- mmldigi
Preface
What is Oxidized Gold Ore and How is it Formed?
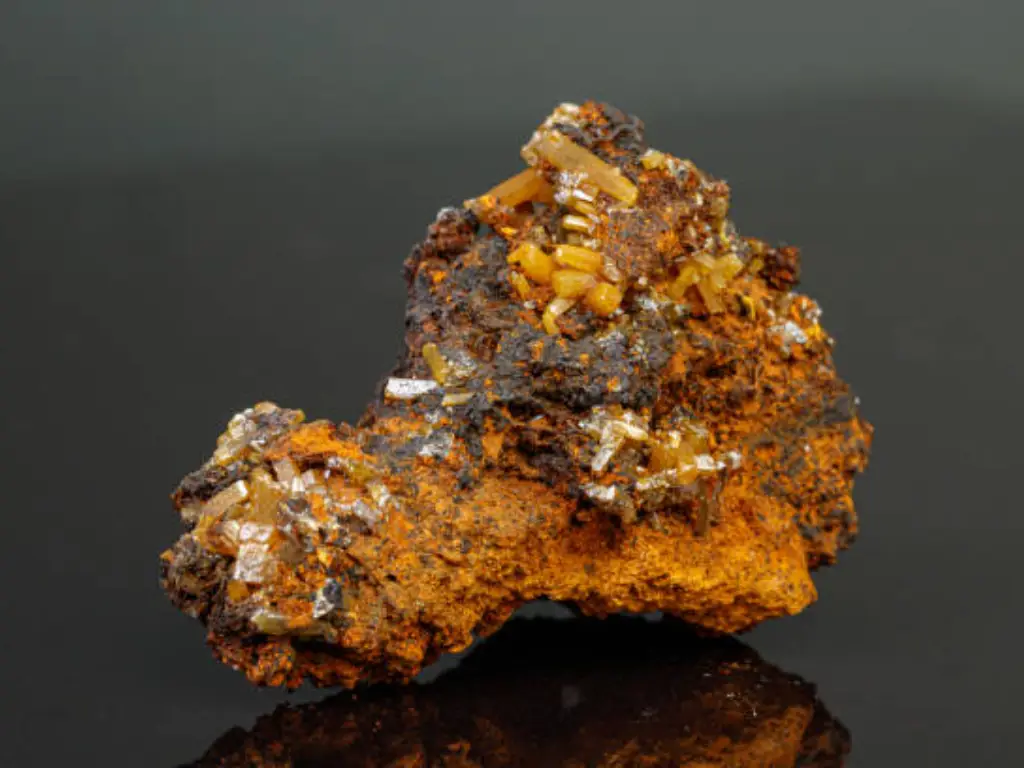
Oxidized gold ore is a kind of gold ore that has been chemically transformed through oxidation, which is the process of reacting with oxygen and water for a long time.
This happens when primary gold deposits, which include sulfide minerals, are weathered closing to the surface of the Earth’s crust. After some time, sulfide minerals are oxidized together with water, breaking down into several oxides, hydroxides, and clay minerals. This alters the original mineralogy of the ore body. Gold is liberated in the sulfide matrix and during the breakdown, is much more accessible to be extracted. Therefore, oxidized gold ores are basically the eroded surface of higher sulfide gold deposits, marked by oxidized minerals and frequently contain gold which is more easily processed through rudimentary methods such as cyanidation.
Applications of Oxidized Gold Ore
Complete Oxide Gold Ore Processing Process
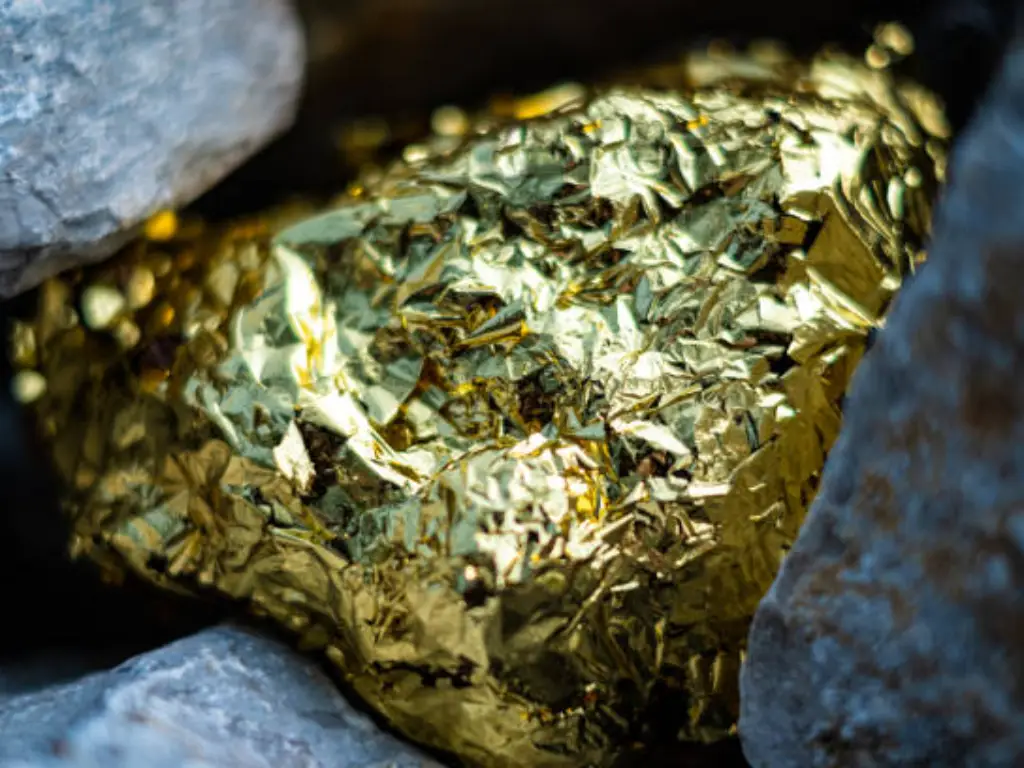
Key Equipment for Oxidized Gold Ore Processing
Equipment | Features and Properties | Application in Processing Step |
---|---|---|
Crushers | Durable construction, high capacity, and efficient reduction of ore size | Used in the initial stage to break down large chunks of ore into manageable sizes for further processing. |
Ball Mill | Efficient grinding, adjustable particle size, robust design | Used in the grinding stage to achieve the desired fineness of the ore particles, enabling better liberation of gold. |
Shaking Tables | Precision gravity separation, adjustable settings, durable | Used in the gravity separation stage to concentrate gold particles based on density differences. |
Flotation Machines | High recovery rates, effective reagent distribution, easy to operate | Used in the flotation separation stage to collect gold particles by making them hydrophobic and allowing them to float. |
Magnetic Separators | Strong magnetic fields, selective separation, low energy consumption | Used in the magnetic separation stage to remove magnetic minerals, leaving behind non-magnetic gold-bearing material. |
Autoclaves | High pressure and temperature capabilities, effective oxidation | Used in the pre-treatment stage to break down refractory minerals and make gold more accessible for extraction. |
Thickener Tanks | High capacity, efficient solid-liquid separation, low maintenance . | Used in the concentration and filtration stage to remove excess water from the slurry |
Filter Presses | High-pressure filtration, effective moisture removal, durable design | Used in both concentration and dewatering stages to further remove moisture from the concentrate. |
Activated Carbon Columns | High adsorption capacity, durable, easy regeneration | Used in the adsorption stage to capture gold-cyanide complexes from the solution. |
Smelting Furnaces | High temperatures, precise control, efficient refining | Used in the refining stage to purify the gold concentrate and achieve high purity levels. |
Lorem ipsum dolor sit amet, consectetur adipiscing elit. Ut elit tellus, luctus nec ullamcorper mattis, pulvinar dapibus leo.
How to Select Cutting-Edge Equipment?
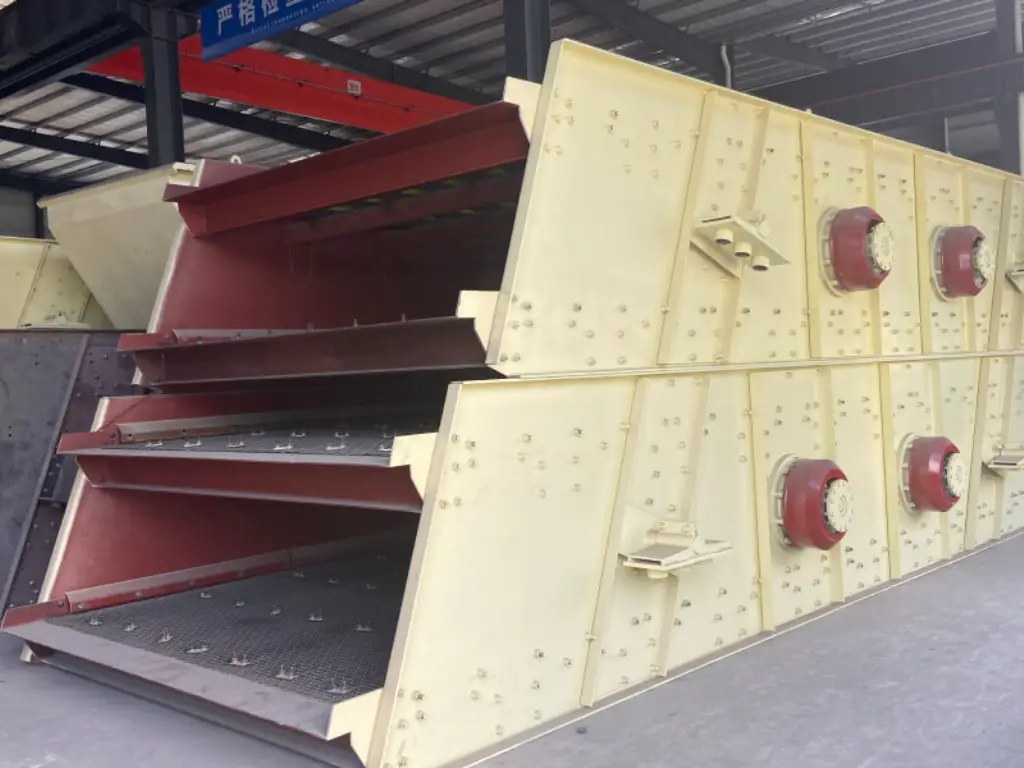
To explore how different screen designs influence the sorting process, check out Vibrating Screen Design Demystified: Types and Benefits.
Problems and Solutions for Processing Oxidized Gold Ores
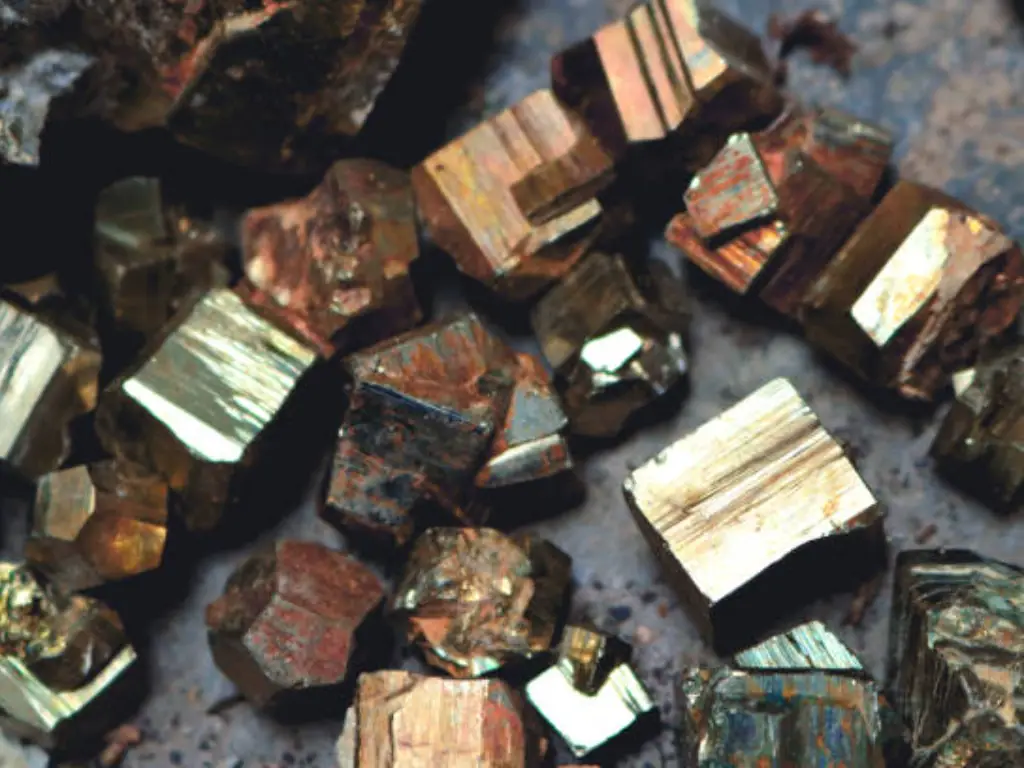