- Home
- Blog
- Equipment Info
- Simple Guide: How Does a Jaw Crusher Work?
What is the Crushing Process?
The crushing process is a critical stage in converting huge stones, bulky materials into smaller, more manageable sizes for various applications in industries like mining and construction. This intricate process can be broken down into several key stages, each with its specific objectives and equipment. Let’s explore these stages, including the typical feed size for each stage:
Crushing Stage | Objective | Equipment Used | Initial Feed Size | Size Reduction | Process Details |
---|---|---|---|---|---|
Primary Crushing | To reduce large and bulky materials to a manageable size. | Jaw Crusher | 500 mm to 800 mm | Reduced to about 125 mm to 150 mm. | Large chunks of material are fed into the jaw crusher where strong compressive forces break them down. |
Secondary Crushing | To refine the size of the materials from the primary crushing stage. | Cone Crusher, Impact Crusher | Usually between 125 mm and 150 mm | Further reduced to 20 mm to 40 mm. | The material from the primary crusher is fed into secondary crushers for a more uniform and finer size. |
Tertiary Crushing | To obtain even finer material suitable for specific requirements. | Fine Jaw Crushers, Cone Crushers | Typically, in the range of 20 mm to 40 mm | Reduced to between 1 mm and 10 mm. | Essential for producing fine aggregates like sand. |
Quaternary Crushing (if applicable) | To produce ultra-fine materials for specialized applications. | Vertical Shaft Impact Crushers, Specialized Fine Cone Crushers | Generally between 1 mm and 10 mm | Achieves particle sizes of less than 1 mm. | Utilized for specialized, high-quality applications requiring extremely fine materials. |
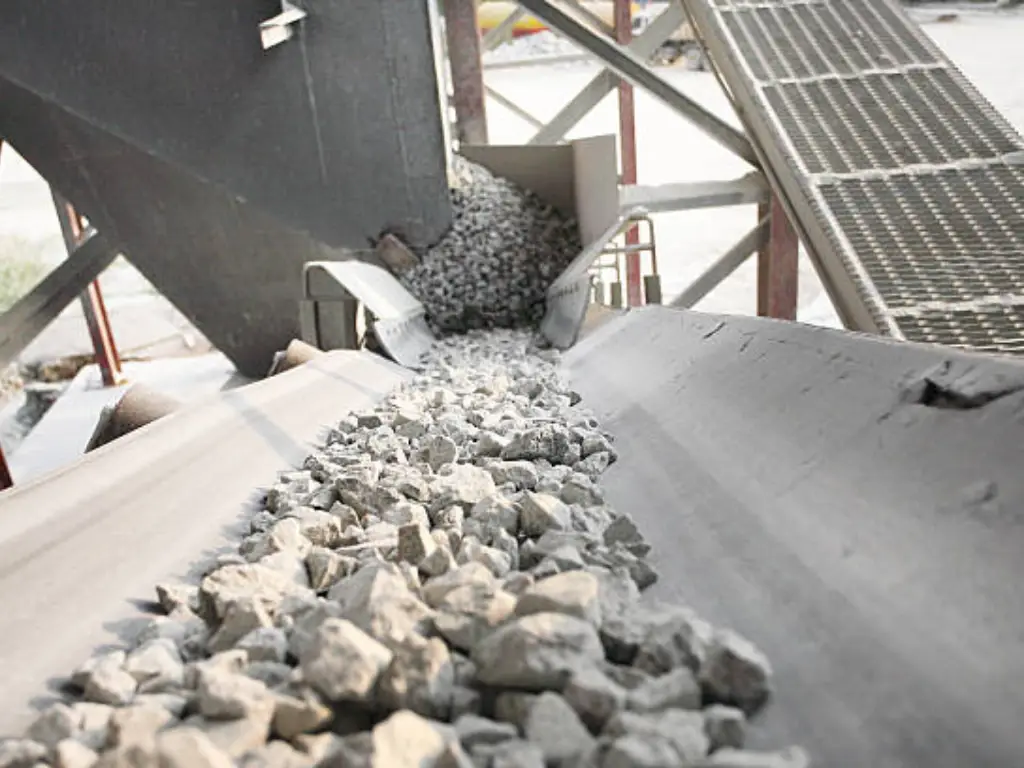
Each stage in the crushing process plays a vital role in the size reduction of the material. Starting from the initial feed, which can be as large as 800 mm, the process methodically reduces the size. Primary crushing tackles the largest pieces, breaking them down to a more manageable size for secondary crushing, which further refines the material into smaller stones. Tertiary, and sometimes, quaternary crushing stages are then employed to achieve the desired fine sizes. This step-by-step reduction ensures that the final product meets the specific requirements of the intended application, be it construction, manufacturing, or mineral processing.
What is a Jaw Crusher?
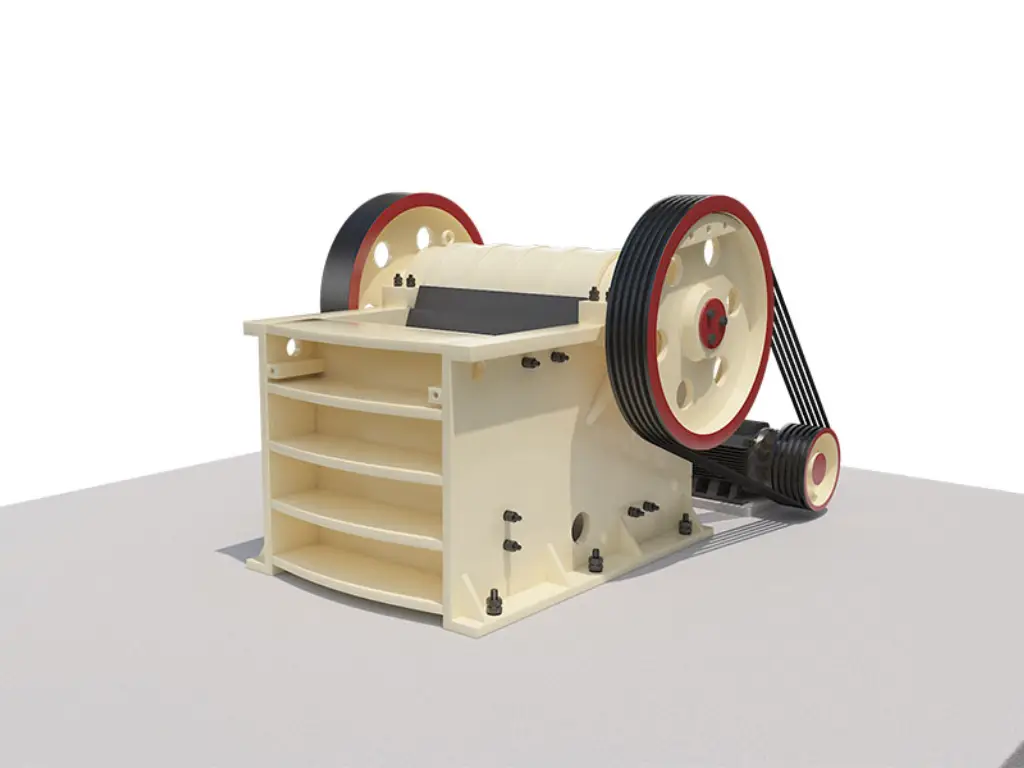
A jaw crusher is a robust, essential and rugged crusher used primarily in mining and construction for the initial crushing of large rocks and ore. Positioned at the start of the crushing process, it uses compressive force between two jaw plates to break down large materials into smaller, manageable pieces. Learn more about how jaw crushers compare to impact crushers in the article, Impact Crusher vs Jaw Crusher: What’s the Difference?.
Basic Components of a Jaw Crusher
When we talk about a jaw crusher, we are referring to a sophisticated piece of engineering. At its core, it has two main components: the fixed jaw and the movable jaw. The fixed jaw stays put, while the movable jaw, powered by an eccentric shaft, moves in a reciprocating motion. This motion brings the movable jaw closer to the fixed jaw, crushing the material in between.
Other crucial parts include the toggle plate, a safety device that serves as a fuse in the system, preventing damage to the crusher when uncrushable material is fed into it. Then there’s the eccentric shaft itself, which is the heart of the crusher, creating the necessary motion to crush the material. The jaw plates, made of hardened steel, withstand the tough impact of crushing large stones. And let’s not forget about the discharge opening at the bottom of the crushing chamber, which determines the size of the crushed material exiting the crusher.
How Does a Jaw Crusher Work?
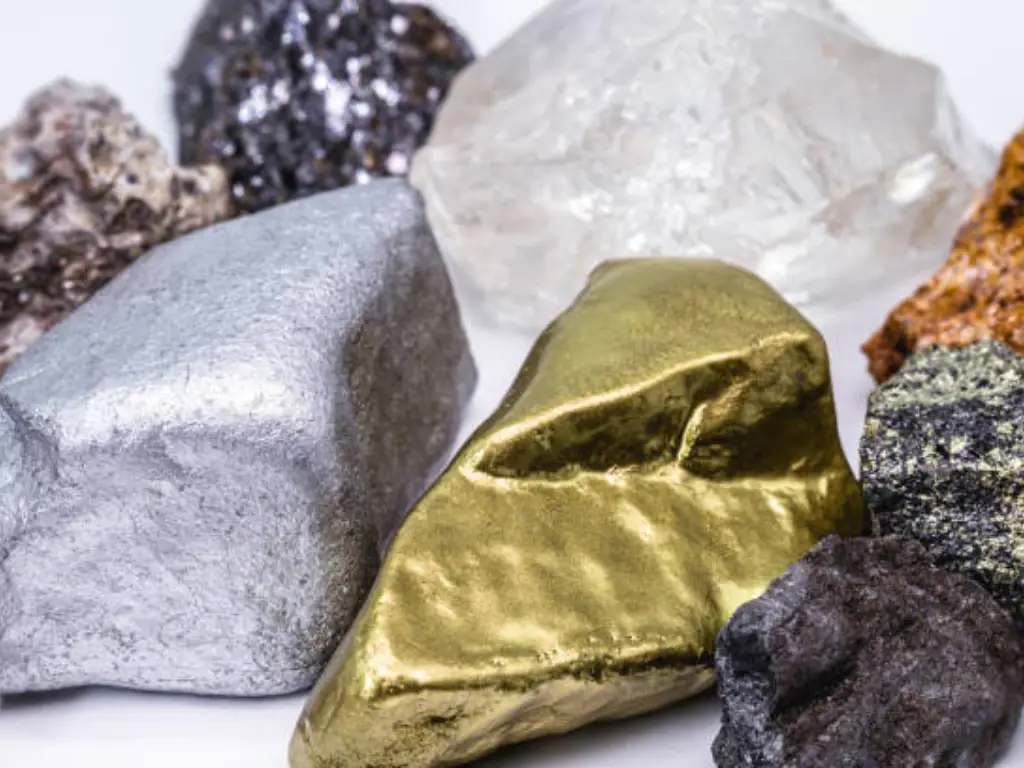
A jaw crusher operates by the movement of a movable jaw in relation to a fixed one to crush large rocks into smaller pieces. It does this by using a spinning shaft that makes the movable jaw move back and forth. When the movable jaw goes towards the fixed jaw, it squishes the stuff in between and breaks it into smaller bits. Then, this broken stuff leaves the crusher through an opening at the bottom called the crushing chamber cavity. How big this opening is and how the jaw moves decide how small the broken pieces will be in the crushing chamber.
To understand the process better, refer to An Easy Guide to Jaw Crusher Diagram.
Different Types of Jaw Crushers
There are mainly two types of jaw crushers: the single toggle and the double toggle (or Blake crusher). The single-toggle jaw crusher features a moving jaw suspended on the eccentric shaft. It’s known for its efficiency in crushing but tends to be more susceptible to wear because of the high motion of the jaw. On the other hand, the double-toggle jaw crusher, which has two toggles and a separating pitman arm, offers more movement to the lower part of the jaw. It’s known for its ability to crush tougher materials, including hard stones and abrasive materials, making it a popular choice in the mining industry.
These types cater to different needs and materials. The choice between a single or double toggle jaw crusher depends on the nature of the task, the size of the feed material, and the required size reduction. For large, heavy-duty operations, a double-toggle jaw crusher is often the go-to. For smaller, less intensive tasks, a single toggle might be more appropriate.
How Crushing Forces are Applied
In jaw crushers, the crushing force is generated by the movement of the movable jaw plate towards the fixed jaw plate. This force is a result of the mechanical pressure created by the eccentric shaft and transmitted through the toggle plate. The interesting thing is how these forces are applied to the material. The crushing force is not uniform. It’s highest at the point where the material is largest, and the jaw plates are closest together (near the top of the crushing chamber). This is where the most intense crushing happens.
The force decreases as the material moves down the chamber, getting smaller and smaller until it’s sufficiently crushed to pass through the discharge opening. The variation in force throughout the chamber ensures efficient crushing and contributes to the versatility of the jaw crusher in processing a wide range of materials.
Design Features of Jaw Crushers
Jaw crushers include several key design features:
- Deep Crushing Chamber: Enhances feeding capacity and overall throughput.
- Steep Nip Angle: Ensures effective material compression for better crushing efficiency.
- Adjustable Discharge Opening: Allows control over the size of the output material.
- High Manganese Steel Jaw Plates: Offer durability and wear resistance.
- Replaceable Liners: Protect the crusher and extend its lifespan.
Material Handling in Jaw Crushers
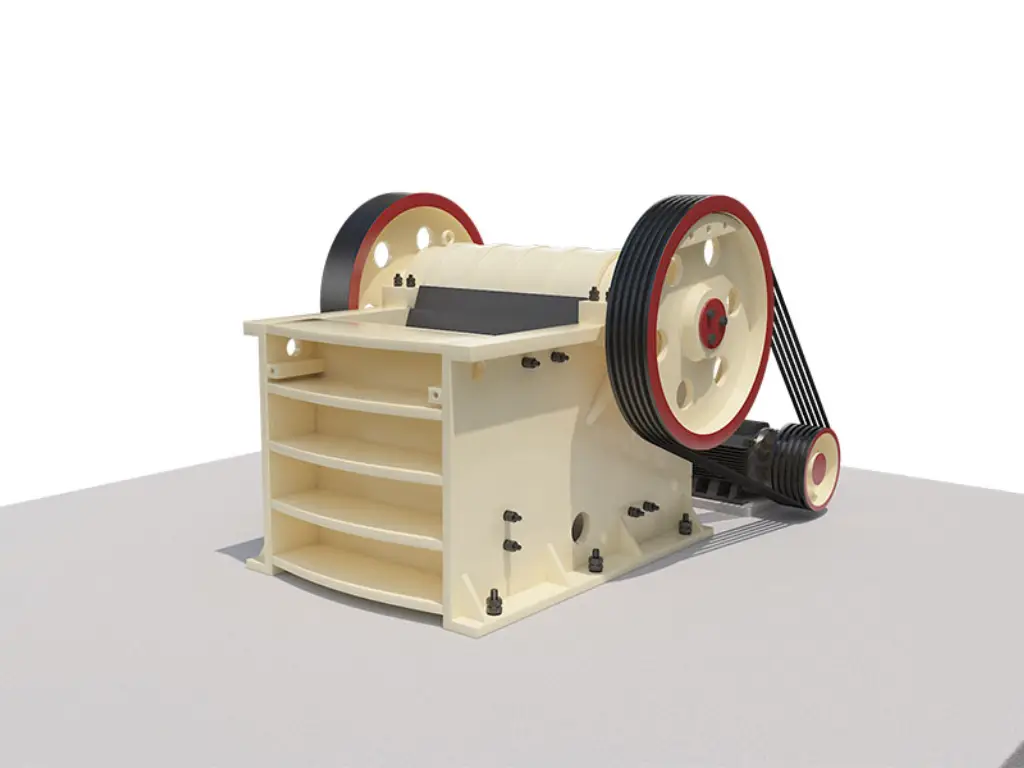
Jaw crushers are really handy machines that can handle all sorts of materials. Let’s look at what they can do:
- Hard Rocks and Ores: They’re great with tough stuff like granite and basalt.
- Softer Minerals: Got something like limestone? No problem, it’s softer and easier to crush.
- Metallic Ores: They can take care of metals like iron, copper, and gold ores too, making them smaller for further steps.
- Construction Materials: Need to recycle concrete and asphalt from building sites? Jaw crushers are perfect for this.
- River Pebbles and Gravel: These are common in outdoor designs and construction, and jaw crushers handle them well.
- Quartz and Glass: Whether it’s for industrial use or recycling, these crushers can break down quartz and glass.
- Coal and Chemicals: In places where coal and certain chemicals need to be smaller for better use, these crushers do the job.
This wide range of uses shows how flexible jaw crushers are. They can deal with different kinds of materials, whether they’re hard, soft, big, or small. That’s why they’re essential in so many different fields.
Maintenance and Care of Jaw Crushers
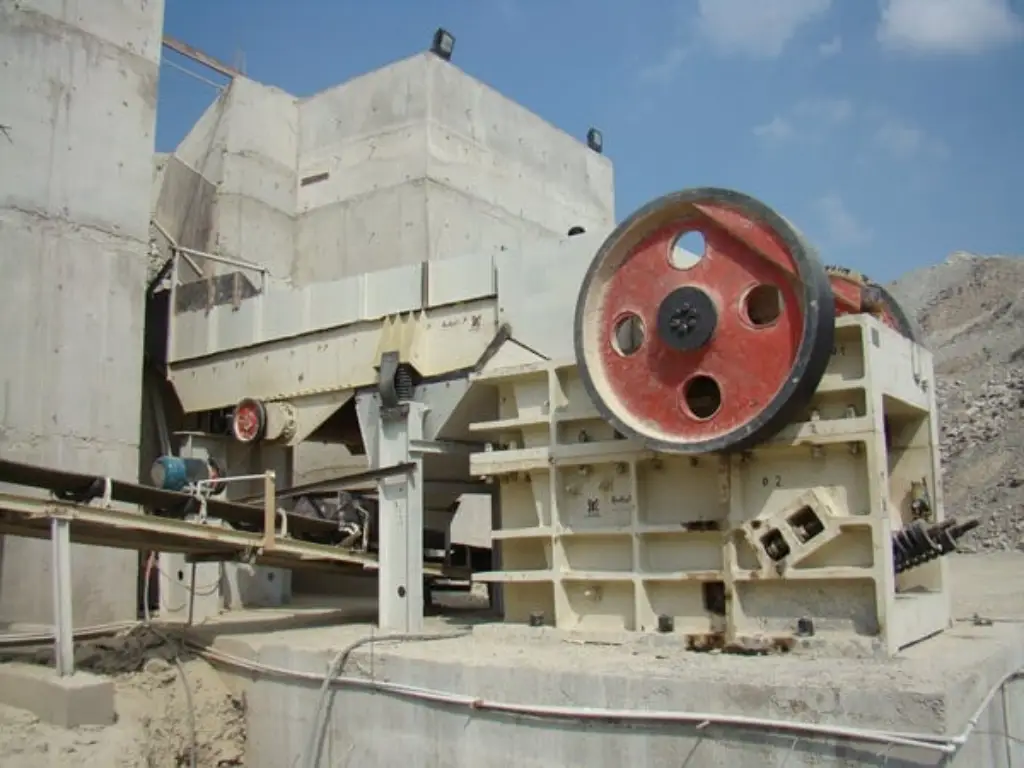
Keeping your jaw crusher in great shape is key to ensuring it works well and lasts a long time. It’s all about regular checks and updating parts that wear down, like the jaw plates and toggle plates. It’s super important to keep all the moving parts, especially the bearings, well-lubricated to avoid wear and tear.
It’s also smart to keep an eye on the size of the materials coming out. This can tell you a lot about when it’s time to tweak or replace parts due to wear. A clean and well-maintained jaw crusher doesn’t just last longer; it also works more effectively. So, taking good care of your jaw crusher is a must, especially if you’re in the mining or construction industry. This kind of attention to your crusher will definitely pay off by making it a reliable part of your work.
Common Problems and Troubleshooting
In the operation of jaw crushers, challenges such as jaw plate wear significantly impair efficiency, necessitating timely replacement when discharge sizes increase. Blockages, often caused by sticky or wet materials, require consistent cleaning and careful material feeding to prevent. Abrupt operational stops demand immediate inspection for overloaded feeds or mechanical faults. Regular maintenance is crucial for early problem detection and resolution, maintaining operational continuity.
Where to Find the Best Crushers for Your Projects?
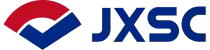
Engage with JXSC, a distinguished entity within the realm of extraction and industrial mineral operations, for pre-eminent jaw crushers. These devices are capable of meticulously transforming voluminous materials into granular or pulverized forms, boasting capacities that span from 1 to an impressive 1000 metric tons per hour. What sets JXSC apart is their bespoke approach to the configuration of feed apertures, adeptly addressing the heterogeneous demands prevalent across quarrying, metal processing, and ancillary industries. Accumulating nearly four decades of specialized experience, JXSC’s acclaim stems from furnishing effective and sturdy mineral processing apparatus. They have consummated in excess of 1000 mining ventures, adeptly dealing with upwards of 40 distinct ores and minerals. Their international presence, with apparatus deployed across no fewer than 40 countries and territories, attests to their consummate expertise and steadfast reliability in this sphere.
Conclusion
In the world of mining, jaw crushers are absolutely essential. They transform big rocks into smaller pieces, perfect for a variety of uses. Understanding how these crushers work, their types, and how to keep them running smoothly is crucial for any project. Choosing the right jaw crusher is more than just completing a job; it’s about working efficiently and saving time and money in the long run. Whether you’re an engineer, a mine owner, or providing specialized mining services, knowing your way around jaw crushers is key. This knowledge lets you make smart choices that really benefit your work.