- Home
- Blog
- Equipment Info
- Mining Separation Techniques & Equipment: A Comprehensive Guide
- mmldigi
What is Mining Separation and Why It Matters?
As we enter the grand stage of extracting resources, everything hidden beneath the Earth yields an amazing bounty. Everything from the burdening rocks of iron ores to the less valuable raw materials is processed within it’s industrial separation and mining. It is also known that this extraction is not simply a technical practice, but a modern civilization’s foundation. The world we live in would cease to function without modern day machinery that utilizes copper wires to generate power for cities alongside skyscrapers created from iron ores. Every single valuable metal, raw material, or mineral undergoes this transformation.
Theoretically, without effective mining separation, it would be difficult to utilize the raw ore extracted from the earth. Think of digging a hole in a mountain, and trying to extract one single grain of gold. It is similar to a task of finding a needle in a haystack. Mining separation provides the means and processes to concentrate these minerals so that their further processing and use becomes economically reasonable. Also, efficient separation reduces waste, protects the environment and achieves the maximum recovery of precious minerals and resources that are often sought after, but limited in nature. As the world moves towards a more sustainable paradigm of resource management and conservation, it becomes ever so important to optimize mining separation. This is the part which unlocks the treasures of the world for civilization to utilize and converts what is deemed as only potential from earth into resources to bolster the industries and life itself. Hence, efficient ore extraction is paramount for the miners and the world’s economy.
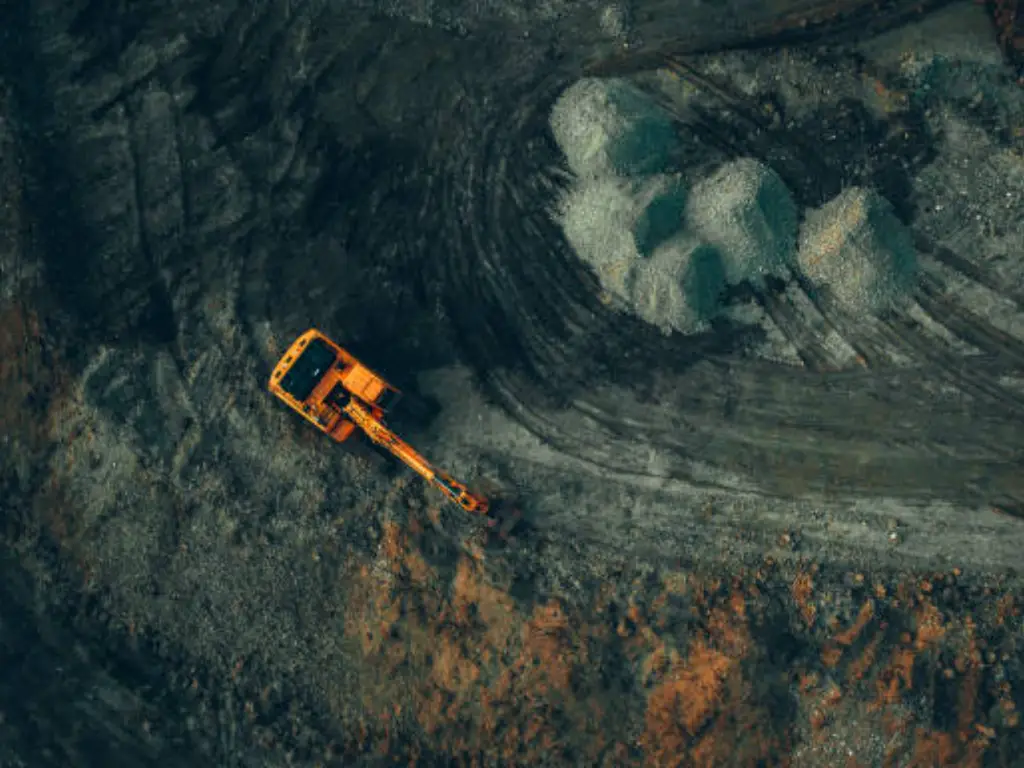
Key Mining Separation Techniques Explained
The field of separating mining involves a collection of methods that apply different physical or chemical characteristics of the minerals to separate them. These methods can be classified more generally according to the mechanism utilized.
Flotation is one of the most common which separates the minerals on the basis of hydrophobic minerals repelling water while hydrophilic minerals attract water.
Another major group is gravity separation which relies on the differences of specific gravity between the useful minerals and the worthless rock. This is the case for jigging, where solids are separated in a pulsing liquid medium, or spiral concentration, which relies on a combination of gravity and centrifugal force.
Magnetic separation is a potent strategy for targeting magnetic minerals. This minerals can be separated from non magnetic materials due to their selective attraction when a magnetic field is applied.
Finally, electrostatic separation is done when the concerned minerals have different electrical conductivities. There are some situations where specific valuable metals could be obtained from chemical processing by a method called solvent extraction.
Each of these primary techniques, which are often applied in combination or sequentially, serve as the backbone of the mineral processing engineer’s toolbox allowing swift and precise separation of minerals from the earth’s cradle. That is how mineral processing works.
Flotation: Principles and Applications in Mining
Flotation is a modern technique extensively used in mineral processing. It is based on the differential wettability of mineral surface and is quite simple yet effective. Think of tiny bubbles rising through a slurry which is a mixture of finely ground ore and water. Because of the treatment with certain chemical reagents called collectors, some mineral particles become hydrophobic and preferentially attach themselves to these air bubbles. These bubbles ascend to the surface and form a froth layer which float valuable minerals concentrate while the hydrophilic gangue stays in the slurry. Within the flotation cells, there is bubble-particle contact through agitation for proper mixing.
Flotation is applicable to many different types of useful minerals and is used for the extraction of copper, where it separates copper sulfides effectively from the other minerals. Gold, which is commonly found with sulfide minerals also benefits from flotation, as do lead, zinc, and molybdenum which is often recovered by flotation. The flexibility of flotation lies in its modification for different specific mineral systems by changing the amount and type of various reagents that are added such as collectors, frothers, or modifiers. The efficiency of flotation is an important issue for plant supervisors in mines. In contrast, some parameters such as particle size, diameter of pulp, and temperature have also to be changed to achieve better control of flotation and thus better performance of separation equipment.
Gravity & Magnetic Separation Methods Overview
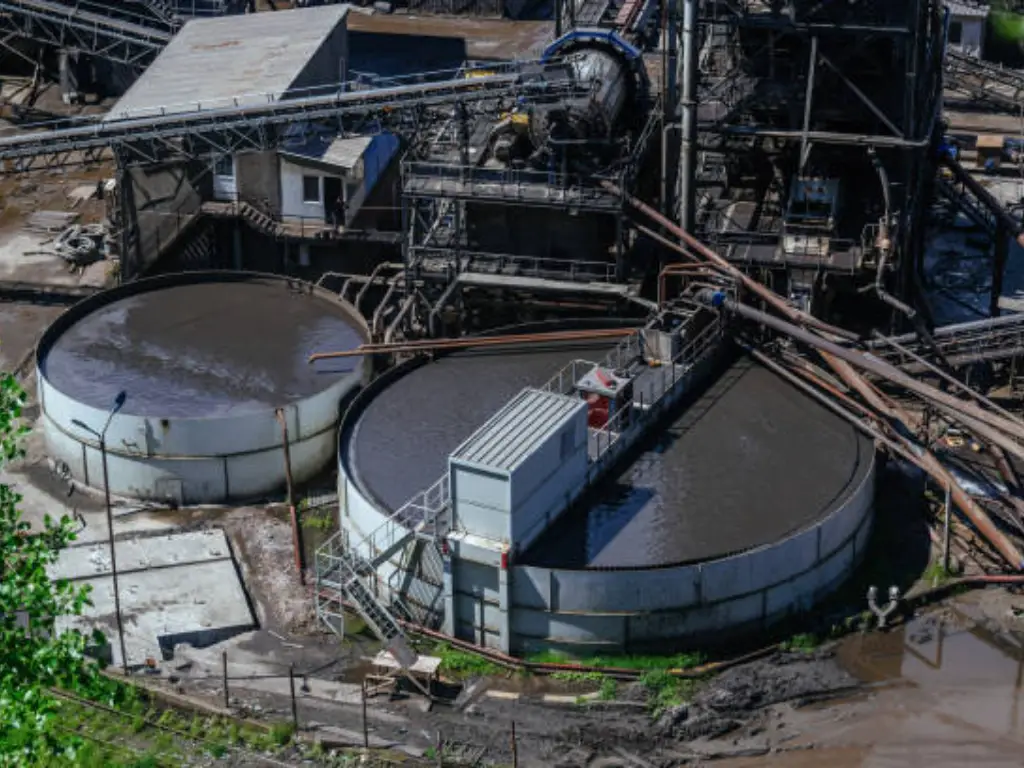
Even though flotation is widely used for fine-grained separations, magnetic separation and gravity separation methods still work remarkably well for coarser materials and specific minerals such as sands while being more economically favorable.
Gravity separation is based on the notion that denser materials sink faster to the bottom of a fluid medium. An example would be panning for gold. The denser gold particles settle at the bottom of the pan, while the sand and gravel are less dense and are washed away. Modern gravity separation methods like jigging use pulsating water flows to stratify particles based on density. A more complex version of this technique makes use of spiral concentrators, which have a helical trough. In these, the combination of gravity and centrifugal force make the denser minerals move towards the inner part of the spiral and leave the lighter gangue moving outwards. Shaking tables combine shaking motion and water flow above a riffled surface to achieve the separation of minerals of various densities.
Magnetic separation, however, uses the magnetic susceptibility of select minerals. This technique is very useful in the separation of iron bearing minerals, such as magnetite and hematite, from non-magnetic iron bearing gangue. There are various kinds of magnetic separators, from low-intensity ones that serve strongly magnetic minerals to highly intense ones which serve weakly magnetic minerals. Often, the magnetic particles are separated from the non-magnetic materials by the use of rotating drums or belts with permanent magnets placed at proper angles to attract and guide the magnetic particles.
Feature | Gravity Separation | Magnetic Separation |
---|---|---|
Principle | Difference in specific gravity (density) | Difference in magnetic susceptibility |
Applicable Minerals | Gold, tin, tungsten, chromite, iron oxides (some) | Magnetite, hematite, pyrrhotite, ilmenite (and some others) |
Particle Size | Generally effective for coarser particles | Effective across a range of particle sizes, including micron sizes |
Complexity | Relatively simple and low-cost | Can range from simple to complex, depending on intensity |
Key Equipment | Jigs, spirals, shaking tables, dense medium separators | Drum separators, belt separators, high-intensity separators |
As such, these two techniques, whether used in isolation or in combination with other techniques, offer effective alternatives and complements to flotation in the vast field of mining separation and ore concentration. When using these techniques, one should first assess the type of mineral ore being dealt with.
Essential Equipment for Effective Mining Separation
● Jaw crushers
● Cone crushers
● Ball mills
● Vibrating screens
● Hydrocyclones
● Flotation cells
● Shaking tables
● Magnetic separators
● Thicker
● Water removal units
● Drying units
The achievement of effective mining separation is dependent on the proper set of separation tools. Each has its own specific responsbility in a mineral processing plant. The initial phase begins with primary drilling and grinding activities using two progressively narrower jaw crushers, cone crushers, and ball mills. These serve to reduce the rough ore ROM and free the desired minerals within. Screening and classification devices employ vibrating screens and hydrocyclones that divide particles by size, ensuring proper feeding for the following primary separation processes.
Crucial to the separation is attachment of the bubble to the mineral, which takes places in flotation cells. Following gravity separation using jigs, spirals, shaking tables, magnetic separation the rest of the magnetic minerals are removed in various types of seperators. Also important to the piece process circuit in secondary handling of the slurries by slurry pumps, which transport thick mixes, and units that combine thickening and water removal from the concentrates. After this process, there is a need for further concentration by drying.
JXSC - Mineral Processing Equipment Manufacturer
To achieve reliable and energy effective solutions in mineral processing for a mining operation, JXSC would be a trusted partner. JXSC has positioned itself as a dominating manufacturer and supplier of an extensive range of mining equipment which comprise durable jaw crushers, efficient cone crushers, high-performance flotation cells and ball mills. There is no doubt JXSC is focused on the provision of tools required for effective separation mining. Our equipment is designed with a focus on durability, maintenance, and performance which enables mining companies to maximize their recovery rates and achieve their production targets while processing costs of the company are equally considered. Visit www.minejxsc.com and check out our catalog to see what we offer and how our services can help improve your mineral processing plant. Further visit our site for more information and contacts. We cater customers in Europe and other places in the world.
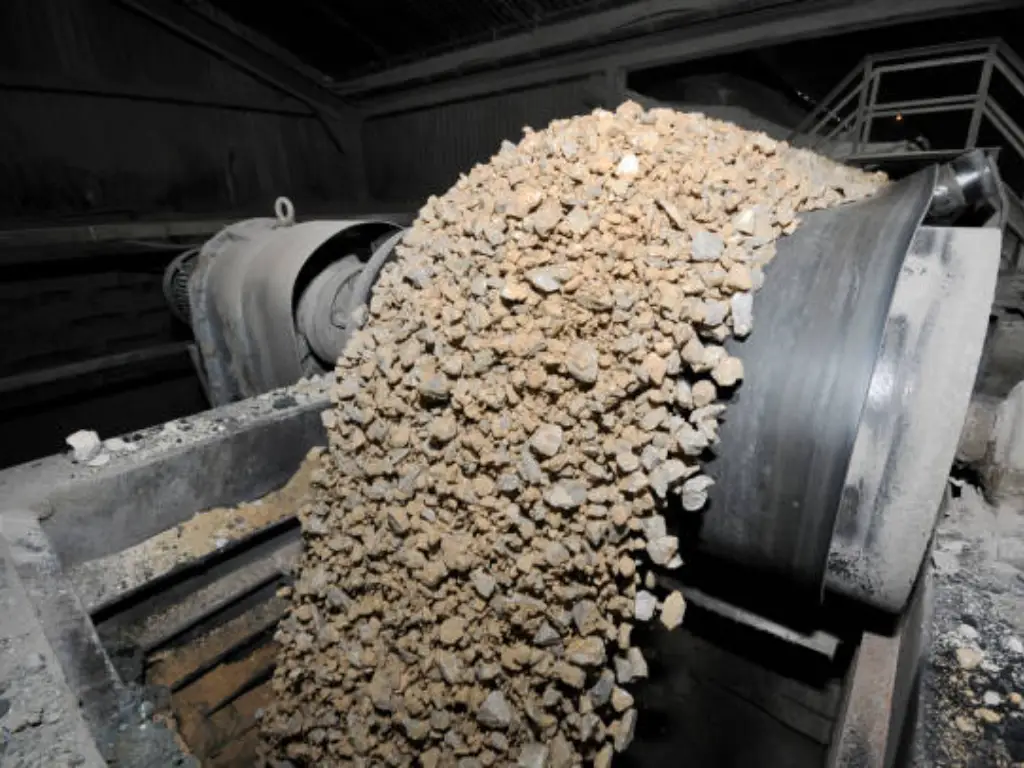
Factors Influencing Mining Separation Efficiency
Achieving optimal efficiency in mining separation is more complicated than deploying equipment; there are many details to consider.
The size of the particle is important. The minerals have to be freed from the accompanying gangue by crushing and grinding them into a reasonable granulation suitable for the separation method that has been selected. Not grinding enough will result in poorly liberated mineral particles, and grinding too much can waste energy and, in some cases, make separation very difficult. These indirect processes are controlled by quality assurance supervisors who are essential in managing these parameters.
The initial step known as “mineral liberation,” which heuristic poses as separation of valuable ore from gangue, determines roughly where the efficiency limit rests. Knowing the mineralogical features of the type of ore body is fundamental in deciding what the degree of optimum grinding is and what the separation strategy should be.
Also, pulp density, the ratio of solids to liquids in a slurry, is very much an important factor because it influences both flotation and gravity concentration effects.
For chemical processes and flotation, the pH and eh (redox potential) of the slurry are most important. Reagents that are put into flotation, like collectors, frothers, and modifiers, have to be selected as to their amounts so that the right minerals are caused to adhere to the bubbles of air made.
Last but not least, water quality is significant. Its pH and the ions that are in suspension has the most profound effects on the separation processes at hand. A complete understanding and control of these conditions is necessary to improve mineral recovery and lower dilution in tailings for environmental purposes.
Choosing the Right Separation Method and Equipment
The choice of the method of separation and the corresponding separation equipment comes down to a very important decision that is dependent on a multitude of factors, meaning it requires detailed knowledge of the ore and its associated characteristics as well as the goal. The mineralogical composition of the ore is the most important factor. Each of the various minerals has their own distinct physical and chemical processing characteristics that enables them to be subjected to a given separation process. For example, it is easy to perform flotation on sulfide minerals, as well as the gravity separation of dense minerals such as gold and cassiterite. Separating magnetic minerals is often straightforward due to the applicability of magnetic separation.
Issues of ore grade and the desired concentration grade are of considerable importance too. Economically viable concentrate grades may be unobtainable from low-grade ores without more aggressive and efficient separation techniques. The financial side including capital expenditure, processing costs, and energy expense remain critical for managers of the mining plants. The selected approach must be reasonable from a technical point of view as well as economical for the given mining operations. In addition, methods that reduce the use of water and energy, as well as the creation of hazardous waste, are now more frequently chosen because of environmental and sustainability concerns. The overall optimum is a balance of all these criteria which is seldom reached without pilot plant trials and expert’s judgment on the expected performance of separation equipment and methods on process efficiency and sustainability.
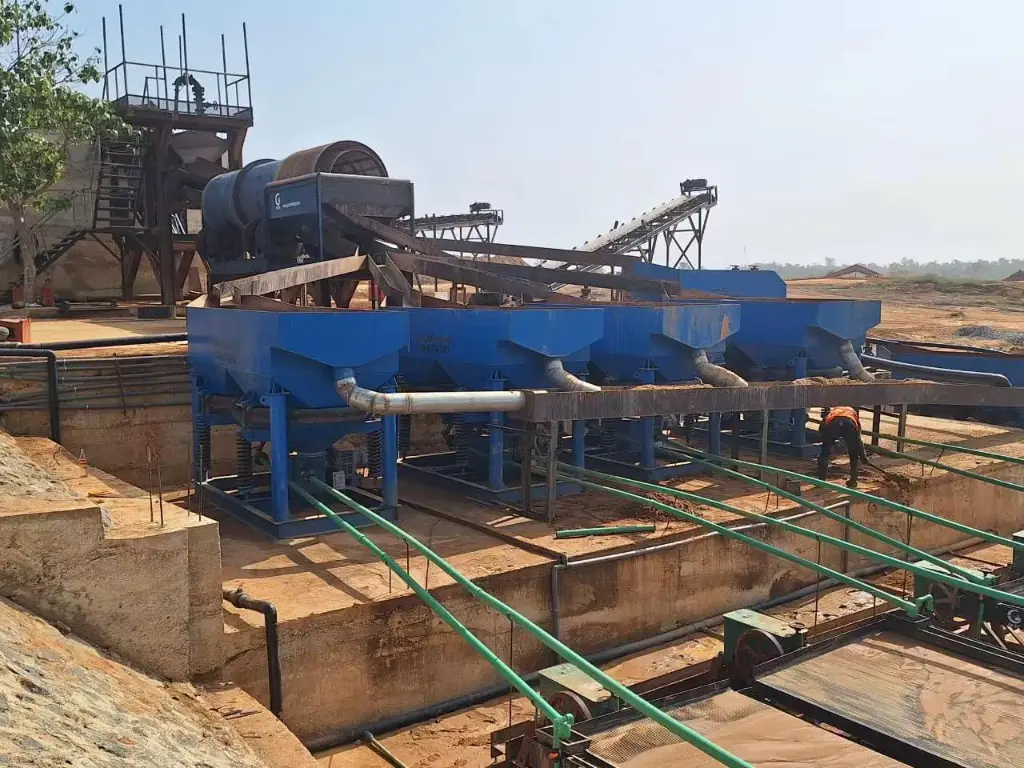