- Home
- Blog
- Equipment Info
- Comparison Guide: Jaw Crusher vs Cone Crusher
- mmldigi
Jaw crushers and cone crushers are broadly utilized within the mining industry. They play a significant part in mineral handling. These crushers exceed expectations at breaking down different mineral minerals into littler pieces. This makes it less demanding to extricate profitable materials. A report by Amazing See Investigate gives curiously information. The worldwide crusher advertise was esteemed at around USD 1.73 billion in 2020. It is anticipated to develop at a CAGR of 8.1% from 2021 to 2028. The expanding request for crude materials in development and mining drives this development. Jaw crushers and cone crushers are exceedingly effective and flexible. They can handle a wide run of mineral metals, and this makes them fundamental within the mining industry. Their capabilities have altogether contributed to the market’s development. In this article, we are going explore the key differences between jaw crushers and cone crushers. This data will assist you in deciding the foremost appropriate crusher for your particular mining prerequisites.
Different Working Principles
Jaw Crusher Working Principle
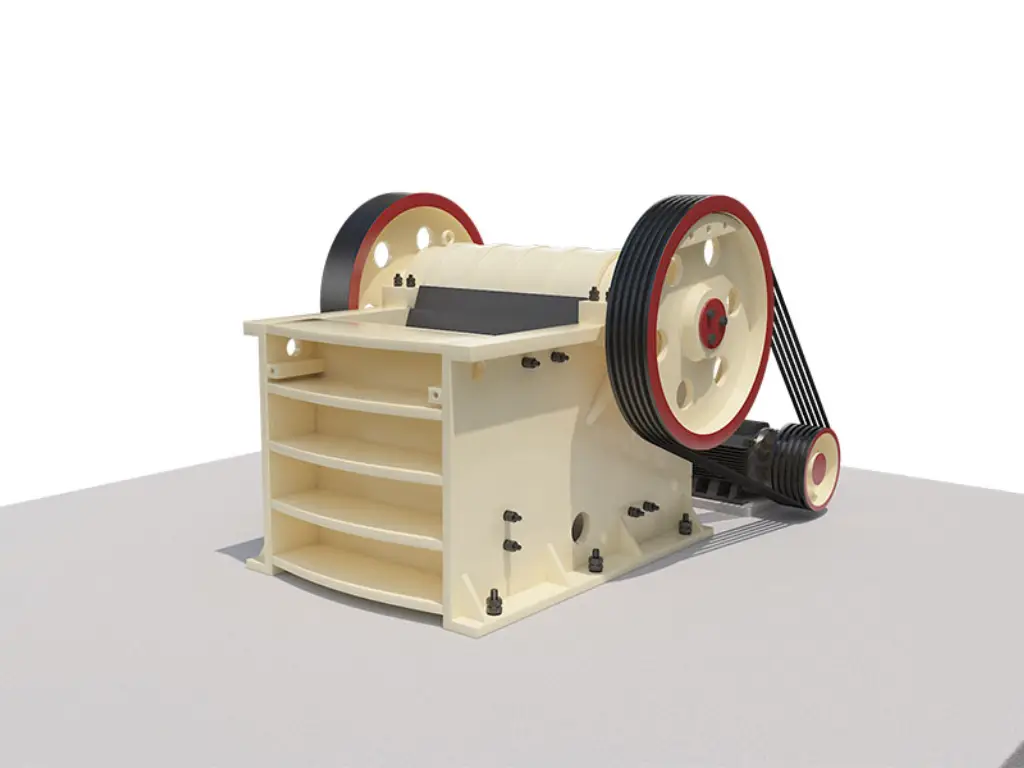
Jaw crushers work on a straightforward but efficient principle of compression. They have several key components. These include a fixed jaw plate and a movable jaw plate. An eccentric shaft and a toggle plate are also part of the design. The movable jaw plate is attached to the eccentric shaft. A motor or engine drives this shaft. As the eccentric shaft rotates, it makes the movable jaw plate oscillate back and forth. This creates a crushing action against the fixed jaw plate. The crushing action uses compressive force.
The crushing process starts when raw material is put in the crushing chamber from the top. The movable jaw plate moves toward the fixed jaw plate. It compresses and crushes the material. The crushed material then falls through the gap between the jaw plates. This gap is called the closed side setting (CSS). The material comes out of the bottom of the crusher.
The size of the crushed product depends on the CSS. You can change the CSS by moving the toggle plate. A smaller CSS makes a finer output. A larger CSS makes a coarser product. Jaw crushers usually have a reduction ratio of 4:1 to 9:1. This means they can make the feed material up to 9 times smaller in one pass.
Cone Crusher Working Principle
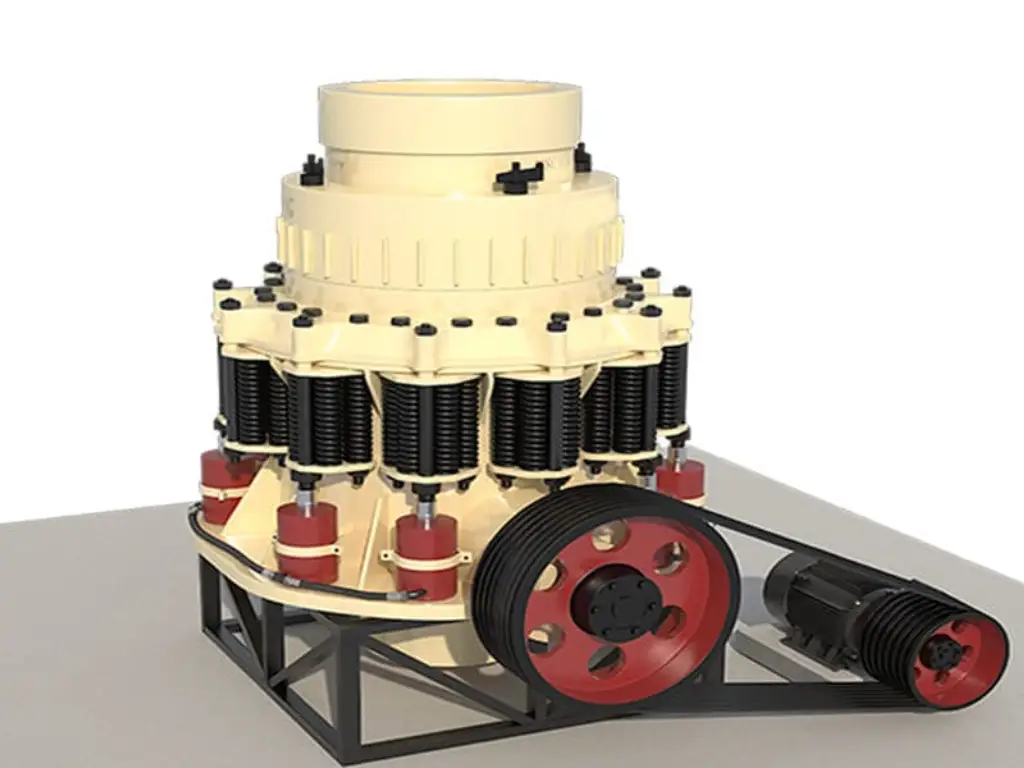
Compared to jaw crushers, cone crushers feature a more advanced crushing action. A cone-shaped mantle, concave bowl liner, eccentric assembly, and main shaft make up a cone crusher’s major components. The primary shaft, which the mantle is mounted on, is driven by an engine or motor via a hydraulic drive system or a belt.
The eccentric assembly makes the mantle wobble inside the concave bowl liner. This happens when the main shaft rotates. The wobbling motion crushes the material. It compresses and breaks down the material between the bowl liner and the mantle. Crushing occurs constantly as the material moves downward. It goes through many stages of size reduction in the crushing chamber.
The crushed product’s size depends on the closed side setting (CSS). CSS is the smallest gap between the mantle and bowl liner. It’s located at the bottom of the crushing chamber. You can change the CSS either hydraulically or mechanically. The method depends on the cone crusher model. A smaller CSS will give you a finer output. However, a bigger CSS will produce a coarser product.
Compared to jaw crushers, cone crushers have a higher reduction ratio, usually between 6:1 and 8:1 in a single pass. They also make a more cubic and evenly-shaped product because of the interparticle crushing action that happens inside the crushing chamber.
To sum up, jaw crushers use a back-and-forth compression action to crush material between a fixed and a movable jaw plate, while cone crushers use a wobbling mantle inside a concave bowl liner to continuously squeeze and break down material. These different ways of working lead to distinct output characteristics and suitable uses for each type of crusher.
Material Suitability Differences
Jaw crushers and cone crushers are built to deal with various kinds of materials, depending on how hard they are, how abrasive they are, and how big the pieces are. It’s really important to know these differences when you’re trying to pick the right crusher for your specific job.
Jaw crushers are ideal for processing a variety of materials, including hard and abrasive stones, such as:
1. Granite
2. Basalt
3. Quartzite
4. Sandstone
5. Cobblestone
6. Recycled concrete
With their powerful jaws, jaw crushers can easily break down large, chunky boulders and blocky feed sizes. Because of this, they are an excellent option for crushing various hard stones with high compressive strength. Because of the way a jaw crusher operates, it can process a wider range of materials with ease because it is less picky about particles or moisture in the input material.
Cone crushers, on the other hand, work well with medium-to-hard materials, like:
1. Limestone
2. Dolomite
3. Iron ore
4. Copper ore
5. Molybdenu
Cone crushers work better at crushing these materials because they use a combination of compression, impact, and attrition forces to produce a finer, more uniform product.
Different Crushing Stages
Jaw stone crushers and cone crushers are more often than not put to work at distinctive stages of the crushing process, since they have their claim special qualities and create distinctive output sizes. Jaw crushers are generally utilized within them to begin with arrangement, which is called essential smashing (primary crusher). They’re built to require enormous, crude materials straight from the mine or quarry and break them down into smaller, more manageable pieces that can be prepared processed for further.
Cone crushers, on the other hand, are more often used in the secondary and tertiary crushing stages. After the jaw crusher has done the primary crushing, the material gets fed into a cone crusher to be made even smaller. Sometimes, several cone crushers might be used one after the other to get the product to the desired size and shape. Cone crushers are also good for fine crushing and making a product that’s more cube-shaped, which is really important for lots of uses, like making aggregate for concrete and asphalt.
Feed Size Differences
When it comes to the size of the material you can feed into them, jaw crushers are built to handle bigger pieces than cone crushers. Most jaw crushers can take feed sizes from 150-1,000 mm (6-40 inches), and some of the really big models can even handle pieces up to 1,500 mm (60 inches). Cone crushers, however, need smaller feed sizes to work well, usually no more than about 250 mm (10 inches), though some larger models can manage feed sizes up to 350 mm (14 inches). The reason cone crushers need smaller feed sizes is because of the way they’re designed and how they crush the material. To avoid getting blocked up and to keep running efficiently, cone crushers need the material to be fed in evenly and consistently.
Product Gradation Differences
One very crucial factor to consider when choosing between a jaw crusher and a cone crusher is product gradation, or more specifically, how the crushed material is spread across various sizes. The grade and form of the finished product vary somewhat depending on the type of crusher and how it is constructed.
With more fines and longer, more elongated particles in the mix, jaw crushers often generate a broader variety of particle sizes. A jaw crusher’s typical product gradation looks somewhat like this:
* Fines (<4.75 mm or 0.19 inches): 20-30%
* Medium-sized particles (4.75-19 mm or 0.19-0.75 inches): 30-40%
* Coarse particles (>19 mm or 0.75 inches): 30-50%
The reason jaw crushers have a higher percentage of fines and elongated particles is because of how they crush the material. Jaw crushers mainly use compression and impact forces to break things down, which can lead to a product that’s not as uniform in shape and not as cube-like compared to what you’d get from a cone crusher.
On the other hand, cone crushers produce a more uniform and cubical product, with a lower percentage of fines. The typical product gradation from a cone crusher will have the following distribution:
* Fines (<4.75 mm or 0.19 inches): 10-20%
* Medium-sized particles (4.75-19 mm or 0.19-0.75 inches): 50-60%
* Coarse particles (>19 mm or 0.75 inches): 20-40%
The more uniform and cubical product shape produced by cone crushers is a result of the crushing action that involves a combination of compression, impact, and attrition forces. The interparticle crushing action within the crushing chamber also contributes to the production of a more cubical product, as the particles are continuously compressed and abraded against each other, resulting in a better grain shape.
Production Capacity Comparison
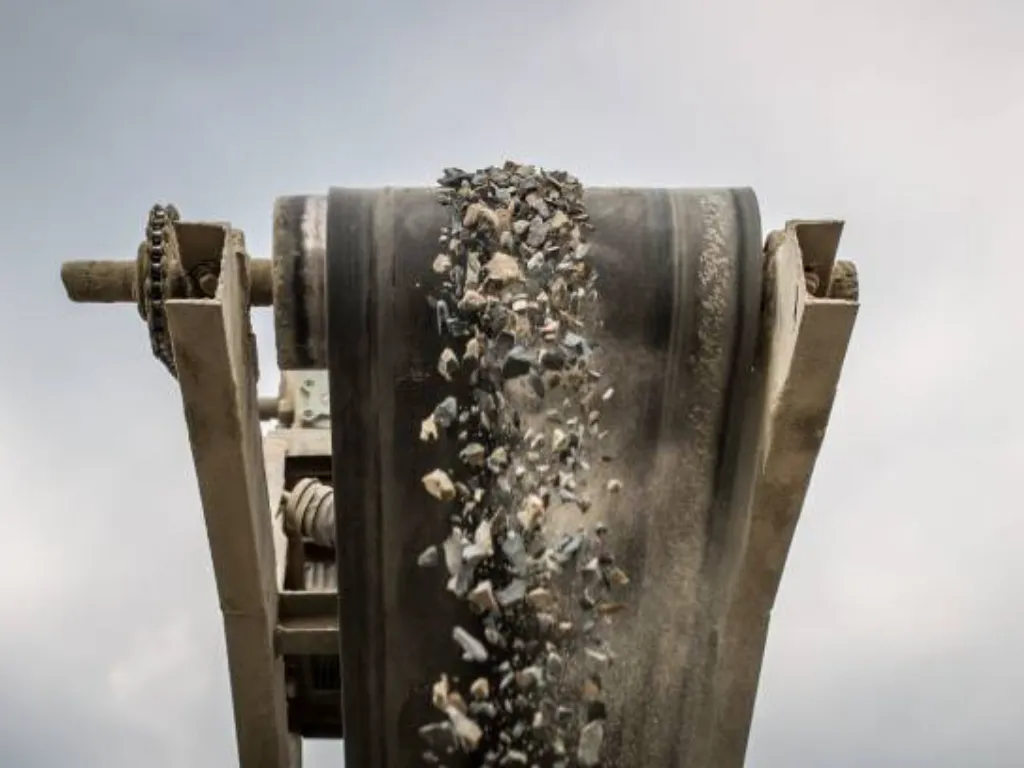
Jaw crushers usually have a higher hourly processing capacity than cone crushers when comparing equipment of similar sizes. Jaw crushers have an hourly capacity of 200–1,000 tons; medium-sized equipment typically handle 300–600 tons. Cone crushers, on the other hand, typically have an hourly capacity ranging from 100 to 750 tons, with medium-sized units averaging 200 to 500 tons. It’s crucial to remember that a crusher’s real processing capacity is dependent on a number of variables. These consist of the material type, feed size, crusher settings, and operation environment. While choosing the best crushing equipment for your operation involves many factors, production capacity shouldn’t be the only one taken into account.
Energy Consumption Differences
When you look at jaw crushers and cone crushers that are about the same size and can handle the same amount of material, jaw crushers usually need less energy to run. The main thing that uses energy in a jaw crusher is the motor or engine that powers the eccentric shaft. This shaft makes the movable jaw plate swing back and forth, crushing the material against the fixed jaw plate. Depending on the size of the crusher and how hard the material is, a jaw crusher typically uses between 1 and 2 kWh of energy for each ton of material it processes.
However, because cone crushers use compression, impact, and grinding forces to crush the material, they often consume more energy. The hydraulic system, which modifies the crusher settings, and the engine, which powers the main shaft of a cone crusher, consume the most energy. Depending on the size of the crusher, the kind of material being crushed, and the final product’s size and form, a cone crusher typically consumes 2 to 4 kWh of energy per ton of material processed.
Different Wear Parts
Jaw crushers and cone crushers have different wear parts that are subject to constant abrasion and impact forces during the stone crushing process.
Jaw crusher wear parts:
* Fixed jaw plate
* Movable jaw plate
* Cheek plates
* Toggle plate
* Toggle seats
Cone crusher wear parts:
* Mantle
* Concave
* Bowl liner
* Dust collar
* Torch ring
These wear parts are usually made from top-notch materials that can stand up to a lot of wear and tear, like high-manganese steel, chromium molybdenum alloy steel, or ceramic composites. They’re designed so that you can swap them out when needed, since they get worn down quite a bit over time from being constantly exposed to abrasive materials and the forces of the crushing process.
Initial Investment Differences
When it comes to the upfront cost, cone crushers usually have a higher price tag than jaw crushers of a similar size and capacity. This is because cone crushers have a more complex design, need to be made with more precision, and often come with extra features like hydraulic adjustment systems. However, the higher price of a cone crusher can often be justified by the fact that it can produce a finer, more consistent product, has better production efficiency, uses less energy, and delivers better product quality in the long run.
Maintenance Cost Differences
Since jaw crushers are simpler in construction, they require less maintenance; yet, over time, cone crushers can save you more money for maintenance. This is because a cone crusher’s wear-resistant components endure longer before breaking down and its handy maintenance features make maintenance easier. Therefore, even though a cone crusher may initially cost more, it can save you a great deal of time, energy, and resources because it breaks down less frequently, wear components don’t need to be changed as often, and maintenance is simpler when the crusher is operating.
Noise and Dust Level Differences
Jaw crushers are usually louder than cone crushers because of the back-and-forth motion of the movable jaw and the way the material slams against the crushing plates. Cone crushers, on the other hand, tend to be a bit quieter since the crushing action is more of a continuous, gradual process with less impact and not as much vibration.
When it comes to how much dust they make, jaw crushers can kick up more dust during the primary crushing stage because they’re dealing with bigger pieces of material and using more force to crush them. Cone crushers, which are used later on in the process, might generate finer dust particles since they’re working with material that’s already been through the first round of crushing.
Application Differences
Jaw Crusher Applications:
- Primary crushing in mining operations
- Quarrying of granite, basalt, limestone, and sandstone
- Recycling of concrete and construction debris
- Processing of materials with high clay content or moisture levels
- Crushing hard, abrasive materials like cobblestone and river gravel
Cone Crusher Applications:
- Secondary crushing and tertiary crushing stages in mining operations
- Aggregate production for concrete and asphalt
- Processing of medium to hard materials like limestone, dolomite, and iron ore
- Fine crushing of minerals such as copper ore, gold ore, and molybdenum ore
- Production of a uniform and cubical product shape for various industries
Multi-Stage Crushing Circuit Applications:
- Mining operations with large feed sizes and high production requirements
- Quarrying operations that require a specific product size and shape
- Aggregate production plants for construction materials
- Mineral processing facilities for the production of concentrates
- Recycling plants for the production of high-quality recycled aggregates
Jaw Crusher VS Cone Crusher: Factors to Consider in Selection
When selecting between a jaw crusher and a cone crusher, several key factors should be considered to ensure the best fit for your application. The following table provides a comparison of these factors and recommendations for each crusher type:
Factor | Jaw Crusher | Cone Crusher | Recommendation |
---|---|---|---|
Material properties | Ideal for hard, abrasive materials | Better suited for medium to hard materials | Consider material hardness, abrasiveness, and size |
Feed size | Can handle larger feed sizes (up to 1,500 mm) | Requires smaller, more consistent feed size (up to 350 mm) | Choose based on the feed size of your material |
Product requirements | Produces a wider range of particle sizes and shapes | Produces a more uniform and cubical product | Evaluate desired product size, shape, and gradation |
Production capacity | Generally higher capacity (200-1,000 tons/hour) | Typically lower capacity (100-750 tons/hour) | Assess throughput requirements and match with crusher size |
Crushing stages | Primarily used in primary crushing stages | Used in secondary and tertiary crushing stages | Determine the required crushing stages for your application |
Energy consumption | Lower energy consumption (1-2 kWh/ton) | Higher energy consumption (2-4 kWh/ton) | Consider energy efficiency and its impact on operating costs |
Maintenance and wear parts | Simpler design with fewer wear parts | More complex design with a greater number of wear parts | Evaluate maintenance requirements and costs for each type |
Initial investment and operating costs | Lower initial investment cost | Higher initial investment cost | Compare upfront costs and long-term operating expenses |
Environmental factors | Produces more noise and dust in primary crushing | Generates finer dust particles in secondary/tertiary crushing | Consider noise and dust generation, and environmental regulations |
How to Select Stone Crusher for You?
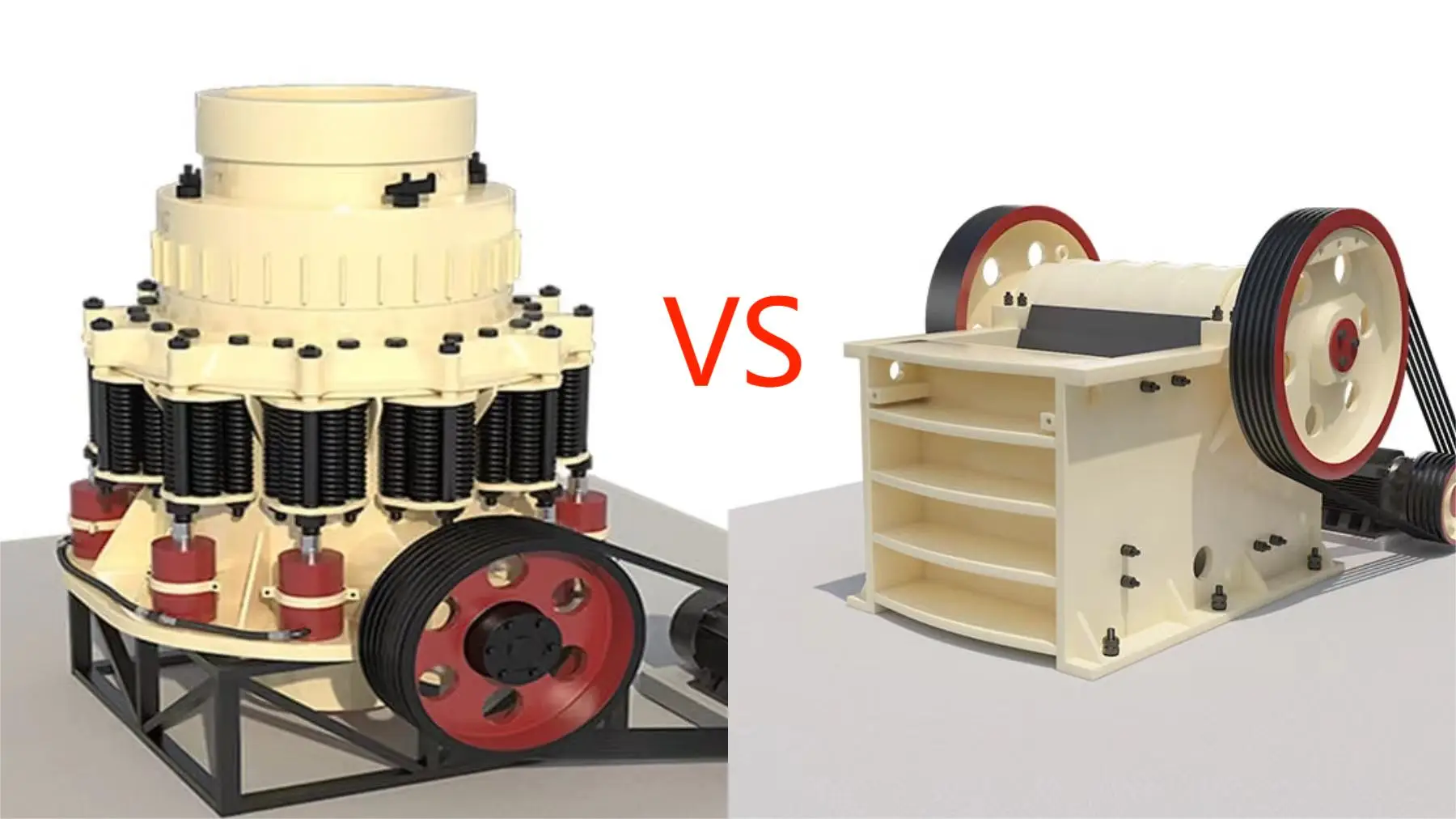
When you’re attempting to choose out a jaw crusher or cone crusher, there are a bunch of different things you would like to think approximately. Typically to form beyond any doubt you get the finest execution, effectiveness, and esteem for your cash. Take a see at what the material is like and how big the feed size is. Additionally, consider what measure you want the yield to be and how much throughput you wish. The sum of space you’ve available is another huge calculate. You ought to too think around how durable the crusher is and what kind of maintenance it’ll require. Energy efficiency is truly imperative for keeping costs down. You’ll have to be carefully see at the forthright fetched and the working costs. It’s a great thought to conversation to a few experienced experts for counsel. They can assist you select the crusher that’s the leading fit for your particular circumstance. This will guarantee simply get dependable, effective, and temperate execution. Making the proper choice is key to having an effective crushing operation.
JXSC-Your Mining Processing Equipment Manufacturer
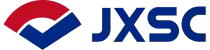
JXSC could be a well-known and regarded title within the mining world, and they offer a wide extend of intense, effective mineral preparing hardware. This includes impact crushers, gyratory crushers, hammer crushers, roller crushers, horizontal shaft impact crushers, vertical shaft impactors, and mobile plants. All of their gear is planned to grant you a tall pulverizing proportion whereas keeping vitality utilization moo, much obliged to highlights like optimized feeding opening sizes, narrow openings, and fixed walls. The group at JXSC works closely with each client to come up with customized arrangements that take into consideration the particular properties of the minerals being handled and the required yield. With a enormous 30,000 ㎡ factory and encounter working with over 40 diverse sorts of mineral minerals, JXSC has the information and capabilities to handle almost about any challenge. They too utilize progressed advances like spinning rotors and horizontal shaft impactors to stay at the bleeding edge of the industry. At the conclusion of the day, JXSC is all around giving tried-and-true mineral innovation and equipment that can assist you overcome any impediment and turn crude minerals into productive items.
Conclusion
At the conclusion of the day, choosing whether to go with a jaw crusher or a cone crusher comes down to your particular circumstance and what you wish the crusher to do. By taking the time to truly understand what each sort of crusher is sweet at and where they drop short, and after that coordinating those characteristics to your specific prerequisites, you’ll get the foremost out of your pulverizing operation in terms of productivity and profitability. This way, you will be able to deliver high-quality items that meet your customers’ needs, whereas keeping your operation running easily and effectively.