- Home
- Blog
- Mineral Solution
- What is Mineral Processing and Its Steps?
- mmldigi
The Significance of Mineral Processing
At the heart of it all, mineral processing boosts the mining industry’s knack for making the most out of ore deposits in a profitable way. It’s all about picking out and concentrating the good stuff – those valuable minerals. This not only helps mining projects make more money but also plays a big part in looking after our environment. By making it possible to get minerals from less rich ores, it cuts down on the need to mine too much, saving precious natural resources and keeping the landscape from being messed up.
Commonly Processed Minerals Include:
● Metals: This category encompasses a wide range of elements that are essential for various industries, including but not limited to aluminum, bauxite, chalcopyrite (a major copper ore), chromite (the main source of chromium), copper, galena (lead ore), gold, hematite (an iron ore), iron, lead, magnetite (another iron ore), molybdenum, nickel, platinum, silver, sphalerite (zinc ore), tin, and zinc.
● Non-metals: Coal, quartz, diamonds.
● Industrial Minerals: This category includes phosphate, potash, and sulfur—key ingredients in fertilizers; gypsum, used in construction; and barite.
● Precious Stones: Apart from diamonds, other precious stones like rubies, emeralds, and sapphires.
All these minerals go through mineral processing to boost their purity, concentration, or overall usefulness, showing just how versatile and essential this area is in the mining world. Thanks to advances in technology and smarter ways of doing things, the mineral processing industry keeps getting better and better, making sure we can get the most out of the earth’s mineral treasures in a sustainable and efficient way with the right equipment.
5 Steps to Mineral Processing
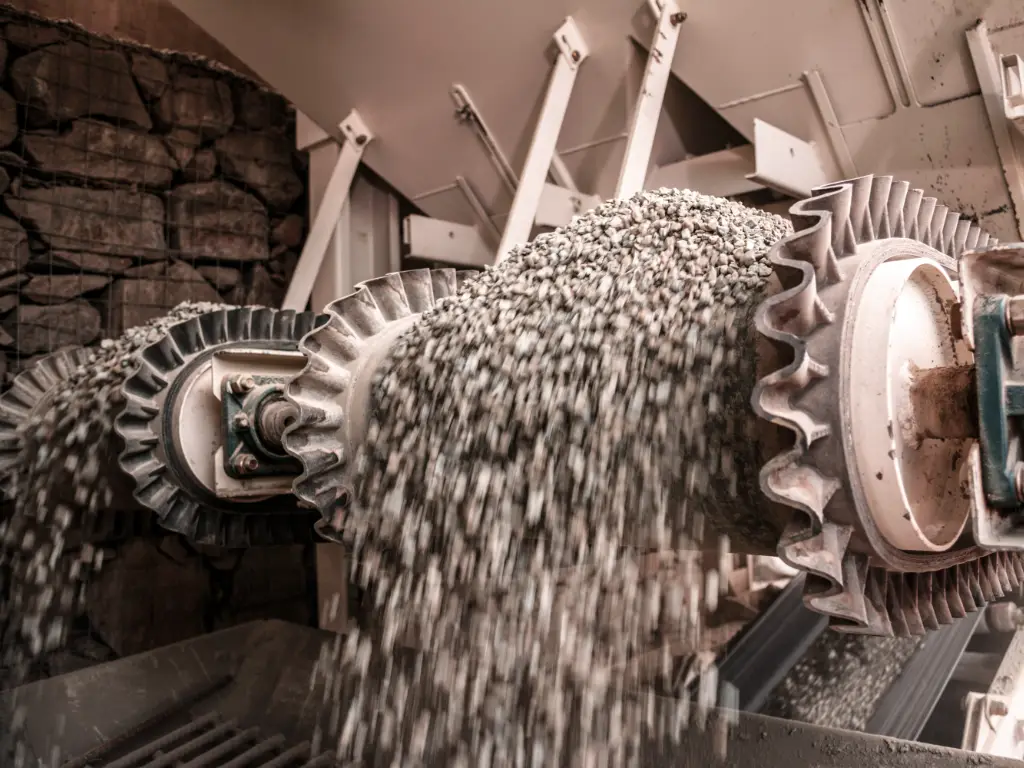
Step 1: Crushing and Grinding
Step 2: Screening and Classifying
Step 3: Concentration (Mineral Processing Method)
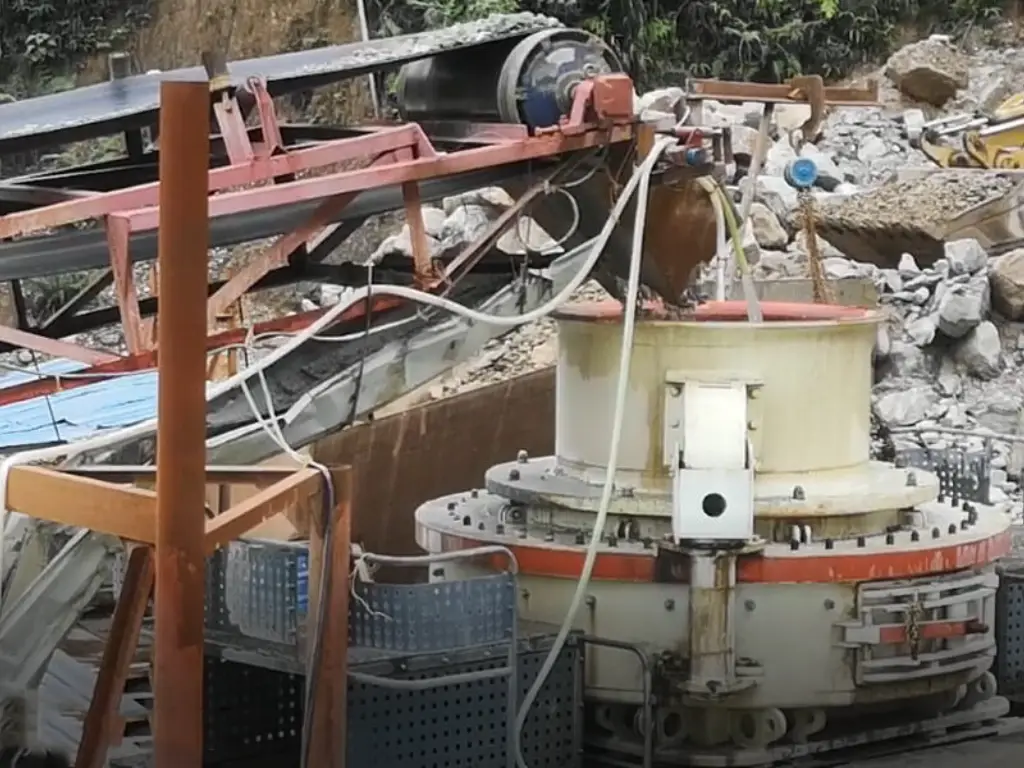
Gravity Separation
Magnetic Separation
Flotation
Electrostatic Separation
Chemical Beneficiation
Step 4: Dewatering
Step 5: Drying and Final Product Processing
Case Study: Mineral Processing for Gold
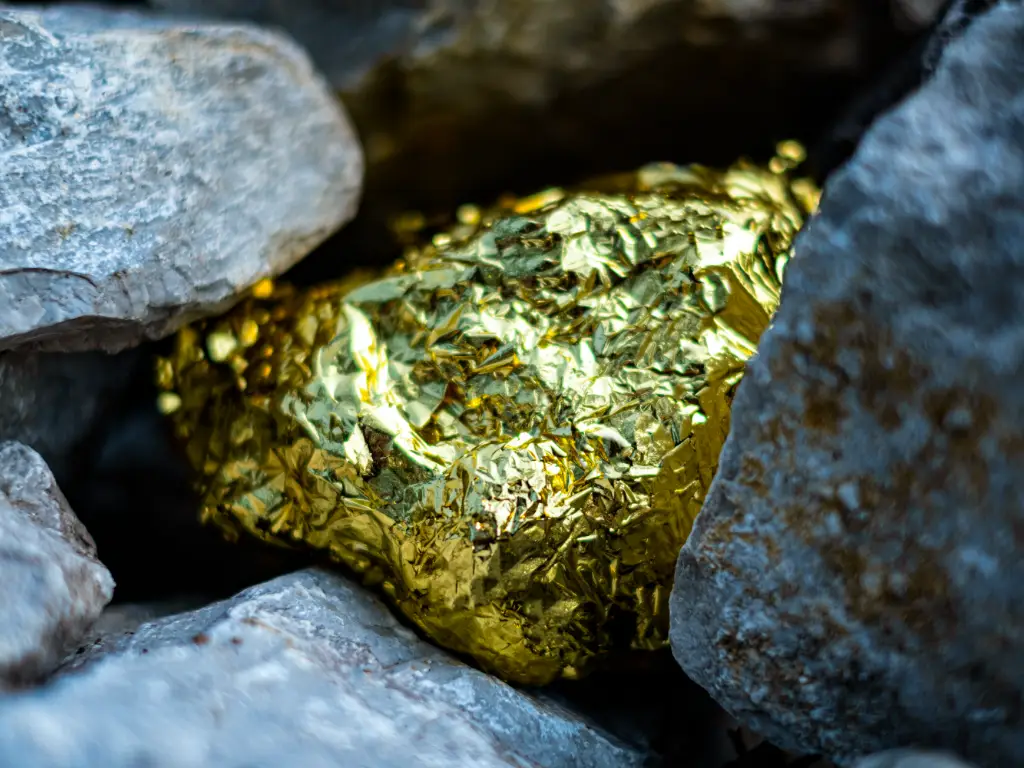
1. Alluvial Gold Processing: When we talk about alluvial gold, it mainly goes through a process called gravity separation. This happens because the gold is found in riverbeds, streambeds, and floodplains, mixed in with lighter dirt and sand. Here’s how we do it:
● Feeding: We start by feeding the soil into the process, using cool gadgets like vibrating feeders or just loading it by hand.
● Washing and Sieving: Then we clean the gold using gold trommel wash plants and screens. This helps us get rid of the dirt and separate the gold from other small bits.
● Primary Selecting: First, we use machines that spin super fast or special jig machines to separate the gold.
● Final Concentration and Refining: Then, to get all the gold together, we use shaking tables, sluice boxes to catch any missed bits, and smelting furnaces to make the gold pure.
2. Rock Gold Processing: On the other hand, processing rock gold begins with physically breaking down the ore by crushing it, sometimes in several steps, to get it ready for separating. Just like with alluvial gold, after we prepare it at the start, the ore taken from quartz veins or other hard rock spots goes through:
● Gravity Separation: Here’s where equipment like shaker tables come into play, especially useful for getting the oxide gold separated right after crushing.
● Flotation and More: For gold mixed with sulfide minerals, we often use flotation to get the gold away from those sulfides. And for the really tricky ores, we might even use more steps, like ball milling, to make sure we’re getting as much gold out as we can.
Central Role of Gravity Separation: In both alluvial and rock gold mining, gravity separation is the star at the start. For alluvial gold, its straightforward and effective way of picking gold out from lesser materials makes it the top pick. It’s usually the first step, followed by even more detailed methods. With rock gold, gravity separation teams up with other methods, such as flotation for the gold that’s mixed with sulfide minerals, showing just how complex the ore can be. This mix-and-match strategy helps us get the most gold we can, showing just how flexible gravity separation is when we’re dealing with different mining techniques.
What Mineral Processing Equipment Do You Need?
Equipment Category | Equipment Type |
---|---|
Crushing and Size Reduction | Jaw Crushers
Cone Crushers Gyratory Crushers Hammer Crushers Impact Crushers Roll Crushers |
Grinding and Further Size Reduction | Ball Mills
Rod Mills SAG Mills Vertical Roller Mills |
Separation and Concentration | Magnetic Separators
Flotation Cells Gravity Separation Equipment (e.g., Jigs, Spirals, Shaking Tables) Centrifugal Separators Hydrocyclones |
Dewatering and Moisture Reduction | Thickener Tanks
Filter Presses Vacuum Filters Rotary Dryers |
Material Handling | Conveyor Belts
Feeders (e.g., Apron, Grizzly, Vibrating) Bucket Elevators |
Tailings Management | Tailings Dams
Paste Thickeners |
Refining and Smelting | Smelting Furnaces
Electrolytic Cells |
Conclusion
FAQ
Raw minerals are often interspersed with impurities or other, unrefined elements. Moreover, the processing of minerals aids in separating the impurities and non-valuable components from the useful ones. This makes the minerals ready for use in industries, manufacturing or even at a consumer level.
Processing removes impurities and changes the form of the minerals, often transforming raw ores into refined metals or materials. This makes them more suitable for industrial, technological, or construction purposes.
The initial stage involves extracting raw ores, followed by mechanical and chemical processes that isolate and refine useful parts into metals, construction materials, or other useful products for industries such as transportation, construction, and technology.