribution. Take the important considerations into account and your requirements to choose the right mill for your mining business. Choosing the right supplier is crucial for efficiency. Check out the Top 5 Ball Mill Manufacturers to Power Your Manufacturing Needs.
FAQs
What role does the design of the mill play in choosing between SAG and ball mills?
Depending on the structure of the mill, the type of job that the mill is most suited to perform is determined. SAG mills have coarser feed sizes (sag mill feed) and process more material due to the bigger diameter and length to diameter ratios. Ball mills employ steel balls as the grinding media and are suitable for both wet and dry grinding. Knowledge of these components is helpful in decision making depending on the characteristics of the process and the material. Operating conditions of the mill, power consumption of SAG mills, and different charge load actions also play a very significant role in this regard. Also, the size and type of the grinding media used in the mill can also influence the grinding process, where SAG mills are capable of using larger grinding media than ball mills.
What are the maintenance considerations for SAG and ball mills?
SAG mills are bigger in size and use rock particles that are abrasive and hence put more pressure on the mill and hence need frequent maintenance. Ball mills require less amount of maintenance as compared to other mills as the wearing down of steel balls is uniform and the design is simple. Compared to other types of mills, there is higher predictability of maintenance with ball mills.
How does the decision of SAG and ball mills influence the process characteristics?
SAG mills are used in the first stage of comminution where large size material (mill feed) is being fed to the mill and the characteristics of the material are not uniform. Ball mills are more suitable for later stages because they produce fine and uniform particle size. This depends on the grinding process that is to be done and the size of the particles that is expected at the end of the process.
What are the differences in particle size distribution when using SAG mills and ball mills?
SAG mills contain a broader size distribution of the larger particles due to the interaction between the rock particles and the steel balls that are used to impact the contents of the mill. This is ideal for the initial grinding where the size and capacity of the shell of the mill are of utmost importance. On the other hand, ball mills which use steel balls and where rock particles are not involved, produce a more uniform and finer particle size distribution. This makes ball mills the right equipment for applications that require specific particle size. The type of mill to be selected depends on the type of ore, the amount of the ore, the size of the particle desired and the inclusion of rock in SAG mills.