- Home
- Blog
- Mineral Solution
- A Comprehensive Guide to the Ball Milling Process
What is Ball Mill?
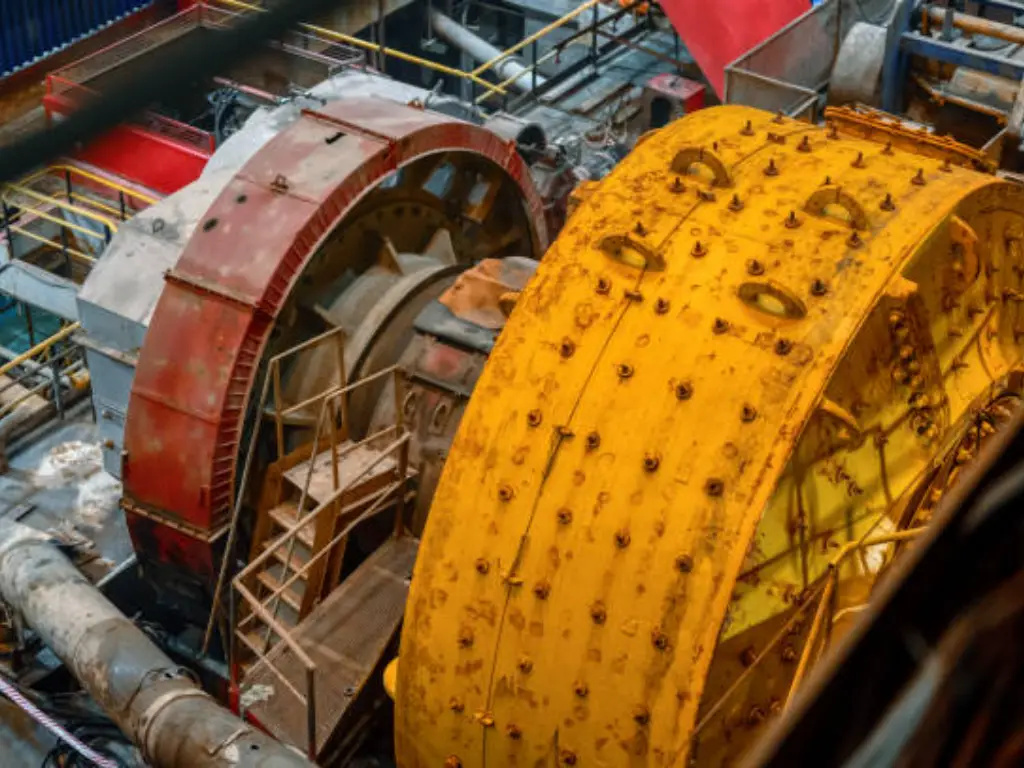
A ball mill is a type of grinder used to reduce the size of materials through grinding and particle size reduction process. Its primary application is to disintegrate materials into fine particles to facilitate several chemical reactions and enhance the properties of the materials. The ball milling process is carried out by using balls, which can be steel balls or ceramic balls, to apply force on the feed materials to reduce its size through impact and attrition as the balls fall from near the top of the shell.
Ball Mill vs Other Grinding Equipment
Grinding Method | Description | Pros and Cons |
---|---|---|
Ball Mill | A cylindrical device used for grinding materials like ores, chemicals, and ceramics. It rotates around a horizontal axis, partially filled with the material to be ground plus the grinding medium. | Ball mills are highly efficient for fine and ultra-fine grinding, and they are versatile for various materials. However, they have high energy consumption and require regular maintenance to ensure optimal performance. |
Rod Mill | Similar to a ball mill, but uses long steel rods as the grinding media. The rods grind the ore by tumbling within the mill. | Rod mills are more suitable for coarse grinding and have lower energy consumption for certain applications. However, they are limited to a narrower range of materials and are less efficient for fine grinding tasks. |
Sag Mill | A semi-autogenous grinding mill that uses a combination of ball and rock/ore as the grinding media. | SAG mills offer high throughput and can process large volumes, making them suitable for bulk processing. On the downside, they have high operational costs and require careful management of grinding media size and material characteristics. |
For detailed differences, click SAG Mill vs Ball Mill: Choosing the Right Grinding Mill
Successful Ball Milling Applications
Ball milling has found successful applications in various industries due to its versatility and efficiency. Here are some notable fields and examples:
● Mineral Processing: Commonly employed in the grinding of ores such as copper, gold and iron ores.
● Pharmaceutical Industry: For milling active pharmaceutical ingredients into fine particles.
● Materials Science: For the production of new alloys and compounds by mechanical alloying such as advanced ceramics, nanomaterials.
How Does a Ball Mill Work?
The working principle of a ball mill is that it is a cylindrical structure that rotates horizontally for the purpose of grinding the grinding media and the material to be ground. When the cylinder rotates, the material and the grinding media are lifted to the high side of the cylinder and then dropped due to the force of gravity . This results in impact and attrition, hence the size reduction.
Key Components of a Ball Mill
● Cylinder: The portion of the mill that is actively used to grind the material and is typically made of steel or ceramic. It is mounted on the axis that includes the grinding media and the material to be ground.
● Grinding Media: Maybe steel balls, ceramic balls or even pebbles. The type of media used in milling affects milling efficiency and the particle size distribution of the final product.
● Motor and Drive System: It is responsible for the rotation of the cylinder. The speed and direction of rotation can be altered in a way that will be most effective in milling.
● Liner: Influences the movement of the grinding media and shields the cylinder and increases milling effectiveness.
● Discharge Mechanism: Allows for the milled material to be easily discharged from the mill. This can be a grate or an overflow type depending on the design of the mill
Ball Milling Process
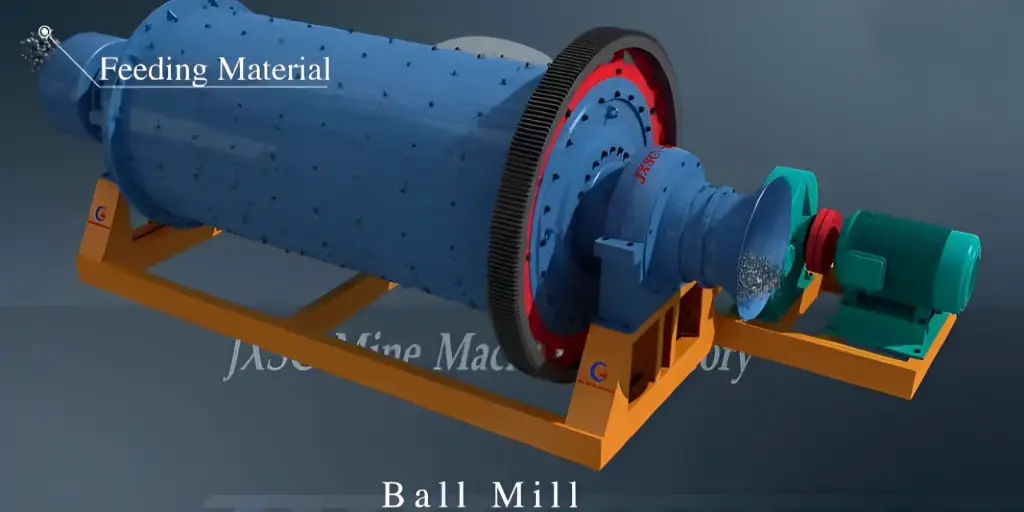
Step1 Feeding Material: The process begins with the feeding of raw materials into the ball mill. From the image, it can be observed that materials are charged into the mill through a particular charging system. Such materials may be ores, chemicals, ceramic materials and so on. The feed size should be regulated in order to enable grinding and any large particles may need to be ground again.
Step2 Rotation of the Cylinder: Once the materials have been fed into the ball mill, the cylindrical container begins to revolve on a horizontal axis. This rotation is done by a motor and drive system which is seen at the far end of the mill in the picture. The rotational speed can be adjusted to ensure that the grinding media and the material are lifted and cascaded in the right manner for grinding.
Step3 Grinding Action : In the rotating cylinder, the grinding media and the material to be ground are lifted on the side of the cylinder that is rising and then they fall due to the force of gravity. This action results in the impact and abrasion forces between the grinding media and the material which crushes the material to a smaller particle size. The effectiveness of this step is determined by the rate of rotation, size and density of the balls and the time of milling.
Step4 Particle Size Reduction: When the grinding media are in motion and are causing the material to be ground, the size of the particles is gradually reduced. The motion and friction of the grinding media on the material continues to crush the feed material into smaller sizes. This interaction between the grinding media and the material can be controlled and enhanced by adjusting the milling parameters including milling time and the weight of the grinding media making it very important in the enhancement of the process as well as the product.
Step5 Discharging the Milled Material : When the material has been ground to the required size it is discharged from the mill. The discharge mechanism which may be a grate or an overflow type helps in the discharge of the milled material from the cylinder. The particles of the required size are separated from the grinding media and taken for other processes or uses. Any coarse material may be returned back to the mill for further grinding if it is too large to pass through the classifier.
Step6 Gathering and Processing the Output : The final process is to collect the milled material and analyze the particle size distribution to achieve the required size. The methods that can be used to determine the particle size distribution include sieve analysis, laser diffraction or dynamic light scattering. This data is useful in enhancing the milling process and ensuring quality of the final product.
How to Optimize Ball Milling for Maximum Efficiency?
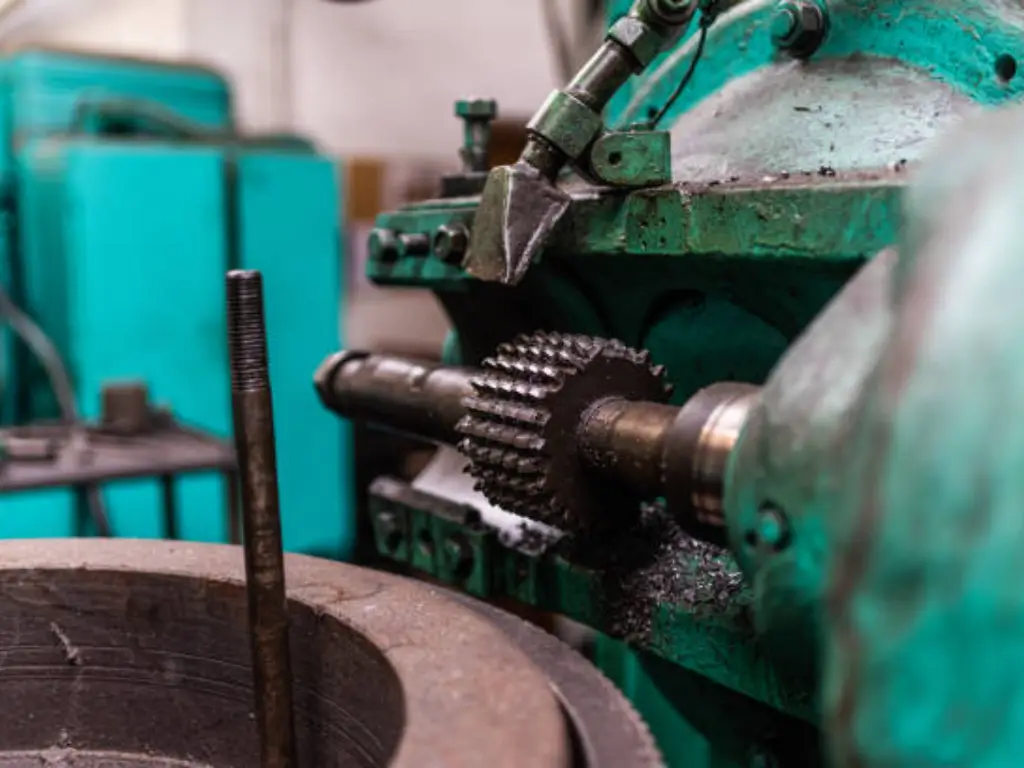
For the ball milling process to be as efficient as possible, several factors need to be controlled and regulated. Here are key considerations:
● Adjust the Rotational Speed: Change the speed of rotation of the ball mill in order to make the grinding media to be lifted and cascaded effectively. This increases the force applied on the particles to get the best results in size reduction. The optimal speed is variable depending on the mill and the material that is being ground.
● Select the Appropriate Grinding Media: Choose the grinding media that are suitable for the material and the size of the particles that are to be produced. Yes, steel balls, ceramic balls, and pebbles are all useful but they have their own advantages and are used in different processes. The size and density of the grinding media have a very significant influence on the milling process.
● Control the Feed Size: Ensure that the feed size of the material is as per the ball mill requirement. In general, it is observed that the feeds with smaller particle sizes yield better milling and finer particle sizes than the larger feed sizes. Feed material should be well prepared to enhance milling and reduce energy consumption.
● Optimize Milling Time: Optimize the milling time so that the grinding is adequate while at the same time being as energy efficient as possible. Long milling time may lead to production of small particle sizes but at the same time it leads to high wear of the milling tools. This way, the milling duration is well regulated to achieve the desired particle size distribution as required in the process.
● Maintain the Right Media Load: Ensure that the mill is charged with appropriate amount of grinding media. Overloading or underloading of the milling machine can also have an impact on the efficiency of milling and quality of the end product. It is recommended that the media load should be checked and balanced at least once a week.
● Implement Regular Maintenance: Make sure that the mill is always in its best performing state by making sure that it is always in good condition. Liners and balls should be inspected frequently and replaced when they are worn out. Maintenance reduces the periods that the milling equipment will be off and thus increases its useful life.
● Monitor and Control Temperature: Check that the temperature of the milling process is not high so as to cause overheating of the machine. Temperature changes affect the properties of the material and the milling process. Temperature can be controlled by cooling or by milling at certain intervals.
● Use Advanced Monitoring Tools: Integrate sensors and automation to monitor the milling process and provide real-time data. These tools provide information on speed, load, and temperature among other factors. Real-time monitoring allows the changes to be made as soon as they are required, which in turn increases the overall milling efficiency.
Conclusion
Ball milling is a process that is still evolving with the aid of new technologies and the science of materials. Future trends could be the development of new types of grinding media with higher energy efficiency, the use of high-tech technologies and automation systems for process control, and the use of new materials to improve the characteristics of the grinding process. As industries are shifting towards more efficient and sustainable processes, the ball milling process is expected to have a higher demand in applications such as mineral processing and synthesis of advanced materials.
FAQs
How to measure the particle size distribution after ball milling?
Particle size distribution after ball milling can be analyzed by laser diffraction, dynamic light scattering or sieve analysis. These methods give quantitative data on the distribution of particle size in the milled material and hence the extent of milling can be controlled and optimized.
How to choose the right grinding medium for ball milling?
The type of grinding medium to be used depends on the material to be ground, the required particle size and the milling conditions. Some of the most used grinding media are steel balls, ceramic balls and pebbles. The density, hardness and chemical composition of the grinding media should be taken into account to increase the milling efficiency and obtain the required results.
How does ball milling compare to other particle size reduction techniques?
Ball milling is very efficient in reducing the particle size and attaining a narrow particle size distribution as compared to other methods. It operates on the basis of impact and abrasion, imparting high kinetic energy to the grinding media, which can be steel or ceramic balls, or rods of stainless steel or alumina.