- Home
- Blog
- Mineral Solution
- Crushing in Mineral Processing: Enhancing Ore Recovery and Quality
- mmldigi
What is Crushing in Mineral Processing?
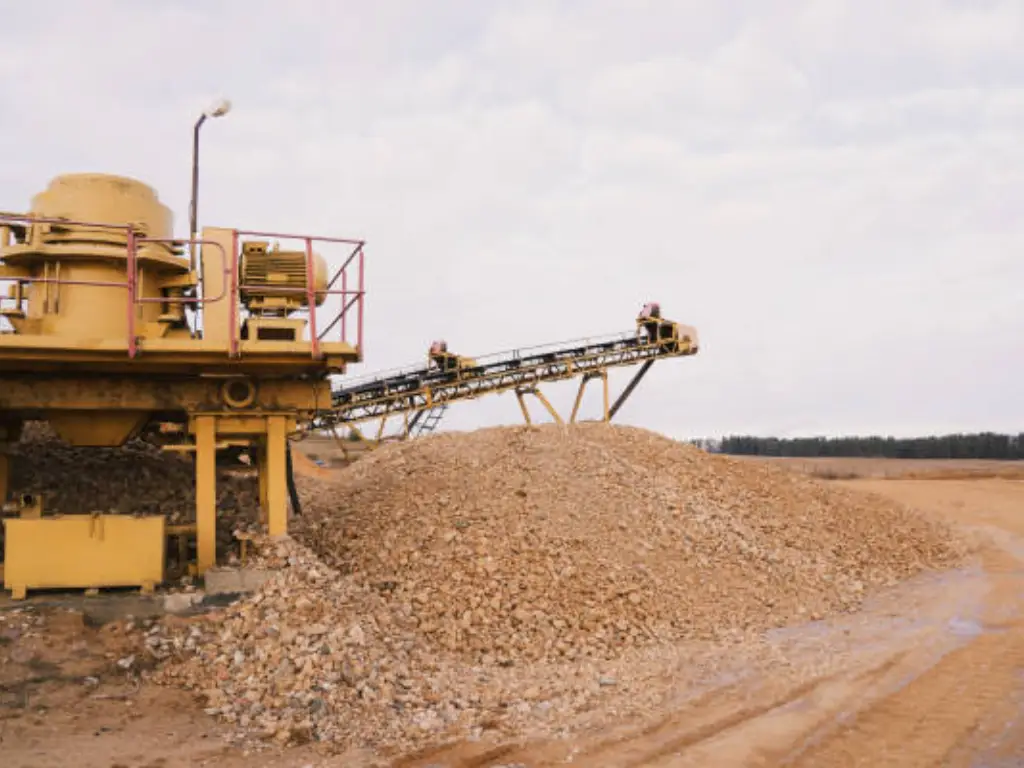
Crushing in mineral processing is the first step that involves breaking of the large ore materials into smaller sizes by crushing machinery. This process is important because big size of the ore can be problematic to the subsequent processes like grinding and separation. The primary purpose is to enhance liberation of the valuable minerals from the waste rock hence increasing the efficiency of the final product. Through fine grinding, we are able to increase the surface area of the particles, which in turn increases the effectiveness of subsequent separation methods. This is not just about reducing the size of the ore; it is about the efficient flow of operations in the plant for the highest return on investment.
Crushing operations may be performed in several stages, mainly primary crushing where large size of ore is broken into smaller sizes. After this it is possible to use secondary and tertiary crushers to obtain the desired particle size. Each crushing stage has been designed to handle specific particle size and the final crusher product, so only the right particle size is taken for further processing. It is crucial that all players in the chain of the mineral processing value addition process understand this process at length since it determines use of energy, efficiency and the overall profitability of the mining operation.
How Does Crushing Work in Mineral Processing?
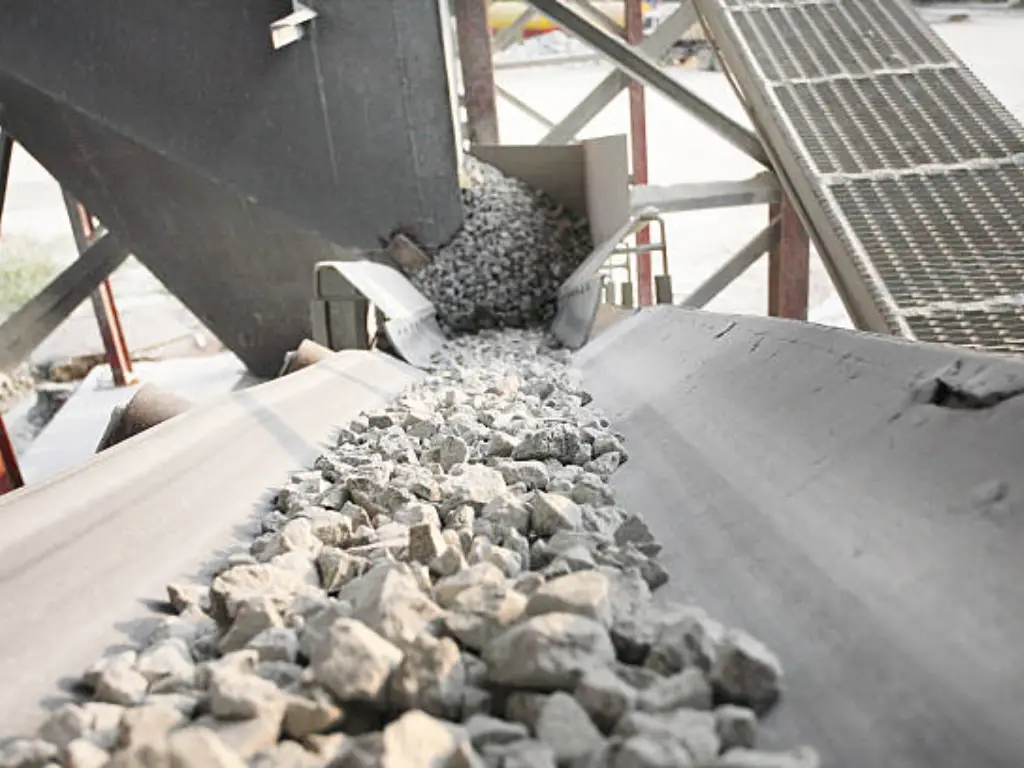
Comminution in mineral processing starts with the ore in a primary crusher where the material is reduced to smaller sizes through the application of mechanical forces. The size of the ore is an important aspect here as the bigger the ore the harder it is to crush. In the first stage, the ore is crushed into smaller size by the help of a jaw crusher or gyratory crusher, using both compression and impact forces. When crushing the ore, the feed rate and the size of the fragments that are obtained should be controlled. This means that the crushed material is fit for further milling by means of a ball mill, a sag mill, or a grinding mill, as well as a magnetic separation process.
After the ore has been crushed it goes to the next stage which is the second stage; this may involve the use of secondary crushers which reduce the size of the ore into fine particles. The stage is crucial for enhancing the efficiency of separation of the valuable minerals from the waste rock. Some crushers, such as the cone crushers supported at the bottom of the gyrating cone, are efficient in producing good sized product with maximum yield. Crushing has to be done according to the properties of the minerals, as each one may need a particular method to achieve the required size. For instance, while crushing soft ores, the equipment used may be durable, but when crushing harder ores, more durable equipment may be required to avoid frequent replacement of the machinery.
In dry conditions it is easier to achieve better results of the crushing process and this is particularly true when working with harder rocks. When the final product of the crusher is fine and the material fed to the next grinding stage is satisfactory, mining cost can be controlled and profitability can be achieved. This method is like making a sweet deal for a savings account which gives the maximum returns by investing the initial deposit (or ore) in a series of well calculated steps. In the end, knowledge of how crushing works and what tools to use, such as a grizzly screen for preliminary sorting, is useful for managing a mineral processing plant and improving the extraction of valuable materials.
What Factors Affect The Efficiency of Crushing Operations?
The efficiency of the crushing operation depends on the physiochemical characteristics of the ore, the type of crusher, and the operating parameters such as the feed size and the crushing rate. It was observed that the hardness of the material, its moisture content, and its fracture toughness would be determining factors that would decide how easily the material could be crushed.
Furthermore, the design and delivery of the crushing equipment also have significant impact on the efficiency of the crushing. Maintenance and replacement of worn out parts also diminishes the time that the machinery spends offline, thus increasing production.The other important consideration is the reduction ratio which is the ratio of the size of the feed material to the size of the crushed material. However, a high reduction ratio calls for higher energy consumption; therefore, it is possible to set a standard that will effectively meet the required particle size while not consuming a lot of energy. It is possible to monitor these parameters in real time using advanced control systems by which further improvements to the crushing process can be made.
Common Types of Crushers Used in Crushing in Mineral Processing

In the world of mineral processing, various types of crushers are employed, each designed for specific purposes and materials. Understanding these different types is crucial for selecting the appropriate equipment for a particular mineral processing application.
1.Hammer Crushers: These machines utilize high-speed rotating hammers to crush materials. They are effective for soft to medium-hard ores and can achieve significant size reduction, making them suitable for processing materials like coal, gypsum, and limestone.
2. Cone Crushers: Renowned for their efficiency, cone crushers are used primarily for secondary and tertiary crushing. They excel in producing uniform-sized products and are ideal for hard ores such as granite and basalt.
3. Jaw Crushers: These are typically used for primary crushing and are known for their ruggedness. They can handle a wide variety of materials, from soft clays to hard rock, making them a versatile choice for many mineral processing operations.
4. Impact Crushers: These machines are designed for producing high-quality aggregates. They use impact force to break apart materials and are often employed in the processing of softer ores like limestone and sandstone.
5. Roll Crushers: Utilizing two or more rotating cylinders, roll crushers are effective in reducing the size of larger materials. They are commonly used for materials like coal and salt, providing a uniform product size.
JXSC provides a comprehensive range of rock crushers for sale, designed to enhance efficiency and maximize ore recovery in mineral processing.For more details, visit rock crusher for sale.
Crushers in Specific Applications
Mining:
● Hammer Crushers (e.g., for gypsum and coal)
● Jaw Crushers (e.g., for primary crushing of hard rock)
● Cone Crushers (e.g., for granite and basalt)
Construction:
● Impact Crushers (e.g., for producing aggregates)
● Roll Crushers (e.g., for soft rock applications)
Recycling:
● Jaw Crushers (e.g., for concrete and asphalt)
● Impact Crushers (e.g., for glass and plastic materials)
Recent Innovations in Crushing Technology
The crushing technology field is very dynamic and new technologies are being developed for increasing efficiency and minimizing the negative impact on the environment. A rather remarkable development has been observed in automation and control systems. Today’s crushers are fitted with a variety of sensors and software that enable the monitoring of the process and changes in the feed material. This not only enhances performance but also minimizes energy use since equipment is made to work at their best.
The other area of innovation is in the choice of materials to be used in the construction of the crushers. Superior materials used in the manufacturing of the crushing components improve the durability of the crushing parts hence reducing the frequency of replacements. In addition, the use of digital technologies like predictive maintenance and remote monitoring enables the operators to prevent failure occurrences hence reducing the time that equipment takes to be out of order. These are important in the mineral processing industry so as to remain relevant in the market.
Conclusion
As we look to the future, the prospects for crushing in mineral processing are set to undergo a major revolution. The push to sustainability will remain a focal driver of research and innovation to generate new technological solutions that will help in minimisation of the impacts of mining. New inventions in energy-saving crushing equipment like electric and hybrid crushers will be widely applied when the industry aims to reduce its emissions.
At the same time, the introduction of artificial intelligence and machine learning will transform the organization of crushing processes. These technologies are capable of recognizing high volumes of data for different purposes, such as determining efficiency and predicting corresponding maintenance requirements. The industry continues to adopt these trends and any firm that has invested in these modern crushing technologies will not only improve on the quality and rates of the ore that they produce, but also stand to benefit from the future of the mineral processing industry.
Maximize Ore Recovery with JXSC Rock Crusher Machine
JXSC provides the best rock crusher machine for customers and aims to maximize the ore yield through performance. In the design of the rock crusher, new technology is incorporated in the crushing process to improve efficiency and improve the liberation of the minerals. Jaw crusher, impact crusher, cone crusher, and other equipment in the mineral processing factory, JXSC has a variety of types of crushers for sale. The original design of these machines is such that they can handle the rough nature of mining applications and at the same time, deliver steady performance.
The JXSC rock crushers are designed with high strength and heavy duty characteristics to serve various industries effectively. These are machines that are easy to use and have numerous safety features to minimize time loss and enhance efficiency. This has a jaw crusher for primary crushing, an impact crusher for the secondary stage, and a cone crusher for the tertiary stage of rock crushing. JXSC rock crushers offer you higher ore yield and better mining revenue.
FAQs
How does crushing impact ore quality?
Size reduction is a critical factor that defines the quality of the ore. When ore is crushed several factors come into play including size of large chunks of rock and the angle of the mantle. The kind of crushing method, either open circuit or closed circuit, influences the end result of the crusher product. In an open circuit, the large size particles may not be reduced to the right size thus making the ore quality to be inconsistent. On the other hand, closed circuit means that only particles of the desired size are allowed to pass through, hence enhancing a separation process. Moreover, the selection of steel balls and various minerals in the grinding mill will improve the liberation of value minerals, which will have a direct impact on the grade of the ore.
What are the environmental impacts of crushing in mining?
Crushing in mining operation can have severe effects on the environment. The process also produces dust and noise which are likely to cause harm to the birds and other animals within the locality and the neighbors respectively. The employment of humongous financial nerd machinery results in resource depletion and emissions. Furthermore, if excessive time is invested in wasteful procedures, then more energy is consumed, and carbon emissions are increased. Health costs and diseases concerning the respiratory system due to dust exposure can also be experienced in neighboring communities. Appropriate management and innovation offer a way out by encouraging proper handling of money in the industry through saving on expenses incurred in pollution control.
What is the difference between crushing and grinding in mineral processing?
Comminution as a process is central to most operations in mineral processing although crushing and grinding are two distinct operations with different objectives. The first step is crushing where large rocks are reduced to smaller size by means of crushers. These processes may use different methods, for instance, the flat cone angles used in gyrating cone crushers affect the bottom of the gyrating cone’s performance in breaking the ores. Crushing is followed by milling, which further breaks down the particles to liberate minerals from the waste rock, in a mill that uses steel balls. Crushing is concerned with the reduction of the size of the ore, while grinding is concerned with the liberation of the minerals in question, which in turn influences the efficiency of the separation process as well as the recovery rate of the minerals. Knowledge of the best option for each stage is crucial, especially for operators with bad credit or those that require a debt relief program to finance improvements.