- Home
- Blog
- Mineral Solution
- Mastering Magnetic Separation in Mineral Processing
- mmldigi
Introduction to Magnetic Separation in Mineral Processing
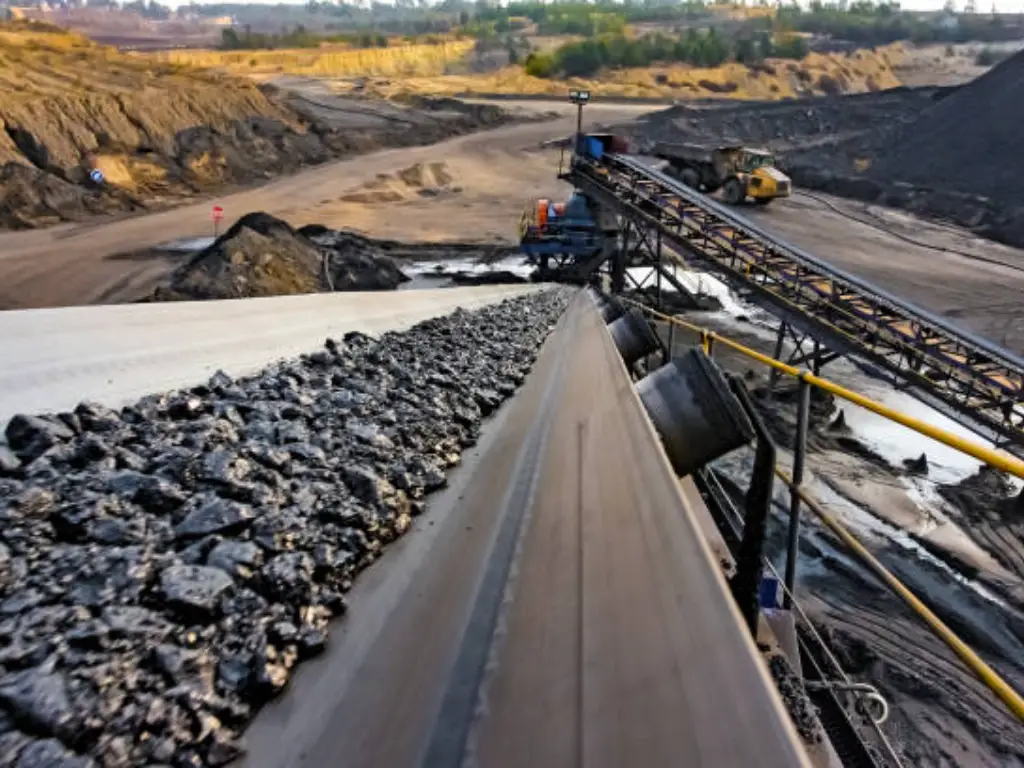
Magnetic separation not only enhances the effectiveness of the industrial mineral processing operations but also enhances the quality of the raw material by separating the unwanted impurities. High intensity mineral processing methods have been enhanced by new magnetic separation technology including high intensity magnetic fields and equipment. These advancements make it possible to separate fine magnetic particles with higher accuracy, hence improving the purity of the final product and the overall performance of various industries.
Magnetic Separator vs. Electrostatic Separator
Feature | Magnetic Separator | Electrostatic Separator |
---|---|---|
Purpose | Separates magnetic minerals from non-magnetic ones | Separates particles based on electrical conductivity |
Nature of Materials | Works on magnetic minerals like iron ore, magnetite | Works on both conductive and non-conductive materials |
Working Principle | Uses magnetic fields to attract and hold magnetic particles | Uses electrical charge to attract oppositely charged particles |
Materials Separated | Iron ore, magnetite, hematite, manganese, ferrous metals | Rutile, zircon, monazite, ilmenite, silica sands |
Operation | Employs magnetic drums, pulleys, or rollers to sort materials | Employs electrostatic plates and rolls to separate materials |
Types of Materials | Magnetic substances, ferrous metals | Conductive and non-conductive minerals |
Magnetic separators employ an external applied magnetic field to pull out magnetic materials such as iron ore and ferrous metals. These machines work on the principle of applying magnetic force to pull out fine particles from the feed material. Electrostatic separators, on the other hand, work based on the conductivity of the minerals, whereby electrical fields are used to separate conductive and non-conductive materials. Both techniques are useful in the process of sorting out different minerals based on their physical and chemical characteristics.
For more information on separation techniques, check out Understanding Electromagnetic Separation: A Comprehensive Guide and gain comprehensive knowledge.
Key Principles of Magnetic Separation in Mineral Processing
Magnetic separation is based on the differences in magnetic properties of the minerals present in the ore. Magnetic susceptibility defines the behavior of a mineral in a magnetic field. The process operates on the principle of magnetism where magnetic particles are attracted to the magnetic field hence can be separated from non-magnetic particles. The magnetic minerals are attracted towards the magnetic surface by applying a strong magnetic field, leading to efficient separation while non-magnetic particles are separated effectively behind. This selective separation makes it possible to extract the product in the most efficient manner and, at the same time, achieve the highest level of purity.
In mineral processing, magnetic separation is most useful for the recovery of ferromagnetic minerals, tramp iron, and the removal of the magnetic fraction as contaminants from the feed. Some of the principles include; enhancing the field intensity, controlling the size of feed material, and achieving the right separation efficiency to obtain the right concentrate.
Learn more about the fundamental concepts behind effective magnetic separation by clicking Mastering Magnetic Separation Method: Unlocking Power.
Factors Affecting Magnetic Separation Efficiency
● Magnetic Field Strength: The degree of the magnetic field determines the effectiveness of the separation process. Higher magnetic field intensity means that more magnetic particles are extracted from the slurry, especially the weak magnetic minerals such as hematite.
● Feed Particle Size: The size of the feed material has a direct impact on the separation efficiency of the equipment. The magnetic separation of fine particles is more effective than that of coarser materials, but the latter may need to be adjusted to the magnetic separator.
● Magnetic Susceptibility: Magnetic susceptibility varies from one mineral to the other depending on the type of mineral. Magnetic separation is more effective on minerals with high magnetic susceptibility while low magnetic susceptibility minerals may need enhanced magnetic separation methods.
● Feed Rate: The rate at which material is fed into the magnetic separator affects the process. A slow feed rate means that the magnetic minerals spend more time in contact with the separator, hence improving the efficiency of the separation.
● Moisture Content: Magnetic separation is another process that can be affected by high moisture content in feed material. When the material is wet, the particles tend to stick together, which makes it challenging for the magnetic forces to sort them correctly.
Types of Magnetic Separators Used in Mineral Processing
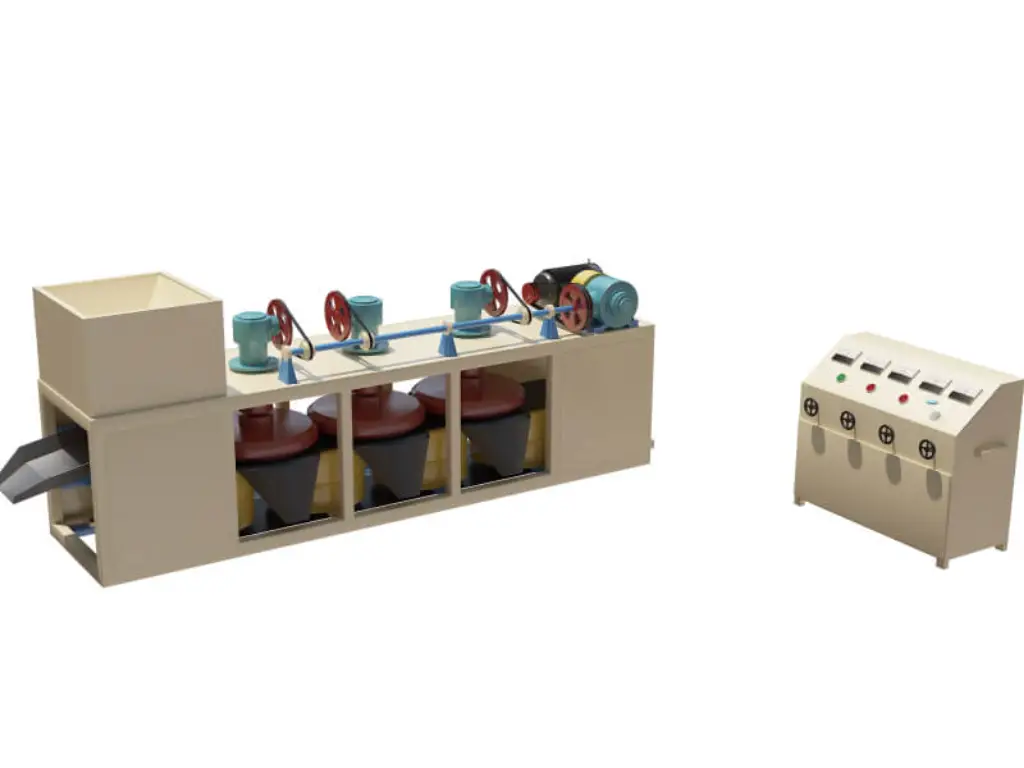
The choice of the right type of magnetic separator depends on the nature of the material to be separated and the type of separation required. Every kind of separator has its own function and works under different conditions.
● Dry Drum Magnetic Separators: These separators are used for dry material mainly for the separation of coarse ferromagnetic materials. They are used in mining for iron ore processing, where they are utilized in conveyor belt systems to recover iron rich fractions, including fine iron, from raw feed. The magnetic drum attracts ferrous metals from non-magnetic materials as the feed passes through.
● Wet Drum Magnetic Separators: These are employed in the wet processing of fine magnetic particles, especially in the mining of iron ore, to recover magnetite. These are water-based separators that enhance the high efficiency of the separation by allowing the magnetic minerals to stick to the drum while the non-magnetic materials are washed away.
● Magnetic Disc Separators: These separators are widely employed in the separation of fine, magnetic minerals. They comprise of several discs which rotate within a strong magnetic field to attract magnetic minerals such as monazite and ilmenite from non-magnetic materials. It is very efficient in the processing of rare earth minerals and mineral sands.
● High-Intensity Magnetic Separators: Intended for the separation of weak magnetic minerals including hematite and manganese, these separators generate a powerful magnetic field that attracts fine, low magnetic materials. They are applied in dry and wet processes depending on the type of the ore and the required processing.
● Eddy Current Magnetic Separators: These separators are best suited for recycling where a rapidly rotating magnetic drum generates eddy currents that repel non ferrous metals such as aluminum and copper. They are commonly applied in the recycling industry to sort metals from the rest of the waste.
● Overbelt Magnetic Separators: These separators are located above conveyors and are employed for the extraction of ferrous materials from bulk materials in mining industries. The magnetic force attracts magnetic particles from the moving feed to guarantee product purity and to eliminate metal inclusion in subsequent processes.
● Induced Roll Magnetic Separators: These separators are used for the fine separation of minerals which have different magnetic properties. They are commonly employed in the concentration of materials such as feldspar, silica, and quartz through the application of induced magnetic fields created by the rolls to separate weakly magnetic minerals.
JXSC‘s magnetic separator can be customized according to application requirements. Check out the magnetic separator machine to learn more.
How to Select the Right Magnetic Separator for Your Mineral Processing Needs?
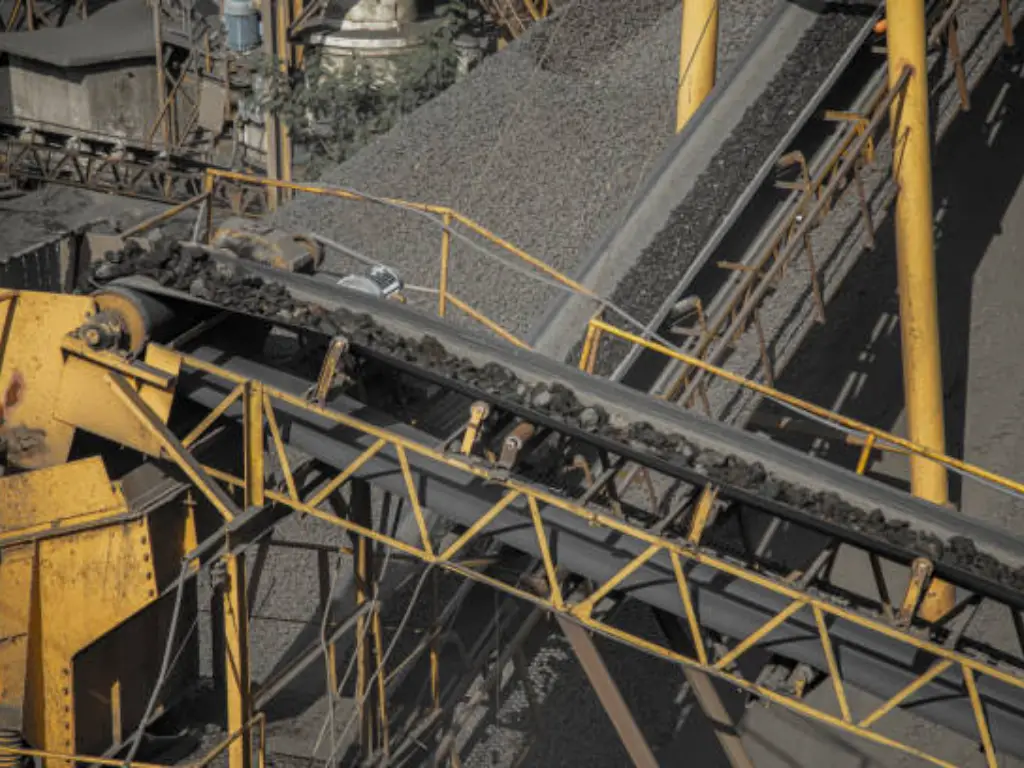
● Material Type: Determine the magnetic properties of the minerals to be separated and the size of the particles. Select a separator that is capable of meeting the demands of the properties of the feed material.
● Processing Environment: It is also important to decide whether the material will be processed in a wet or dry environment. Wet drum separators are used in wet environments while dry drum separators are used in dry environments.
● Particle Size Distribution: The size range of the feed material affects separator performance. Fine particles may need high power separators while coarse particles may be separated using normal drum separators.
● Field Strength Requirements: Assess the magnetic field strength that is required to efficiently recover weak magnetic minerals. In some cases, high-intensity separators may be required for the material such as hematite or siderite.
● Processing Capacity: Make sure that the selected magnetic separator has the capacity to sort the amount of material in your process. Large scale mining may need high capacity, robust separators to ensure that throughput is sustained.
Cost-Benefit Analysis of Magnetic Separation in Mineral Processing Plants
The application of magnetic separation equipment can be very cost effective for mineral processing plants. Magnetic separators help in minimizing waste and enhancing the efficiency of the use of raw materials since it enhances the purity of the product and the recovery rates. This translates into a fast return on investment (ROI) as less energy and time is used in other purification processes. Also, the use of high-quality magnetic separators has low maintenance costs, hence lowering the operational costs in the long run. Taking all these factors into account, magnetic separation technology is still a cost-efficient method for mineral processing companies that want to increase productivity.
Conclusion
The development of magnetic separation technology in the future is focused on increasing the efficiency and resource-saving. High gradient magnetic separators, new energy efficiency, automation and sensor technologies are expected to be the key drivers of the industry in the future. With the increasing need for resource recovery and mineral purification, there will be a need for more accurate and energy efficient magnetic separation technologies.
JXSC Magnetic Separators for Versatile Applications
JXSC is a professional manufacturer of magnetic separators and offers magnetic separation equipment according to the characteristics of the mineral processing plant. JXSC has a CAD and 3D design team that can provide detailed layouts of the product and process within 24 hours and present the clients with a 3D video of the whole setup. This means that every solution is tailored to the specific mineral type and the processing needs of the mineral. The magnetic metal separators of JXSC are designed with changeable magnetic field intensity to meet the requirement of different minerals and materials, including weak magnetic minerals and ferromagnetic materials, to provide the best separation effect for each project.
Also, JXSC’s factories have modern equipment to produce equipment and accessories for mining quickly and pack them according to the needs of mining companies worldwide. JXSC is capable of manufacturing separators according to the clients’ requirements and providing the mining solutions in 20-40 days, which is much shorter than the average time. This speed, coupled with a profound knowledge of mineral processing, makes JXSC a trustworthy collaborator for clients who want to obtain high-quality and cost-efficient magnetic separation equipment as soon as possible.
FAQs
What are the environmental benefits of using magnetic separation in mining?
Magnetic separation is also friendly to the environment since it does not require the use of chemicals and the generation of waste. It also helps in the reduction of the environmental effects of mining and the energy needed in the processing of materials.
What minerals have high magnetic susceptibility?
Magnetic minerals are those that have high magnetic susceptibility and are easily attracted to magnetic fields hence can be easily separated in magnetic separation processes. Some of the examples are magnetite (Fe₃O₄), which is one of the most magnetic minerals and pyrrhotite. Other minerals that are known to be magnetic include ilmenite and hematite, but they are less magnetic than magnetite.
What is the role of magnetic field intensity?
The strength of the magnetic field used in separation depends on the magnetic field intensity. Higher intensity fields are required for the separation of weak magnetic minerals such as hematite, while lower intensity fields suffice for strong magnetic minerals such as magnetite. Changing the field intensity makes it possible to achieve better separation of the minerals depending on their magnetic characteristics, thus enhancing the efficiency of the separation process.