- Home
- Blog
- Mineral Solution
- Comprehensive Overview of Gravity Separation Method for Gold Mining
- mmldigi
Preface
The extraction of gold has gone through a number of changes over the years, and different techniques have been invented to enhance the extraction and recovery of gold. Of all these methods, the gravity separation method is preferred because of its simplicity, cheap and eco-friendly. This method relies on the fact that gold is denser than most of the other materials, which makes it suitable for mineral separation. In this paper, the reader will be introduced to the gravity separation method, including its fundamentals, uses, and the various equipment employed in the process.
What is Gravity Separation Method?
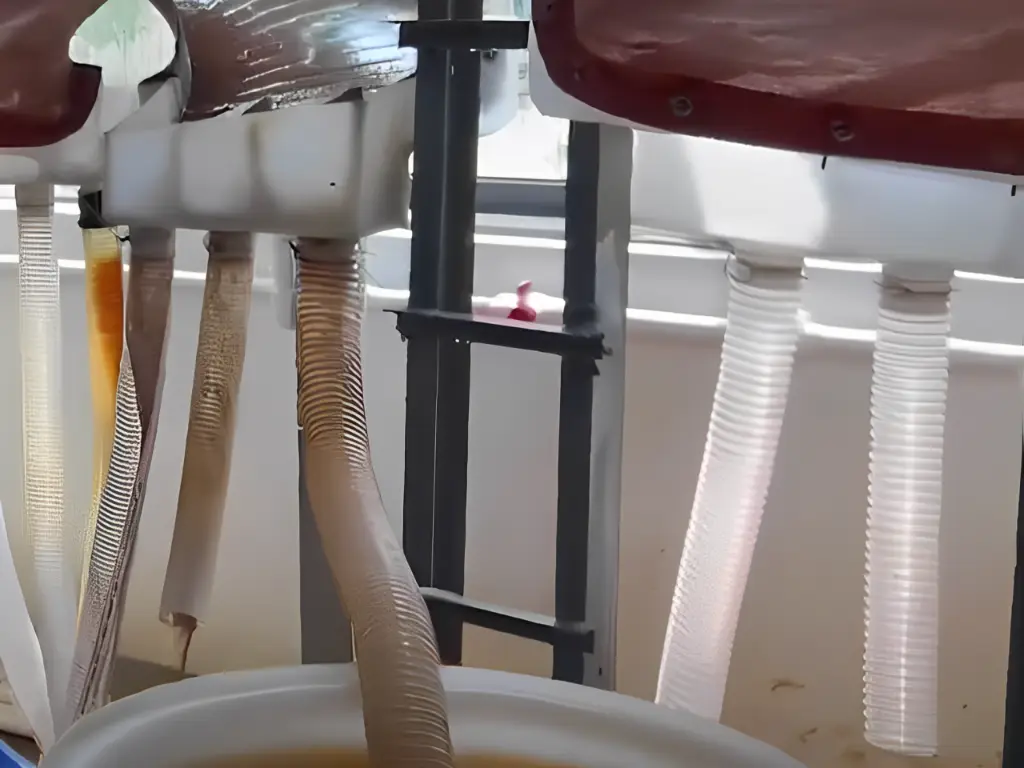
The Gravity Separation Method is a technique used in mineral processing to sort particles according to their specific gravity. This method relies on the force of gravity to help in the accumulation of denser particles while the lighter particles are washed or blown away. The process normally involves the use of equipment that provides motion in order to separate the denser particles from the lighter ones.
Gravity concentration is most suitable for the concentration of ores and recovery of minerals like gold. This is widely used in mining since it is easy to use, cheap and can process large quantities of material. The method is also friendly to the environment since it does not involve the use of chemicals to separate the minerals but rather depends on the physical characteristics of the minerals.
Gravity Separation vs Other Gold Mining Methods
Method | Characteristics | Pros and Cons |
---|---|---|
Gravity Separation | Uses gravity to separate heavy gold particles from lighter materials. Common techniques include panning, sluicing, shaking tables, and jigs. Often used in combination with other methods for better efficiency. | Low operational cost, simple technology, and environmentally friendly as it doesn't use chemicals. However, it has limited effectiveness for fine gold particles and requires significant manual labor. |
Cyanidation | Leaches gold from ore using a cyanide solution. Suitable for low-grade ore. Involves multiple stages, including leaching, adsorption, desorption, and recovery. | Highly effective for extracting gold from low-grade ore with a high recovery rate, but there are environmental and safety concerns due to the use of toxic chemicals, as well as high operational costs and complex procedures. |
Flotation | Separates gold from ore by using chemicals to create froth. Often used for sulfide ores. Involves crushing, grinding, and flotation stages. | Effective for complex ores with sulfides and can achieve high recovery rates, but it has high operational and capital costs, requires skilled personnel and complex infrastructure, and has an environmental impact due to chemical use. |
Amalgamation | Uses mercury to form an amalgam with gold. Gold is then extracted by heating the amalgam to vaporize the mercury. One of the oldest gold extraction methods. | Simple and inexpensive, this method is effective for fine gold recovery but highly toxic and dangerous due to mercury use, leading to severe environmental and health impacts. Its usage is declining due to better alternatives. |
Heap Leaching | Involves stacking ore in a heap and irrigating it with a leaching solution. Gold is leached from the ore and collected from the base of the heap. Suitable for low-grade ores. | The process is cost-effective for low-grade ore and simple and scalable. However, it has a slow recovery process and potential for environmental contamination due to leachate. |
Application of Gravity Separation in Mineral Processing
● Gold Mining: Panning, sluicing, shaking tables, jigs, spiral concentrators.
● Coal Processing: Dense medium separation, jigs, cyclones, wash plants.
● Iron Ore Beneficiation: Spirals, jigs, dense medium cyclones, gravity concentrators.
● Rare Earth Mineral Recovery: Shaking tables, spiral concentrators, centrifugal concentrators, magnetic separators.
● Tin and Tungsten Mining: Shaking tables, jigs, sluices, spiral concentrators.
4 Common Gravity Separation Methods
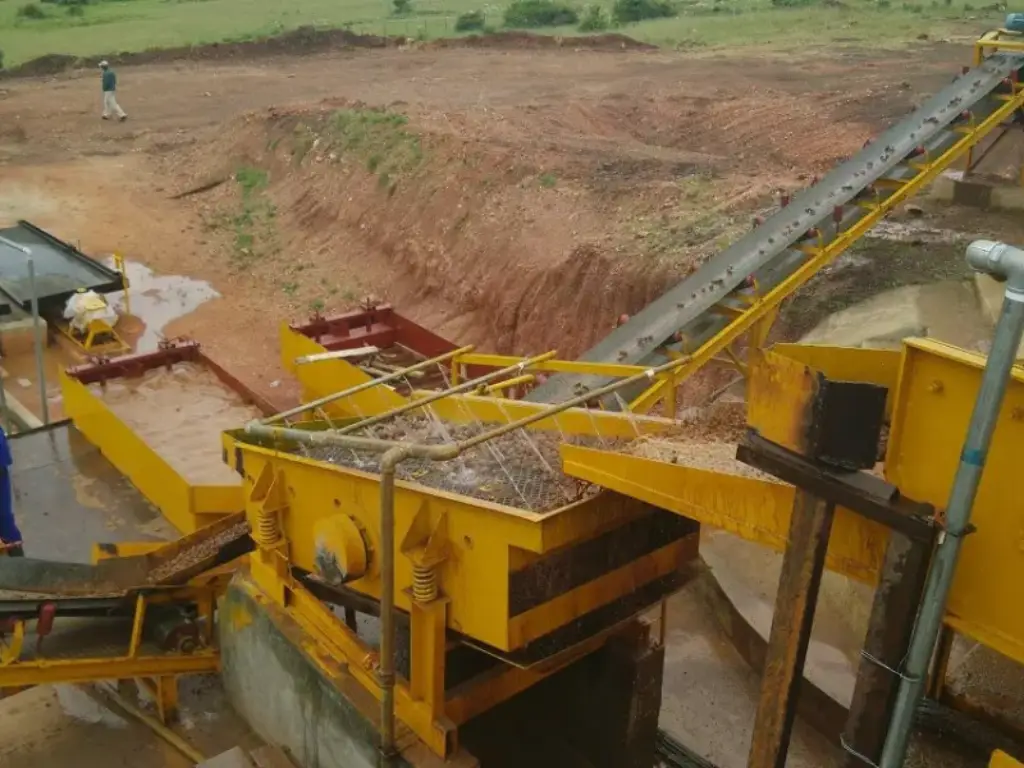
Gravity concentration is one of the most common methods of concentration of the valuable minerals from the ore based on the differences in their specific gravity. This method is widely used because of its efficiency, low cost, and applicability to large amounts of material. Here are four common gravity separation methods:
Jigging Gravity Separation
Jigging gravity separation involves the use of a jig which is a machine that oscillates the material in water in a vertical motion. This pulsation enables the denser materials to sink to the bottom while the lighter materials remain on the top. This makes jigging very efficient in the separation of coarse and medium sized particles, especially when dealing with ores that have a wide difference in densities. It is widely applied for the treatment of iron ore, coal and other minerals.
Jigging is very efficient in providing high degree of separation and hence widely used in the mineral processing plants. Furthermore, jigging can process large throughput and is relatively cheap in terms of operating cost as compared to other separation methods. Jigging is one of the most effective methods of separating high value minerals from a mixture, but it may not be as efficient as a very fine material. It is most useful in cases where there is a large difference in the density of the valuable minerals and the gangue.
Vibrating Table Gravity Separation
Vibrating table gravity separation involves the use of a vibrating table that moves the material on a slanting plane. The vibration makes the particles to move and sort themselves depending on their densities, the heavier particles move up while the lighter particles move down. This method is suitable for the separation of fine particles. Vibrating tables are used mostly in the extraction of gold, tin and other heavy minerals and are very efficient and can sort with a high degree of accuracy.
The adjustable vibration intensity and table slope make it possible to achieve the best separation efficiency for various mineral processing applications. The main benefit of vibrating tables is that they can achieve high concentrations of fine particles, but the drawback can be the increased costs of maintenance and operation due to the use of mechanical equipment. Vibrating tables are most appropriate for processes where the recovery of fine particles is important and where it is important to be able to control the operational parameters to obtain the required separation results.
Looking for top solutions? Check out Top 5 Vibrating Screen Manufacturers to enhance your gravity separation process.
Spiral Chute Gravity Separation
Spiral chute gravity separation is a process in which the material is fed at the top of a spiral shaped chute and allowed to flow in a helical path. The force that is created by the spiral movement assists in the separation process depending on the specific gravity of the particles; the particles with higher specific gravity will be closer to the center of the spiral while the lighter particles will be pushed outwards. This method is especially useful for the classification of fine materials and is applied in the concentration of chromite, zircon and other ores.
Spiral chutes are preferred due to low operational cost and simplicity of installation and thus are widely used in many mineral processing plants. Also, they can process particles of varying sizes and have a high throughput rate. Spiral chutes are also advantageous in that they can handle large throughputs of material with little or no harm to the environment because no chemical reagents are used. However, a limitation is that the separation efficiency can be influenced by the feed particle size and pulp density. They are best suited for use when the feed material is not very different in size and density and high throughput is desired.
Dense Medium Separation
Dense medium separation (DMS) employs a dense medium which is a water based fine magnetite or ferrosilicon suspension to sort particles by their relative density. The material is then fed into a vessel containing the dense medium where the lighter particles float while the heavier particles settle at the bottom. This method is very efficient, especially when dealing with ores that have a large difference in density. DMS is used in diamond, lead-zinc and other precious mineral processing and is accurate with large throughputs.
The method is useful in the mining industry because it provides a sharp separation and can be used on a number of minerals. In addition, the dense medium can be reused, thus cutting down on expenses and the effects on the environment. One of the strengths of DMS is that it has high separation efficiency and accuracy for the ores with significant difference in density, but one of the weaknesses is that it has high initial cost and the density of the medium has to be well controlled for the process to work well. DMS is especially suitable for the concentration of high value minerals where accuracy is paramount and where throughput rates must be optimized.
Types of Equipment Used in Gravity Separation Method
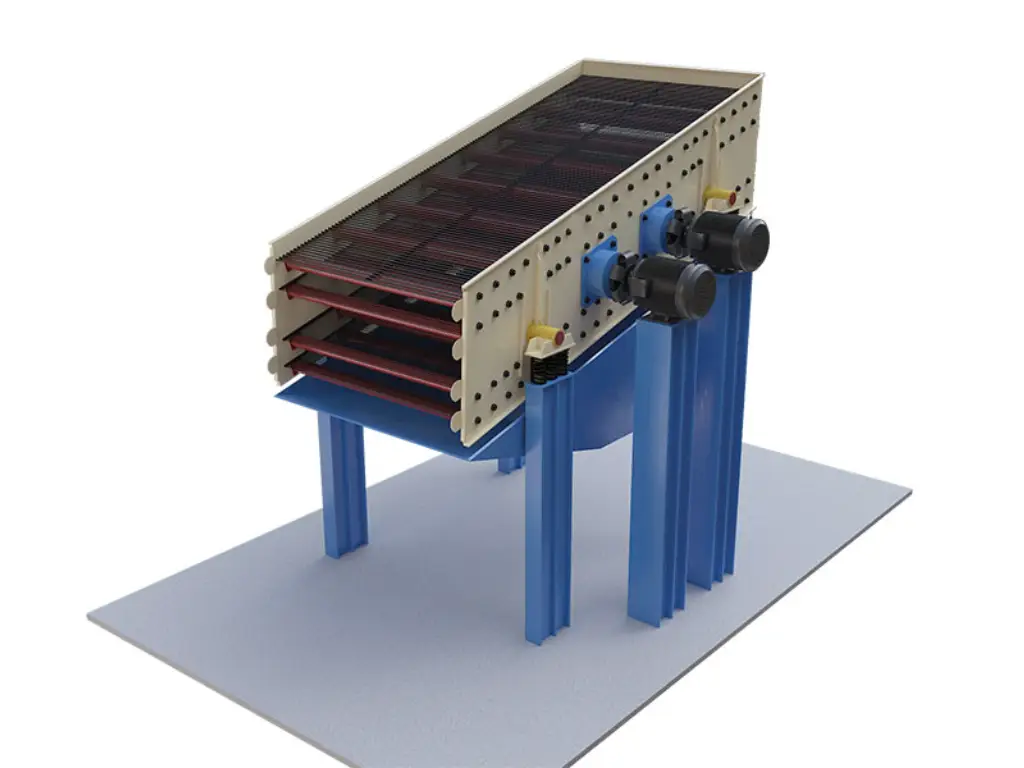
Gravity concentration is a method of concentrating the ore based on the differences in the specific gravity of the ore and the gangue. This method is commonly used in gold mining and operates on the basis of the difference in weight of the materials. Here are the main categories of equipment used in gravity concentration and their uses and advantages.
Panning
Panning is the most basic and probably the oldest technique of gold extraction. This is a process that involves mixing a pan that contains sediments and water in a circular motion to enable the denser gold particles to sink to the bottom. The lighter materials are washed over the edge. Panning is very effective but requires a lot of manpower especially for small scale operations and recovery of gold from placers. It is a low impact technique and is very useful in selecting and probing potential gold bearing zones.
Sluice Boxes
Sluice boxes are long narrow troughs with riffles on the base. While water is passing through the sluice, the riffles are designed to allow the heavier materials such as gold to settle at the bottom while the lighter materials are washed away. Sluice boxes can handle more material than panning and can be used in small scale as well as large scale mining. They are easy to build and manage and that is why they are preferred by miners.
Shaking tables are specific types of equipment that provide an up-and-down motion to sort particles depending on their specific gravity. The table surface is tilted and a mixture of water and crushed ore is introduced at the top end. When the table is shaken, the denser gold particles are transported to the end while the lighter particles are taken away. Shaking tables are very efficient and can even classify particles of gold that other methods may not be able to detect. They are mostly used in laboratories and small to medium scale mining.
Jigs are equipment that employ water pulses that help in the classification of minerals depending on their density. The jig is made up of a screen or a sieve on which the material is placed and water that is pumped through the material to make the heavier particles sink at the base. Jigs are very efficient for the recovery of coarse gold and are usually employed in combination with other processes. They are long lasting and can accommodate a large amount of material.
Spiral concentrators work by using the force of gravity and centrifugal force to sort particles according to their density. The material is fed at the top of the spiral and water is added to make the material to form a slurry. When the slurry is flowing down the spiral, the denser particles are forced to the outer perimeter of the spiral while the lighter particles remain in the center. Spiral concentrators are useful in the recovery of fine gold and are usually applied in combination with other gravity concentration processes to enhance the overall recovery.
Centrifugal Concentrators
Centrifugal concentrators increase the force of gravity in order to help separate fine particles of gold from other materials. These machines rotate at high speeds in order to generate a strong centrifugal force which forces denser gold particles to be trapped in a holding chamber. Centrifugal concentrators are very effective for fine gold recovery and are in use in most modern mining operations. They use less water than other processes and can extract gold from very low grades of ores.
Gold Wheels
Gold wheels, or spiral wheels, are used for panning fine gold particles from concentrates. These machines employ a circular spiral motion to help in the sorting of gold from other materials. The material is fed onto the wheel, and water washes the lighter particles while the heavier gold particles remain on the wheel. Gold wheels are most suitable for fine gold recovery from concentrates that are produced from other separation processes. They are easy to use and can be carried around hence preferred by most hobbyist miners.
How to Choose High-quality Gravity Separators
● Understand the Separation Process: Make sure that the equipment you are going to use is appropriate for the gravity-based separation process you need. This entails knowledge on how the separator deals with various materials such as the higher density and the lower density particles and the extent to which it can achieve stratification and sedimentation.
● Consider the Size Range: Assess the performance of the equipment in terms of size of particles that it can process, from micron sizes to grain sizes. Good separators should be able to handle materials with different grain sizes and be able to separate them in the best way possible regardless of the size difference.
● Evaluate the Specific Application: Select a separator depending on the requirements of the mineral processing, for instance DMS for coal or manganese ores. Knowledge of the specific application will assist in choosing a separator that is best suited for that particular application.
● Assess Operational Efficiency: When selecting separators, ensure that they have easy operations and do not require frequent maintenance. The ideal separators should be cheap to operate and maintain but should offer high performance regardless of the conditions prevailing at the time of operation.
● Conduct a Mineral Processing Test: Conduct comprehensive mineral processing tests to determine the efficiency of the separator on the desired minerals including platinum, copper or chromium. The tests can show how the equipment performs with regard to impurities and the required separation efficiency in actual operating conditions.
Visit gravity separators to find efficient solutions for gold recovery and ore concentration.
Factors Affecting the Efficiency of Gravity Separation Method
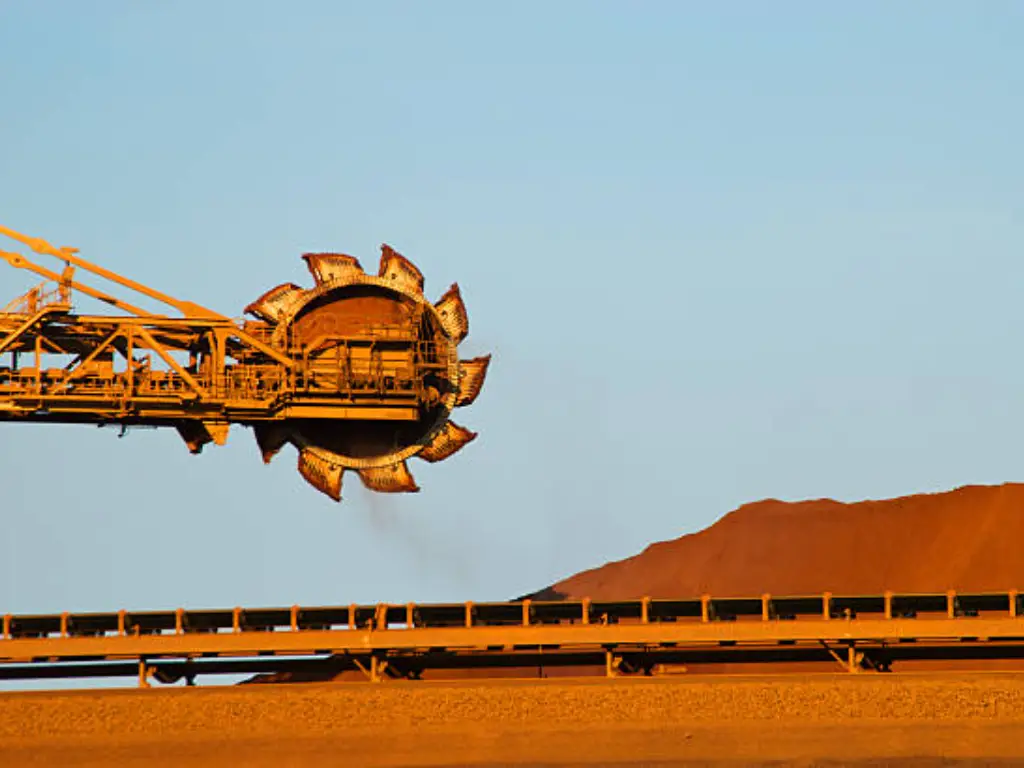
Particle Size and Shape: The size and shape of the particles play a very important role in the efficiency of the gravity separation. Particles that are larger and more condensed settle at a faster rate than those that are smaller and less condensed. Non-spherical particles may settle in a different manner compared to spherical ones. The efficiency of the separation process is improved by the right particle size distribution.
Specific Gravity Difference: The difference in specific gravity between the valuable mineral and the gangue material is important. When the specific gravity is higher, the separation is more effective since there are higher differences in the specific gravity. A minimal difference may lead to poor separation and hence low recovery rates. Selecting the right medium to bring out these differences is very important.
Fluid Dynamics: The flow rate and viscosity of the fluid used in separation influences the process. The flow rate should be sufficient to allow for separation without creating turbulence. High viscosity fluids may also slow down the particles’ movement and therefore decrease the efficiency of the process. The properties of the fluid have to be optimized in order to achieve the best results in the separation process.
Equipment Design and Configuration: The design and the setup of the gravity separation equipment are the main determinants of the performance. Parameters like the angle of inclination, surface roughness, and vibration frequency have to be fine tuned. Maintenance and calibration of equipment are crucial to guarantee that the equipment will work as expected. Optimizing the equipment for certain ores can improve outcomes.
Feed Rate and Consistency: The flow rate of the material through the separation equipment is another factor that influences efficiency. This means that feed rates are constant and do not overload the process of separation. Fluctuations in feed rate also cause poor separation and result in the loss of valuable minerals. Feed rate is another important factor that should be closely monitored and regulated to achieve the best results.
How to Improve the Efficiency of Gravity Separation?
Improving the accuracy of particle size classification by means of screening and hydraulic classification results in better separation. High performance equipment like the centrifugal concentrators and the shaking tables can improve the recovery rates by a big margin. Also, it is important to ensure that the operating conditions are well controlled, for instance, feed rates and water flow rates. This means that the equipment is always in good working condition through proper maintenance and calibration. Finally, combining gravity separation with other suitable techniques like flotation or magnetic separation can improve the general efficiency and recovery of minerals in the processing plants.
Improve gravity separation by exploring the vibrating screen diagram in the Detailed Guide: Vibrating Screen Diagram for Efficiency.
Future Trends and Innovations in Gravity Separation Method for Gold Mining
It is expected that the future of gravity separation in gold mining will experience further development due to technology and the environment. Other trends are the advancement of new and improved separation equipment that can effectively sort out even the smallest of particles and various types of ores. New technologies like improved centrifugal concentrators and superior hydraulic classifiers are designed to improve the yield of gold and at the same time, cut on energy and operating expenses. Also, there is a shift towards the use of environmentally friendly practices, thus the use of technologies that reduce the use of chemicals and enhance water reuse. All these advancements hold the potential of making gravity separation even more efficient and environmentally friendly in the future of gold mining.
Conclusion
Gravity concentration is one of the most important techniques in mineral processing as it provides a way of separating the valuable minerals from the unwanted gangue. With knowledge of this method and its uses, the different types of equipment that are used in mining, the mining operations can be made more efficient and the recovery rates increased. It is therefore important to choose the right gravity separation method depending on the mineral processing requirements and desired outcome.
FAQs
Which gold ores are most suitable for gravity concentration?
Gravity separation is most effective on gold ores with large differences in density between gold and other minerals. Some examples include the placer gold deposits where the gold is free and easily amenable to separation from the other minerals and the lode gold deposits that contain large and coarse gold particles.
Is it possible to apply gravity separation in combination with other gold extraction techniques?
Yes, gravity separation can be used in conjunction with other methods of gold extraction, including flotation and magnetic separation, to increase the overall recovery of gold. This combination makes it possible to process ores with fine and coarse gold particles in an efficient manner.
What precautions should be taken while using gravity separation equipment?
Measures that can be taken to enhance safety include; proper maintenance of the equipment, training of the operators, and adherence to safety measures. Operators should use the right PPE and adhere to the SOPs to avoid cases of accidents and injuries.