- Home
- Blog
- Equipment Info
- Mining Plant Guide: Types, Equipment, and Key Operations
- mmldigi
Different Types of Mining Plants Explained
Mining enterprises chiefly operate with one goal in mind to ensure the smooth and uninterrupted operation of these industries. They centralize all activities that go into the functioning of the company, such as taking out the raw ore from the earth for mineral processes that yield mineral concentrates or refined metals like gold, copper, nickel, etc. To comprehend their importance, it’s critical to appreciate the various categories on the basis of which these plants may be classified. Just like different branches of a tree or a shrub, a mineral processing plant diverges based on the specific minerals they process. An example would be a gold ore processing plant that uses different processes and equipment compared to a plant that processes iron ore. Similarly, the scale of operation dictates the complexity and design of the plant. A large-scale industrial operation will have sprawling complexes with sophisticated machinery while an artisanal mine will have a simpler setup. In addition, the methods chosen for an extraction and the process of owe greatly influence its typology. Physical separation techniques are applied by certain plants whereas others utilize chemical processes. For instance, there are plants with nickel with specific equipment that are modernized to concentrate the residual nickel to an optimum value and or several percent at the end product.
Grasping these differences is vital in beginning to value the complex realm of mineral processing.
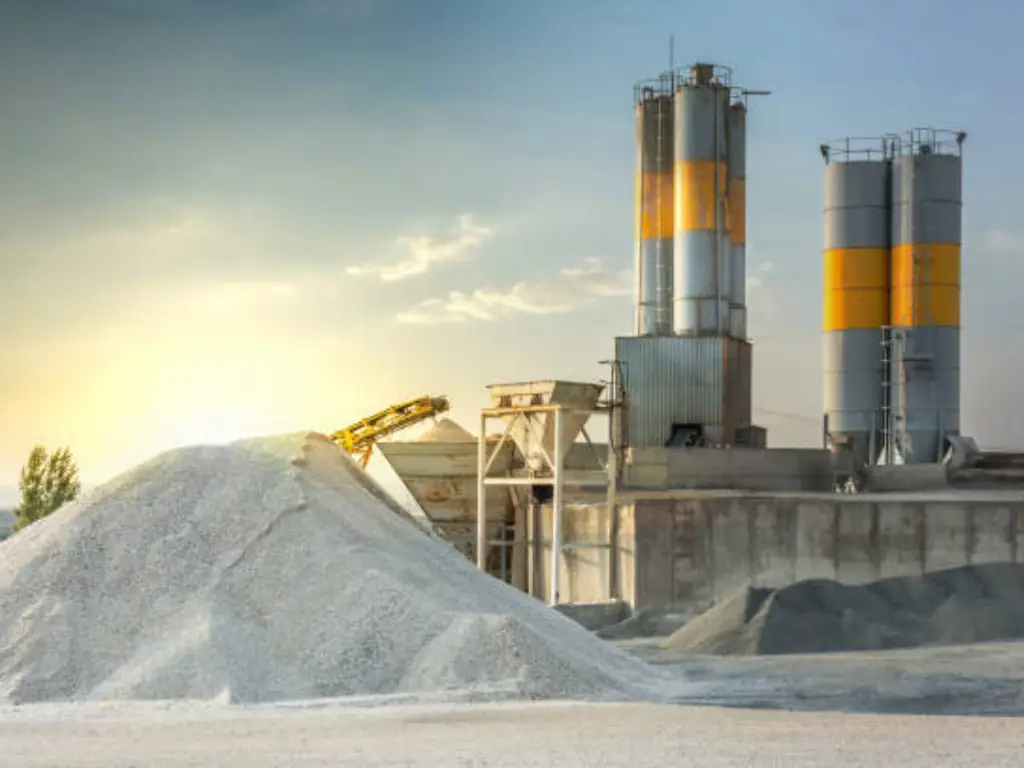
Essential Equipment in a Mining Plant
Every component of a mining plant functions coherently like a carefully choreographed symphony where every piece of heavy equipment plays a fundamental piece. The most complex machines to operate are the crushers, or the workhorses, which, as in the use of progressively smaller hammers to smash massive rocks, use multi-stage shredding to decrease the size of raw ores into smaller pieces. Relatively smaller chunks of rocks are next put in either rod or ball mills that grind them into extremely fine powder for refinement inbound processes. Imagine making coarse flour finer.
Flotation cells are critically important for most metallic ores and these cells do employ clever techniques to salvage precious materials separated from waste by employing chemical reagents in conjunction with air bubbles. For some magnetic ores, i.e. iron, strong magnets, and magnetic separators, can be utilized to grab and isolate the helpful materials. Rings or spirals that serve as jigs used in gravity concentration equipment can also serve heavier minerals by difference of mass or density. The concentrate from which the material is drawn for filtering or thickening is called the stage, where the ater supply is dramatically reduced, thus controlling the amount of moisture within the concentrates for better refinement and transportation.
Every piece of equipment is fundamental in the entire system of mineral extraction including robust crushers and delicate flotation cells. Facilities processing nickel or cobalt will have particular equipment designed for those metals.
Mining Plant Design and Layout
It is like sketching the design for an intricate industrial biome when it comes to creating a mining plant. There are many details that need to be examined to guarantee effectiveness, security, and also the financial aspects.
The plant’s site is the first factor of consideration. Having it located at the mining site greatly reduces transport costs. Likewise, having easy access to water and power is important. The process flow is the core of the design, determining the order in which the equipment is installed, so as to enhance material movements and eliminate bottlenecks. There are also restrictions regarding the spatial planning of the plant that needs to be taken into account. For example, there is a need for an adequate working space for equipment function, maintenance needs, and movement of people. Safety aspects are fundamental, they shape the location of emergency exits, showers, and safety ventilation. In addition, the design must provide some allowances for changes in the future, both in expansion and advancement of technology. There is also primary consideration that relates to the plant, such as the positioning of water, electricity, and compressions air pipelines. The costing design must also incorporate the efficiency of energy for economic profit.
The well-configured and strategically located mining plant can serve as the basis for a well-managed and sustaining mining activity which has the potential to occupy large extents ranging from some hectares.
Key Operational Processes in Mining
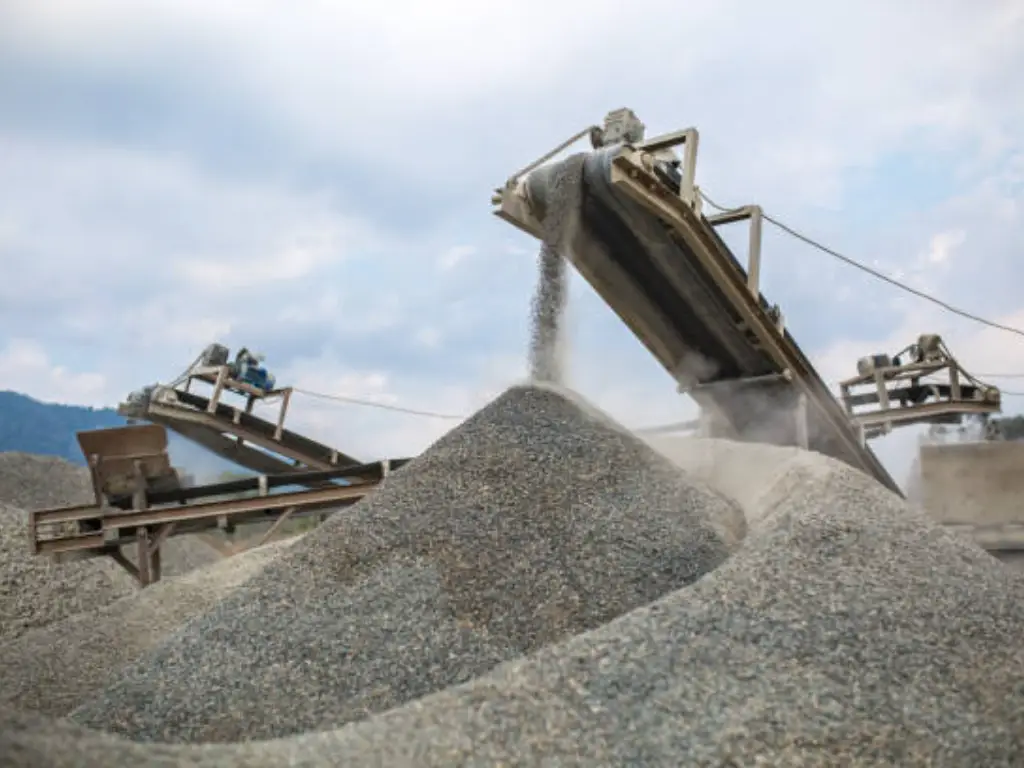
Mineral processing and separation rely heavily on the type of ore processed, so understanding basic concepts and procedures with the mining plant process of the ore in this miners plant is important. Following is a simplified overview of the methods involved.
1. Crushing: The first stage is mainly loosening the hard rocks causing bulges and easily cutting the reduced pieces.
2. Grinding: The primary step at this stage consists of turning the processed materials into powder form so they may be further processed. In doing this, powerful jaw-type crushers are used, thus allowing to unstuck the separates.
3. Mineral Processing (Separation): Mineral Processing (Separation): This is the center of the operation where techniques depends on the ore type:
● Flotation: Sulphide minerals are commonly used by this method which is dependent on surface chemistry. This method hinges on the selective attachment of minerals to air bubbles where they are separated from waste material.
● Magnetic Separation: Powerful magnets are used to attract and isolate the required materials in this technique that is effective for magnetic ores.
● Gravity Concentration: The separation of minerals based on density variation is accomplished with this method.
4. Dewatering: Generally in a slurry phase (solid particles suspended in a liquid), the valuable materials are contained after the separation stage. Further processing by dewatering enhances the value of the product by getting rid of excess water.
5. Tailings Management: The last and most important step is the controlled and safe disposition of remainder tailings.
Each of these steps, from the initial crushing to the final tailings disposal, is a critical link in the chain that transforms raw ore into valuable materials.
Environmental Considerations for Mining
Mining activities, by their very nature, entail considerable engagement with the environment. There must be forethought and strategies to lessen impacts where applicable, particularly regarding practicing responsible mining and climate change issues mining. Some of the primary environmental issues for mining plants are listed below:
● Wastewater Treatment: Effective methods ought to be put in place to remove contaminants before water used for processing is discharged so that the water is not harmful to water bodies.
● Air Emission Control: Dust and other airborne particles resulting from crushing, grinding, and similar operations ought to be managed to reduce their emissions into the air.
● Solid Waste Management: Planning and policies towards sustainable collection and disposal of tailings and other solid waste types; while trying to reduce land degradation and potential groundwater pollution should be put in place.
- Land Reclamation and Rehabilitation: Efforts to develop areas recouped post-mining should be aimed at integrating them into a more settable or natural ecosystem and should encourage the growth of desirable vegetation.
- Biodiversity Protection: Local vegetation and wildlife impacts such as habitat destruction and fragmentation should be dealt with in ways that its effects are lessened through mitigation measures.
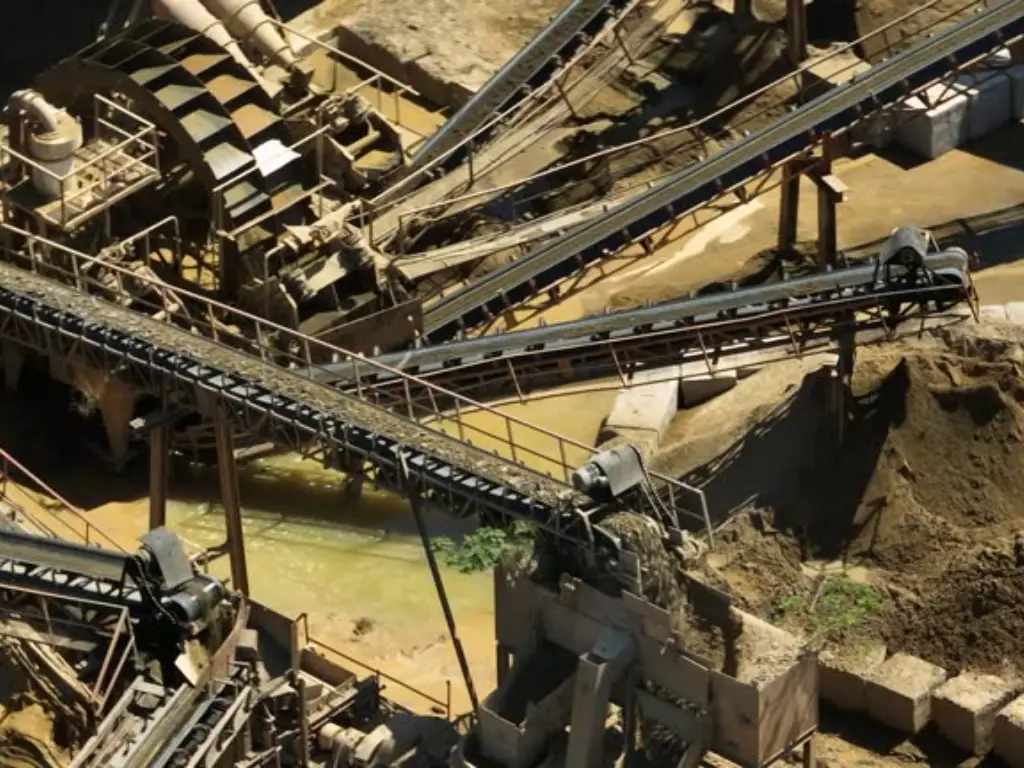
Advanced Technologies in Mineral Processing
Progress in the processing of minerals is necessitated by the increasing efficiency of achieving lower rates of environmental pollution, as well as for processing ores that are becoming increasingly complex.
Control and automation systems are becoming widely available and enhance the optimization and monitoring functions of plants. Data mining is enhanced with machine learning to anticipate and optimize a number of steps of the procedure. To address the operational and environmental challenges, new energy-efficient devices are being designed. In areas with limited water resources, dry processes which use little to no water are becoming more popular.
In addition, ARA initiatives are expected to provide programs that hope to transform the current state of the mining industry. New methods called phytomining extract nickel and cobalt from the soil with the help of specific plants called hyperaccumulators, with the primary challenge being how to bring such a method into practical application. The lower costs of mining, and as a result, higher profits from mineral mining encourage the application of new technologies that will meet the requirements of environmental protection legislation.
Choosing the Right Mining Plant Equipment
Choosing the right equipment for a mineral processing plant design is a daunting task. Mistakes in decision-making can directly affect the plant’s operational efficiency and profitability. The following is a checklist of specific requirements that must be addressed:
● Processing Capacity: The machinery should be able to accept the designed volume of ore.
● Ore Characteristics: Different kinds of ore require different equipment to process them. This includes everything from chemical makeup, density, and concentration of nickel or copper to the specific separation technologies used.
Property | Gold | Iron Oxide | Copper |
---|---|---|---|
Chemical Composition | Au | Fe², O³ | CuFeS² |
Density (g/cm³) | 19.3 | 5.26 | 4.1-4.3 |
Hardness (Mohs) | 2.5-3 | 5-6 | 3.5-4 |
Color | Yellow | Reddish-brown | Brass-yellow |
- Budget: The capital and maintenance expenditures can not be overlooked.
- Equipment Quality and Reliability: High productivity rates can be sustained with minimal downtime when reliable and robust machinery is employed.
- After-Sales Service and Support: Continuous operation of the equipment relies heavily on readily available spare parts and maintenance.
JXSC Mining Equipment: Your Trusted Partner
Selecting suppliers is key as not all partners have of reliable reputation. For those organizations who need trustworthy and quality mineral processing instruments, JXSC Mine Machinery does come to mind. We have a wide selection of gear alongside mineral processing for specialized services to cater to the requirements of different types of mining companies. If you wish to know more about how we can assist you in your mining projects, check our website at [https://www.minejxsc.com/]. Often, new investments in the mining sectors aid in the purchase of such important pieces of equipment.
Future Trends in Mining Plant Technology
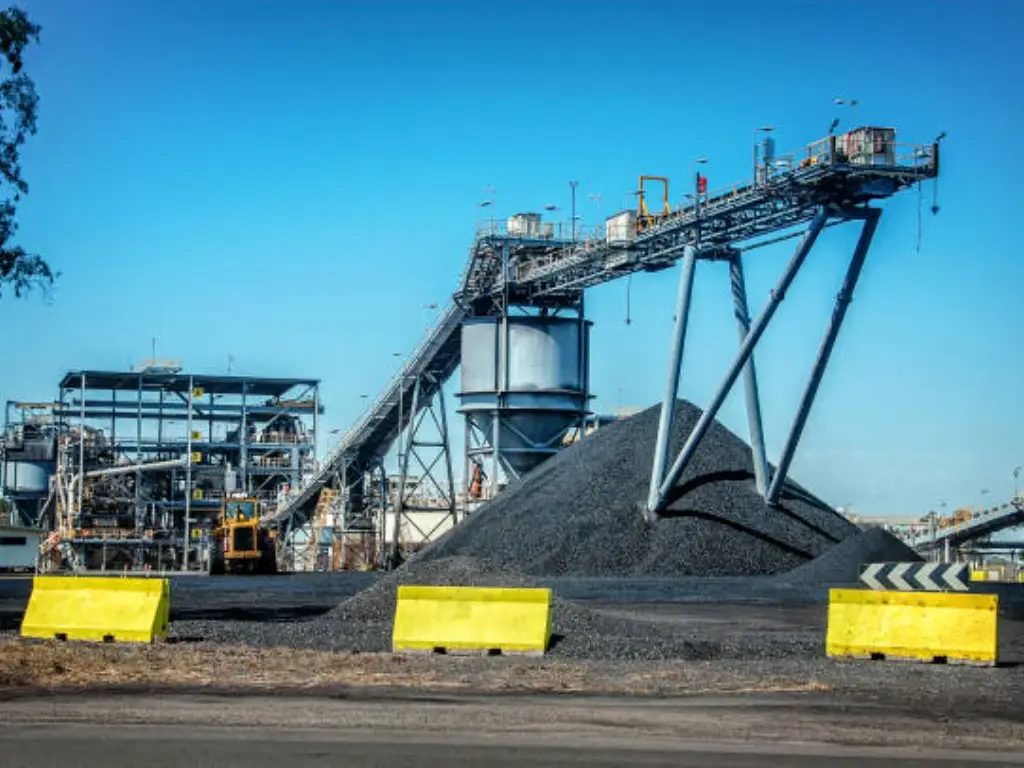
We should anticipate noteworthy enhancements in automation, eco-friendliness, and overall effectiveness for the future direction of mining plant technology. Greater use of artificial intelligence (AI) and machine learning (ML) algorithms to streamline processing activities and improve maintenance scheduling are within reach. These advances will facilitate a more precise approach toward operational decision-making. In parallel, the development of advanced sensor systems will make it possible to capture very detailed information, further improving system supervision and control.
Increasing focus on environmental mitigation, especially with regard to the rising concern for climate change, will act as a fundamental impetus toward innovation on resource minimization processing techniques. Additionally, it is anticipated that waterless processing approaches and better waste management systems will become the focal point as the industry pivots toward sustainable working methods. Also, the construction of modular and portable processing plants is likely to lessen the environmental harm caused by conventional immobile processing plants.
The ongoing research projects, combined with adequate funding, will most likely turn these technologies into reality. Some notable achievements may be the improvement in the phytomining of plants with higher biomass for the extraction of nickel and cobalt. These trends point towards a time when mineral processing plants are expected to increase productivity and also protect the environment, thereby improving irresponsible mining practices.