- Home
- Blog
- Equipment Info
- Crusher Parts Guide: Types, Selection, and Maintenance Tips
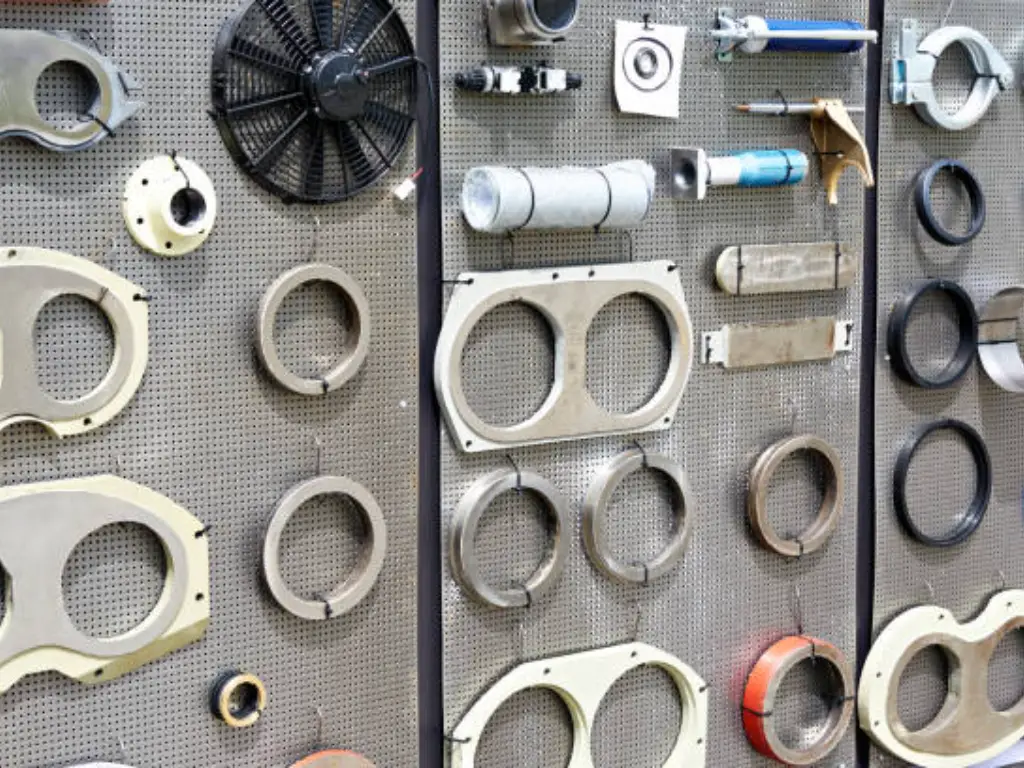
Why Crusher Parts Are Crucial for Mining & Aggregate
The harsh needs of the aggregates sector and mining activity put a lot of strain on machinery, especially the incredibly robust and servant-like crucial which is a crusher. Stone crusher machines are colossal machines that float the idea of preposterously shrinking huge boulders and ores to much more reasonable shapes. Crude as it may seem, these tough skins of metal continuously augment and maintain the production line to function at full throttle. But, as strong as a crusher is, it cannot function effectively without its multitude of constituent parts known as the crusher parts. Understanding quite the paradox of a puzzle, each part is critical to the main system. If any of the parts fail, whether it is through unfortunate failure or wear and tear of perpetual movement, the system at whole comes to a cease. Those standstill periods are pure unproductiveness which means if calculated, there are finances lost.
Hence, emphasizing the meaning of a crusher part cannot be mere an abstract thought exercise. It is rather an urgent need in making sure that there has to always be some level of efficiency, minimizing costly delays, and allowing golden profits to come from mining, quarrying, construction aggregate production, and also recycling efforts. The search for parts conducted process through procurement or performance enhancement is something that can either amplify business or diminish it, hence grave thought must be provided to this.
Types of Crusher Parts: Wear Parts vs. Spare Parts
Despite appearing to be a maze of metals, alloys, and crushing tools, the world of crusher parts can be simplified to two basic categories: wear parts and spare parts. Knowing the difference between these categories is important for proper maintenance and stock control.
Wear Parts
The heroes of the crushing process are the expendable parts which have been created to take impact of the machine’s processes. Their task is to face the crushing processes abrasive and impact forces. Imagine them as equipping tires to a vehicle- tires which are meant to get worn and need replacing through use. For cone crushers, the key wear parts are the mantle (which is the moving crushing part) and the stationary crushing surface, which are the concave in the form of cone liners. In the jaw crushers, the foremost wear parts are the jaw plates (both movable and stationary) with the rib or side wall of the jaw which is a covering the frame of the crusher. In the impact crushers, the blow bars (parts which inflict the impact load on a body) and impact plates or hoppers against which the material is smashed are the most often used parts that wear. To give maximum life, these parts are made out of hardened materials such as manganese steel or impregnated alloys. Their replacement is however, invariable in the ordinary course of working of a crusher. Availability of these parts is essential.
Spare Parts
This expansive category includes everything else that may need to be replaced because it is broken, damaged, or needs upgrading. Wear parts are expected to go through frequent replacements while spare parts have a longer life, but they are equally as important in order to avoid downtime.
Spare parts for cone crushers may have the main shaft, eccentric, misaligned bearings, gears, and hydraulic cylinders. Jaw crushers may have parts like the toggle plate, toggle seat, bearings, and springs. Impact crushers spares might be the rotor, bearings, liners that do not contact with the materials, and hydraulic systems.
It smoothens repairs and keeps everything running as it should without worsening problems. This increases the wear life of the entire crushing equipment and prevents production halts.
Understanding Different Crusher Types and Their Components
It is essential to have a basic knowledge of various types of crushers and their primary parts to choose and manage the right crusher parts effectively. In the mining and aggregate industry, the most common are cone, jaw and impact crushers. Each has its own crushing action and thus needs its own specific parts. For primary crushing of big quantities, there is also a type of gyratory crusher.
Cone Crushers: Crushers of this type work by crushing a piece of material between a rotating mantle (inner cone) and a stationary concave (outer cone). The space between two surfaces shrinks as the material is being lowered, which makes it break.
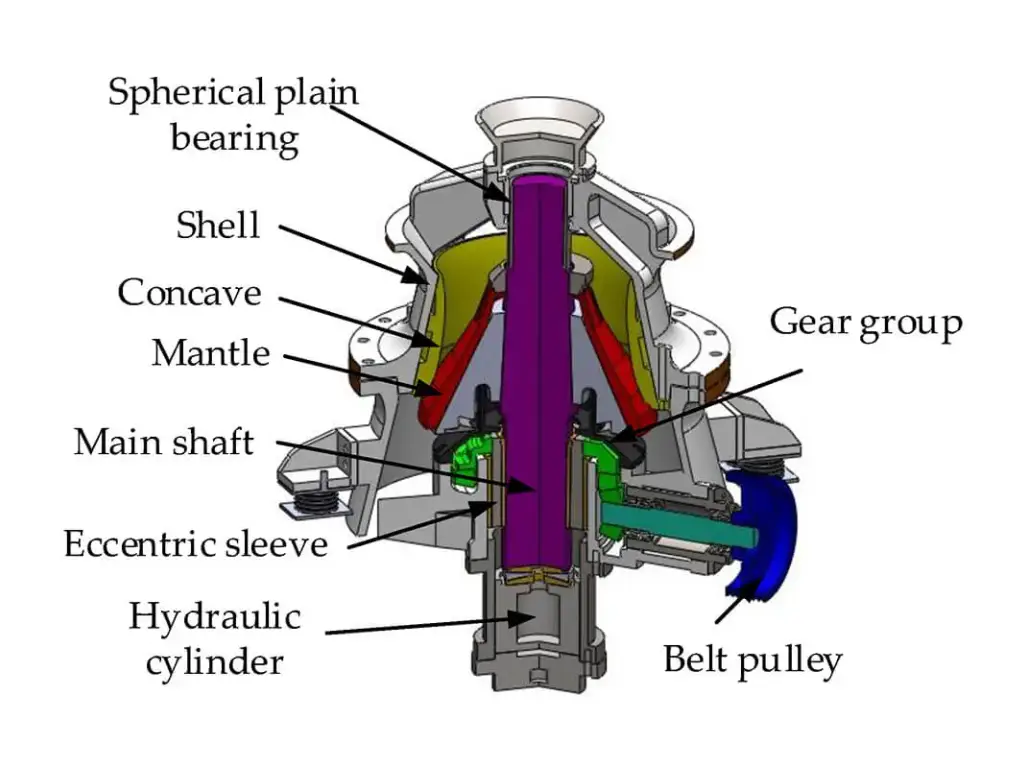
Key cone crusher parts name include:
● Frame: The main structural support of the crusher.
● Main Shaft: A vertical shaft that supports the mantle.
● Eccentric: A rotating component that causes the mantle to gyrate within the concave.
● Mantle: The inner, moving crushing cone.
● Concave (Cone Liners): The outer, stationary crushing cone.
● Head: The upper part of the mantle assembly.
● Adjustment Ring: Used to adjust the gap between the mantle and concave, controlling the output size.
● Hydraulic Cylinders: Often used for overload protection and adjustment.
Jaw Crushers: A jaw crusher uses compressive force to break down material. A jaw stone crusher consists of two crushing surfaces: a stationary jaw plate and a movable jaw plate. The movable jaw plate articulates back and forth relative to the fixed jaw plate, compressing and breaking the material.
Key jaw crusher parts names include:
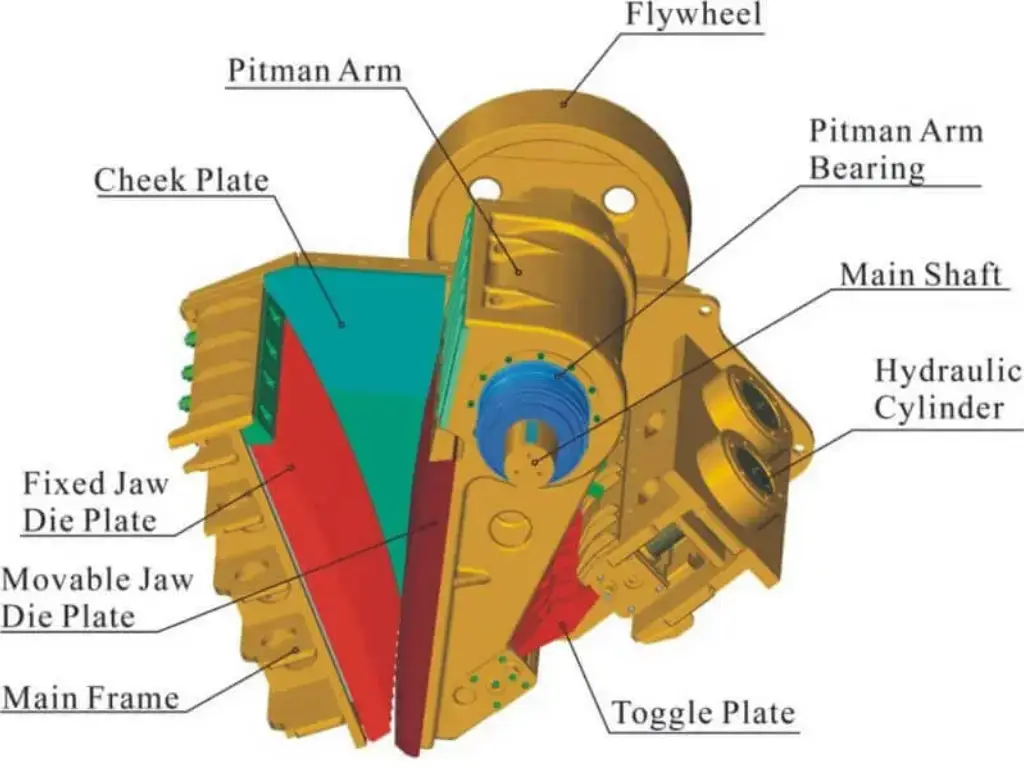
Key jaw crusher parts names include:
● Frame: The robust structure housing the crushing mechanism.
● Fixed Jaw Plate: A stationary crushing surface.
● Movable Jaw Plate: A crushing surface that moves back and forth.
● Eccentric Shaft: Drives the movement of the movable jaw plate.
● Pitman: Connects the eccentric shaft to the movable jaw plate.
● Toggle Plate: A safety mechanism that allows the movable jaw to swing away if uncrushable material enters.
● Cheek Plates: Protect the sides of the crushing chamber from wear.
Impact Crushers: Maximum crushing forces are achieved through the use of impact and impactors. Feed material is broken down using blow bars that quickly rotate and hit the surface. They are then smashed into blade-like plates which are stationary and set in place.
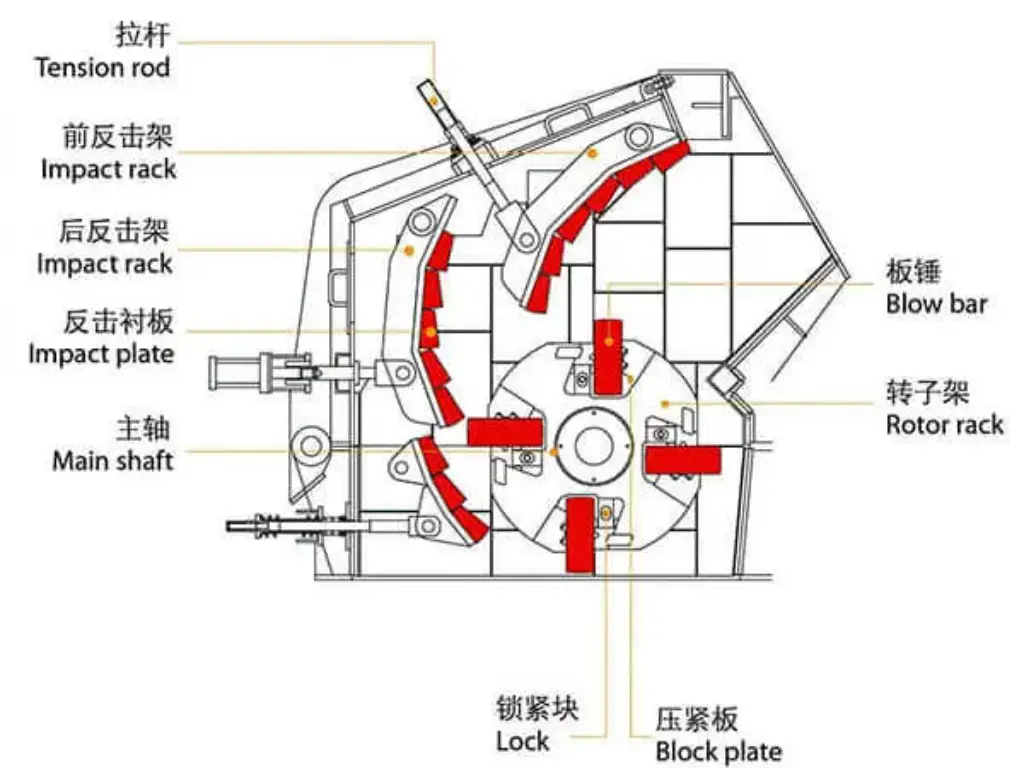
Key components include:
● Frame: The main support structure.
● Rotor: A rotating assembly that holds the blow bars.
● Blow Bars: The impacting elements that strike the material.
● Impact Plates (Aprons): Stationary surfaces against which the material is thrown.
● Liner Plates: Protect the internal walls of the crusher from wear.
Adjustable Components: Mechanisms to adjust the gap between the blow bars and impact plates, controlling product size.
Knowing how other components of the machine work together is essential when searching for appropriate replacement parts for maintenance and repairs.
Selecting & Optimizing Crusher Parts for Specific Applications
Selecting and optimizing the parts of the crusher is not a simple task. The selection changes with the application, especially with the material’s type and their hardness level. For example, the wearing is different between crushing softer materials such as limestone versus using highly abrasive and hard ores like granite or quartzite.
Choosing the wear parts becomes challenging with high hardness ore if optimal performance of the crusher is still to be nullified. Standard manganese steel tends to wear rapidly, which leads to constant replacements and increasing downtime. In such scenarios, the use of high-chromium cast iron advanced alloys components with ceramic inserts or proprietary alloys can prove beneficial as they significantly enhance the wear life of the components, which in turn reduces the cost per tonne of material. The design and geometry of the parts is of utmost importance too.
For example, a cone crusher mantle with a steeper angle of the cone might be more effective in finer crushing than coarser reduction. A broader angle is more optimal for coarser reduction. Different tooth profiles of jaw crusher plates can also be designed to have stronger holds for the material and better jaw crushing throughput. The choice of the wear parts of a crusher dictates its efficiency.
Here’s a table illustrating the relationship between ore type and potential crusher types:
Ore Type | Hardness (Mohs Scale) | Suitable Crusher Types | Considerations for Parts |
---|---|---|---|
Limestone | 3-4 | Jaw Crusher (primary), Impact Crusher (secondary), Cone Crusher (tertiary) | Standard manganese steel wear parts may suffice. Focus on throughput and efficient crushing chamber design. |
Granite | 6-7 | Jaw Crusher (primary), Cone Crusher (secondary/tertiary), Gyratory Crusher (primary) | Requires higher manganese content or specialized alloys for wear parts. Consider robust spare parts for higher stress. |
Quartzite | 7 | Jaw Crusher (primary), Cone Crusher (secondary/tertiary) | Demands premium wear-resistant materials like high-chromium iron or ceramic inserts. Regular maintenance and inspection are crucial for longer wear life. Consider epoxy crusher backing for added support. |
Copper Ore | 3-4 (varying) | Jaw Crusher (primary), Cone Crusher (secondary/tertiary), Impact Crusher (depending on type) | Material abrasiveness can vary. Select wear parts based on specific ore characteristics. Consider flotation requirements downstream when choosing crusher types. |
Gold Ore | 2.5-3 (free milling) to 7 (refractory) | Jaw Crusher (primary), Cone Crusher (secondary/tertiary), Impact Crusher (depending on type) | Similar to copper ore, abrasiveness varies. Consider the downstream gold recovery process when selecting crusher types and ensuring minimal contamination. The choice of liner material can be important. |
Optimize Your Crushing with JXSC Mineral Processing Equipment.

Founded in 1985, JXSC takes advantage of its decades of experience with mineral processing. Our primary area of proficiency is in the separation of minerals during all stages of mining, but we also have an impressive rock crushing technology base which is demonstrated through our powerful and durable rock crushing machine. Our two modern factories covering an area of thirty thousand square meters have sophisticated manufacturing facilities and are staffed with professionals who are committed to producing high-quality crushing equipment for sale.
Here at JXSC, we know that even before you can think of getting any results, the most important decision that you may want to deal with is selecting the best crusher. This becomes a necessity when dealing with very tough materials like high-hardness ore. Throughout the years, our highly experienced technical team has mitigated the years of product feedback from customers and continuous product enhancements to enable them to offer crushing appliances built for tough applications. The evolution of our cone crushers, from single to multi-cylinder hydraulic cones, exemplifies this commitment. Likewise, the shift from manual jaw opening to hydraulic jaw opening is a demonstration of focus on user-friendliness and automation. As a result, the superior engineering in these products guarantees the best wear parts and equipment life.
At JXSC, you can choose reliable crushing solutions, such as crushers that contain premium electrical motors with reducers, steel plates, and wear-resistant linings. Our years of dedicated endeavor have given us the insight to find the best technological solutions for problems related to crushing processes.
Crusher Parts Manufacturers and Suppliers Information
Choosing a reliable manufacturer or supplier is critical for assuring quality. With regards to Sourcing Crusher Parts, suppliers of all parts, components and subsystems offered for sale by a vendor need to be dependable. Here are a few prominent players in the industry, offering a wide range of replacement parts:
Superior Industries
● Recommendation Rating: ☆☆☆☆
● Headquarters: Morris, Minnesota, USA
● Key Products: A comprehensive range of crushing equipment and crusher parts, including jaw crushers, cone crushers, horizontal shaft impactors (HSI), vertical shaft impactors (VSI), and their respective wear parts and spare parts. They also offer conveying, screening, and washing equipment.
Specific Description:
Specialized in rock facing and load out, Superior Industries strives to supply the complete solution. This enables them to manufacture their parts inhouse to superior mines standards thus a precise fit is a guarantee. Their consistent stocking of parts minimizes downtime and is a great benefit to customers. Their product line caters to various industries, including agriculture, mining, aggregates, and many more.
Metso
● Recommendation Rating: ☆☆☆☆☆
● Headquarters: Espoo, Finland
● Key Products: A global leader in providing technologies and services for the mining, aggregates, and flow control industries. Their crusher parts portfolio covers a wide range of equipment, including cone crushers (like the Nordberg and Symons series), jaw crushers, and impact crushers. They offer both oem parts and aftermarket solutions. They are known for their major cone crusher models support.
Specific Description:
Metso is well known for their high quality wear parts and spare parts assembled with advanced alloys to increase their life span under extreme operating conditions. Metso also optimizes the efficiency and safety of their product by providing wear part lifting tools and chamber optimization services. Available locally for many people, their global support assures everybody will get service. Local search may return satisfying results depending on your current position.
Cutting Edge Supply
● Recommendation Rating: ☆☆☆
● Headquarters: Temescal Valley, California, USA
● Key Products: Primarily focused on providing aftermarket crusher wear parts for various brands and models of crushers. Their offerings include mantles, concaves, jaw plates, blow bars, and more, often with a focus on longer wear life.
Specific Description:
Cutting Edge Supply is a family-owned independent company that specializes in high quality wear parts, wear enhancement products, and full service repair work for heavy machinery.
The firm serves some of the most important industries today such as mining, construction, material handling, agriculture, as well as waste management and recycling. Cutting Edge Supply has earned a reputation as a principal supplier of ground engaging tools, crushing wear parts, screening media and custom specialty abrasion resistant and high strength steels. In addition, they provide professional hard chrome plating services along with custom and remanufactured pins and hydraulic cylinder repairs. These services, along with their numerous welding services which include bucket repairs, liner installation, and many others, make them the leaders in the industry.
Extend Crusher Parts Life: Operation & Maintenance Tips.
To make sure you limit costs and improve operational efficiency, you must work towards prolonging the wear life of your crusher parts. Ensuring effective operation and maintenance practices can go a long way in prolonging the life span of these essential parts. Provided below are a few tips to get you started:
● Ensure Proper Feeding: Do not overload the machine or the materials as this will increase the wear and tear on the system. Instead, maintain consistent feed rate throughout the operation.
● Regular Inspections: Make sure you put in place a plan for regular inspections on all the parts of the machine. Watch out for signs of wear and tear such as thining cracks and shift deformation. If wear and tear is caught early, it can be managed in a resolution before it grows too damaging.
● Correct Lubrication: Guarantee that there is proper lubrication as this will decrease friction on moving parts within the machine. Always check and make sure intervals are met as suggested by the manufacturer.
● Tighten Fasteners: You need to also check and tightem all fasterners and bolts. Failing to do so can lead to extreme vibrations leading to wear from unintentional adjustments.
● Monitor Operating Parameters: It is important to take note of the temperature, vibration levels and current for the motor. Paying attention to major changes in these can aid in trouble shooting problems relating to parts or the machine itself.
● Implement a Preventative Maintenance Schedule: Maintenance scheduling Servicing and replacement of certain wear parts must be done in regular intervals relative to the usage of the machine. Consider applying an epoxy crusher backing if there are certain liners that need support.
● Train Operators and Maintenance Personnel: Anyone operating or maintaining the plant must be adequately versed on how to properly operate and maintain the delicate parts.
● Use Quality Parts: It is true that price may come into play, but when considering the long term performance of the crusher, the reputable manufacturers’ parts will always outperform others and cost less in the end. Steel foundries do not always include the required quantity of manganese and that may affect the parts’ durability.
Following these operational and maintenance practices will help increase the lifespan of your crusher parts whilst saving the aggregate industry money through reduced replacements.
Conclusion: Key Takeaways for Crusher Parts.
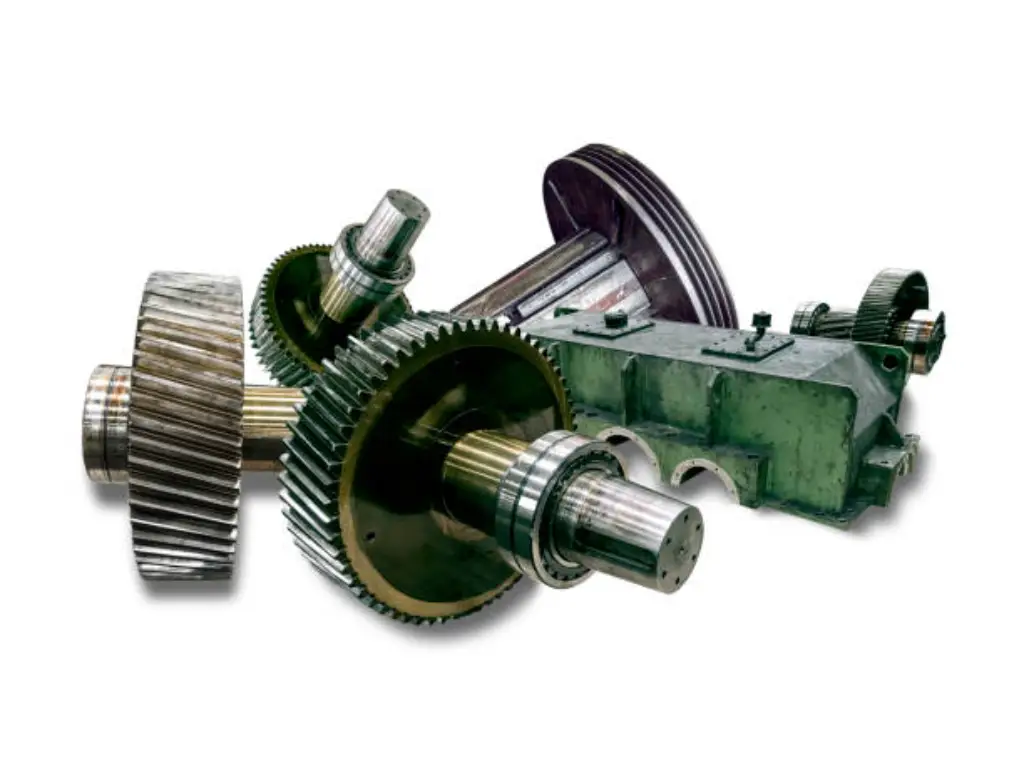
Parts of the crushers operate as the important organs of the crushing process as they determine efficiency, productivity, and operational costs in the mining and aggregate industries. Differentiating and understanding the definition and characteristics of wear parts versus spare parts, as well as the various elements that make up the different types of crushers, are essential for effective maintenance and management.
Correctly identifying and selecting the appropriate crusher wear parts for the specific application, especially in the case of difficult materials, is critical to maximizing the operational performance of the crusher and minimizing overall wear. Serious manufacturers and suppliers guarantee quality components, which is vital for many companies.
Finally, efforts on maintenance and proper operation procedures should not be neglected since they are important for increasing the wear life of such parts and using the returns on investments that have been put into the crushing equipment. When careful attention and knowledge is given towards the logic and care of crusher parts, the success and lifespan of the operation is increased.