- Home
- Blog
- Mineral Solution
- A Comprehensive Guide to Mineral Processing
What is Mineral Processing?
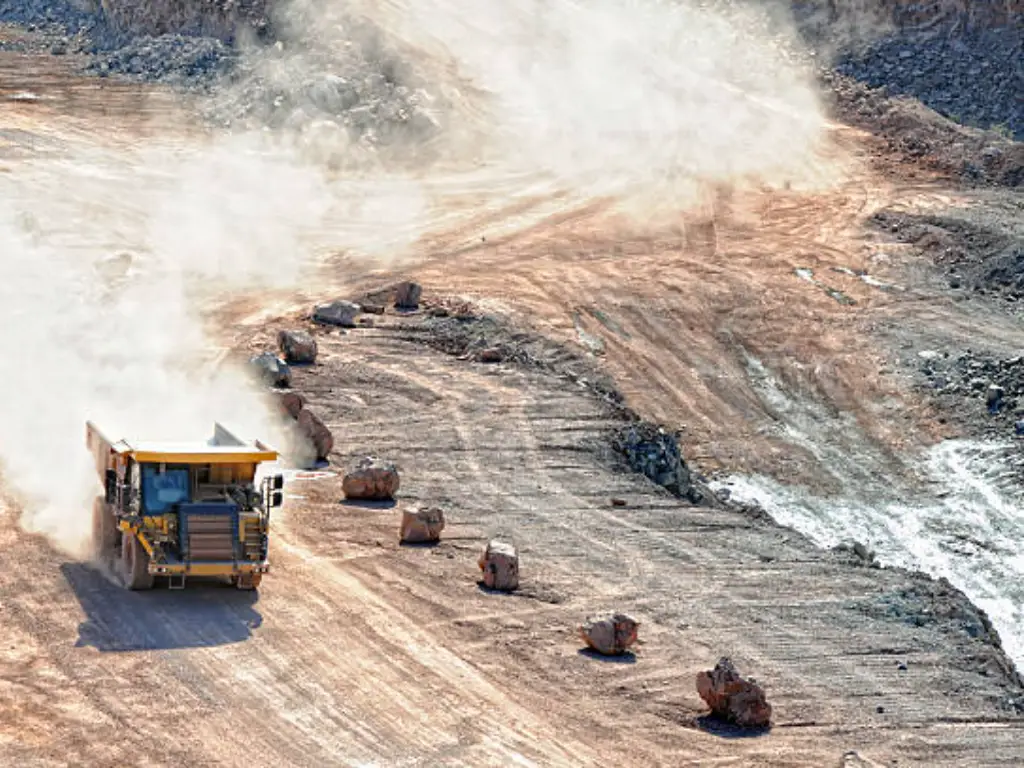
Mineral processing which includes the processes of crushing, grinding, dressing or beneficiation and concentration is an essential part of the extractive metallurgy. It is the techniques employed in the identification of valuable minerals from waste rock or gangue materials in order to improve on the market value of the ore. This process is very important in the mining industry because it defines the effectiveness and profitability of the extraction processes. In ore concentration, we make sure that only the valuable minerals are liberated to be recovered, hence minimizing the negative effects of mining.
In other words, mineral processing is the process by which mined materials are prepared and made suitable for handling and transport as well as for further processing. It includes a range of processes relevant to the features of the minerals and products with a focus on the throughput rate. Whether through crushing, grinding, concentration, or separation methods, the goal remains the same: in order to recover as much of the valuable minerals as possible while processing as little of the gangue as possible.
Key Stages of Mineral Processing
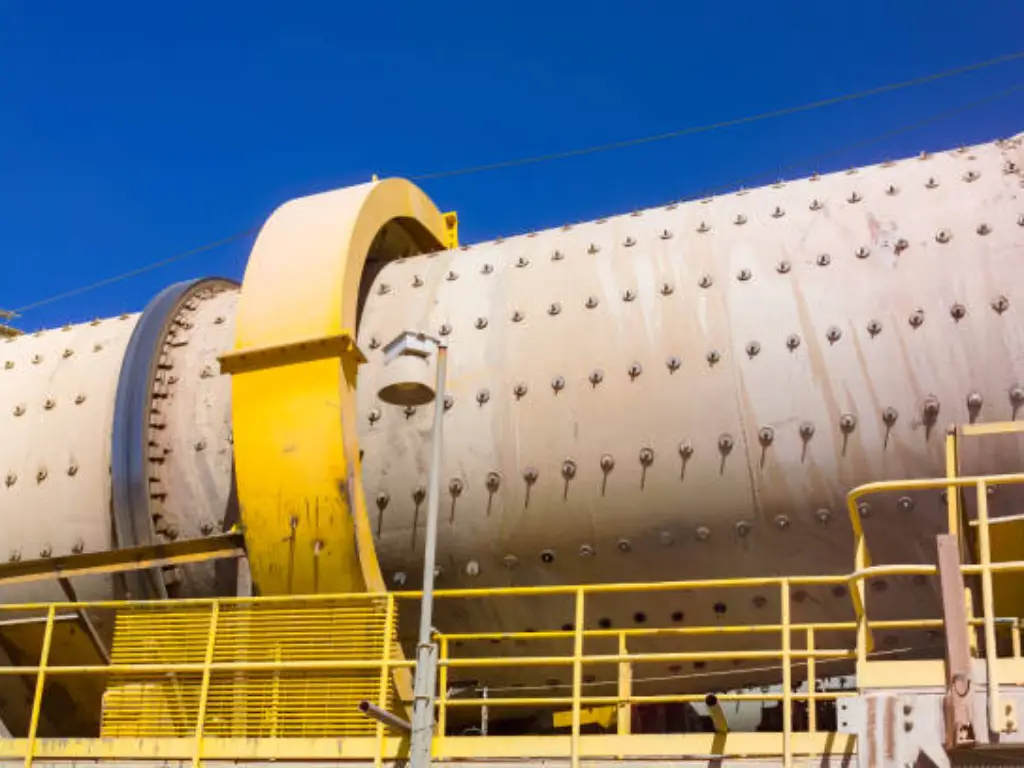
The mineral processing journey typically begins once ore is extracted from the mine and continues through various stages until the valuable minerals are isolated and refined. Understanding these stages is essential for optimizing recovery rates and ensuring efficient operation within processing plants.
Crushing and Grinding: The Fundamentals of Comminution
Comminution involves size reduction following two main operations which include crushing and grinding which play a main role in freeing up valuable minerals from earthing. In crushing operational stage, the enormous pieces of ore are crushed into fine size employing different kinds of crushers like, Jaw crusher, Cone crusher and Gyratory crusher. In addition to breaking down the size of the ore it also aids in the liberation of locked minerals within the waste rock.
After the process of crushing, grinding is done in grinding mills, for example, rod mills and ball mills. Here the ore is again finer reduced to size to improve its amenable to get separated from one another. The grinding process is critical to the operation since it determines the subsequent stages of liberation, and mineral concentration processes. Optimizing the comminution process results in higher internal floatation recovery of valuable minerals, lesser energy consumption, and operational cost.
Sizing and Classification: Techniques for Efficient Material Separation
After the ore has been crushed and ground, the next activity is to size and classify the material. This stage is important for effective classification of the material based on size and density of the particles. Several methods are used to sort the particles, with a view of grouping the ones that are of similar size.
Screening and hydrocycloning are some of the most widely used methods for particle size distribution and separation of particles. Screening involves passing the material through screens or mesh whereby the finer particles are passed through while the larger ones are retained. Hydrocyclones work on the principle of density differentiation through the use of centrifugal force in order to classify the materials in the right manner for the subsequent processing steps. This classification is essential when it comes to enhancing the efficiency of the separation techniques such as gravity separation and froth flotation in order to increase the percentage yield of the targeted minerals.
Concentration Methods: From Gravity to Froth Flotation
Concentration is the method of enhancing the proportion of valuable minerals in the ORE. Several methods are used depending on the nature of the minerals, their physical and chemical properties that are being processed. Gravity concentration separation is one of the oldest and simplest methods of separation based on the differential specific gravity of minerals. This method is most suitable for dense materials such as gold and tin bearing ores.
Conversely, froth floatation has emerged as the most popular method of enriching valuable minerals from the ore. In this method, chemicals known as collectors are introduced into a suspension of fine particles of the ore, with which the desired minerals selectively react. Bubbles are then released and the hydrophobic minerals float to the top of the slurry in the form of a froth which can be scooped off. This technique has brought a significant change in the processing of minerals since it enhances the recovery of numerous minerals such as copper, lead, and zinc.
Magnetic and Electrostatic Separation: Advanced Techniques in Mineral Processing
Magnetic separation and electrostatic separation are some of the sophisticated methods that cart exhibit the varied properties of the mineral. Magnetic separation is based, principal, on the ability of minerals separated to the magnetic field. For instance magnetic minerals such as magnetite can be easily separated from other non magnetic materials through application of magnetic forces hence this technique is considerately effective in iron ores processing.
While, in electrostatic separation process, the minerals are separated by their individual charges. In this method, a stream of particles is exposed to an electric field whereby charged particles go in diametrically different directions. Although this technique is particularly applied in the processing of mineral sands, which are a kind of industrial mineral, these minerals are often processed many times. Flotation and dense media separation are two of the most important methods of improving the efficiency of the processing of minerals for the purpose of separating value bearing minerals.
Dewatering in Mineral Processing: Methods for Efficient Water Removal
Dewatering is an important phase in the mineral processing process and is aimed at having most of the water content of the processed material separated in order to give a transportable and salable product. The objective of dewatering is to reduce the weight and volume of the material to be conveyed, thus reducing considerably ontransport cost.
Dewatering procedures include filtration, sedimentation and centrifuging as well. Filtration uses many types of filters to select on the basis of size while sedimentation use relies on enhancing particles density through gravity so that they may settle at the bottom. Centrifugation operates with the help of centrifugation forces as it is more efficient for disperse systems with fine particles. The purpose of the introduction of these dewatering methods is therefore to increase throughput in mineral processing plants while maturing the final product to meet market standards.
Types of Mineral Processing Equipment
Types | Stage of Use | Function | Applicable Ore Types |
---|---|---|---|
Jaw Crushers | Crushing | Primary size reduction of large ores | Coarse materials, metal ores (e.g., gold, copper, iron) |
Gyratory Crushers | Crushing | Coarse size reduction and material handling | Hard rock, large deposits (e.g., granite, basalt) |
Cone Crushers | Crushing | Secondary size reduction, producing smaller, uniform particle sizes | Medium to hard ores (e.g., copper, nickel) |
Rod Mills | Grinding | Fine grinding using steel rods to achieve particle liberation | Various ores (e.g., copper, lead, zinc) |
Ball Mills | Grinding | Ultra-fine grinding of materials, using steel balls for impact and abrasion | Ferrous and non-ferrous minerals (e.g., gold, silver) |
Spiral Concentrators | Concentration | Gravity separation of minerals based on density differences | Heavy minerals (e.g., gold, tin, coltan) |
Hydrocyclones | Classification | Size classification and density separation using centrifugal forces | Various ore types, particularly fine materials |
Magnetic Separators | Separation | Magnetic separation of ferromagnetic minerals from non-magnetic materials | Iron ores, industrial minerals (e.g., magnetite) |
Froth Flotation Cells | Concentration | Separation of minerals based on surface chemistry, using air bubbles | Copper, lead, zinc, and other sulfide ores |
Screening Equipment | Classification | Separating materials based on size, preventing oversize material from proceeding | All types of ores and aggregates |
Filter Presses | Dewatering | Solid-liquid separation to remove excess water from slurries | Processed ore slurries and tailings |
Thickeners | Dewatering | Concentrating slurries by allowing solids to settle and removing excess liquid | Tailings and mineral concentrates |
Dewatering Screens | Dewatering | Separating water from solids to produce a dry product | Final concentrate from various ore types |
Gravity Separators | Concentration | Using gravity to separate heavy minerals from lighter materials | Gold, diamonds, and other heavy minerals |
Centrifuges | Dewatering and Separation | Separating materials based on density and moisture content | Fine minerals and tailings |
JXSC provides quality equipment for boosting recovery rates. Explore mineral processing equipment to unleash mineral potential.
Applications of Mineral Processing Techniques
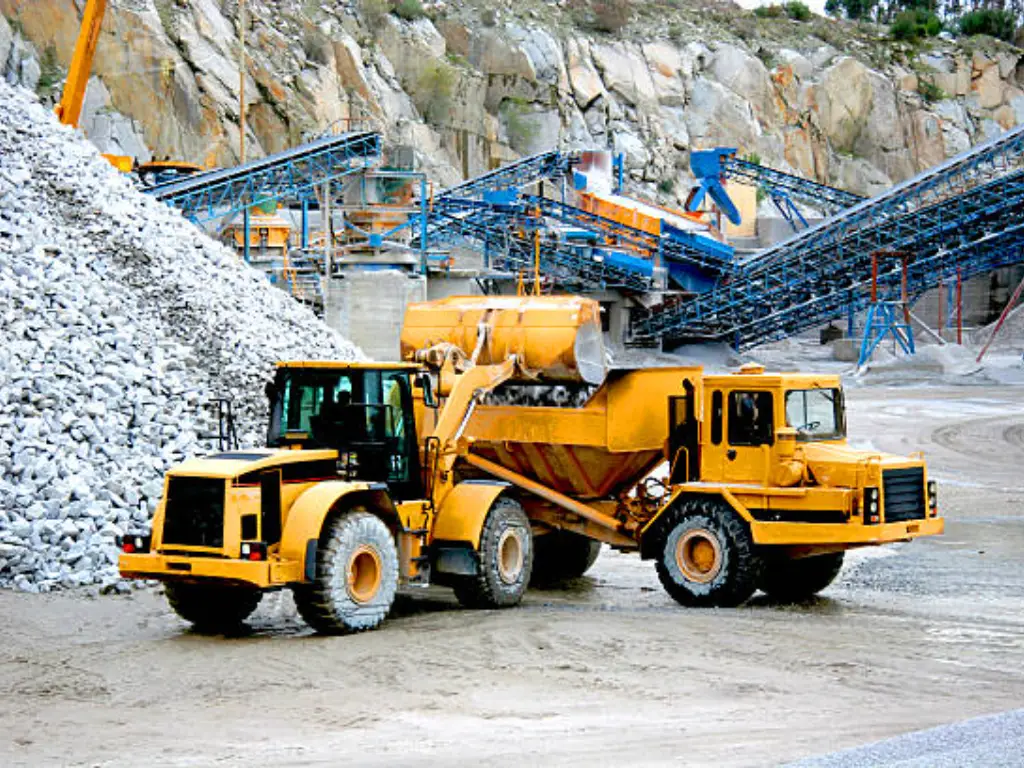
● Mining Industry (e.g., Gold extraction,Copper recovery,Iron ore processing)
● Construction Industry (e.g., Production of aggregates, Sand and gravel extraction)
● Chemical Industry (e.g., Processing of industrial minerals, Production of fertilizers)
● Environmental Remediation (e.g., Recovery of valuable metals from waste,Treatment of contaminated land)
● Recycling Industry (e.g., Recovery of metals from electronic waste, Processing of scrap metals)
Conclusion
Mineral processing is a critical intermediate link in the mining value chain and acts as the link between the extraction of raw ore and the generation of marketable minerals. Mineral processing does not only improve the recovery of valuable minerals but also supports sustainable mining through the optimal sorting of valuable minerals from waste rock. The tools and methods used in this area are crucial for achieving maximum production, minimizing adverse effects on the environment, and satisfying the increasing global demand for minerals.
The constant development of new technologies in mineral processing makes the subject even more relevant in the industry. As processing techniques are developed and enhanced to be more automated, the mining industry will be able to see better yields, less generation of waste and more friendly to the environment.
Maximize Recovery Rates Using JXSC Solutions
JXSC Mine Machinery Factory is one of the leading mineral processing companies because it provides clients with professional mineral processing equipment and solutions. JXSC is a company that has been in the mineral processing business for almost 40 years and has developed into a reliable company that offers innovative mineral processing technology that helps to increase the recovery rate of the processed materials. JXSC equipment and technologies are used in more than 200 mining projects around the world, with high recovery rates of 90-95% for different minerals. This level of performance is a clear indication of JXSC’s competence in mineral beneficiation and its capacity to help clients to get the best out of their ore processing business.
Besides, JXSC provides not only the superior equipment but also the professional services, such as engineering consulting, technical flow chart designing, and service supporting. Through the combination of the latest technology and a customer-oriented strategy, JXSC offers solutions that eliminate the challenges of mineral processing. The engineers at JXSC are highly professional and always ensure that they consult with the clients to come up with the best mineral processing equipment that will improve on the efficiency of the plant and at the same time minimize on the time that the plant takes to be on a break. This focus on innovation and customer satisfaction makes JXSC a preferred partner in the mineral processing industry where the recovery rates and costs are the key factors that determine success. No matter it is gravity separation, flotation or magnetic separation, JXSC is committed to solving the mining problems and providing the best solutions for clients.
FAQs
How does mineral processing differ from extractive metallurgy?
Mineral processing is mainly concerned with the separation of the mineral of interest from the gangue or waste rock through physical means such as comminution and concentration. This process is important in the preparation of the ore for extractive metallurgy, which is the chemical process of extracting metals from the concentrated material that has undergone mineral processing. For example, while mineral processing may entail the use of a conveyor belt to transport crushed ore, extractive metallurgy will proceed with processes such as pyrometallurgical processes to purify the extracted metals.
What role does water play in mineral processing?
Water is used in large quantities in the mineral processing process plant and is used in many different stages of the process. It has various functions including helping in the grinding process by preparing a slurry that includes the ore and assisting in the process of sorting out valuable minerals from the gangue materials. Process water is also required for the management of the material bed in flotation cells and the running of devices such as wire mesh screens and wedge wire screens. Furthermore, the size distribution of the particles in the process water must also be controlled in order to achieve the best results of the separation process.
What is the significance of particle size in mineral processing?
Particle size is a critical factor in mineral processing because it determines the efficiency of the separation techniques to be used. Lower sizes of particles generally result in improved liberation of the valuable minerals, which in turn increases the rates of recovery. In the grinding process, the material is further ground with the help of steel balls to make it as fine as possible to pass through the screen deck. Control of particle size distribution is important because larger particles may not be able to move relative to one another and this results in inefficient separation and poor processing results.
How do different minerals affect the processing techniques used?
Some of the minerals have specific physical and chemical characteristics that dictate the right method of processing. For instance, magnetic minerals can be separated using magnetic separation methods while others can be separated using froth floatation based on hydrophobicity. The extraction of nickel can be done through various methods such as gravity separation and chemical extraction depending on the type of the ore. The list of reasons for choosing certain techniques includes mineral content, the level of purity that is expected and required, and the relative motion of particles in the circuit that determines the efficiency of the recovery.