- Home
- Blog
- Mineral Solution
- A Comprehensive Guide to the 4 Types of Iron Ore
- mmldigi
What is Iron Ore?
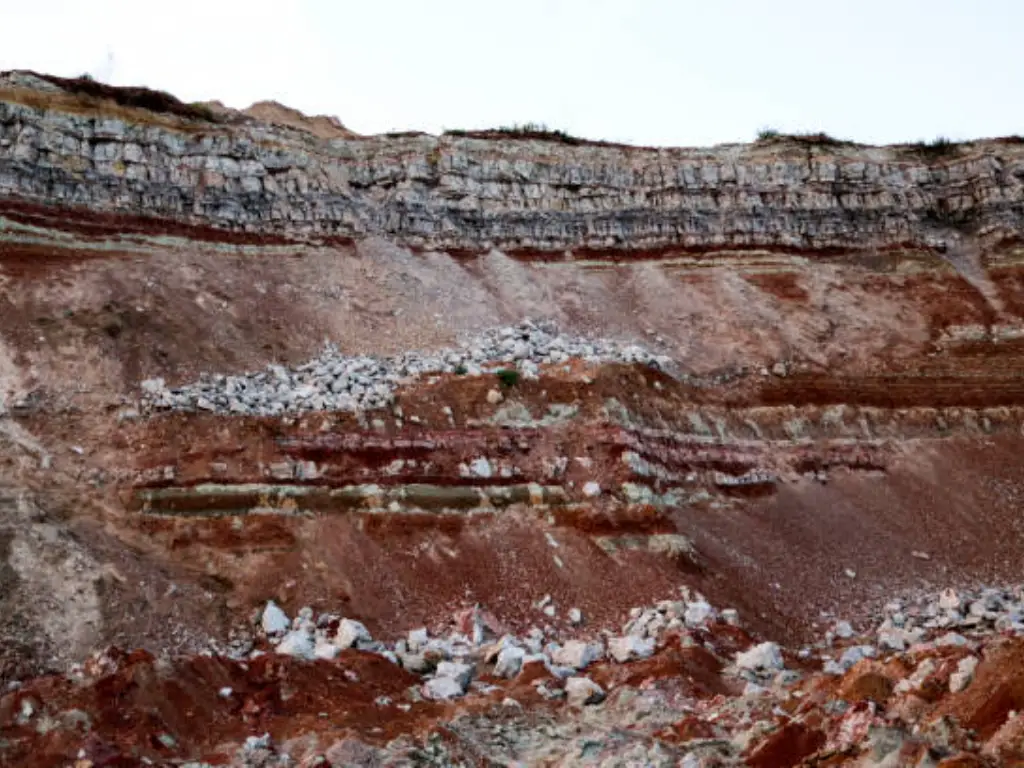
Application of Iron Ore
Where can you Find iron ore?
China
Brazil
Western Australia
Application of Iron Ore
Types of Iron Ore
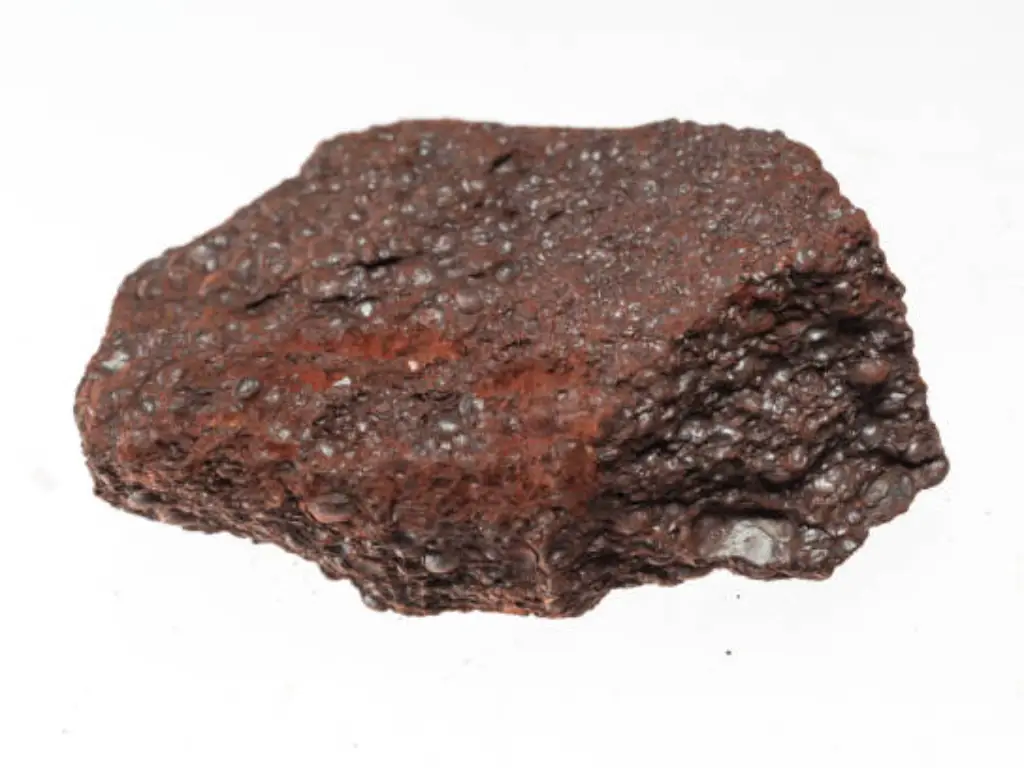
Haematite
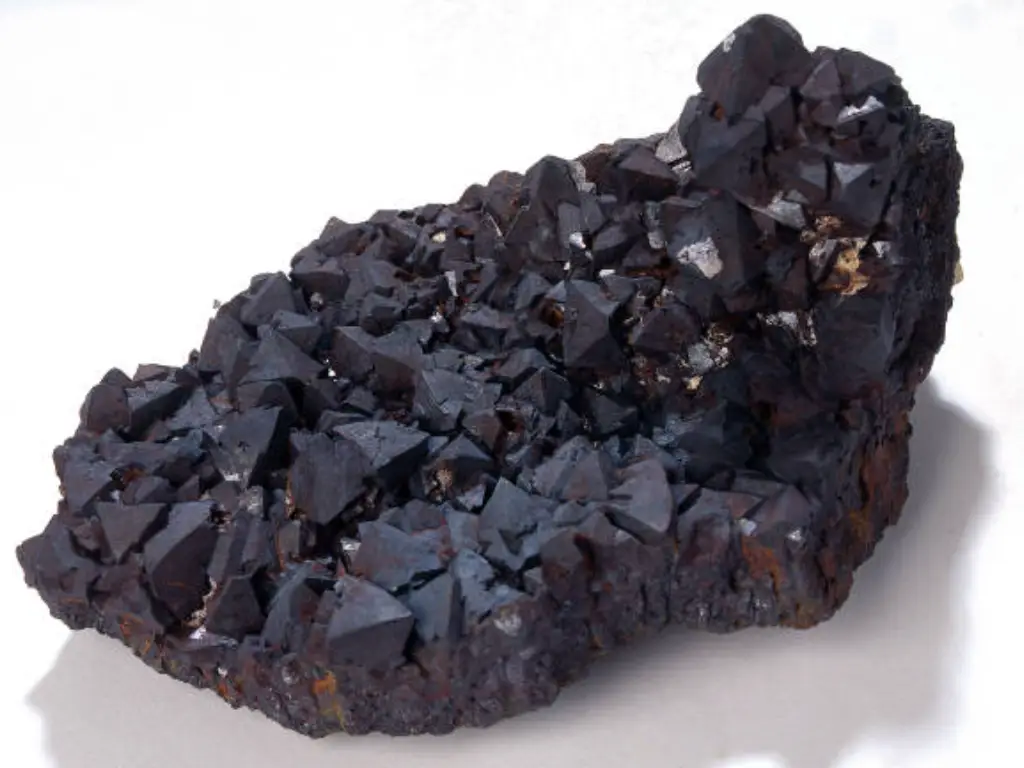
Magnetite
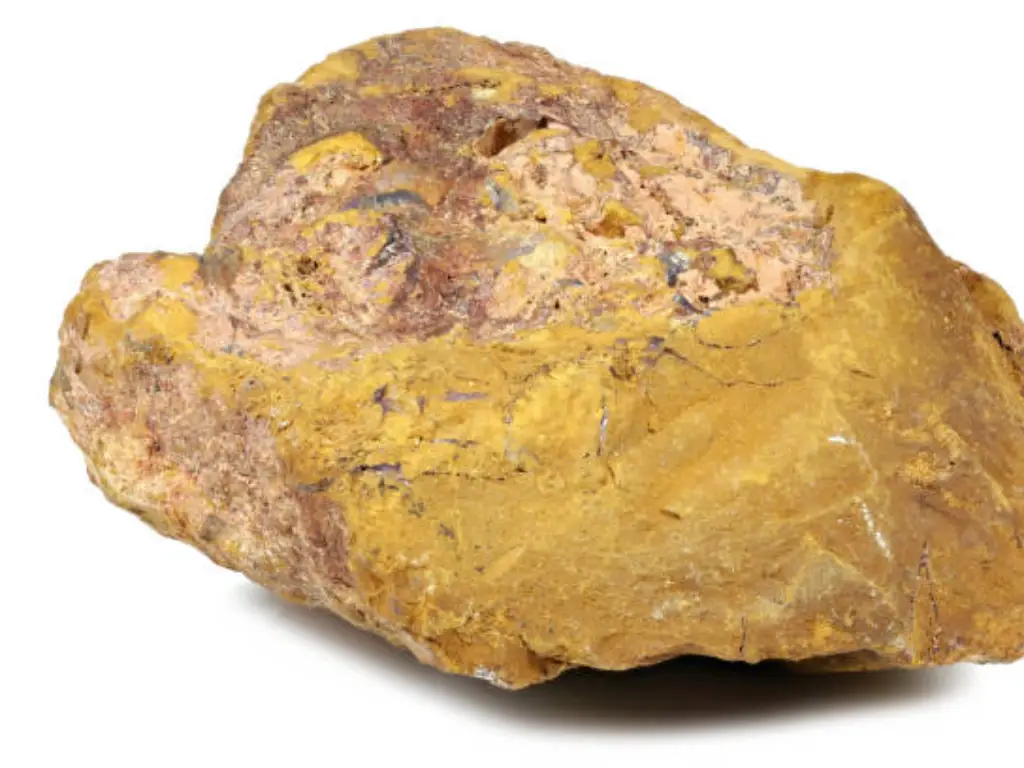
Limonite
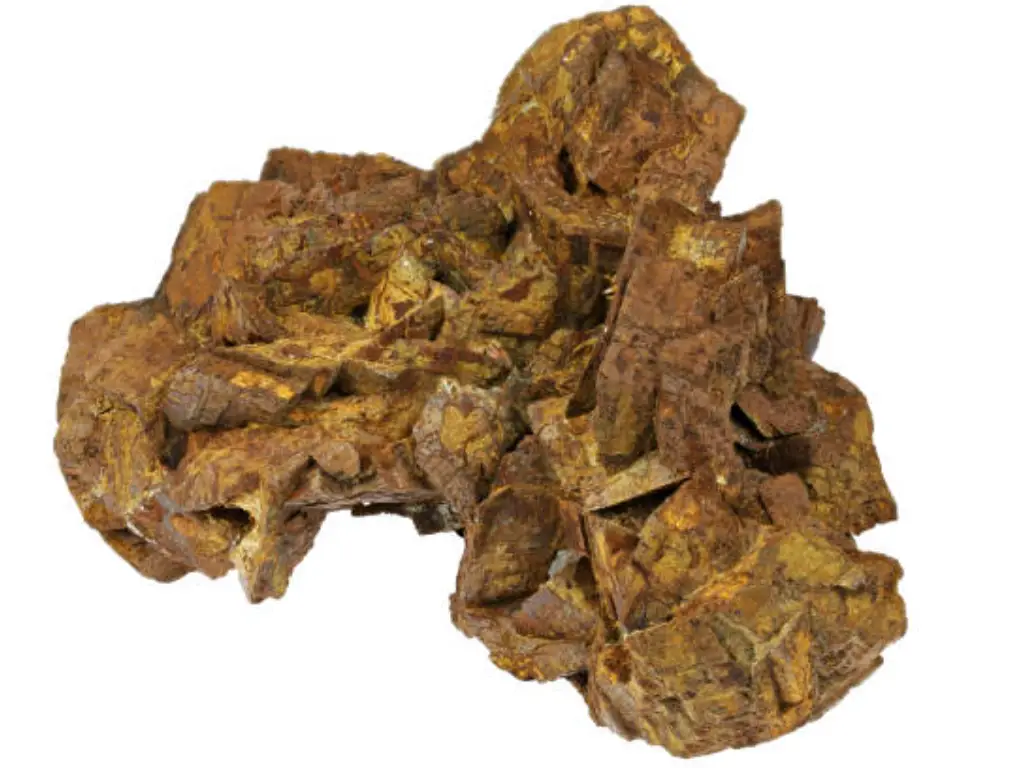
Siderite
Which Ore is Suitable for Iron Smelting?
How Is Iron Mined?
Equipment Used in Ore Ming
Name | Characteristics and Functions | Mining stage |
---|---|---|
Drilling Rigs | Used to create holes for blasting or collecting ore samples | Exploration and extraction |
Blast Furnaces | Large, high-temperature furnaces for smelting iron ore | Smelting |
Crushers | Machines that break down large rocks into smaller pieces | Crushing |
Conveyors | Transport ore and materials within the mining site | Material handling |
Magnetic Separators | Devices that use magnetic fields to separate iron ore from waste | Beneficiation and mineral separation |
Flotation Cells | Equipment used to separate minerals based on their chemical properties | Beneficiation and mineral separation |
Ball Mills | Machines that grind ore into fine powder | Grinding and beneficiation |
Thickeners | Equipment used to concentrate ore slurry by removing water | Beneficiation and mineral separation |
Feeder Equipment | Devices that control the flow of ore to various processing stages | Material handling and processing |
Want to get more detail about ore mining equipments? Visit https://www.minejxsc.com/mineral-processing-equipment/.
Process of mINING iron Ore
How to Improve Mining Efficiency?
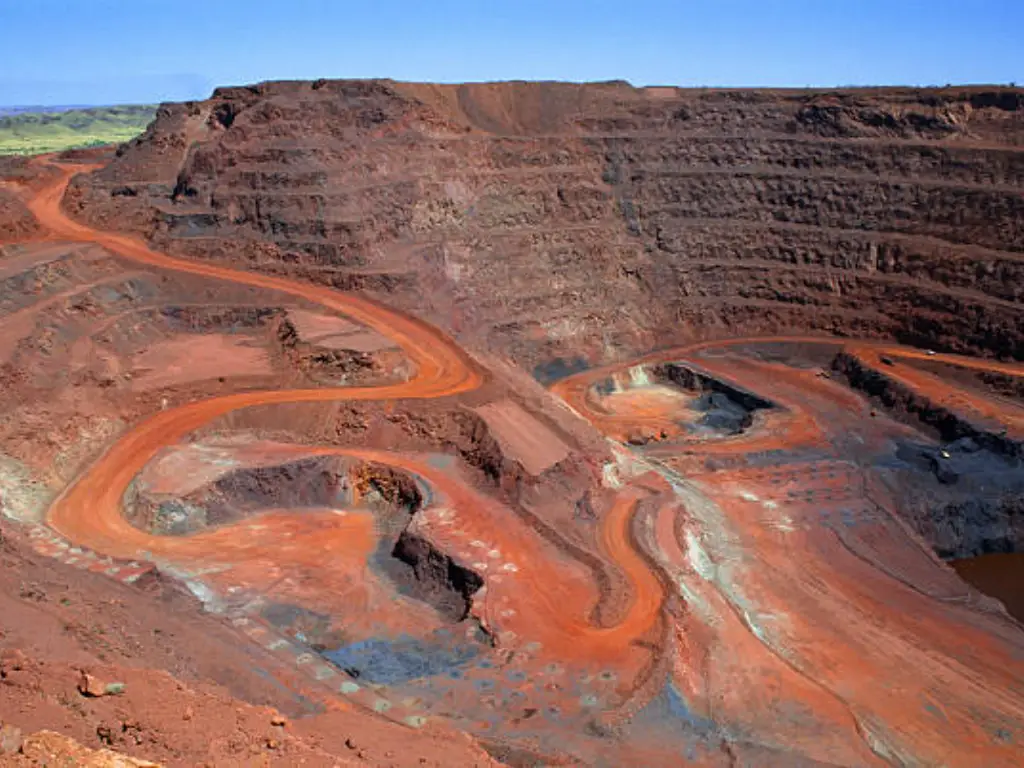
Environmental Effects and Sustainability in Iron Mining
Conclusion
With a presence in more than 60 countries around the world JXSC boasts reliable mining machine quality as well as reasonable processing flow design and exceptional after-service. The company offers a wide range of services like engineering consultation mineral processing experiments mine design installation and commissioning personal training tracking service management of dressing plants. In collaboration with JXSC customers may have their mining process seamlessly.
Partner with JXSC for Iron Ore Processing Excellence
Different factors like worldwide steel demand, technology advances, and environmental rules affect the market of iron ores. Furthermore, the quest for industrializing economies will continue to fuel the demand for iron ore strongly. However, industry’s future will be determined by sustainability concerns and a necessity for more efficient mining practices.
Future supplies will need technological breakthroughs in automation as well as advanced beneficiation techniques to minimize their impact on environment while at same time meet rising demands. Companies such as JXSC Mine Machinery Factory with expertise in mining equipment and processing solutions are well suited to guiding the industry to more sustainable and effective methods.