- Home
- Blog
- Equipment Info
- Mineral Processing Solutions: Exploring Types of Jaw Crusher
- mmldigi
The Essential Role of Jaw Crushers in Ore Processing
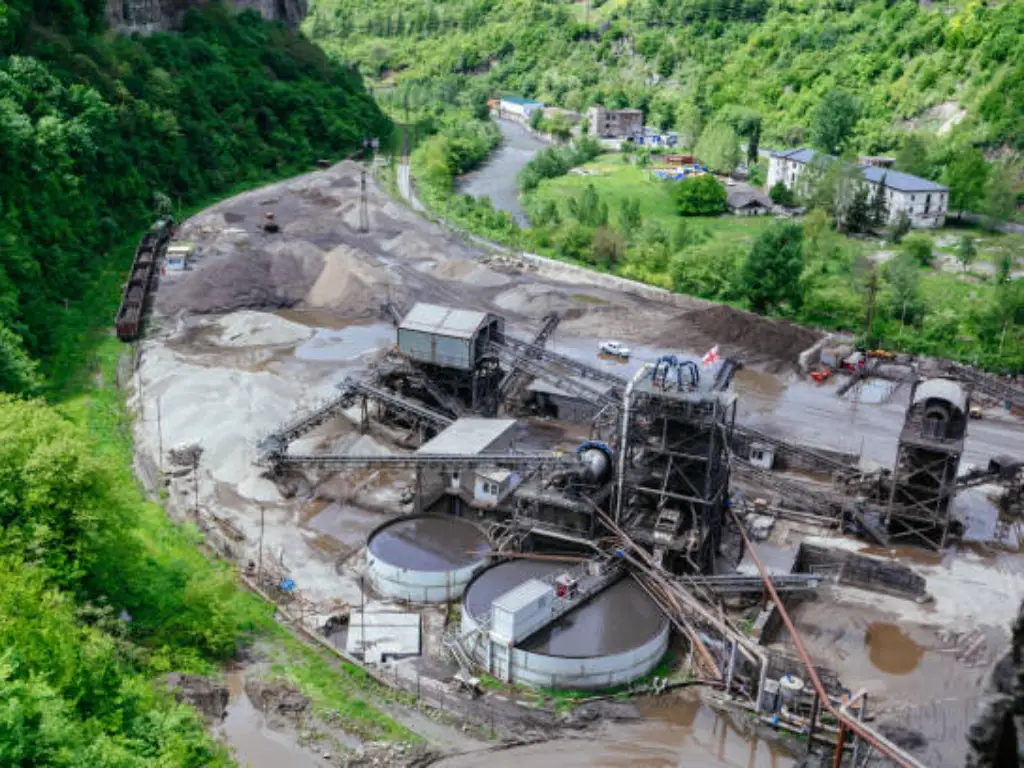
Jaw crushers are truly the bedrock of any material processing work in both the mining and construction worlds. They play an essential part in smashing up big, tough chunks of material into smaller bits, preparing them for the next steps where these valuable bits of earth are processed and valuable minerals are pulled out. These hefty machines kick off the process that turns plain raw stuff into the polished materials that are key for all sorts of building and crafting jobs. If it weren’t for the strong crushing power of jaw crushers, getting minerals out of ore would be way more of a hassle, really showing just how crucial they are to the whole industry.
The Fundamental Design and Operation of a Jaw Crusher
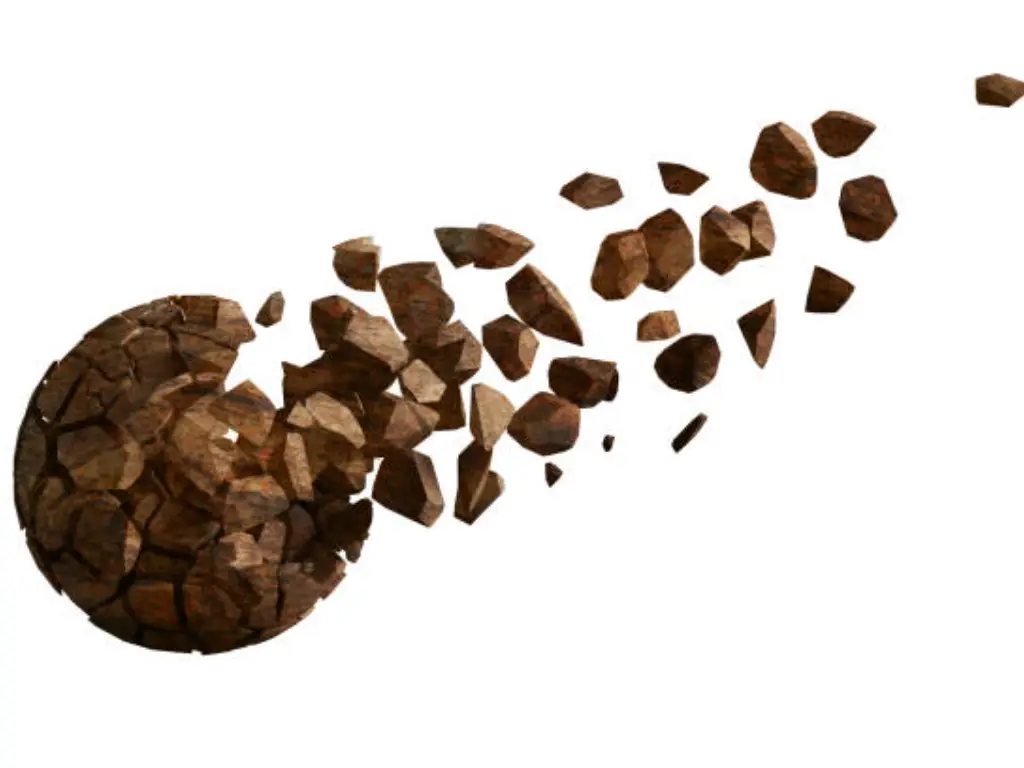
At the heart of jaw crushers is a super-efficient design meant for tackling the toughest crushing jobs. In a nutshell, these hefty units use a straightforward technique: they have two sturdy jaw plates, a stationary one and a moving one. You feed the stuff you want to crush into a V-shaped area — the crushing chamber — that’s made by these plates. When the moving jaw squashes the stuff against the still jaw plate, everything gets squeezed, cracks up, and breaks into tinier bits and pieces.
The whole process of breaking things down first happens thanks to an eccentric shaft, which makes the moving jaw swing and apply the crushing force. One really handy thing about jaw crushers is that you can change the size of the end product by shifting the discharge opening’s spot. Because of this tweakable feature, jaw crushers can adapt to a bunch of different crushing needs. This flexibility is why these crushers can do all sorts of jobs, like making big quarry rocks smaller or getting minerals ready for industry work. They’re total pros at dealing with tons of different materials and sizes, all thanks to their straightforward yet smart way of working. This smooth operation is exactly why jaw crushers are basic, must-have machines when it comes to mineral processing.
To visualize the design, refer to jaw stone crusher: An Easy Guide to Jaw Crusher Diagram.
Comparing Primary and Secondary Crushing with Jaw Crushers
Starting with primary crushing, jaw crushers really show their might in breaking down huge chunks. They’re built to take on big feed materials — we’re talking rocks up to a meter (three feet) across. At this primary crushing stage, the goal is to make these big rocks more manageable, shaving them down to sizes between 150 and 300 mm (6 to 12 inches) to reduce the size of large rocks. Grinding down to these smaller sizes makes it easier to handle the rocks in the next steps. And since some jaw crushers can churn through 500 tons an hour, they’re cut out for this big job.
Now, when you look at secondary crushing, it’s all about finessing materials that have already been roughed up by a primary crusher. This time, the pieces coming in are usually between 100 and 250 mm (4 to 10 inches), and the aim is to get them even smaller, down to about 25 to 80 mm (1 to 3 inches). This middle step is super important if you need specific sizes for things like building projects, pulling out minerals, or more detailed industrial processing. Jaw crushers in the secondary stage are geared to give you a finer crush, and they’re usually more compact than their primary counterparts.
What’s really nifty about jaw crushers is how they can be dialed in to work with various materials and sizes. You can tweak your machine to spit out the exact end product you need for your specific application and operational requirements. This kind of customization is key for nailing those operational goals and keeping things running smoothly, whether you’re in the first round of breakage or fine-tuning for the final outcome.
Types of Jaw Crushers
Single Toggle Jaw Crushers
Picture this: in a single toggle jaw crusher, the main engine shaft is installed at the very top. Now, the swing jaw hangs on this shaft, leading to some fancy jaw movement that’s a bit more complex than what you’d find in double toggle crushers. As the swing jaw dances up and down, its path looks like an ellipse. This funky dance move really puts the squeeze on the stuff we’re crushing, especially as the jaw moves down. And because of this nifty setup, crushing happens effectively in each and every cycle. This is totally what you want for smashing materials that need a lot of elbow grease, fast. The single lever setup doesn’t just cut down on the crusher’s weight and bulk but also kicks up efficiency a notch, perfect for the heavyweight champ of crushing – the primary stage – and keeping things running smoothly.
Double Toggle Jaw Crushers
Double toggle jaw crushers feature a hinge at the top of the swing jaw. This design uses two toggles or levers to create movement. The eccentric shaft is positioned behind the swing jaw, and the toggle plates connect the lower part of the swing jaw to the drive mechanism. As the eccentric shaft rotates, it drives the toggle plates to move, creating a powerful crushing action as the angle between the two toggles becomes more acute. This mechanism ensures a more uniform and concentrated force distribution across the material, resulting in efficient crushing. The double toggle crusher is known for its ability to process hard and abrasive materials with a higher reduction ratio, making it ideal for both primary and secondary crushing applications.
Hydraulic Jaw Crushers
Hydraulic jaw crushers incorporate advanced hydraulic technology to control the jaw’s movement. Unlike traditional mechanical systems, these crushers use hydraulic cylinders to adjust the crusher’s setting and to provide overload protection. The hydraulic system allows for precise control over the jaw movement, enabling adjustments to the crusher’s discharge opening with minimal effort. This feature is particularly beneficial for operations requiring frequent changes in material size or for clearing blockages efficiently, enhancing operational safety and productivity.
Mobile Jaw Crushers
Mobile jaw crushers are distinguished by their mobility, enabling them to be moved close to the material or site of operation. These crushers are mounted on tracks or wheels and can be easily relocated around a site or between sites. The mobility of these crushers reduces the need for transporting material to the crusher, thus lowering operational costs. Mobile jaw crushers are equipped with direct drive systems and advanced control technologies, optimizing performance for various applications, from demolition and recycling to mining and quarrying.
Blake Jaw Crushers
Blake jaw crushers, also as double toggle jaw crushers, are characterized by the position of the pivot of the swing jaw, which is located at the top of the machine. This design allows for a larger feed size and a higher capacity, making it suitable for primary crushing. The motion of the swing jaw in a Blake crusher is predominantly vertical, which provides a compression action on the material. This vertical movement of the movable jaw plate is more efficient at reducing large, hard materials into smaller pieces, offering a higher reduction ratio and better uniformity of the product size.
Dodge Jaw Crushers
Dodge jaw crushers have a swing jaw fixed at the lower position, creating a unique action for crushing material. This design allows the jaw to move up and down, providing a compressing action that is effective for softer materials or for applications where precise product sizing is not critical. The design of the Dodge jaw crusher provides a crushing action that minimizes wear on the jaw plates, making it suitable for applications where abrasive materials are not the primary focus.
Stationary Jaw Crushers
Stationary jaw crushers are designed for fixed-site operations where mobility is not required. These crushers are typically used in mining, quarrying, and large-scale industrial applications, offering high capacity and robust construction to handle heavy-duty operations. The design of stationary jaw crushers focuses on durability and efficiency, with features that accommodate large feed sizes and high throughput, making them an optimal choice for permanent installations.
Track Mounted Jaw Crushers
Track mounted jaw crushers combine the benefits of mobile crushers with the stability and high capacity of stationary models. These crushers are mounted on heavy-duty tracks, allowing for easy movement within a site or between locations. The design of track mounted crushers focuses on flexibility and efficiency, providing advanced features that enhance productivity and performance for a wide range of applications, including aggregate production and recycling.
PEX / PE Jaw Crushers
PE and PEX jaw crushers have diverse roles in the breaking down of rocks and ores. PE crushers, often chosen for primary crushing jobs, are built strong enough to take in big chunks of materials and break them down efficiently. With PE crushers, you can expect a high volume of reduction. PEX crushers, however, shine when it comes to grinding down the already crushed material even more in secondary or tertiary crushing, giving a fine and uniform end product. What’s great about both PE and PEX crushers is their tough build and straightforward design, making them flexible enough to crush all sorts of materials. These machines are, like the Swiss army knives of the mineral processing world—reliable, easy to handle, and ready for a variety of tasks.
For pricing details of various jaw crusher types, read Jaw Crusher Price: A Comprehensive Guide for Buyers.
Selecting the Right Jaw Crusher for Your Mineral Processing Project
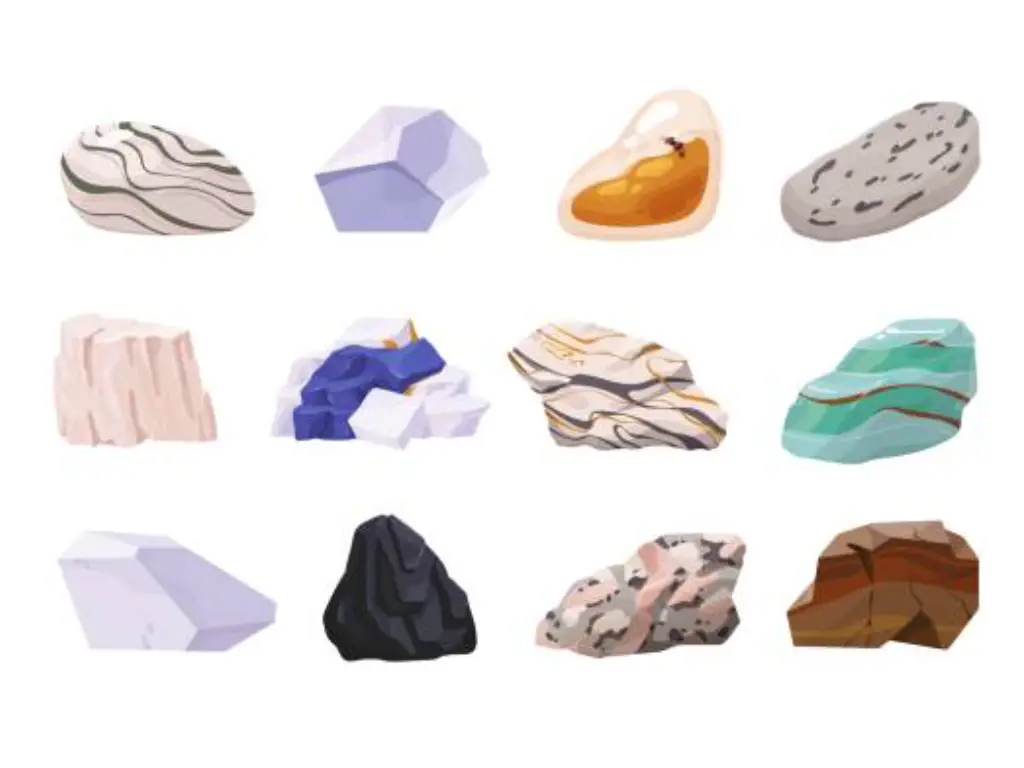
Check Out Material Characteristics
- Hardness
- Abrasiveness
- Size of raw material
Final size you're aiming for Crushing
- Final size requirements
- Reduction ratio
Understand Application Requirements
- Primary crushing vs. secondary/tertiary crushing
- Specific needs of the mineral processing project
Consider Operational Needs
- Mobility (site-to-site transport)
- Adjustability (changing product size)
- Volume of material to be processed
Evaluate Crusher Types
Type of Jaw Crusher | Best Suited for Ores | Why Suitable |
---|---|---|
Single Toggle | All types, gold, copper, large quartz rocks | Efficient crushing of large-sized hard ores |
Double Toggle | Hard and abrasive, iron ore, chromite, diamond-bearing rock | Powerful crushing action for very hard and abrasive ores |
Hydraulic | Varied, nickel, tin, and various hard ores; sticky clay ores | Adjustable and precise, good for ores requiring careful handling |
Mobile | All types, limestone, sandstone, for on-site processing needs | Mobility allows for direct processing at extraction sites |
Blake | Large, hard, massive sulfide ores, large phosphate rocks | High capacity suitable for robust primary crushing of large ores |
Dodge | Softer and smaller, coal, gypsum, soft shale | Effective for softer materials with a gentle crushing action |
Stationary | All types, iron ore, granite, and high-volume quartz | Ideal for large-scale operations requiring continuous, high-capacity crushing |
Track Mounted | All types, gold, silver, and portable ore bodies | Combines mobility with high capacity, suitable for mining operations with changing locations |
PEX / PE | All types, copper, zinc, small to medium gold ore bodies | Good for precise size reduction in secondary/tertiary crushing stages |
Factor in Production Capacity
- Required throughput
- Efficiency under specific operational conditions
Account for Maintenance and Operational Costs
- Durability and wear resistance of components
- Ease of maintenance and repair
Compliance with Environmental and Safety Standards
- Dust and noise control
- Safety features for operators
Conclusion
Jaw crushers are absolutely vital in the mining world, helping us break down raw materials into something we can actually use. With all the different kinds of jaw crushers out there, you’re sure to find the perfect one for the job, whether you need the tough single toggle or Blake crushers or the adaptable, on-the-go track mounted versions. Picking the best jaw crusher is super important and means you’ve got to know your stuff about the materials you’re dealing with, what your site can handle, and what you’re aiming to achieve with your project.
Picking JXSC as Your Trusted Mineral Processing Equipment Supplier
Opting for JXSC as your go-to for mineral processing kit means teaming up with a name that’s solid in the biz. We’re all about top-notch quality, fresh thinking, and making sure things run like a dream. JXSC rolls out a whole lineup of gear that’s cut out for the mixed bag of jobs the mineral processing world throws at you. We’re not just about jaw crushers; our know-how runs the gamut of the processing line, with smart setups crafted to crank up output and streamline your workflow. Whether it’s tough-as-nails primary crushers or all-around mineral processing plants, JXSC’s gear is all about custom builds, sturdy design, and keeping things humming while keeping the upkeep easy on your pocket. Choosing us, you nab way more than just gear—you snag a full-on ally that’s dialed into making your project shine.