- Home
- Blog
- Mineral Solution
- The Complete Copper Extraction Process Explained
History and Evolution of the Copper Extraction Process
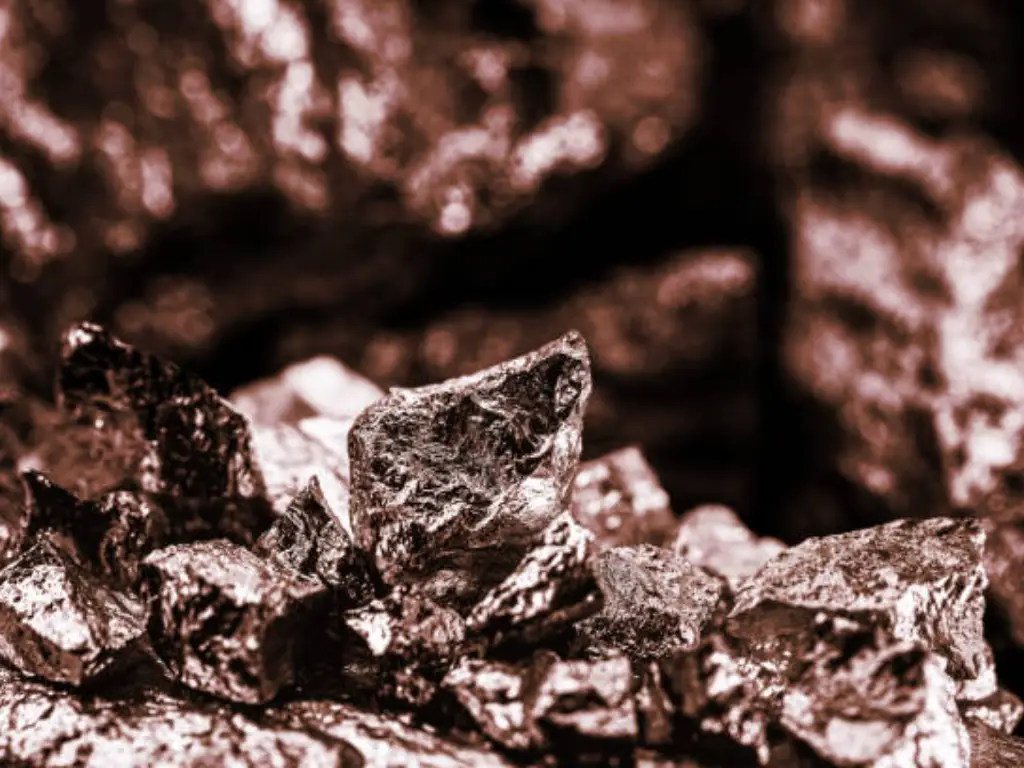
Copper extraction has been in existence since prehistoric period, with the earliest signs of extraction being recorded in the Middle East around 6000 BCE. The ancient Egyptians and Sumerians for example used copper to make tools, weapons and ornaments because of its ductility and its ability to resist corrosion. The techniques used in these early ages were crude and involved a lot of handwork and basic processes of smelting. In the Copper Age, the availability of large copper deposits in areas such as North America allowed for the creation of significant quantities of copper metal, leading to the production of copper for various electrical requirements in today’s world.
In the course of the centuries, the process of copper extraction has been developed and improved. The Industrial Revolution was a turning point as new and better equipment and methods were developed such as froth flotation that enhanced efficiency and productivity. Froth flotation was used in concentrating copper from a variety of minerals by taking advantage of the differences in the nature of the mineral surface of the ore. In the 20th century, new technologies like solvent extraction and electrowinning (SX/EW) made it possible to process low-grade copper ores, including copper oxide ores. Heap leaching also emerged as a significant technique for processing such ores, where the ore is crushed and placed in heaps, and a leaching solution is used to dissolve the copper. Modern copper industry uses highly efficient technologies that are focused on the use of resources, which indicates the development of technologies and the need for copper in various sectors of the economy.
Types of Copper Ores
Types | Dsecription | Extraction Methods |
---|---|---|
Sulfide Ores | Contain copper combined with sulfur, typically found deep underground. | Extracted using flotation, followed by smelting and converting. |
Oxide Ores | Contain copper combined with oxygen, found closer to the earth's surface. | Extracted using hydrometallurgy, including leaching and SX/EW. |
Mixed Ores | Contain both sulfide and oxide minerals. | Require a combination of both flotation and hydrometallurgical methods. |
Steps in Copper Extraction Process
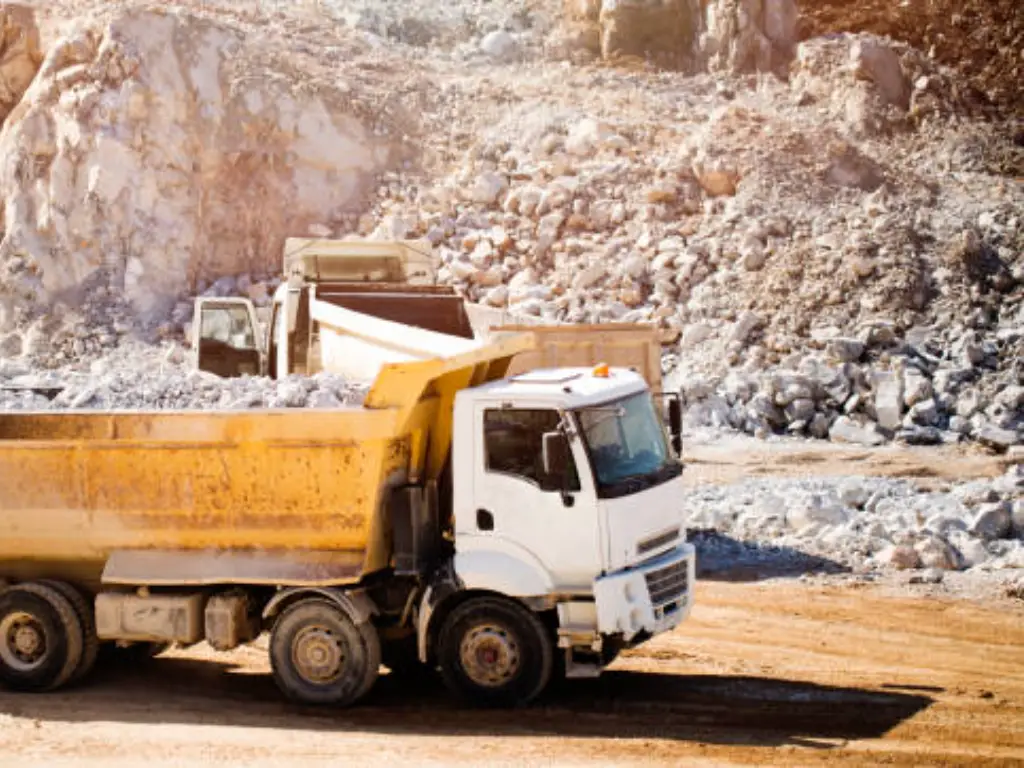
Ore Ming
Copper mining is normally done through open-pit or underground mining techniques. In North and South America, copper sulfide ores are found in large quantities and these techniques are used in mining. Underground mining entails the sinking of shafts and development of tunnels to reach the deposits of the ore, while on the other hand open pit mining entails the removal of large quantities of material and rock to get to the ore.
Crushing and Grinding
Once the ore has been extracted it is milled and pulverized to fine powders to increase the efficiency of the extraction process. This increases the surface area of the ore particles which is important for the next step of concentration. The crushed ore, which is now in the form of small pieces of copper, is further ground in mills to fine particles. The process aids in ensuring that the ore is well prepared for concentration, hence improving the extraction of copper.
Ore Concentration
The concentration of copper ore involves several methods, including flotation and magnetic separation, to increase the copper content in the ore.
● Magnetic Separation: Magnetic separation is a process of concentrating the desired material by the use of a magnetic field. In the context of copper extraction, this method is employed to separate iron sulfides from copper sulfides. The crushed and ground ore is then taken through a magnetic separator which has strong magnetic fields. These magnets capture and retain magnetic minerals like iron sulfides while letting non-magnetic copper minerals pass through. The efficiency of this method depends on the magnetic characteristics of the minerals contained in the ore. This step is useful in the first stages of ore concentration, as it prepares the flotation process for a more concentrated amount of copper minerals.
● Flotation: Concentration of copper ores is mainly done through flotation, especially for copper sulfide bearing ores. The ore is then ground to a fine powder and then mixed with water to form a slurry to which different chemicals are added. Such chemicals include collectors that enhance the hydrophobicity of the copper minerals and frothers that enhance the stability of the froth. Air is then added into the slurry and bubbles are formed which surround the hydrophobic copper particles. These air bubbles float to the surface and form a froth layer which is removed leaving behind the copper concentrate. The other gangue minerals which do not stick to the bubbles, fall to the bottom and are also discarded as unwanted material. Flotation enables copper to be separated from other minerals and the product is a high grade concentrate that can be taken for smelting.
Smelting
The concentrated ore is then smelted through heating the ore in reverberatory furnaces to high temperatures. In smelting, the ore becomes molten and the chemical changes take place between copper sulfides and other materials, depending on the nature of the ore. A reducing agent like scrap iron is usually used to help in the extraction of copper from its sulfide state. The molten matte produced is composed of copper, iron sulfides, and other unwanted elements.
Conversion and Pyro-Refining
The molten matte is then taken through a converter furnace where it is heated further and air is blown through the molten material to oxidize the remaining sulfur and iron. This process results in blister copper which is about 98-99% pure. Pyro-refining entails further heating to eliminate other impurities to get metallic copper with higher purity.
Electrolytic Refining
The blister copper is rolled into copper anodes which are then refined electrolytically. In an electrolytic cell, the copper anodes are placed in a solution of copper sulfate and sulfuric acid. An electric current is passed through the solution and copper ions move from the anode to the cathode where they are reduced to form copper metal. This process produces highly pure copper that can be used in industries.
Subsequent Processing
The end product of the electrolytic refining process is copper metal that can be fabricated into other forms, including copper alloys and other copper products. Copper is used in its pure form in various areas such as electrical wire, heat exchanger, and as an alloying element in stainless steel.
Factors Affecting The Purity of Copper Extraction
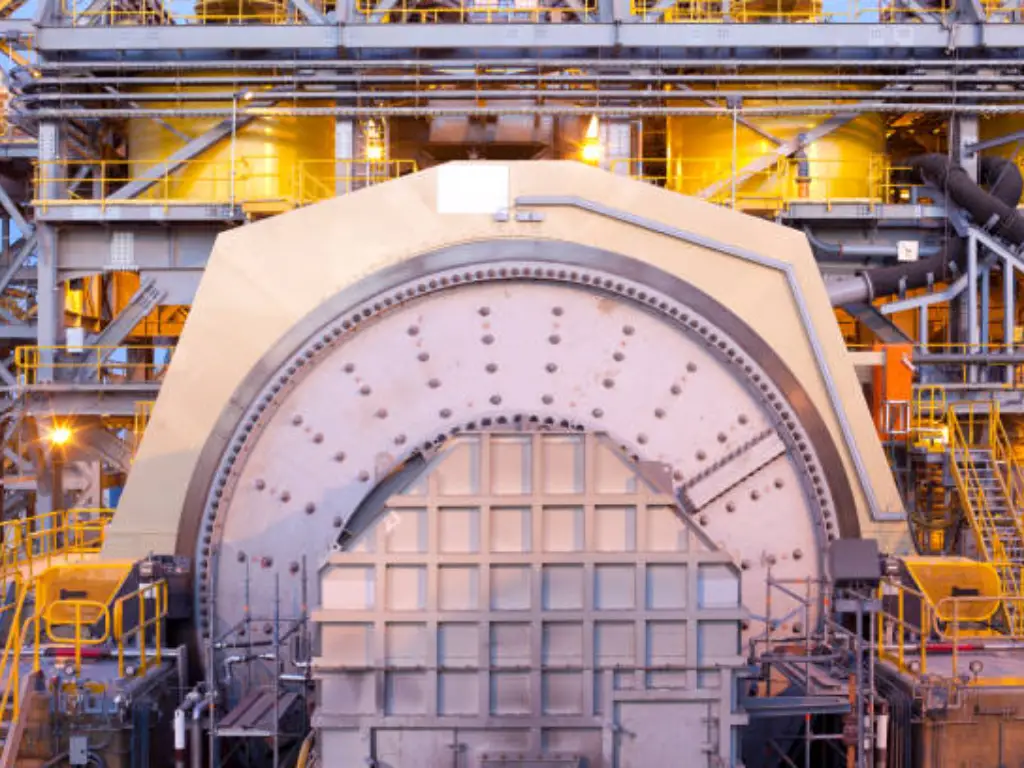
● Ore Type and Grade: The type and grade of the ore determine the quality of copper produced since some ores are richer in copper than others. High-grade ores yield higher purity and are less likely to contain impurities while low-grade ores take more processing and may contain impurities.
● Ore Pretreatment: Proper pretreatment of the ore, such as drying and grinding, ensures that the ore is in the right condition for the subsequent processing steps and hence affects the final purity.
● Flotation Process Parameters: The type of reagents used and the conditions within the flotation cells determine the efficiency of the flotation process in the separation of copper minerals from the gangue.
● Smelting Process: The smelting process involves the use of heat and time, the type of furnace used and the time taken to smelt the copper all determine the level of purity of the copper produced.
● Impurity Treatment: Proper elimination of impurities like sulfur and iron during the smelting and refining processes is important in producing high purity copper.
● Equipment and Technology Level: The type and the level of technology of the equipment used in the extraction process such as crushers, grinders and smelting furnaces affect the quality of the final product.
JXSC provides high-quality mining equipment such as crushers and grinding mills, ensuring efficient ore processing and high-purity copper extraction.
Environmental Impact of the Copper Extraction Process
The extraction of copper has various effects on the environment, the major ones being the generation of waste and the use of chemicals. Mining activities also have negative impacts on the environment as they involve the destruction of large tracts of land, thus affecting the habitats of animals and plants and leading to soil erosion. The smelting process also produces sulfur dioxide gas which is a pollutant that causes air pollution and acid rain. Also, the disposal of the tailings, which are the waste products of the ore processing, can cause water pollution if not well handled. Measures that have been taken to address these effects include employing sustainable technologies, disposal of waste, and land reclamation to allow for the regeneration of the land.
Conclusion
The future of copper extraction will be focused on the improvement of the existing methods and the creation of new technologies. Techniques like in-situ leaching which is less damaging to the environment and development in the solvent extraction and electrowinning (SX/EW) techniques are some of the promising ones. The industry is also looking at ways of using green energy to support extraction activities in a bid to minimize emissions. With the increasing demand for copper especially in renewable energy and electric vehicles, the industry has to find ways of meeting these needs in a sustainable manner.
Partner with JXSC for Reliable Copper Production
JXSC Mine Machinery Factory provides a complete set of mining operations equipment for the extraction of copper. Our rock crushers are designed for high performance and low operating costs and are made of high-quality materials to last longer. Our ball mills and other grinding machines for wet and dry applications are used in various mineral processing operations.
JXSC has been focusing on the mining equipment manufacturing for more than 35 years, and we are committed to offering our customers with stable and quality products. Our services are flexible and can be adapted to fit the requirements of your project, whether it is consultation, design, installation or maintenance. Choose JXSC for the best copper extraction services that are efficient, reliable, and of high quality.
FAQs
How are copper extraction by-products managed?
Sulfuric acid and slag which are by-products of copper extraction are recycled and treated as wastes. Sulfuric acid, which is produced as a by-product of smelting, is utilized in leaching operations or sold in the market. Slag is treated to obtain other metals or used in construction materials.
What are the major copper-producing countries?
The major producers of copper are Chile, Peru, China, United States and Democratic Republic of the Congo. These countries have large reserves of copper ore and have well developed mining industries.
How is waste managed by copper extraction?
The waste generated from copper extraction is disposed of through tailings storage facilities where the tailings are kept and closely monitored to avoid polluting the environment. Also, attempts are made to reuse water and minimize waste production through proper processing methods.