- Home
- Blog
- Mineral Solution
- Expert Tips for Optimal Mineral Processing Plant Design
What Is A Mineral Processing Plant?
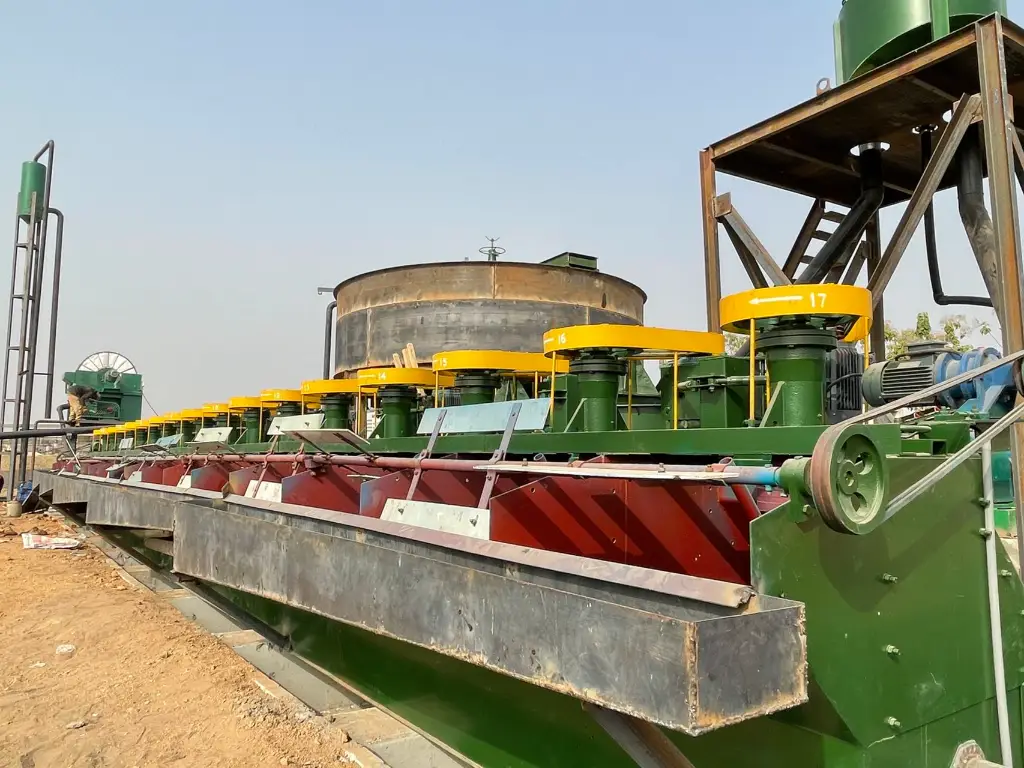
A mineral processing plant is an industrial site that engages in the process of treating mined ore to produce separate products from the gangue. The process comprises several steps such as crushing, grinding, flotation, adsorption and other separation steps and efficiency is possible in each step. These plants have a very significant function in the mining sector since the main aim is to extract as much of the deposit as possible while at the same time controlling the negative effects of the process on the environment. Due to scarcity of resources, effectiveness of these plants is very vital in order to achieve sustainable production.
There are several things to think about while designing a mineral processing plant; type of ores to be treated, the recovery standards expected, and the environmental standards that must be met. These processes will be well coordinated in a well designed plant to get the best results in terms of efficiency and yields with the use of advanced technologies in plant operations. In this regard, the design of a mineral processing plant cannot be viewed strictly in terms of the efficiency of the equipment but as the development of systems that can evolve to meet the changing needs of the industry while at the same time minimising the amount of waste produced and the impact on the environment.
Importance of Mineral Processing Plant Design
Consequently, the design of minerals processing plant and operation of a mineral is very crucial. A well-planned plant is a key to optimal utilization of resources, as well as the best way to minimize material losses. It covers spatial arrangement, equipment identification, process organization, and considerations on the environment. When these factors are considered, it will be easier for companies to increase productivity, minimize costs and guarantee that their operations are sustainable. Consequently, the design of minerals processing plant plays a central role in the sustainability and the ability of mining ventures to compete in the future.
Process Flow Of Mineral Dressing Plant
The process flow of a mineral dressing plant involves several stages, each designed to progressively extract valuable minerals from the ore. Here’s a detailed overview of the process:
Step | Description | Thermal Drying |
---|---|---|
1. Crushing | The ore is initially crushed to reduce its size, making it easier to handle and process | Jaw Crushers, Cone Crushers |
2. Grinding | The crushed material is further reduced in size to liberate the valuable minerals from the gangue | Ball Mills, Hammer Crushers |
3. Screening | Oversized material is separated from the desired size fractions to ensure effective processing | Vibrating Screens, Trommel Screens |
4. Gravity Separation | Dense minerals are separated from lighter gangue based on specific gravity | Shaking Tables, Spiral Chutes |
5. Flotation | Chemicals are added to create bubbles that selectively attach to valuable minerals, allowing separation | Flotation Machines, Mixing Tanks |
6. Dewatering | The separated minerals are dewatered to remove excess moisture before further processing or disposal | Filter Presses, Slurry Pumps |
7. Magnetic Separation | Magnetic fields are used to extract magnetic minerals from non-magnetic gangue | Magnetic Separators, Electrostatic Separators |
The Role of Automation in Enhancing Mineral Processing Plant Design
Automation is a key enabler in the optimization of the mineral processing plant design through the optimization of efficiency, precision and safety. Smart technologies enable plants to monitor and control processes in real time and make changes that would enhance the recovery of resources. Automations lower the dependency on human labor, meaning that the operational risks and costs are lowered as well. In addition, it is possible to make the right decisions that would improve the overall performance of the operators through the use of data analysis. With the development of automation, it will be an essential part of new designs of mineral processing plants in the future of the mining industry.
What Are The Equipments Used In The Ore Dressing Plant?
The success of an ore dressing plant largely depends on the equipment used throughout the processing stages. Various types of machinery are employed, each playing a vital role in mineral extraction and separation. Here’s an overview of some key equipment used in the industry:
Rock Crushers
Crushers are one of the most important equipment in the primary stage of operations in mineral processing. Some of the common types of crushers are jaw crushers that act as the initial stage of crushing where large ore pieces are broken down while others are secondary crushers such as cone crushers that further break the material into smaller sizes. Further, impact crushers and roll crushers are used where needed to get the ore to the appropriate size for further processing. This is done by ball mills and wet pan mills since they help in breaking down the material into smaller particles to enhance recovery of the minerals.
Flotation Machines
In the separation process, flotation machines play an important role in the process of separating valuable minerals from the ore. Flotation machines used in mixing tanks add reagents that cause the formation of bubbles that surround the required minerals. This process also increases the recovery rates and at the same time also increases the purity of the final product. The choice and management of flotation machines are one of the critical factors affecting the effectiveness of a mineral processing plant.
Gravity Separators
Gravity separators include gold concentrators and jig concentrators, which work on the basis of separation by density. Spiral chutes and shaking tables are also used to enhance the separation process that is conducted in the plant. These devices are essential in making sure that in mineral processing the higher value minerals are well recovered, thus making a big contribution to the overall resource yield.
Classifying & Screening Machines
Sorting equipment are crucial in making sure that the ore is sorted out properly before it is processed any further. Trommel screens and vibrating screens are used for size classification whereas spiral classifiers and hydrocyclones are used for additional classification. Gold trommel scrubbers are used in washing and sorting of the ore so that only the best material is taken through the other steps.
Magnetic Separators
Electrostatic separators and three-disc dry magnetic separators are used to improve the quality of the extracted minerals. High intensity magnetic separators are very effective in the concentration of fine particles from gangue. Through the use of these devices, mineral processing plants can enhance the quality of its products and at the same time, reduce for waste.
Tailings Management Equipment
This paper focused on the management of tailings in mineral processing with special emphasis on environmental impact. Infrastructure like the tailings dam and slurry pump are used in handling waste. The waste products of the mineral processing process are stored in tailings dams and the slurry pumps are used to transport the tailings without causing spillage and polluting the environment.
JXSC offers a full range of mineral processing equipment for your beneficiation plant or mineral processing company. Click mineral processing equipment manufacturers to boost your beneficiation efficiency and maximize recovery.
Successful Design Implementation Cases In Mineral Processing Industry
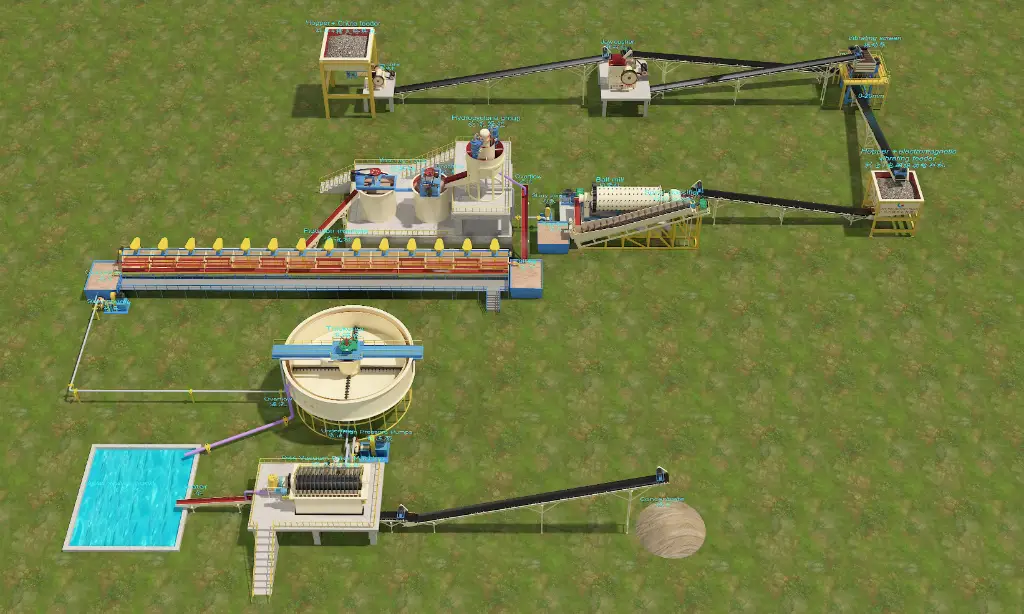
In Nigeria 120tpd lithium ore processing line, the raw ore is loaded by wheel loader and transported to the hopper and then fed to the jaw crusher by the chute feeder. The crushed material is conveyed by a belt conveyor from the jaw crusher to the fine jaw crusher where it is screened by a vibrating screen to get particles of size less than 20mm. Particles of size greater than 20mm are returned to the fine jaw crusher for further crushing. The screened material is discharged by a belt conveyor and is evenly fed to a ball mill for grinding through an electromagnetic vibrating feeder. The milled material is then fed to a spiral classifier; the overflow product goes to the next stage while the sand, which is returned to the ball mill for further milling, is taken. The material then flows into a hydrocyclone and then to a mixing tank, and then it is floated to process spodumene. The spodumene concentrate is taken to a thickener wherein the water that overflows is pumped to a sedimentation tank for its reuse and the thickener underflow is pumped to a disc vacuum filter to filter the nearly dry spodumene concentrate.
Want to get quick reference or valuable guidance about mineral procdessing plant design? Please Click mineral processing solutions to optimization pilot plant.
Factors Affecting The Design Of Mineral Processing Plants
● Ore Characteristics: The physical and chemical properties of the ore being processed significantly influence plant design. Variations in mineral composition and particle size require tailored approaches to ensure optimal processing.
● Regulatory Compliance: Environmental regulations must be considered in the design phase. Compliance with local and international standards is essential to avoid penalties and ensure sustainable operations.
● Technology Integration: The incorporation of cutting-edge technologies, such as automation and real-time monitoring systems, can enhance operational efficiency and reduce costs.
● Scalability: Designing plants with future scalability in mind is crucial for accommodating changing market demands and technological advancements. A flexible design allows for easy upgrades and modifications as needed.
● Cost Considerations: The overall project management must account for both initial capital expenditures and ongoing operational costs. A well-balanced approach ensures that the plant remains economically viable throughout its lifecycle.
Conclusion
If we are to consider the future of mineral processing plant design, the way forward is as follows. Stressing sustainability, efficiency, renovations, and adaptability will be crucial in responding to the needs of a constantly changing environment. By integrating the use of automation and data analytics, plants can improve its resource recovery and at the same time, reduce the adverse impact on the environment, thus, this makes this approach as the new standard text.
Furthermore, the implementation of the best design in the selection of the right equipment, the control of the tailing system will be a key factor in the success of the process control in the mineral processing plant especially in the new plant construction. Thus, there is still a great potential for further enhancement of the resource recovery efficiency as new methodologies and techniques are being discovered. The path to higher efficiency and sustainability of mineral processing plants is long, and the industry has to stay dedicated to the progress.
JXSC: Your Trusted Mineral Processing Expert
JXSC Mine Machinery Factory is a seasoned expert in providing comprehensive solutions and equipment for mineral processing plants worldwide. Established in 1985, we supply a wide range of mining equipment, including rock crushers, grinding mills, magnetic separators, and laboratory tools, while also offering EPC (Engineering, Procurement, Construction) services. Our experience spans across multiple minerals such as gold, copper, diamond, and more, with over 60 countries trusting our innovative designs and top-quality equipment. Backed by international certifications like BV and ISO 9001, we focus on advanced technology to meet the ever-evolving demands of the mineral industry, ensuring optimal plant efficiency and profitability.
JXSC is committed to treating customers as our highest priority, providing customized solutions to meet specific mining requirements, from engineering consultation to equipment installation and commissioning. Our experienced engineers deliver end-to-end services, including plant design, mineral testing, personal training, and management, all aimed at enhancing productivity and minimizing downtime. We pride ourselves on delivering reliable machines and solutions tailored to the unique needs of each project, making JXSC a trusted partner in achieving efficient, profitable mineral processing for over 37 years.
FAQs
What is the significance of tailings management in resource recovery?
Tailings management is crucial for minimizing environmental impact and maximizing resource recovery. Effective management practices ensure that waste materials are handled safely and efficiently, preventing contamination and resource loss.
How can energy efficiency be improved in mineral processing operations?
Energy efficiency can be enhanced through the implementation of advanced technologies, such as automation and process optimization. Additionally, using energy-efficient equipment and adopting best practices in operations can lead to significant energy savings.
What certifications or standards should be considered in mineral processing plant design?
It is essential to adhere to various industry standards and certifications, including environmental regulations and safety protocols. Compliance with ISO standards, for instance, can enhance credibility and ensure sustainable operations in the mineral processing sector.