- Home
- Blog
- Mineral Solution
- Grinding in Mineral Processing: Key Equipment and Technologies Overview
- mmldigi
Grinding in Mineral Processing: Key Equipment and Technologies Overview
What is Grinding in Mineral Processing?
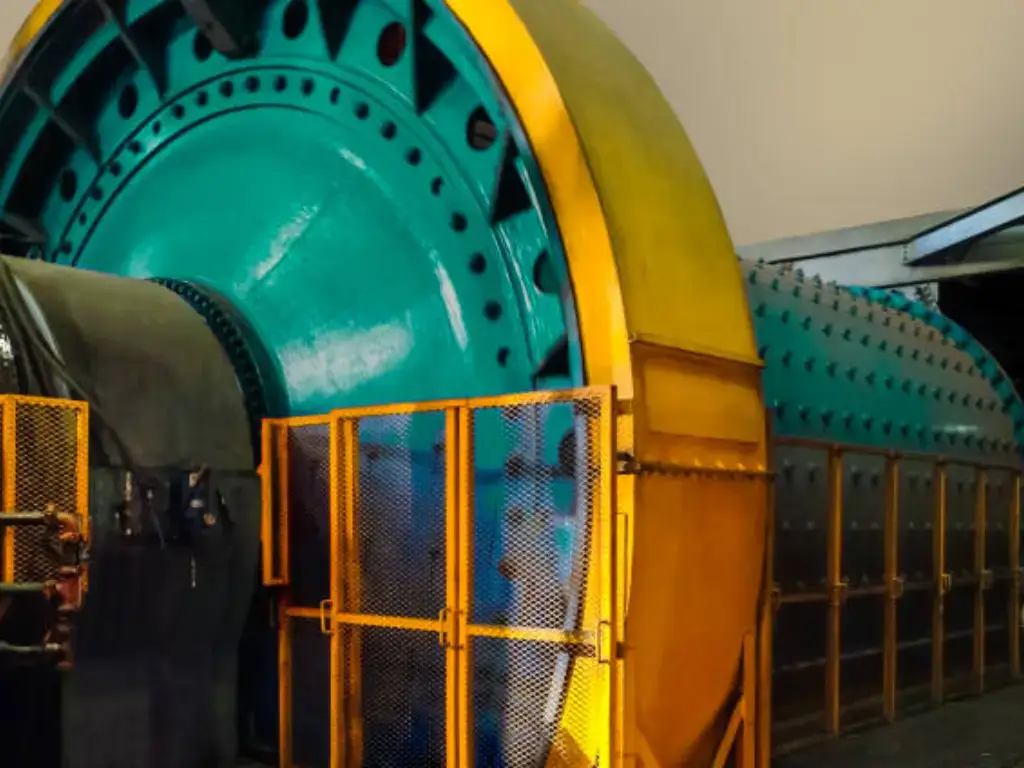
Wet vs. Dry Grinding in Mineral Processing
Criteria | Wet Grinding | Dry Grinding |
---|---|---|
Working Principle | Slurry with water is used for lubrication and cooling, reducing friction. | No water involved, relies on air cooling and abrasion. |
Equipment | Wet grinding mills often require additional infrastructure like pumps and thickeners. | Dry grinding mills can operate with fewer accessories but may need dust collection systems. |
Mineral Suitability | Suitable for minerals that produce slurries like copper, gold, and iron. | Ideal for materials prone to hydration reactions like limestone, coal, and cement. |
Application Areas of Grinding Machines
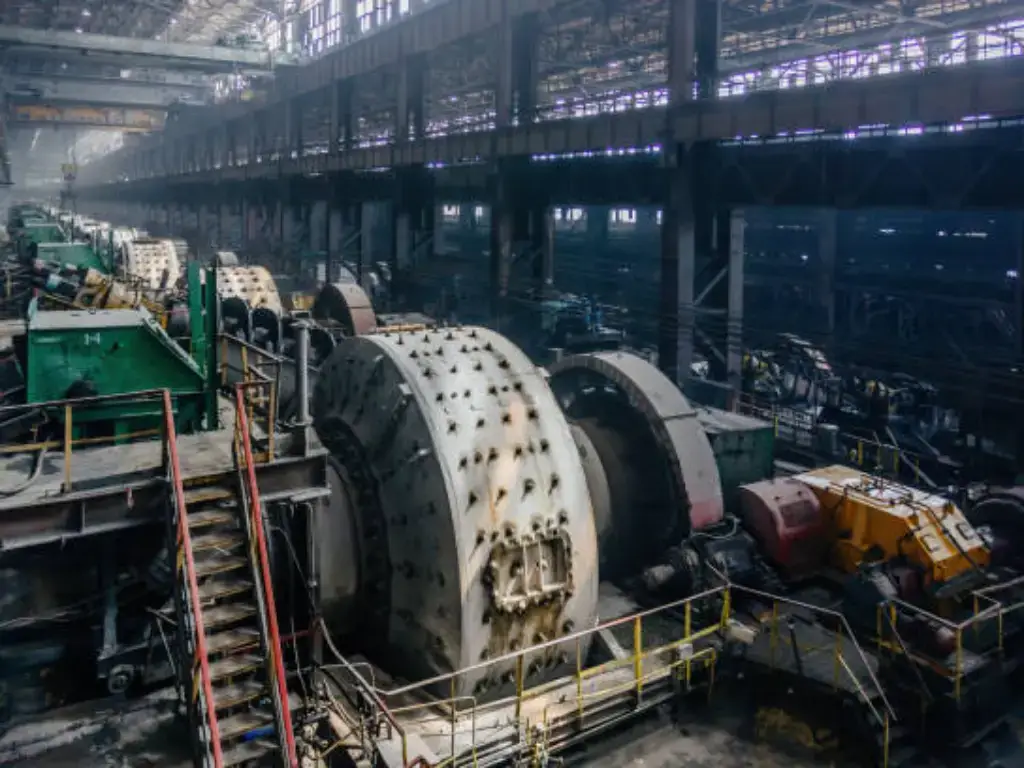
Different Types of Mills for Grinding in Mineral Processing
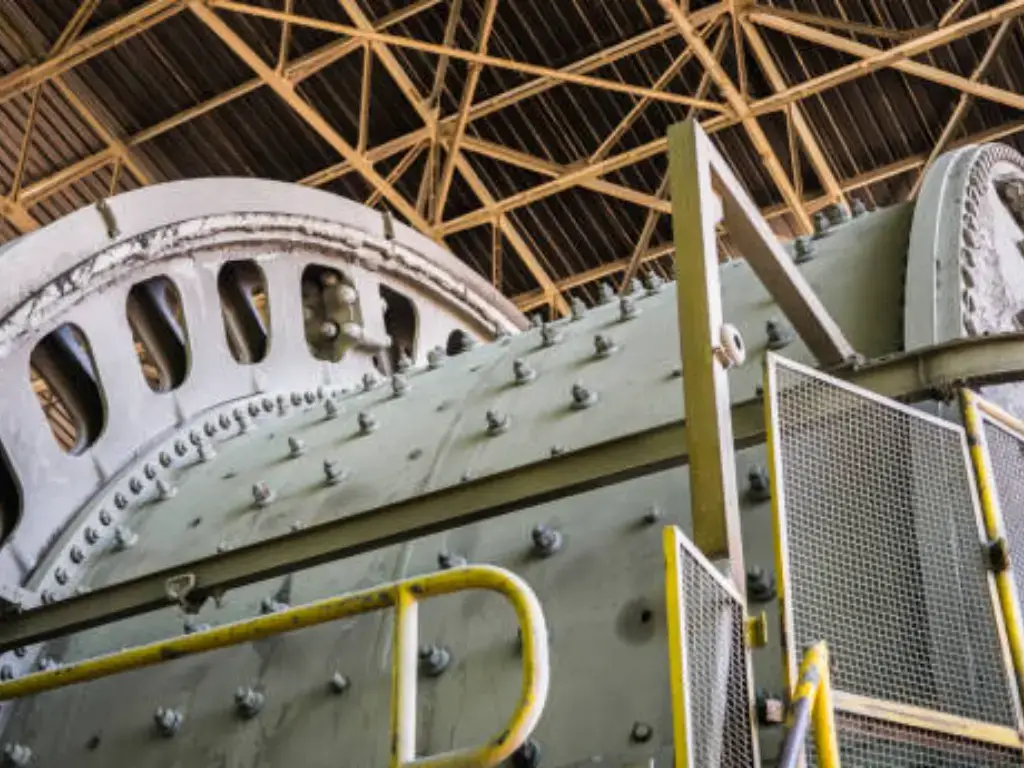
Rod Mill
Ball Mill
Sag Mill
AG Mill
What Are The Factors To Consider When Choosing Grinders?
Future Trends in Grinding Technologies and Equipment
Conclusion
In conclusion, grinding is still an essential element in achieving mineral processing success. It enables the release of valuable minerals from the ores so that other extraction methods can easily be carried out. Whether using ball mills, SAG mills, or any other grinder, improving the grinding process can significantly enhance the recovery rate and decrease expenses. As trends of the future are headed towards automation, energy conservation and use of advanced materials, the importance of grinding technology in the industry will continue to increase.
JXSC's Grinding Mills: Designed for Your Specific Needs
FAQs
Operators should wear protective gear, regularly inspect equipment for wear, and ensure proper ventilation in areas where dust is generated, particularly during dry grinding operations.
Regular maintenance includes checking liners for wear, inspecting bearings, ensuring the alignment of cylinders, and replacing worn grinding media. Periodic vibration analysis is also crucial for preventing equipment failures.