- Home
- Blog
- Mineral Solution
- Iron Ore Mining: The Essential Process for Steel Production
What Is Iron Ore?
Iron ore is a metal bearing mineral substance which is capable of yielding metallic iron (Fe) when it is heated with reductant. It is the main material used as an input to produce steel, and 98% of iron ore is used for this purpose. The magnetite (Fe3O4), hematite (Fe2O3), goethite, limonite, or siderite are the iron ores that are usually found, and the most commonly mined is hematite and copper. Iron meteorites, generally, contain nickel and they are believed to have resulted from accreted bodies of 1,000 km (621 mi) in diameter or larger. In recent years, global mtpa of iron ore has grown steadily to meet growing steel demand, with the Brazilian mining corporation Vale being the world’s largest producer. According to the United States Geological Survey (USGS), global iron ore production in 2021 will be approximately 2.3 billion tons, with Vale leading the way.
Iron ore is obtained through either open pit or underground mining and then proceeds to processing, which involves crushing, screening, and beneficiation in order to raise its iron content level. The ore is mixed and blended to a homogeneous degree and then transported for export.
Where to Find Iron Ore?
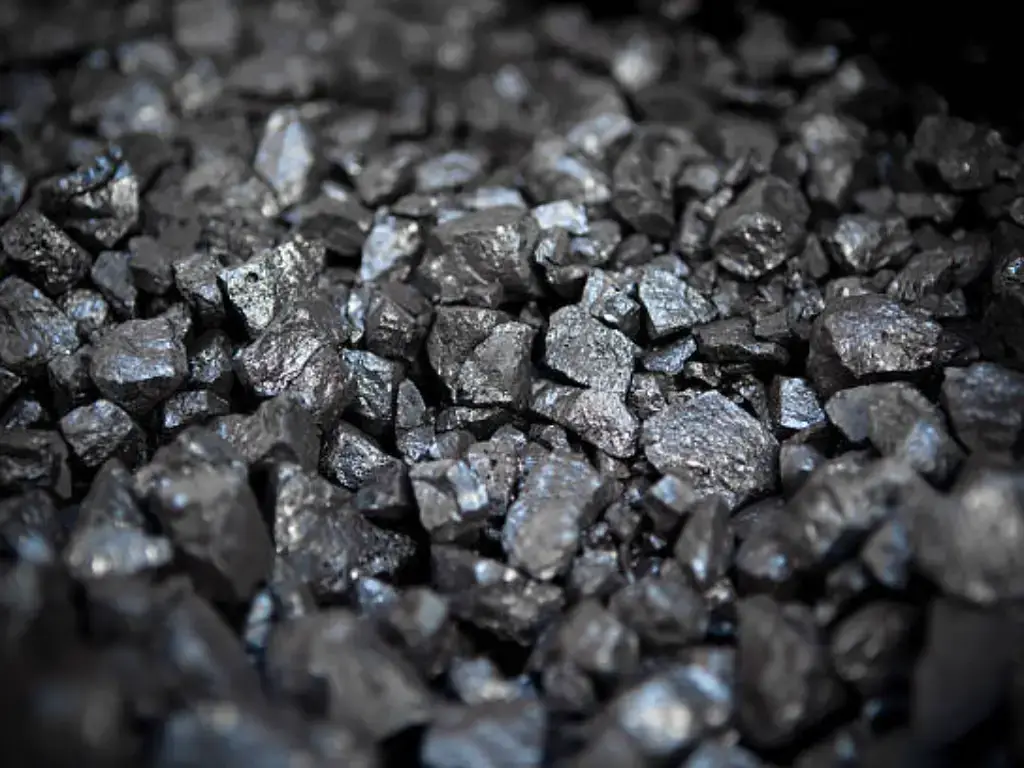
Iron ore deposits are found in various regions worldwide, with the largest producers being Australia, Brazil, China, and India. Significant iron ore mines are also located in the United States, Canada, Russia, and South Africa. In the United States, the majority of iron ore mining takes place in the Mesabi Range, located in Minnesota and Michigan near the Great Lakes.
Australia is the world’s largest iron ore producer, with Western Australia accounting for over 90% of the country’s production. The Pilbara region in Western Australia is home to some of the largest iron ore mines in the world, operated by major companies such as Rio Tinto, BHP, and Fortescue Metals Group. Brazil, the second-largest producer, has its major iron ore mines located in the Carajás region in the state of Pará.
Types of Iron Ore
Hematite, magnetite, and limonite are the three basic types of iron ore, each with unique properties and their own role in the steel making processes.
Hematite
Hematite is the most common and widely mined iron ore due to its high iron content (60-70%) which makes it easy to process. Reddish-black this ore is found in sedimentary rocks and has relatively soft texture, which facilitates their grinding and crushing. Hematite is the most preferred ore for steel production because, when reduced into metallic iron, it requires less energy as compared to other ores. The high iron content and lower impurities in hematite certainly contribute to smoother and better blast furnace operations, and, as a result, better-quality steel products.
Magnetite
Magnetite, although less common than hematite, contains the highest iron percentage with up to 72% of iron. This black, magnetic mineral is formed in the metamorphic and igneous rocks; as a result it is difficult to mine and process. Nevertheless, the magnetic properties of magnetite are more suitable for the separation from gangue minerals, which is facilitated by magnetic separation methods. The magnetite is richer in iron than the other minerals. Therefore, it gives a higher-grade concentrate that is significant in steel production. The higher density of magnetite makes it good for use in heavy media separation, one of the methods used to improve lower-grade iron ores.
Limonite
Limonite, which is also called “bog iron ore,” is a low-grade ore with a yellowish-brown color due to its impurities. It is the byproducts of weathering of other iron-rich minerals and it contains about 20-30% of iron. Nevertheless, limonite has a lower economic value compared to hematite and magnetite because of its lesser iron content combined with the presence of impurities like silica and alumina; however, it has been used in steel production for a long time. The limonite is being upgraded through the beneficiation techniques like washing, jigging and the sintering process before being used as a raw material in blast furnaces. In fact, limonite can be used as a secondary ore to be mixed with the main ores to achieve the required iron content and impurities levels.
The selection of iron ore for steel production relies on various aspects, which include iron content, impurity levels, processing requirements, and the cost-effectiveness. Hematite is the most widely used form as it is fairly common, contains high iron content, and is not difficult to process. Magnetite may be harder in nature, but it is more and more utilized as a raw material in steel production to produce higher-grade concentrates owing to higher iron content. Limonite might not be the most desirable ore, but it can be used in steel production when economically feasible or to provide a blending ore for furnaces to improve performance and product quality.
The Iron Ore Mining Process
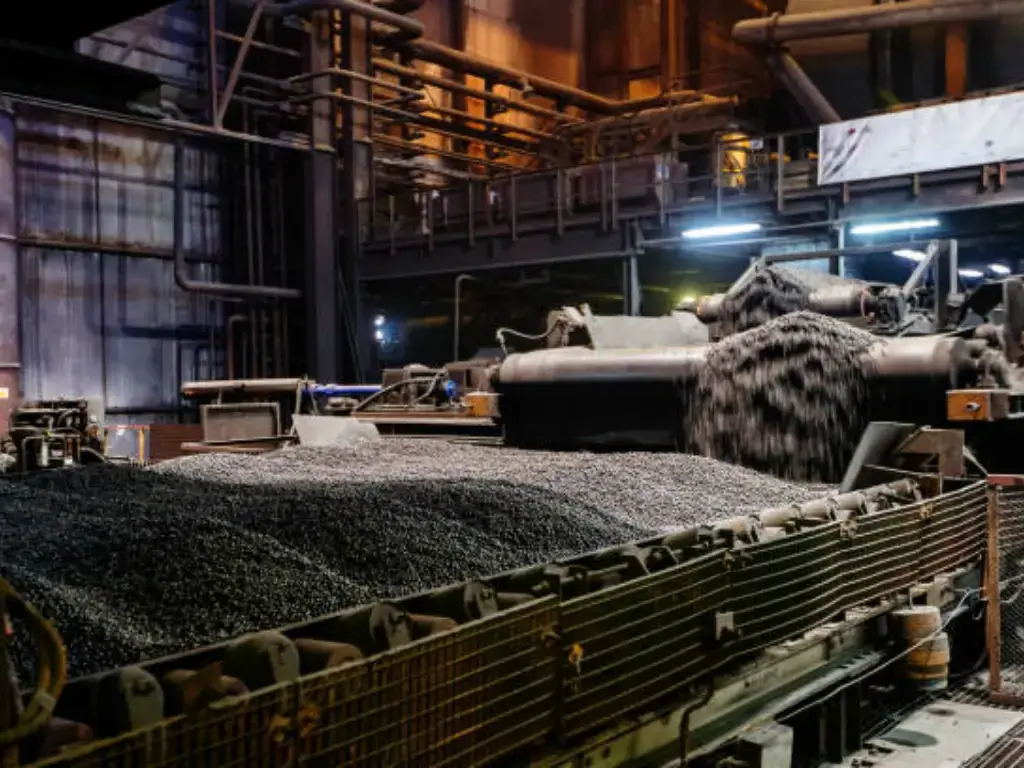
Step 1:Exploration and Site Selection - Finding Good Deposits
The mining of iron ore starts with the process of exploration and site selection. Geologists and mining engineers apply different techniques to identify the probable locations of iron ore deposits, such as geophysical surveys, aerial surveys, and exploratory drilling. The initial survey proves a site to be prospective, with potential deposits in areas such as the Great Lakes region. The next stage is a detailed survey and sampling which is done to determine the volume and quality of the iron ore deposit.
Step 2:Drilling and Blasting: Ore mining from the Earth
Once the deposit of iron ore is feasible, the mining process is moved to digging the ore out from the earth. The most widely used technique is open-pit mining, which involves drilling and blasting the surface rock and soil to get to the ore deposit beneath it in states like Minnesota and Michigan, around the area of Lake Superior. After getting the overburden removed, the iron ore is drilled and blasted to make it smaller pieces that can be easily transported from the mines.
Step 3: Transport - Shipping the Ore to the Processing Plant
Then, the ore is detached by the blasting and the giant vehicles or conveyor belts bring it out of the mine. The ore is carried away to the processing plant. It can be close to or in a distant place. The ore travels by truck, train or ship, the choice of the mode of transportation being decided by the distance and the location. The ore needs to be brought to the plant in an efficient way to enable the iron ore mining process to be carried out effectively.
Step 4: Crushing and Grinding – Ore Preparation for Separation
At the plant, machines called crushers smash the ore into smaller pieces. The first crushers are jaw crushers that break up the biggest chunks. Then cone crushers break it down more. Finally, the ore pieces go into ball mills or rod mills. These are big spinning drums with steel balls or rods inside. As they turn, they grind the ore into a fine powder. This step increases the surface area, so the iron can be separated out more easily in the next step.
Step 5: Magnetic Separation - Pulling Out the Iron
The strong magnets will attract the fine iron ore powder. Iron particles are drawn to and taken by the magnets. This magnetic separation technique is effective for high-quality ores, such as magnetite. A magnet is used to attract magnetic iron particles and the waste rock is discarded. Through this process, we get concentrated iron ore powder. Enhance your iron extraction process with our advanced magnetic separator technology, detailed here.
Step 6: Pelletizing- The process of producing Iron Ore Pellets
The concentrated iron ore is then mixed with binding agents, such as bentonite clay, and formed into small, marble-sized pellets using a pelletizing disk or drum. The pellets are then hardened by firing in a furnace at high temperatures (1,200-1,300°C). Pelletizing the iron ore allows for more efficient transportation and handling, as well as improved performance in the blast furnace during the steel-making process.
Iron Mining Equipment
Equipment | Features | Applications | Benefits |
---|---|---|---|
Drilling Rigs | 1.Rotary or percussion drilling- Drill depths up to 60 meters 2.Hydraulic or electric power 3.Automated or manual operation | 1. Creating blast holes in overburden and iron ore 2.Suitable for surface and underground mines 3.Used in exploration and production drilling | 1.Efficient and precise drilling 2.Versatile for different mine conditions 3.High productivity and reduced operating costs |
Explosives | 1.- ANFO (Ammonium Nitrate Fuel Oil) 2.Emulsion explosives 3.Electronic or non-electric detonators 4.Controlled blasting techniques | 1. Breaking up overburden and iron ore 2.Applicable in open-pit and underground mines 3.Fragmentation of rock for easier excavation | 1.Optimized blasting for improved fragmentation 2.Enhanced safety with controlled detonation 3.Cost-effective and reliable blasting solutions |
Haul Trucks | 1.Rigid frame or articulated trucks 2.Payload capacity from 40 to 400 tons 3.Diesel or electric-drive options 4.Autonomous or manned operation | 1.Transporting iron ore from mine to processing plant 2.Suitable for open-pit and large-scale mines .3.Continuous hauling operations | 1. High payload capacity for efficient transportation 2.Rugged design for tough mining conditions 3.Advanced safety features and operator comfort |
Crushers | 1.Jaw, cone, gyratory, or impact crushers 2.Primary and secondary crushing stages 3.High capacity and reduction ratios 4.Wear-resistant materials | 1.Reducing iron ore size for further processing 2.Applicable for various iron ore types and hardness 3.Integration with grinding circuits | 1.Efficient size reduction for optimized processing 2.Durable components for long service life 3.Customizable designs for specific ore properties |
Grinding Mills | 1. Ball, rod, or autogenous mills 2.Wet or dry grinding processes <br.3.High-efficiency classifiers 4.Automatic control systems | 1.Grinding iron ore into fine particles 2. Suitable for hematite, magnetite, and other ores 3.Preparation for magnetic separation or pelletizing | 1.Consistent and uniform particle size distribution 2.High throughput and energy efficiency 3.Reduced maintenance and wear costs |
Magnetic Separators | 1.Low or high-intensity magnetic separators 2.Dry or wet separation processes 3.Permanent or electromagnetic designs 4.Multiple stages for improved recovery | 1.Separating magnetic iron ore particles from gangue 2.Applicable for magnetite and hematite ores 3.Concentration and purification of iron ore | 1.High recovery rates and concentrate grades 2.Efficient removal of impurities 3.Adaptable to various ore characteristics and plant layouts |
Pelletizing Machines | 1.Disc or drum pelletizers 2.Balling and induration processes 3.Binder addition systems 4. Process control and automation | 1.Agglomerating iron ore fines into pellets 2.Suitable for concentrate from magnetic separation 3.Preparation for blast furnace or direct reduction | 1.Consistent pellet size and quality 2.Improved transportation and handling properties 3.Enhanced blast furnace performance and efficiency |
Processing Iron Ore for Steel Production
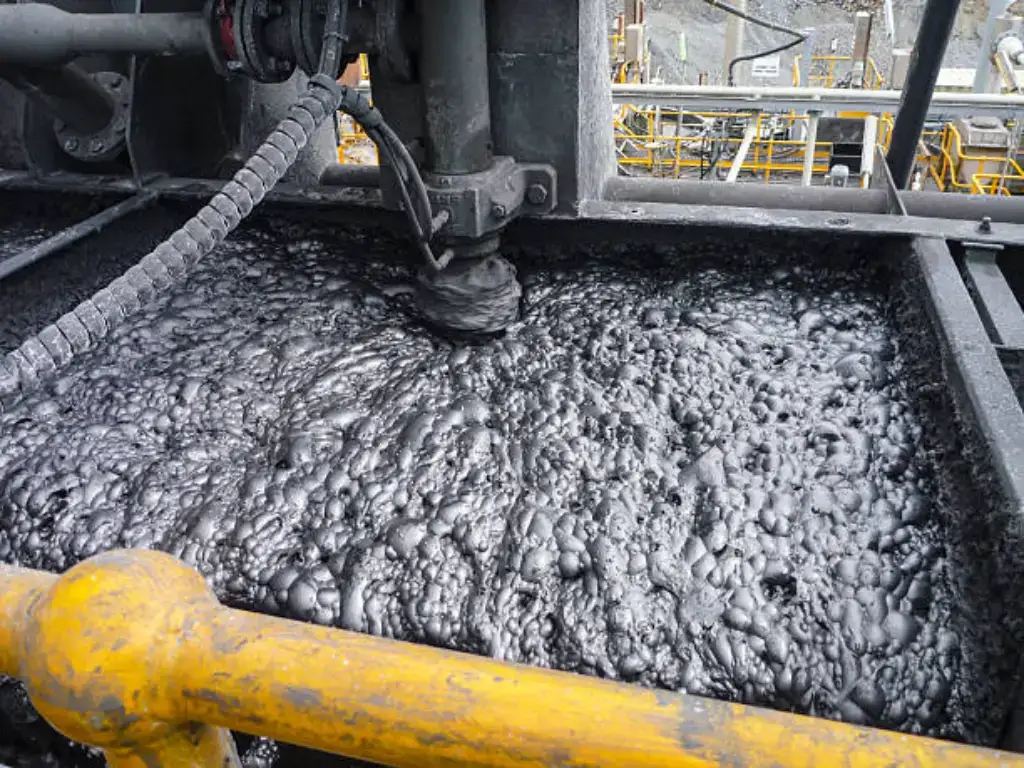
The underlying data shows that the major use of mined iron ore is its processing to make steel. Key commodities raw material for steel plants is iron ore mine, so tons of iron ore are used in many countries’ factories like China,Canada. The first step in the process is the production of pig iron from which the iron ore is converted in the blast furnace and usually occurs in the form of iron oxides. The heated air is blown into the furnace at the bottom which assist in the coking to be burnt and to produce high temperatures (about 1,500°C). Steel production is entirely dependent on natural resources. For instance, iron ore, coal and limestone, which are used to make steel that is employed in various sectors.
It is a blend of the iron ore, coke, and limestone in the blast furnace that undergoes the change and is reduced to form the liquid state, sinking to the bottom of the furnace as pig iron. The limestone works as a flux , it purifies the pig iron from the impurities. The pig iron melt is tapped from the bottom of the blast furnace and either cast into ingots or is transferred in the molten state to the basic oxygen furnace for further processing into the steel.
In a basic oxygen furnace, the pig iron is combined with scrap steel and the other additives such as manganese, silicon, and aluminum in the proper proportions to obtain the desired properties of the steel product. An oxygen stream that is of high purity is blown into the furnace. Through oxidation, the impurities in the pig iron are converted into slag, which is then separated from molten steel. The steel is then drawn out of the furnace, now in its refined state, and can be cast into a number of shapes like slabs, blooms, or billets, which are the end products.
Conclusion
Iron ore mining has been identified as a crucial process that supplies the raw materials needed for steel making, which is an essential element for the modern world’s infrastructure and technology. There are a number of steps in the iron ore mining process, starting with finding deposits that are suitable for mining all the way to processing the ore to a form that can be used in a blast furnace and which requires specialized equipment and knowledge.
With the worldwide steel demand still on the rise, the significance of iron ore mining will continue to become more apparent. The development of mining technology and sustainable methods will be pivotal in creating a steady and conscientious supply of iron ore to be able to cover the world’s demands. By becoming aware of the iron ore mining process and its importance, we will be able to take into consideration the important role this fundamental product has in shaping the world.