- Home
- Blog
- Mineral Solution
- What is the Copper Mining Process? A Step-by-Step Overview
- mmldigi
What is Copper?
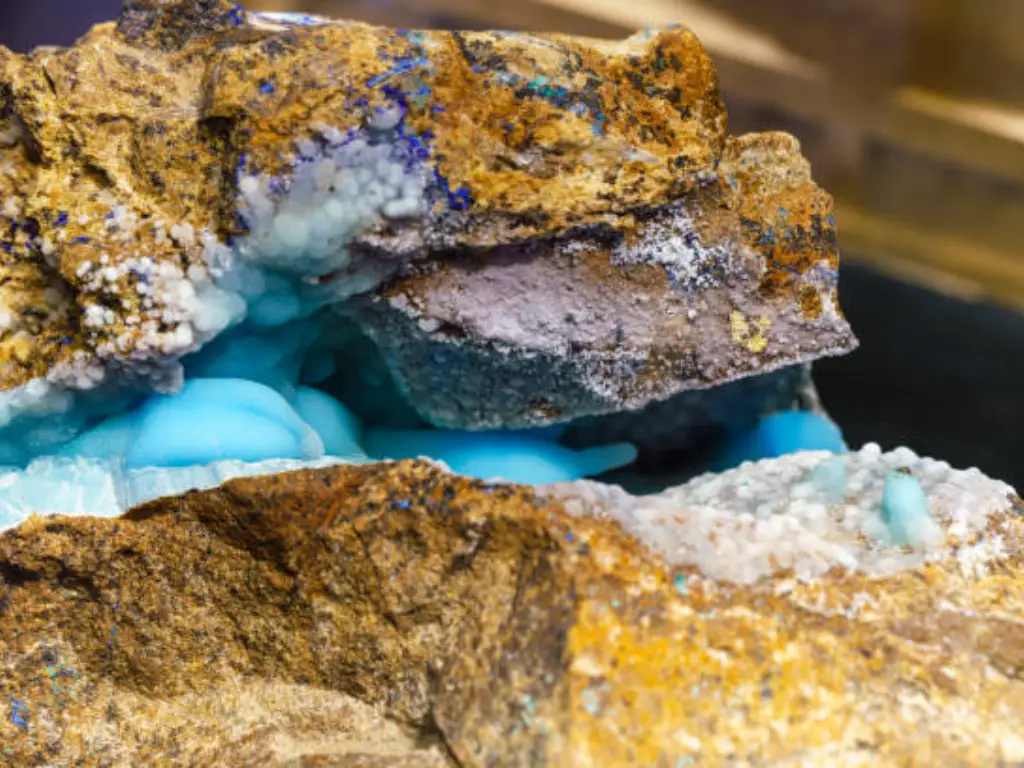
Copper (cu) is a reddish-brown metal that has been a vital part of human society since the beginning of the Copper Age. Being one of the best conductors of electricity and heat, copper is widely used in electrical and plumbing industries, electronics, and automotive industries. It also does not corrode easily and can be alloyed with other metals to form even more useful materials like bronze and brass.
Copper in its metallic form is not usually found in nature in its free state. However, it is found as a component of different mineral ores that require mining and refining to obtain the copper value. These ores are dissimilar in their mineral content and need different methods of mining and processing to extract copper effectively. It is important to understand these differences in order to improve the process of copper mining.
Different Types of Copper Ore
Factor | Chemical Formula | Description |
---|---|---|
Chalcocite | Cu2S | Chalcocite is a dark gray to black mineral with a metallic luster, and it is one of the most important copper ores due to its high copper content. |
Chalcopyrite | CuFeS2 | Chalcopyrite is a brassy-yellow mineral with a metallic luster and is the most abundant copper-bearing mineral. |
Bornite | Cu5FeS4 | Bornite, also known as peacock ore, is a copper iron sulfide mineral that tarnishes to various iridescent shades of blue to purple. |
Malachite | Cu2CO3(OH)2 | Malachite is a green copper carbonate hydroxide mineral often found in botryoidal, fibrous, or stalactitic masses. |
Azurite | Cu3(CO3)2(OH)2 | Azurite is a deep blue copper carbonate hydroxide mineral known for its vibrant color and is often found with malachite. |
Cuprite | Cu2O | Cuprite is a red to dark brown copper oxide mineral with a metallic to sub-metallic luster, often found as an oxidation product of copper sulfides. |
Covellite | CuS | Covellite is a deep indigo blue copper sulfide mineral with a metallic luster, usually found in the oxidation zones of copper deposits. |
What is copper used for?
Copper metal is widely used in today’s industries because of its conductivity, strength and flexibility. It is used in electrical sector in electrical wiring, cables and motors, in construction for pipes, roofing materials and radiators and in industrial sectors for machine parts, heat sinks and electroplating which makes it essential in the modern world.
Comparing Open-Pit and Underground Mining Techniques
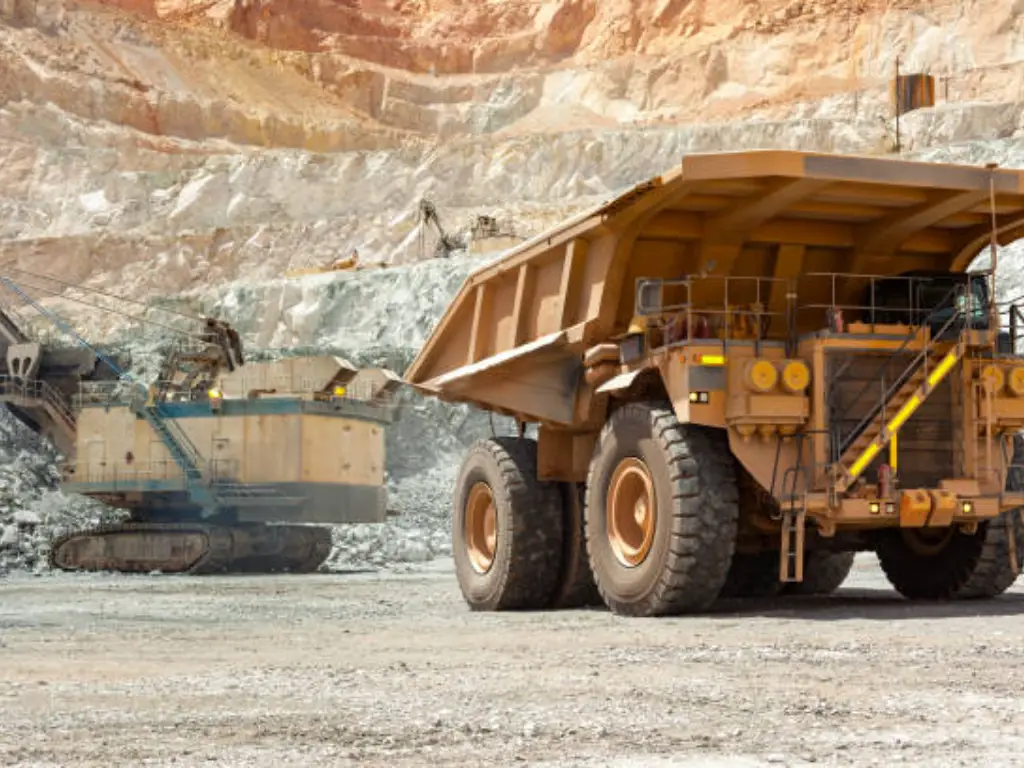
Open-Pit Mining is the preferred method when copper deposits are located near the surface. This method involves the removal of large amounts of overburden (soil and rock covering the ore) to access the copper ore beneath. Open-pit mining is advantageous because it allows for the extraction of large volumes of ore, making it suitable for low-grade copper deposits. The process is highly efficient but has a significant environmental impact due to the extensive land disturbance and the creation of large, open pits that can be challenging to rehabilitate after mining operations cease.
Underground Mining, on the other hand, is employed when copper deposits are located deep below the Earth’s surface. This method involves creating a network of tunnels and shafts to reach and extract the ore. While underground mining is more expensive and complex than open-pit mining, it is more suitable for high-grade ores found at greater depths. It also has a smaller surface footprint, reducing the immediate environmental impact. However, underground mining poses higher risks to workers and requires more advanced technology and safety measures.
What is Copper Mining Process?
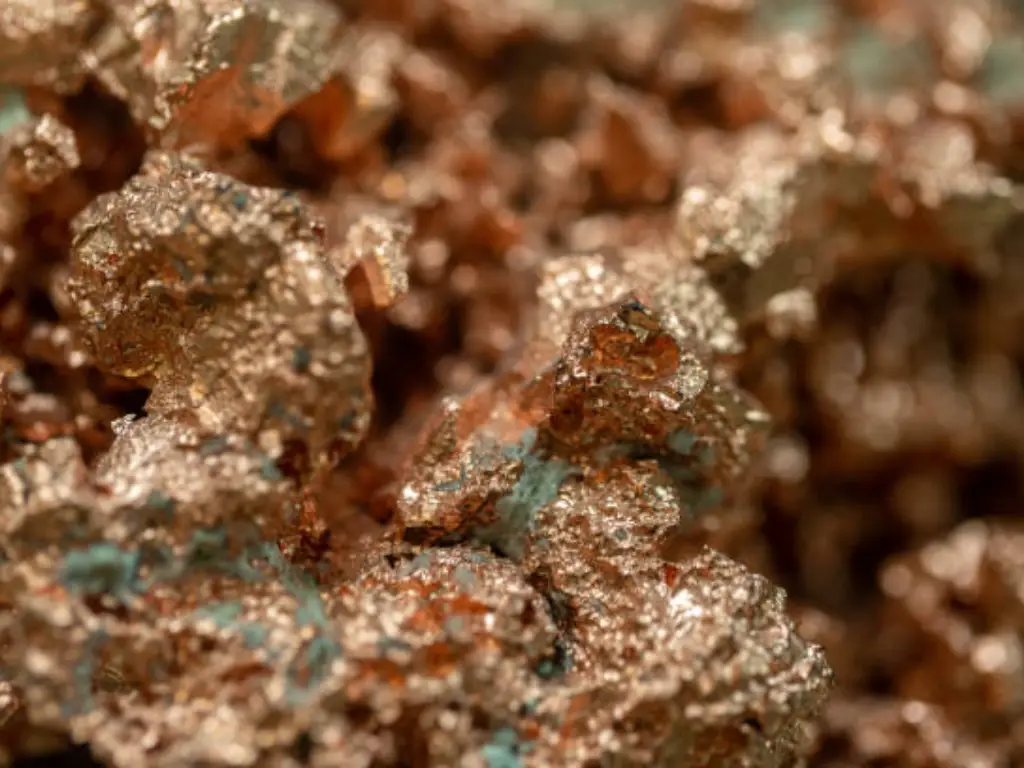
The process of mining copper is carried out through several important stages that help in converting copper ore into metallic copper that can be used.
● Exploration and Geological Survey: The initial processes in copper production are exploration and geological studies. Seismic surveys, satellite imagery, and drilling rigs are some of the tools that geologists employ in the search for copper deposits. These surveys assist in identifying copper minerals in areas such as North and South America, especially in countries such as Chile. The United States Geological Survey can be a great source of information for these explorations. Computerized techniques such as geophysical surveys with ground penetrating radar and geochemical sampling are used to assess the size and grade of the ore bodies. This stage is important in defining the feasibility of mining projects and laying down the framework for optimal copper recovery.
● Ore Extraction: Ore extraction entails getting to the copper bearing materials which are identified during the geological exploration. In areas such as North America this is achieved through underground mining where the miners employ the use of drills and blasting agents to break the rock. The crushed ore is then conveyed to the surface for further treatment. This process involves planning to avoid risks that may harm the workers and the environment.
● Blasting and Drilling: Blasting and drilling are crucial for the purpose of fragmenting large amounts of rock in order to liberate copper minerals. Explosives are placed in holes made by drills that are fitted with diamond or carbide bits. These explosives when exploded cause the rock to break into smaller pieces and hence facilitate movement of the ore to the surface. This method is commonly applied in copper mines in Chile and other mining countries. This process affects the production rate, which makes it an essential factor in the copper industry.
● Crushing and Grinding: Once the ore has been extracted, it is then crushed and ground into a fine powder to make the rock easier to work with. Jaw crushers and cone crushers are used to reduce the size of the ore to smaller sizes and then the material is further crushed by ball mills. This process makes the copper minerals float to the surface of the water and form a slurry of copper particles that can be processed. The crushed ore is now ready for concentration, which will further enhance the percentage of copper before smelting.
● Concentration: Concentration is the process of making the copper content of the ore higher through froth flotation. In this process, the ground ore is mixed with water and reagents in flotation cells and air bubbles are also floated. The copper minerals attach themselves to the bubbles and float on the surface of the solution to form a froth layer which is skimmed off. This leads to the production of copper concentrate, which is a valuable product that mainly consists of copper minerals and other materials. The efficiency of this step is very crucial for the subsequent stages of copper production because it determines the quality of the copper concentrate.
● Leaching: Leaching is used for oxide ores especially copper oxide ores and heap leaching where the ore is stacked into heaps and then sprayed with a leaching solution. This solution, which may contain sulfuric acid, drips through the heap and dissolves the copper oxide minerals. The copper rich solution that is formed is then collected and subjected to further processing to obtain copper. This method is best suited for low grade ores and is used in majority of the copper mines in South America. Leaching is one of the most efficient and cheap methods of extracting copper from copper oxide ores and has greatly boosted the production of copper.
● Smelting: Smelting is the process of heating the copper concentrate in a furnace to obtain molten matte which is a mixture of copper, iron and sulfur. This process involves the oxidation of the metal and helps to remove the impurities from it. The furnace, which may be a flash smelter or a blast furnace, is at high temperatures and the copper minerals melt and form a dense liquid. The molten matte, which contains about 60-70% copper, is then tapped from the furnace and is taken to the converter for further purification. This step is crucial for converting the copper concentrate to a higher purity of copper called blister copper.
● Converting: During the converting process, the molten matte is blown with air or oxygen in a converter furnace. This oxidizes the sulfur and iron and forms blister copper which is about 98-99% pure copper. The converter purifies the product by eliminating the unwanted components from it. This process includes several steps of heating and chemical processes, during which the molten copper is changing its properties until it becomes sufficiently pure. The employment of converter furnaces is common in the copper industry to guarantee quality copper production.
● Electrorefining: Electrorefining is the process of purifying blister copper through the process of electrolysis. In this process, blister copper is the anode and pure copper sheets are the cathode in an electrolytic cell. An electric current is passed through the cell and the copper ions move from the anode to the cathode and form high purity copper cathodes. This method gives copper with a purity of 99%. 99% pure, good for electrical uses because of its high conductivity. The electrorefining stage is important in obtaining copper of very high quality that is required in the copper industry.
● Copper Casting and Production: Copper casting and production include forming the copper into different shapes. The copper cathodes that are obtained from electrorefining are then remelted in a furnace and rolled into billets, rods or any other form that may be required. These forms are applied in the production of items like electrical wires, water pipes, and copper alloys. The production of copper in these forms benefits many industries, thus proving that copper is a good conductor of electricity and can be used in many ways. This final stage helps to prepare copper for the market and for use in industries.
● Waste Management and Tailings Disposal: Environmental concerns such as waste management and tailing disposal are important in the production of copper. Ore processing waste products are called tailings and they are usually disposed in tailings dams or ponds. These facilities are intended to store the waste safely so that it does not pollute the soil and water. The use of modern technology and the implementation of laws and policies make waste management environmentally friendly and secure. The management and treatment of the tailings are critical to the sustainability of copper mining operations and to guarantee that the benefits derived from copper production are not at the cost of the environment.
JXSC provides various mining machines to meet the requirements of each stage of copper mining, including crushing, grinding, flotation, and dewatering, to help customers achieve efficient mining.
Regulatory and Environmental Compliance in Copper Mining
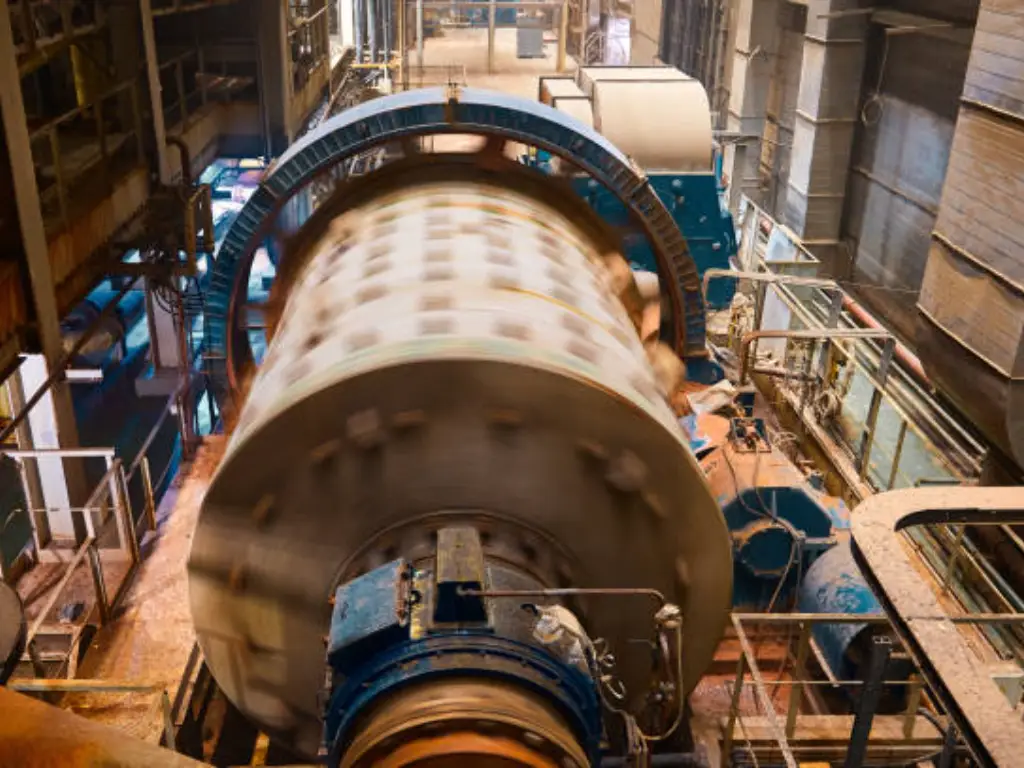
Like any other mining activity, copper mining is regulated by laws that aim at reducing the effects of mining on the environment and promoting sustainability. In countries such as the United States, the Environmental Protection Agency (EPA) has a major responsibility of implementing the regulations that mining companies are supposed to adhere to. These regulations include air and water quality standards, waste disposal, and land reclamation among others.
Any copper mining activity that is to be undertaken has to be done under the approval of the necessary permits and after compliance with the environmental impact assessments. These assessments assist in determining the possible risks that may be faced in the environment and the ways of avoiding them. It is not only a legal requirement but also a necessity to adhere to these regulations in order to sustain a company’s social license to operate. It is mandatory for the companies to adopt measures that will help in the conservation of water and energy, recycling of wastes and prevention of pollution. The above standards have also been made easier by the advancement in technology, thus making it possible for mining companies to mine for copper in a responsible and sustainable manner.
Technological Innovations in the Copper Mining Process
The copper mining industry has experienced technological changes that have impacted on the productivity, safety and environmental impact of mining. Among the most revolutionary changes, it is possible to highlight the use of solvent extraction and electrowinning (SX-EW). This method is especially applied for the processing of low-grade copper ores and consists in the extraction of copper ions from leach solutions by means of solvents. These ions are then electroplated onto cathodes to obtain pure copper from the copper sulfate solution. The SX-EW process is more efficient and less hazardous to the environment than the conventional smelting method and is widely used in the current copper mining industry.
Technology has also been adopted in the copper mining process through automation and digitalization.
Technologies such as remote sensing, drones, and big data analysis help to increase the efficiency of exploration and monitoring of mining areas. Machines replace human labor, which is more efficient and safe for workers and the company. Also, the use of solar and wind energy in mining activities has been effective in decreasing the emission of greenhouse gases in the mining sector. These technologies are essential for the advancement of copper mining to meet the growing demand while at the same time reducing the effects on the environment.
Conclusion
Copper mining and processing is a complex process that involves the use of several pieces of equipment and processes. All the steps are important and have a direct impact on the quality and quantity of the copper produced. The optimization of copper mining and processing can be realized by scientific and reasonable mine design and the application of modern equipment.
Begin Profitable Gold Mining with JXSC
JXSC Mine Machinery Factory is one of the leading manufacturers of copper mining equipment in China, providing the best solution for every stage of copper mining. JXSC has been focusing on the production of copper ore processing equipment for more than 35 years, and JXSC can guarantee that the equipment will help you achieve efficient processing from the crushing and grinding stage to the concentration and refining stage.
JXSC’s product range is jaw crushers, ball mills, flotation machines, and gravity separators that are designed for high performance and durability. JXSC’s advanced technology and fast production cycles also contribute to the reduction of operating expenses, thereby making your copper processing plant efficient. No matter if you are dealing with sulfide ores, oxide ores, or native copper, JXSC develops its solutions based on your requirements to increase the recovery rate and production performance.
FAQs
How long does the copper mining process take?
The time taken to complete the copper mining process may take as short as a few years or as long as several decades depending on the size and depth of the copper deposit, the type of mining techniques used and the effectiveness of the processing plants. Usually, it may take several years from the exploration stage to the production of pure copper from copper ore.
What are the environmental impacts of the copper mining process?
The effects of copper mining include; alteration of land use, water pollution, and emission of greenhouse gases. However, the effects of these activities are managed through modern regulations and technologies in sustainable practices and environmental management.
How much copper is typically extracted from copper ore?
The quantity of copper produced from copper ore depends on the quality of the ore and the effectiveness of the extraction method. Copper ores contain between 1-3% copper, so 100 tonnes of the ore may yield between 1-3 tonnes of copper.