- Home
- Blog
- Equipment Info
- Ultimate Guide to Crushing of a Stone: Methods & Equipment
- mmldigi
Why Crushed Stone is Essential: Diverse Industrial Uses
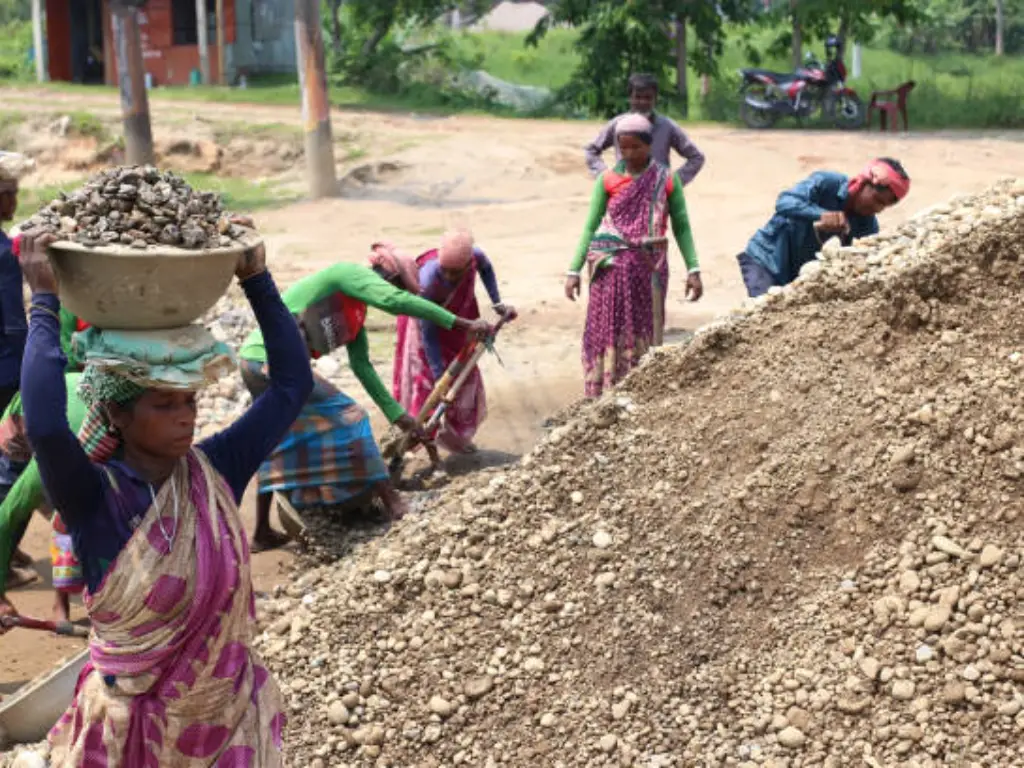
Different Types of Stone and Their Crushing Needs
Stone Type | Typical Initial Stone Size Range | Hardness | Crushing Considerations |
---|---|---|---|
Granite | Up to several meters | Very Hard Rock | Requires robust and powerful crushers like jaw crusher and cone crushers. Abrasive materials nature can lead to higher wear on equipment. |
Limestone | Up to several meters | Moderately Hardness | Generally easier to crushing than granite. Jaw crusher, impact, and cone crushers are commonly used. Can be prone to stone dust. |
Basalt | Up to several meters | Hard Rock | Similar to granite in terms of hardness, requiring strong crushers. Often used for high-quality aggregate. |
Sandstone | Up to several meters | Soft to Medium | Can be crushed relatively easily, sometimes even with hydraulic breakers. May require careful handling due to its abrasive materials nature. |
Quartzite | Up to several meters | Very Hard Rock | Highly abrasive materials and requires crushers with wear-resistant components. Often produces angular and durable aggregate. |
Gravel/River Rock | Variable, up to ~300mm | Soft to Medium | Can often be processed with impact crushers or even screeners and washing, depending on the desired end product. Round shape can affect interlocking in some applications. |
Shale | Variable, often fragmented | Soft | Can be easily crushed but may break down into very fine smaller particles, requiring careful control of the crushing process. Can be prone to moisture content issues. |
Dolomite | Up to several meters | Moderately Hard | Similar to limestone, often used in construction. Requires appropriate crushers based on hardness. In light of this information, it is evident that the larger category of stone is very variable, with ‘boulders’ from quarries and smaller, more manageable stones constituting a portion of it. The hardness of the types of stone, including those found in the bladder, is another critical consideration because it affects the kind of crushers that will be used and the energy needed for the work. |
The Three Stages of Industrial Stone Crushing: Coarse, Medium, Fine
Coarse Crushing Equipment: Primary Jaw Crusher and Impact Crushers
Medium Crushing Equipment: Cone and Secondary Impact Crushers
Fine Crushing Equipment: VSI and Tertiary Crushers
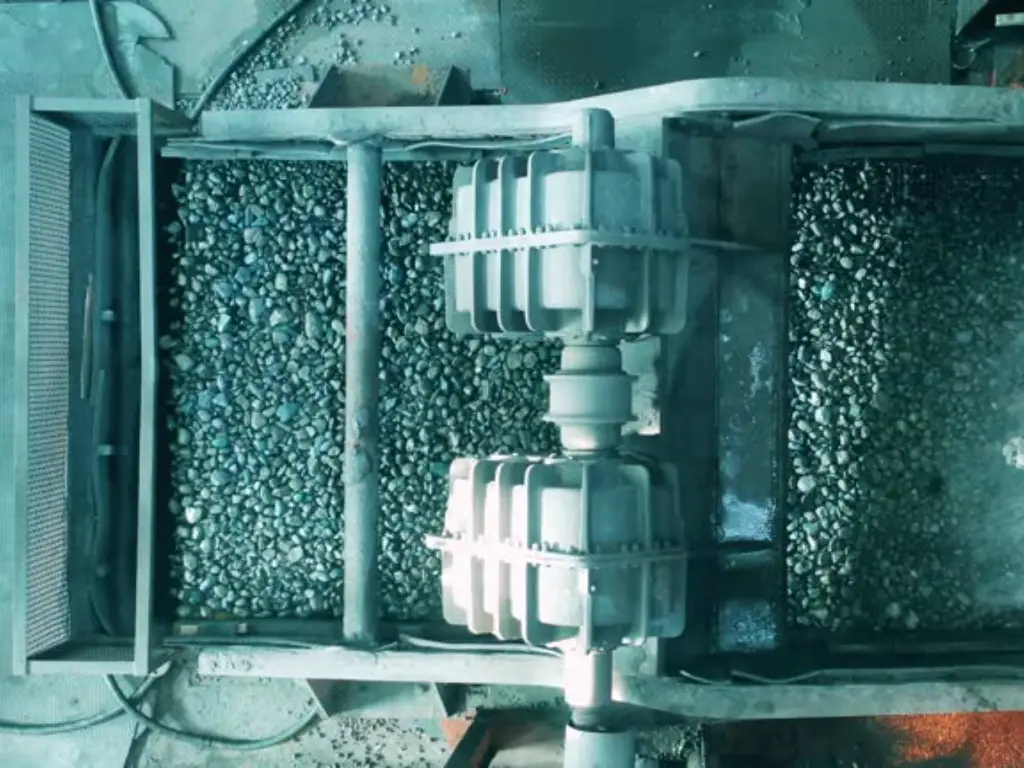
Methods of Crushing Stone: From Manual to Industrial
The procedures that take place on-site, during mining, after mining or even within the works of structures are subjected to a lot of changes due to the presence of highly situated quarries, Pulverizing facilities and several Non-Mining related Industries. These large scale movements of stones provide us with a Voluminous Quantity of waste That Is Initially Treated during the Pre and Post Mining Operations in the form of Gross Leveling Screening and the obfuscating of the waste soil and other materials. In the first stage referred to as primary mining, the crystallized rocks are broken into smaller pieces. In the process of intermediate crushing, trilithon, block and gigantic stone forms are distinguished. In the second stage, crude stone is transformed into refined stone. The basic crushed stone is crushed again and converted into gravel. In the including stone formations we use stones and stony shale to a considerable extent in all forms of construction industry.
Key Equipment for Effective Stone Crushing in mineral: JXSC Solutions
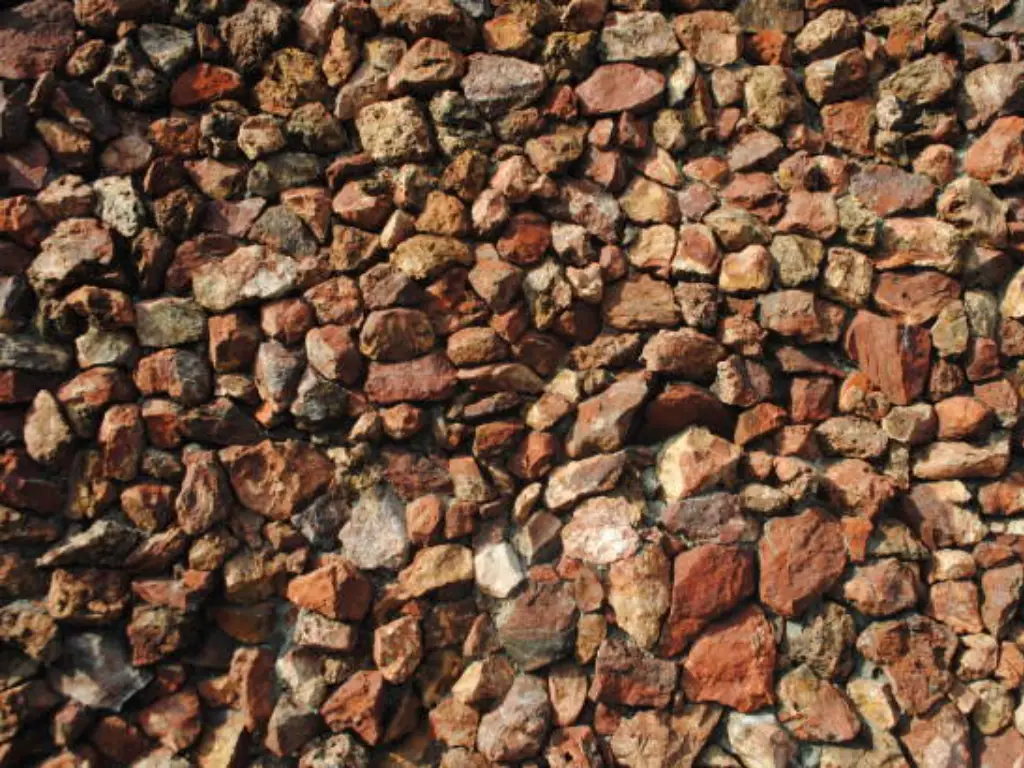
Factors Affecting Crushing Efficiency and Cost Optimization
Choosing the Right Equipment Stone Crushing Solution: Considerations & Tips
1. Type of Stone:
● Limestone: In construction and agricultural industries, limestone is commonly used in the cement sector. Due to its relatively soft nature, it can be well processed with crushers specifically made for soft materials. These crushers should be economical in performance and non-excessive in wear.