- Home
- Blog
- Mineral Solution
- Essential Guide to Vibrating Screen Parts
- mmldigi
What is a Vibrating Screen?
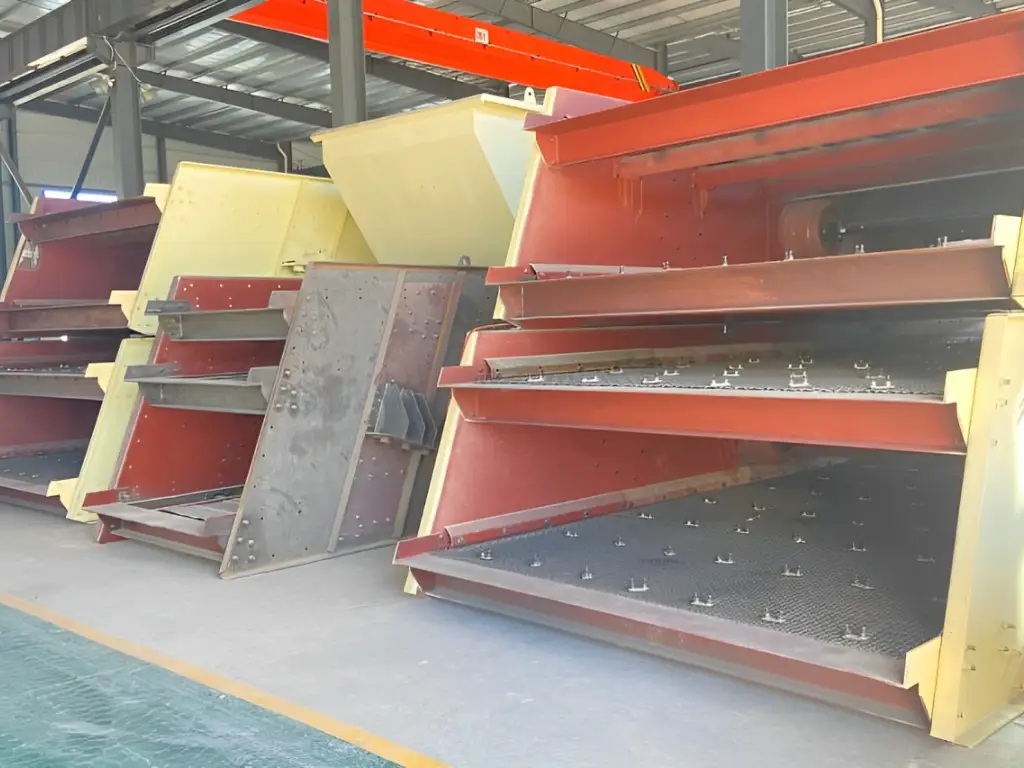
A vibrating screen is a machine used in industries for classification of materials by size, shape and density. It works by oscillating a screen mesh, where smaller particles are allowed to pass through the mesh while the larger particles remain on the surface of the mesh. This separation process is very important in mining, construction, agriculture and recycling industries. Vibrating screens have many advantages, such as high productivity, accuracy, and flexibility, which makes them essential for sorting and classification of materials in various industries. This makes them suitable for use in a wide variety of processes involving wet and dry materials.
The Importance of Vibrating Screen Parts
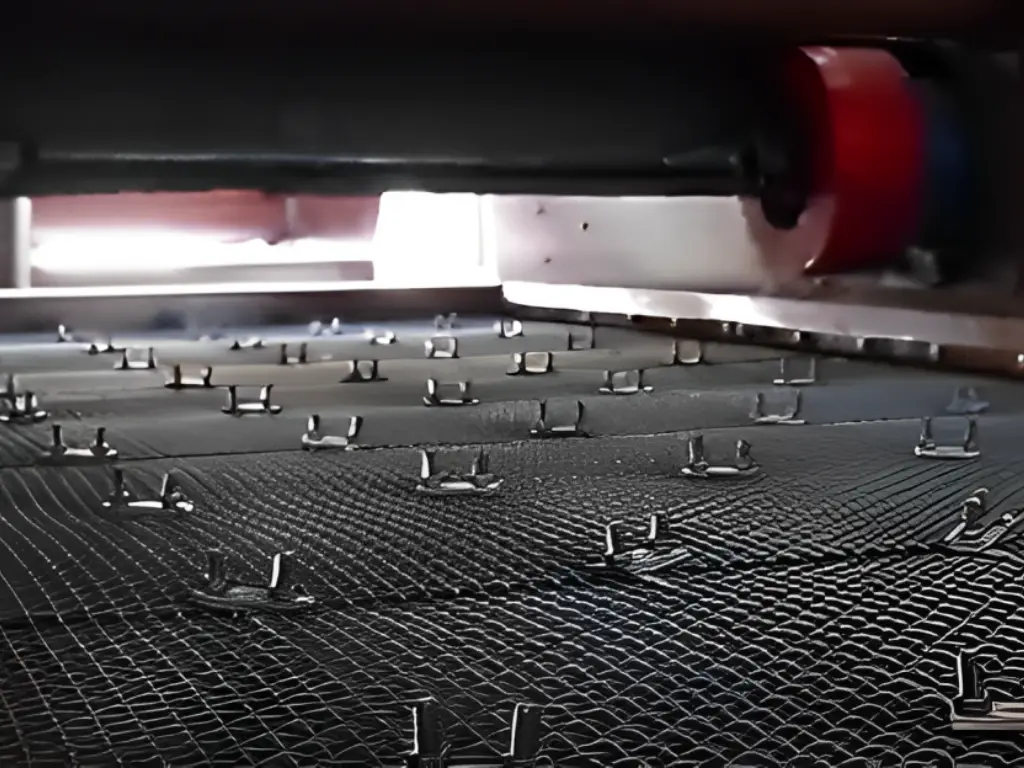
Vibrating screen parts are very important in the performance of the screen and the efficiency of the operation. Every component, ranging from the screen mesh to the side plates, has a crucial function in the proper functioning and durability of the equipment. Knowledge of these parts and their roles can be useful in preserving the screen and its efficiency and prolonging its useful life.
Screen Mesh
The screen mesh is perhaps the most important part of a vibrating screen since it determines the efficiency of the screen. It is the one that physically separates materials. Usually constructed from high tensile steel or stainless steel, the mesh has to endure vibrations and abrasive content. Polyurethane meshes are also used due to its abrasion resistance and longer service life in wet environments. It is also important to note that different applications may call for different mesh sizes and types for the best results. The mesh’s characteristics such as the thickness and the pattern of the holes determine the effectiveness of the screening process.
Side Plates
Side plates are used to give support to the vibrating screen. These are made of high strength steel to provide the necessary rigidity and stability of the screen during its use. They are made to endure the steady pressure and shake that is produced by the screen’s movement. The thickness of the side plates is also important; thick side plates are more durable but they also increase the weight of the machine. Side plates are critical components of structures, and their maintenance is crucial to avoid failure and production loss. They also provide provisions for easy inspection and replacement in their design to ensure that interruption of operations is kept to a minimum.
Cross Members
Cross members are used to help support the screen mesh and to help distribute the load of the screen evenly. Most of them are manufactured from hard wearing steel alloys to guarantee that the mesh is tight and efficient in its role of sifting materials. Cross members are designed to support linear and circular motion where the screen is designed in that way. The arrangement and positioning are crucial for the screen’s stability and functionality on the structure. Cross members should be inspected and maintained frequently to avoid sagging and misalignment, which will affect screening efficiency.
Feed Box
The feed box is the point where the material to be sieved is fed into the screen. Constructed from wear-resistant materials such as AR (abrasion-resistant) steel, it provides for an even distribution of material across the screen mesh which is vital in screening. It is also important to note that a properly designed feed box can enhance the screen’s performance and decrease the wear of the mesh. It frequently contains provisions for reducing the effects of the material flow and avoiding early failure. It is important to make sure that the feed box is in good condition to guarantee proper flow of materials and screening.
Rubber Buffers
Rubber buffers are installed to reduce the vibration and protect the screen and other structures from damages. They are manufactured from natural or synthetic rubber and help in minimizing noise and enhancing the safety of the operation. Rubber buffers also help in increasing the service life of the vibrating screen because they reduce metal on metal contact. Rubber buffers of high quality can greatly increase the service life of the screen. Their design should enable easy replacement in order to maintain a continuous operation without having to undertake extensive periods of downtime.
Vibrator
The vibrator is the main working component of the vibrating screen, which provides the required vibration for the separation of materials. Usually, vibrators are accurate parts that are manufactured from high-quality materials to guarantee reliability. They are of different categories including electric motor driven or hydraulic vibrators depending on the intended use. It is therefore important to service the vibrators frequently and replace them with new ones once they have worn out to avoid unnecessary downtimes. Proper maintenance of the vibrator aids in achieving the right vibration intensity that is required for proper screening.
For better efficiency in screen design and usage, view the Detailed Guide: Vibrating Screen Diagram for Efficiency.
How to improve the lifespan of vibrating screen parts?
Tips | Description | Benefits |
---|---|---|
Regular Maintenance | Perform routine inspections and maintenance to identify and address wear and tear early. | Prevents major failures and prolongs life |
Use High-Quality Parts | Invest in parts made from durable, wear-resistant materials. | Reduces frequency of replacements |
Proper Installation | Ensure all parts are correctly installed and aligned according to the manufacturer’s specifications. | Minimizes undue stress and damage |
Optimize Operating Conditions | Maintain optimal operating conditions by avoiding overloading and ensuring proper tension and alignment. | Enhances efficiency and reduces wear |
Regular Lubrication | Keep moving parts well-lubricated to reduce friction and wear. | Extends the lifespan of components |
For insights into optimizing vibrating screen performance, visit Vibrating Screen Design Demystified: Types and Benefits.
How to Choose the Right Vibrating Screen Parts for Specific Applications?
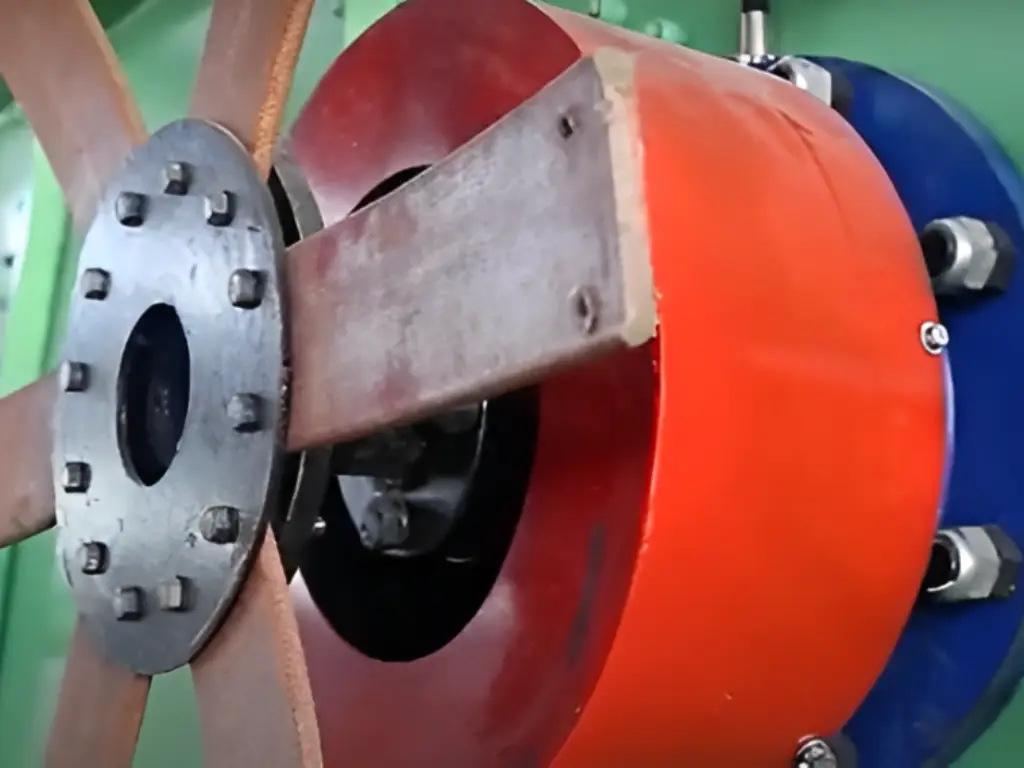
● Identify the Material Characteristics: Know the characteristics of the material you are working on in terms of its physical properties. Some of the aspects that affect the selection of screen parts include particle size, density, moisture content, and abrasiveness. It is important to use the right screen media for the right material to get the best performance and durability.
● Determine the Screening Purpose: Determine whether your application entails scalping, sizing, or dewatering. Both purposes require certain screen types and arrangements. For instance, dewatering screens are normally finer and their tensioning is more critical than that of scalping screens.
● Consider the Operating Environment: Evaluate the environment in which the vibrating screen is to be used in order to determine the most suitable one. These are factors such as temperature, humidity, and exposure to corrosive substances. Selecting materials that are suitable for rough conditions like wet or corrosive conditions . For instance, stainless steel is very important.
● Evaluate the Load and Capacity Requirements: Determine the expected load and capacity of the vibrating screen. The screen size, mesh type, and the load-bearing capacity of the parts should be compatible with the operation requirements to enhance efficiency and reduce the wear and tear.
● Analyze the Maintenance Needs: Think about the possibility to clean and replace the screen parts easily. Select components that can be easily fitted and do not need much time to be fixed. Modular designs can help to allow for faster maintenance and less disruption of operations.
As a professional vibrating screen manufacturer, JXSC offers vibrating screen spare parts that can be designed according to the specific application, so as to guarantee the service life and performance of the vibrating screen.
Conclusion
Thus, vibrating screens are essential tools in various industries for separation and classification of materials. The efficiency of these screens depends on the quality and the functionality of the parts used in the construction of the screens. When choosing the components, it is advisable to use high quality, long-lasting, and adjustable ones from reliable manufacturers like JXSC Mine Machinery Factory to ensure high productivity, longevity and minimal breakdowns. Correct installation and regular maintenance are the key factors that enhance the durability and efficiency of the vibrating screen parts, which are essential in the current industry.
FAQs
How to Properly Install Vibrating Screen Parts?
Some of the measures that need to be taken while installing the vibrating screen parts include; The vibrating screen and its parts should be set on a level ground and all the parts should be well secured to avoid too much vibration. Ensure that you adhere to the manufacturer’s torque settings on bolts and other related fasteners. Ensure that the screen media is aligned and has the correct tension to prevent wear and tear of some parts of the media more than others. Last of all, spin the screen for a few seconds to check that it does not make any strange sounds or vibrate.
How do different vibrating screen parts work together?
Various components of the vibrating screen contribute to the efficient separation of the materials. The screen is used to filter the material by size while the vibrating motor is used to give the required motion to the material to pass through the mesh. The frame is the main component of the assembly and provides the necessary rigidity, and damping springs help to damp vibrations, which reduces noise and wear. In this way, all the components contribute to the proper and efficient screening process.