- Home
- Blog
- Equipment Info
- Impact Crusher vs Jaw Crusher: What’s the Difference?
Basic Steps in the Crushing Process
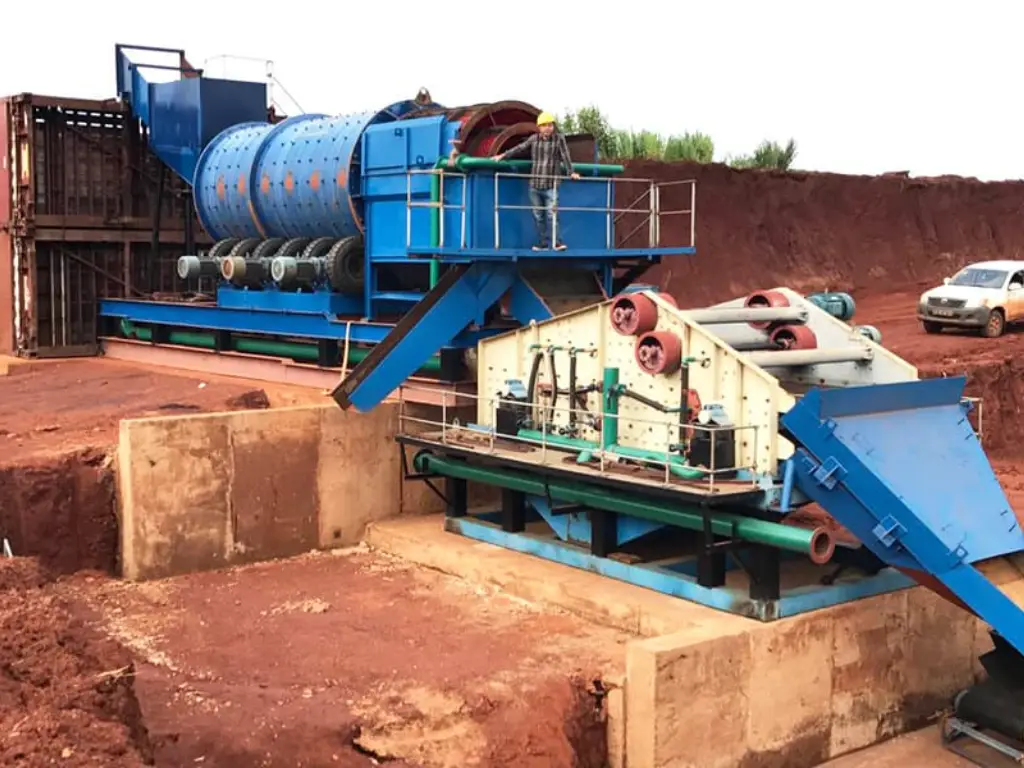
Selection and Preparation of Raw Material
Primary Crushing
Secondary Crushing
Tertiary Crushing and Finishing Processes
After tertiary crushing, the material often goes through additional processes such as screening (to sort the material by size), washing (to remove unwanted particles or chemicals), and sometimes even further reduction stages, depending on the specific requirements of the final product.
From Boulders to Sand: The Overall Picture
- Jaw Crushers for primary reduction (from boulders up to 4-6 feet to 6-8 inches),
- Cone Crushers or Horizontal Shaft Impactors for secondary crushing (further reducing material to 0.5-3 inches),
- Vertical Shaft Impactors for tertiary crushing (creating sand-sized particles of 1/4 to 3/8 inch).
Types and Roles of Crushing Machines
Crusher Type | Crushing Stage | Processed Mineral Types | Input Material Size | Output Material Size | Other Key Features |
---|---|---|---|---|---|
Jaw Crusher | Primary | Gold, Copper, Limestone | Up to 1200mm (48 inches) | 150mm-300mm (6-12 inches) | High durability, suitable for hard materials |
Impact Crusher | Secondary | Limestone, Asphalt, Gravel | Not exceeding 800mm (31 inches) | Var. down to 25mm (1 inch) | High reduction ratio, good for soft to medium-hard materials |
Cone Crusher | Secondary/Tertiary | Gold, Copper, Silver | Up to 300mm (12 inches) | 20mm-50mm (0.75-2 inches) | Precise control over output size, suitable for medium-hard materials |
Vertical Shaft Impactors (VSI) | Tertiary/Quaternary | Sand, Gravel | Up to 50mm (2 inches) | 1mm-5mm (0.04-0.2 inches) | Produces fine particles, good for producing sand-like textures |
Gyratory Crusher | Primary/Secondary | Iron, Gold, Copper | Up to 2000mm (79 inches) | 100mm-200mm (4-8 inches) | Handles large volumes, high throughput |
Roll Crushers | Secondary/Tertiary | Coal, Limestone, Potash | Not exceeding 80mm (3 inches) | 2mm-10mm (0.08-0.4 inches) | Low fine production, suitable for friable materials |
Hammer Crusher | Secondary, Tertiary | Limestone, Gypsum, Coal | Up to 600mm (24 inches) | 15mm-50mm (0.6-2 inches) | High reduction ratio, suitable for brittle materials |
What is an Impact Crusher?
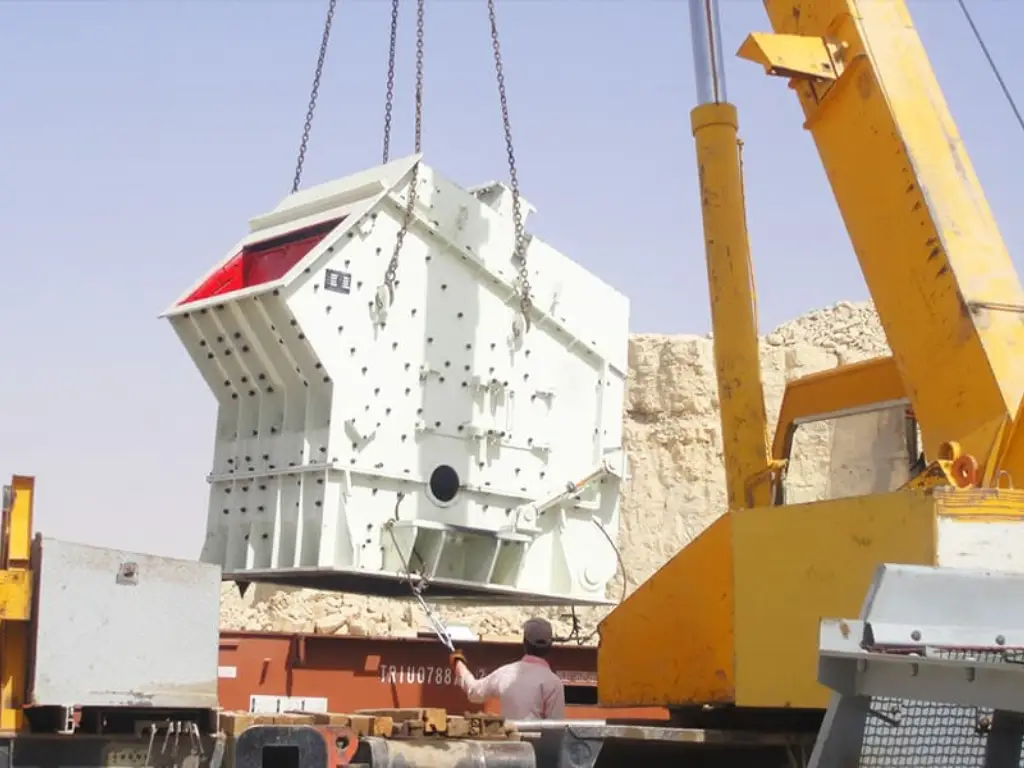
Design Principle and Operating Method
- Rotor: Consider the rotor the core of the impact crusher-it's where the hammers reside. This component is designed to withstand various loads and speeds, ensuring a smooth operation throughout.
- Hammers/Blow Bars: Attached to the rotor, these elements are made from incredibly strong high manganese steel or similarly durable alloys. Their primary role? To hit the incoming pieces and fragment them.
- Impact Plates/Anvils: Positioned within the crushing area, these provide a sturdy platform against which the material is shattered.
- Feed Inlet: This is where the material starts its journey. The design of the feed inlet is vital for regulating how much material enters the crusher and preventing any jams.
- Discharge Opening: This feature controls the size of the output material from the crusher, and can be adjusted to meet the needs of different projects.
- Horizontal Shaft Impactors (HSI): Ideal for softer to medium-hard materials, HSIs offer excellent control over particle shape. They are frequently used for limestone or materials with lower abrasiveness.
- Vertical Shaft Impactors (VSI): Best suited for harder materials like granite and basalt, VSIs focus on producing high-quality sand and aggregates with a cubic shape. They operate by throwing material against stationary anvils using centrifugal force.
Key Features of Impact Crushers
- High Reduction Ratios: Take a typical HSI, for example, it can knock down the size of stuff we're working with by a whopping 20 times. And get this - some VSIs go even further, shrinking things down by up to 50 times depending on what you're breaking up. Imagine taking something as big as 500mm across and squishing it down to just 25mm in one go.
- Production Capacity: When it comes to getting a lot done fast, modern impact crushers are real powerhouses. Let’s say you’ve got a mid-sized HSI that’s about 1 meter wide at its mouth - it can crunch through more than 500 tons of limestone or stuff like that in just one hour.
- Versatility and Product Quality: One significant advantage is the ability to produce uniform, cubical-shaped particles, which is paramount for the concrete and asphalt industry. The cubic shape ensures higher compressive strength and durability for the final product.
- Energy Efficiency: Impact crushers are also known for their energy efficiency. The method of using kinetic energy from the high-speed rotor to break down materials minimizes power consumption while maximizing output.
What is a Jaw Crusher?
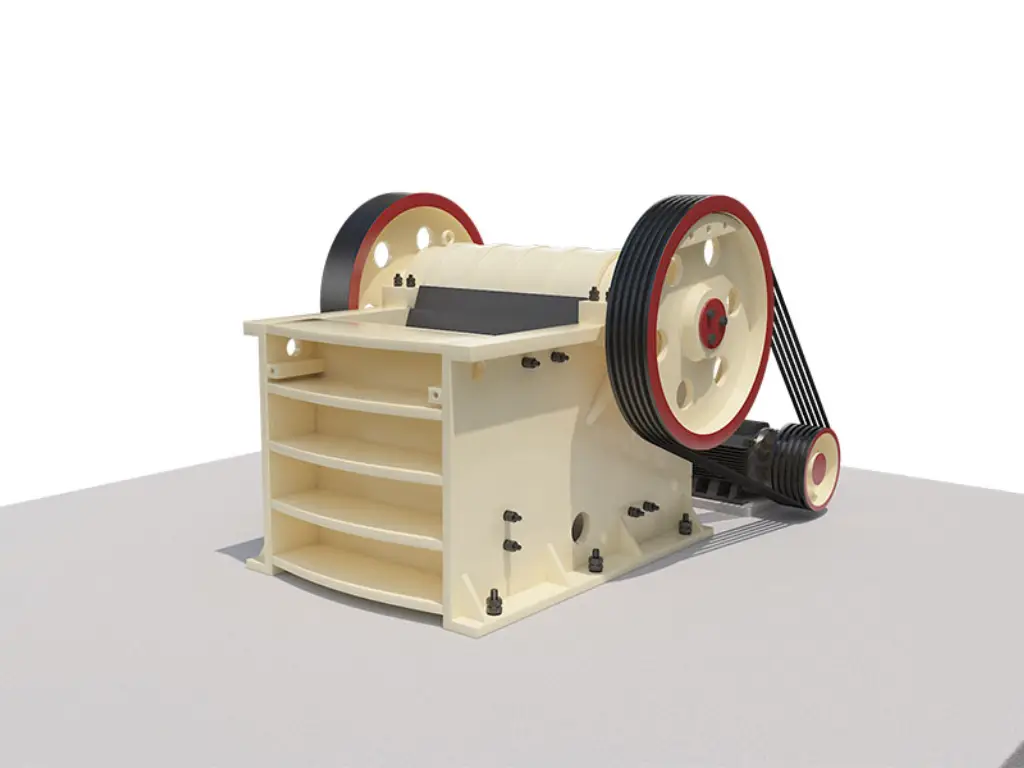
Design Principle and Operating Method
Key Features of Jaw Crushers
- High Crushing Capacity and Size Reduction: One of the standout features of jaw crushers is their strong ability to handle incredibly large feed sizes. Some models can even process giant boulders up to one cubic meter in size. They also have a high reduction ratio of up to 8:1, meaning they can significantly reduce material size in just one go.
- Flexibility in Output Size: The closed side setting (CSS) of a jaw crusher, which is key to determining the size of the end product, can be adjusted. This flexibility lets you change the output size to meet various crushing needs, from breaking down big rocks to creating finely crushed stone. This makes jaw crushers incredibly versatile for various tasks.
- High Processing Ability: High-capacity jaw crushers can crush up to 5000 tons of material per hour, making them perfect for large-scale mining and quarrying jobs. For example, in a large-scale copper mine, a jaw crusher plays a crucial role in breaking down huge chunks of ore before they're further processed in grinding mills.
- Built to Last: Jaw crushers are made to withstand harsh working environments, thanks to their heavy-duty construction and high-quality materials. Their strong design includes a hefty frame and a large flywheel, boosting their efficiency.
- Wide Range of Applications: Jaw crushers are not just for mining and making aggregates; they're also great for recycling. For instance, they can turn old concrete from demolition sites into usable gravel. This shows how adaptable they are.
- Energy-Saving Design: Despite their size, modern jaw crushers are designed to be energy-efficient. Many models come with tech improvements that lower energy use, cutting down on running costs. This focus on better energy management helps reduce the costs of operations.
Comparison Table of the Two Crusher Types
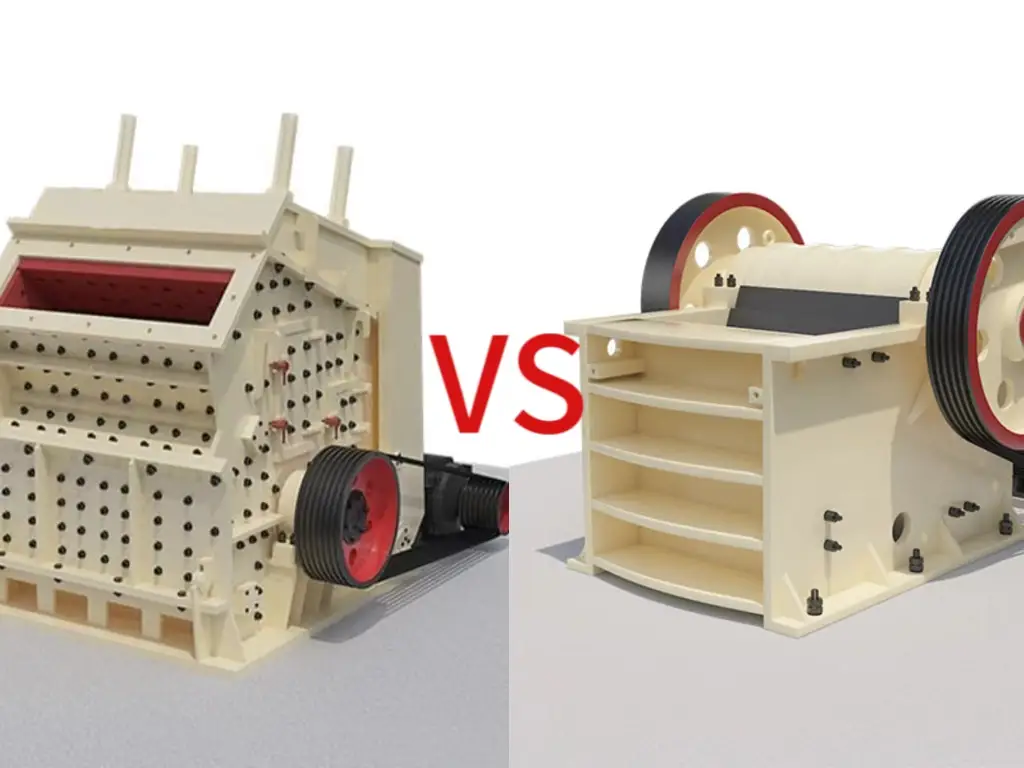
Feature | Impact Crusher | Jaw Crusher |
---|---|---|
Principle | High-speed impact | Compression |
Material Type | More suited for medium to soft | Best for hard materials |
Final Product | Cubical and uniform | Varied sizes tend to be larger pieces |
Reduction Ratio | High | Moderate to high |
Maintenance | Less frequent but higher skill required | More frequent but simpler |
Application | Secondary/tertiary crushing, recycling | Primary crushing, mining, aggregate |
Suitability and Advantages of Jaw Crushers
Most Suitable Types of Rocks/Minerals
Granite stands out for its hardness and abrasiveness, qualities that demand a powerful and durable crusher. Jaw crushers are up to the task, capable of breaking down large chunks of granite into manageable sizes for further processing or direct use in construction.
● Basalt
Like granite, basalt is known for its hardness and durability. It is another common material for jaw crushers to process, often used in road and railway construction after being crushed due to its excellent performance in creating strong, dense aggregates.
● Limestone
Though limestone is comparatively softer than granite and basalt, it is a popular choice for cement production and various construction purposes. Jaw crushers easily handle limestone, breaking it down into sizes suitable for the market.
● Iron Ore
At the beginning of extracting iron ore, big chunks of the ore are first broken down by using jaw crushers. This crucial step significantly makes the iron ore smaller, making the next steps easier, which involve grinding and cleaning it up. These parts of the process are vital for getting the iron ore ready for the market, making sure it meets the right standards for both quality and cleanliness.
● Copper Ore
Crushing Fineness and Capacity
Suitability and Advantages of Impact Crushers
Most Suitable Types of Rocks/Minerals
Impact crushers are champs when it comes to softer rocks and minerals. They have a knack for smashing limestone, gypsum, calcite, and a bunch of others into tinier bits very effectively. But that’s not all they’re good at. Here’s the scoop on some of the best materials they deal with:
● Limestone and Gypsum
These are a dream team for impact crushers because they break easily. This means the crusher can make pieces that are all about the same size, which is awesome if you need to do more with the material later on.
● Calcite and Dolomite
Since these minerals are on the softer side, the gentle whack from the impact crusher works wonders. You end up with finely crushed stuff without beating up the machine too much.
● Asphalt and Concrete Recycling
Got old roads or buildings that need new life? Impact crushers are perfect for this job. Their powerful smacks break down these tough materials into smaller bits that you can use again, which is super efficient.
● Making Stuff for Roads
One cool thing about impact crushers is that they make everything pretty uniform, which is exactly what you want when you’re building roads.
Crushing Fineness and Capacity
Key Factors in Crusher Selection
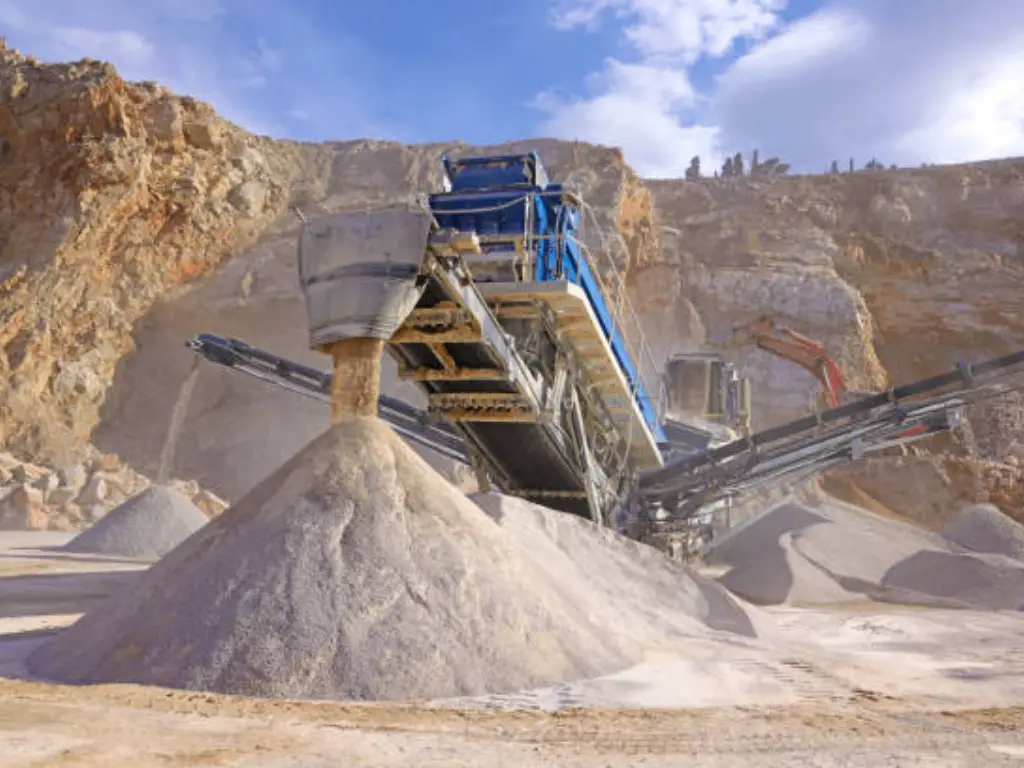
Choosing the right crusher, whether it’s an impact crusher or a jaw crusher, is crucial for your project. Knowing what to consider can not only help you save money but also guarantee that your project goes off without a hitch. Let’s explore the key points that should guide your decision:
1. Material Characteristics
2. Desired Product Size
3. Production Capacity
4. Operation Costs and Efficiency
5. Project Goals and End Use
6. Installation Space and Mobility
Operation and Maintenance
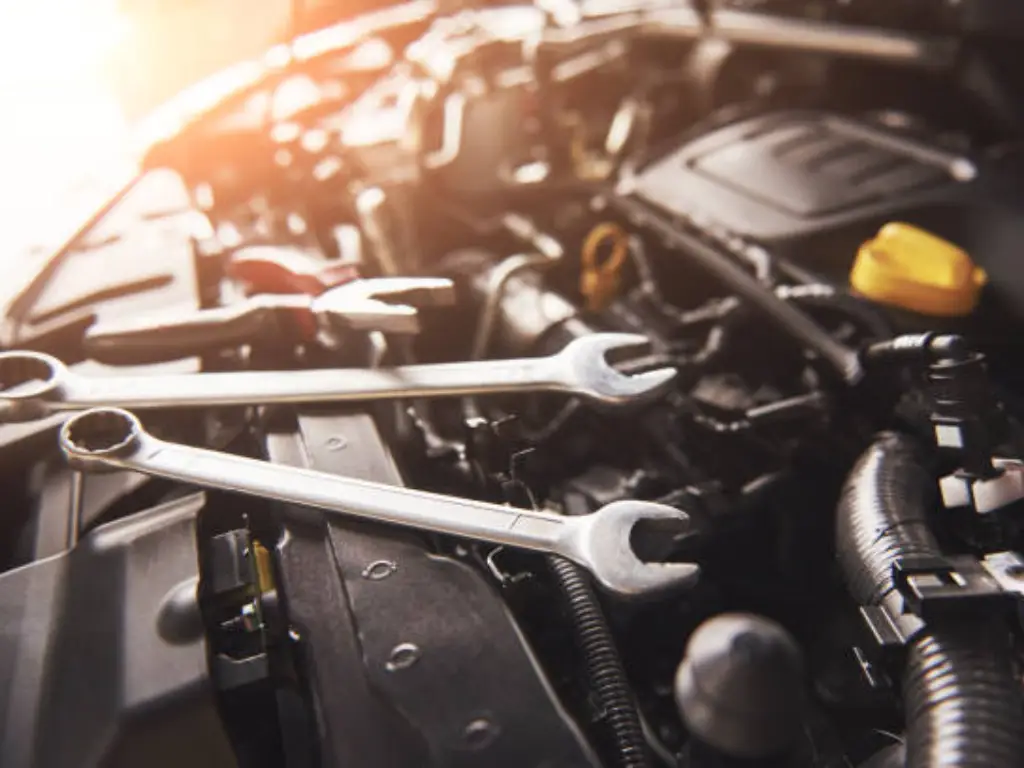
On the flip side, jaw crushers need you to check in more often, but it’s a bit simpler to keep them happy. You’ve got to watch how the crushing plates are holding up and keep everything greased up right. Also, tweaking the settings now and then is crucial to make sure you’re crushing rocks (or whatever you’ve got) to the size you need.
Sticking to these pointers not only makes your crushers last longer and work better, but also keeps your whole operation humming along smoothly.