- Home
- Blog
- Mineral Solution
- Diamond Processing Steps: From Mine to Market
- mmldigi
Kimberlite rock is the foundational source for most of the world’s diamonds, forming deep within the Earth and brought to the surface through volcanic activity. Upon exposure, kimberlite is prone to erosion, a process that naturally releases diamonds into surrounding environments, notably into riverbeds and coastal zones, creating alluvial diamond deposits. These alluvial deposits, formed from eroded kimberlite, are significant; they are estimated to represent about 40% of the global diamond reserves yet account for approximately 70% of the world’s diamond production. This discrepancy underscores the efficiency and prevalence of alluvial mining techniques in extracting diamonds, making these deposits a critical component of the global diamond supply.
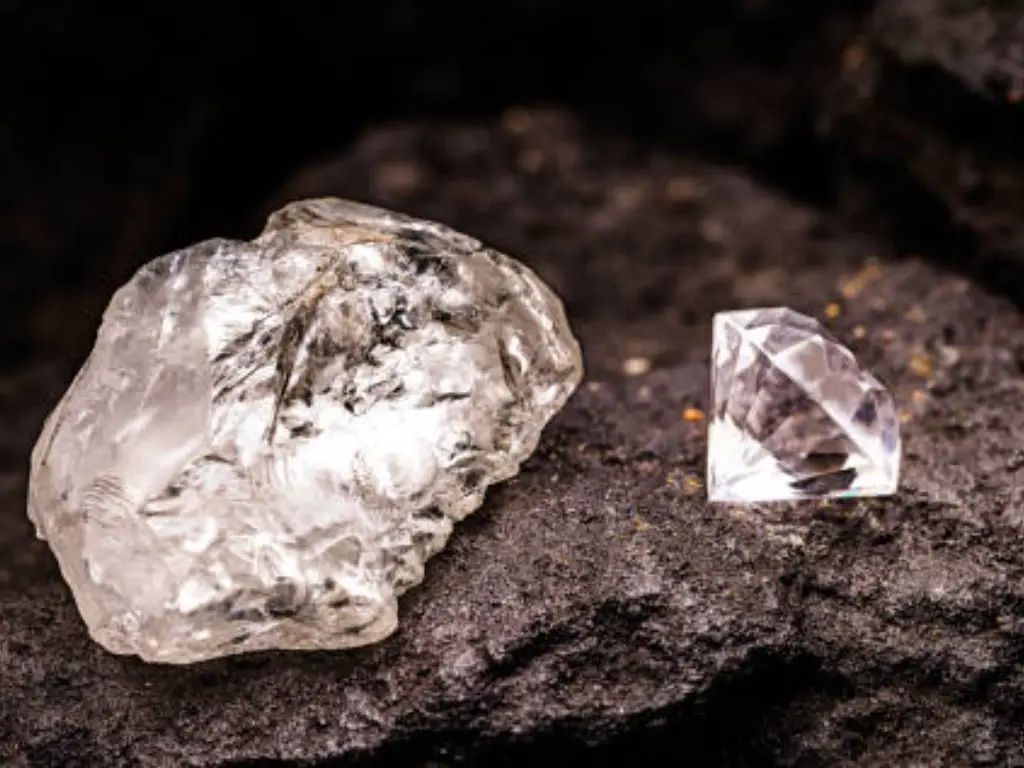
Countries With Abundant Diamond Resources
Places like South Africa, Russia, and Canada are super famous for having loads of diamonds, and they play a huge role in the diamond world. South Africa is a big deal in the diamond history because it’s where the very first diamond was discovered back in 1866. This was a game-changer and since then, South Africa has been at the forefront of the diamond scene. It’s got loads of kimberlite pipes and areas full of alluvial diamonds, making it a go-to place for getting both the rough and the shiny polished diamonds. Then we’ve got Russia and Canada. These countries are the heavyweights of diamond mining, with gigantic areas filled with some of the most important diamond mines out there. They use both the open-pit and underground methods to get to those sparkly gems.
Pipe Mining
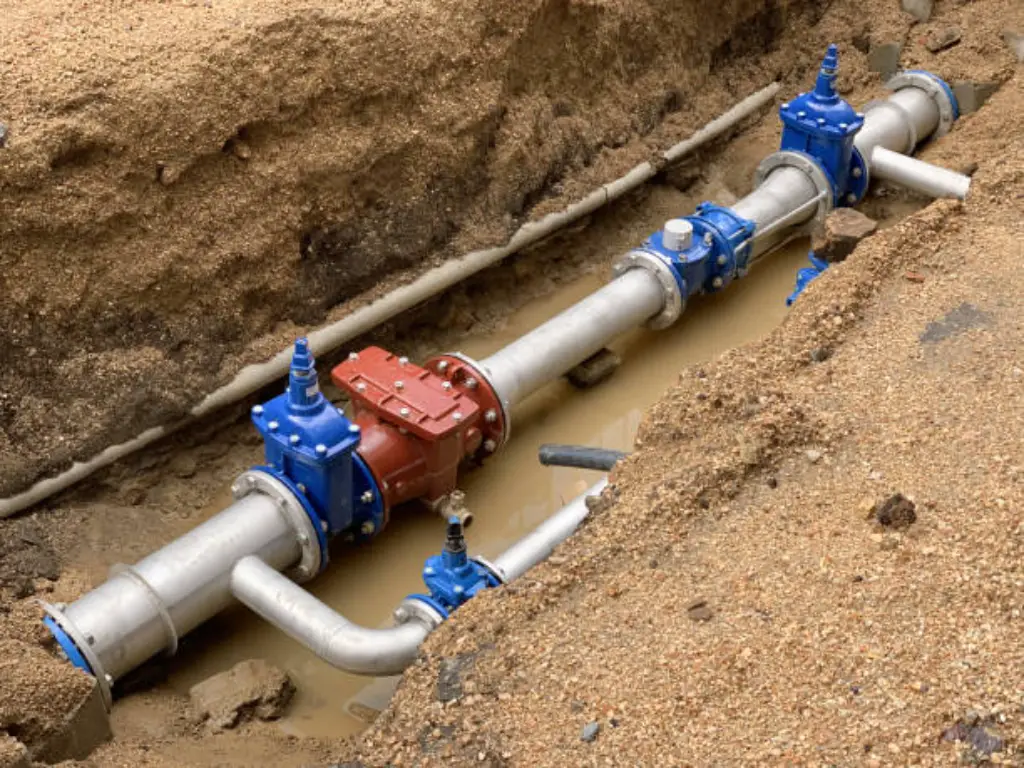
Pipe mining is the most common method used to extract diamonds, there are two types of pipe mining.
Open-Pit Mining:
In open-pit mining, everything kicks off by getting rid of the top layer to reveal the kimberlite pipe underneath. The next big step is blasting, where they use explosives to break up the kimberlite, making it possible to pull out the diamond-rich ore. After the explosion, the broken ore is gathered from the bottom of the pit. They bring in the big machines to move the ore from where it was blasted to where it needs to go next, which is a primary crusher. Crushing the ore for the first time is super important because it makes the ore smaller and easier to handle, setting the stage for all the steps that follow to get those diamonds out.
Underground Mining:
Underground mining, on the flip side, starts with digging shafts next to the kimberlite pipe to reach the ore way down below the earth’s surface. Then, they build tunnels to get to the diamond-filled rock. Setting off explosions in these tunnels breaks the ore loose, where it either falls to the ground or slides down chutes, so it’s easy to collect. After that, the ore is loaded up and taken to the surface, either on trucks or conveyor belts. Just like with open-pit mining, the very first thing they do is crush the ore, either right there underground or up on the surface, depending on how the mine works. Once the ore is crushed, it’s on to the next steps in the process, where they’ll eventually get the diamonds out and ready for more.
Alluvial Mining
Alluvial mining is all about getting diamonds from spots where they’ve ended up after being washed away from their original home in kimberlite and carried off by rivers and streams. This usually happens in the gravel of riverbeds, along lakes, and by the coast. Miners looking to tap into these gravelly goldmines might change the path of a river to get to the diamond-packed layers underneath or they might go for open-pit mining in these areas. That means they carefully peel away layers of dirt and rock until they hit the gravel. Then, they wash and sift through it to pick out the diamond ore, separating it from everything else. This approach makes the most of nature’s way of gathering diamonds in easy-to-reach places and is often kinder to the environment than older mining methods.
Marine Mining
Marine mining off Namibia’s coast is a big leap from the old days when divers would collect gravel from the shallows. Namibia is now a leader in marine mining, with operations covering more than 6,000 square kilometers out at sea. They’re after the seabed’s stash of diamonds, thought to be more than 1.5 billion carats deep under the water. Nowadays, advanced ships with heavy gear and drilling tech head out into the deep blue to get or drill for gravel filled with diamonds. Moving from hands-on, shallow-water collecting to using high-tech ships shows how far the industry has come. It also puts Namibia in the spotlight as a major player in the diamond world.
Diamond Processing Steps
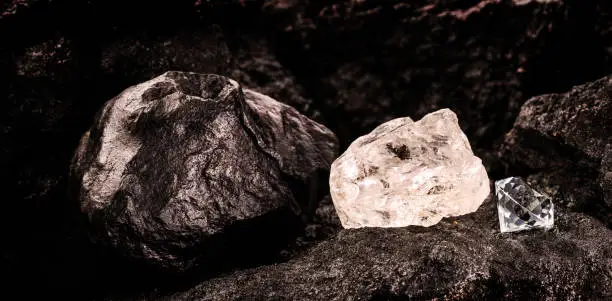
6 Main Steps | Equipment Used |
---|---|
1. Crushing | Jaw Crushers, Cone Crushers,Roll Crushers |
2. Scrubbing and Screening | Drum Washers, Vibratory Screens |
3. Dense Media Separation (DMS) | Cyclones, Dense Media Separation Units |
4. Coarse Recovery and Concentration | Jigging Machines, Grease Tables, X-Ray Sorters, Magnetic Separators |
5. Recovery | Magnetic Separators, X-Ray Luminescence Machines, Laser Fluorescence Detectors |
6. Cleaning, Weighing, and Packaging | Acid Washing Tanks, Precision Scales, Packaging Equipment |
Crushing
The first step in making diamonds ready for sale is crushing the kimberlite ore. This important action helps to free the rough diamonds from the solid rock around them. They use heavy-duty machines to smash the ore into smaller bits, usually making them no bigger than 150 millimeters across. Making the pieces smaller is super important because it helps with the next steps, where the diamonds are separated and pulled out, making sure we get as many diamonds as possible.
Scrubbing and Screening
After the ore has been crushed, it’s time for scrubbing and screening. In the scrubbing phase, the ore gets a thorough wash in a big drum washer. This washes away sticky dirt like clay and mud which might make it harder to separate out the diamonds later. The screening process then sorts the clean ore by size. Tiny bits, smaller than 1.5mm, get thrown away because it’s not worth it to try and get diamonds from them. This stage is super key for making sure the process is efficient, as it keeps only the ore that’s more likely to have diamonds in it, moving everything along to the next step.
Dense Media Separation (DMS)
In this stage, at the separation plant, we use cool tech to take advantage of the crushed ore’s physical traits. We mix ferrosilicon powder with water to make a slurry that’s just the right density to split diamond-filled material from the lighter, useless rock. When we spin this mix in a cyclone, the denser bits with diamonds get flung to the sides and collected. This method of sorting by density is super important for getting diamonds out of the ore effectively.
Coarse Recovery and Concentration
For raw ore: Initially, after crushing and grading (weathered samples need pre-screening), jigging and sorting are conducted. The jigging tailings enter the grinding process, then the unliberated diamonds are dissociated. After dissociation, materials return to the jigging selection cycle several times until the ore is ground to the selected lower limit of particle size.
For alluvial mines: Through washing, screening, grading to remove mud, separating large gravel and fine mud tailings, and clean sand jigging separation, coarse concentrate can be obtained. In the concentration process for diamond extraction, equipment adjusts to different sizes: hand picking for sizes above 4mm; X-ray sorting or grease table for -4+1mm; particle flotation, shaking tables, magnetic separation, gravity separation, selective grinding, caustic dissolution, dense liquid separation, and microscopic screening for -1+0.2mm.
Recovery
Next, we use some high-tech tools to pick out diamonds from the sorted ore. We’ve got gadgets that use magnetism to find minerals around diamonds, X-ray beams to spot diamonds by their glow, and laser tech to pick them by their structure. All these methods together help us grab diamonds with amazing accuracy, making sure we hardly lose any.
Cleaning, Weighing, and Packaging
After finding them, diamonds get a thorough clean, often with acid, to ditch any dirt left. Then we weigh them and pack them up tight. Every package gets a security seal and a certificate to prove where it came from, sticking to the Kimberley Process rules to make sure these diamonds are conflict-free. This last step means our diamonds are ready to go, from deep in the earth all the way to shining in a jewelry store window.
Cutting
The diamond cutting process is an intricate interplay between art and science, expertly executed by diamond cutters who determine the best cut to enhance the carat weight, brilliance, and clarity of rough stones. Utilizing cutting tools powered by an electric motor and a cutting disc coated in diamond powder, one of the hardest materials known, cutters aim for the optimal way to transform a small piece of ore into a faceted diamond. This first objective is to balance the economic perspective with the specific properties of diamonds, ensuring each cut maximizes the diamond’s potential value by considering factors like the specific relative density of the gemstone and the size of the ore.
Polishing

In the polishing process, diamonds are transformed from manageable pieces into finished diamonds that reveal their inherent sparkle. This requires great skill and the use of high-speed polishing wheels coated with diamond dust, targeting every layer of diamond to achieve a glossy finish. The aim is to polish the main facets, lower girdle facets, and the upper girdle in such a way that the angles maximize flashes of light, showcasing the diamond’s fluorescence and bringing out the best fire and brilliance. This optimal method sheds loose excess material, revealing the larger diamonds beneath and ensuring the best cut for maximum return.
Grading
Once the faceted diamond has been cut and polished, its value is thoroughly assessed through a grading process. Professionals utilize sophisticated tools, like magnifying glasses and spectrometers, to measure the diamond bearing ore’s dimensions, assessing elements like carat weight and cut quality. This step is crucial for understanding the economic value of diamonds, highlighting how aspects like cut quality impact the rich concentration of value in each gem. The diamond’s grading from an economic perspective plays a pivotal role in determining its market value and price, ensuring that each finished diamond meets the industry’s highest standards.
Packaging and Selling
After the rigorous grading process, diamonds are cleaned and placed into packaging with a tamper-resistant seal, signifying readiness for sale. Diamond manufacturers and dealers provide detailed certificates that specify the characteristics and grade of each gem, appealing to consumers’ desire for authenticity and quality assurance. These diamonds, having gone through an intensive process from a single blast in the type of mining that recovers tonnes of ore, now enter the jewelry market. They become part of exquisite pieces or are sold directly as valuable investments to consumers who appreciate the meticulous process—from the earliest form of marine mining to the sophisticated solution of ferrosilicon powder used in the extraction—culminating in the maximum return of these precious gems.
This comprehensive process, from the diamond cutting process to its entry into the market, illustrates the transformation of raw, heavy density materials into sparkling treasures, driven by a relentless pursuit of excellence and precision.
FAQs
What methods are generally used in the diamond beneficiation step?
When it comes to processing diamonds, we use a bunch of different methods like gravity and density separation, X-ray and optical sorting, and sometimes even picking them out by hand. These methods make use of diamonds’ unique properties, like how heavy they are, how they glow under X-ray, and the way they look, to separate them from other stuff.
How do diamond processing techniques vary by type of deposit?
Well, the method we use depends a lot on where the diamonds were found. For diamonds stuck in hard kimberlite rock, we’ve got to crush the rock open. If we’re talking about alluvial mining, like in riverbeds, it’s mostly about washing and sifting through the sediment. And for marine mining, where we get diamonds from the seabed, we use special ships with tech to suck up the ocean floor.
How does the beneficiation process differ between alluvial, marine, and kimberlite diamond deposits?
Yes, there’s a bit of a difference. With alluvial mining, things are pretty straightforward – we wash and sift to get diamonds from amongst the gravel and sand. For those found in kimberlite, it’s more complicated; we need to crush the rock and then use heavy separation methods to get the diamonds. And with marine mining, it’s a lot like alluvial mining but done under the sea, so we need ships with special gear to do the sorting and collecting right there on the water.
Conclusion
The whole journey of diamond mining and making them sparkle is super important for lots of industries, not just for the beauty of the final shiny diamond. The careful and clever steps we take to get those diamonds out and make them look their best are key. They help make sure we can keep finding diamonds in a way that’s good for our planet, and they’re a big deal for the tech world and for helping the places where diamonds come from grow. By getting better and smarter at how we extract diamonds, the industry is leading the way to being efficient and taking care of the environment while digging up these precious gems.