- mmldigi
Preface
The processing of oxidized gold ore is a challenging and complex process that needs a lot of expertise in the physical and chemical characteristics of the ore and the available technology. As technology improves the techniques used in the extraction and beneficiation of gold ores have improved to become more efficient and less damaging to the environment. This guide will seek to explain in detail the various steps that are involved in the beneficiation of oxidized gold ore and the equipment and technology that is used in the process. This guide will be useful for both experienced miners and those who are just entering the world of gold ore processing.
What is Oxidized Gold Ore?
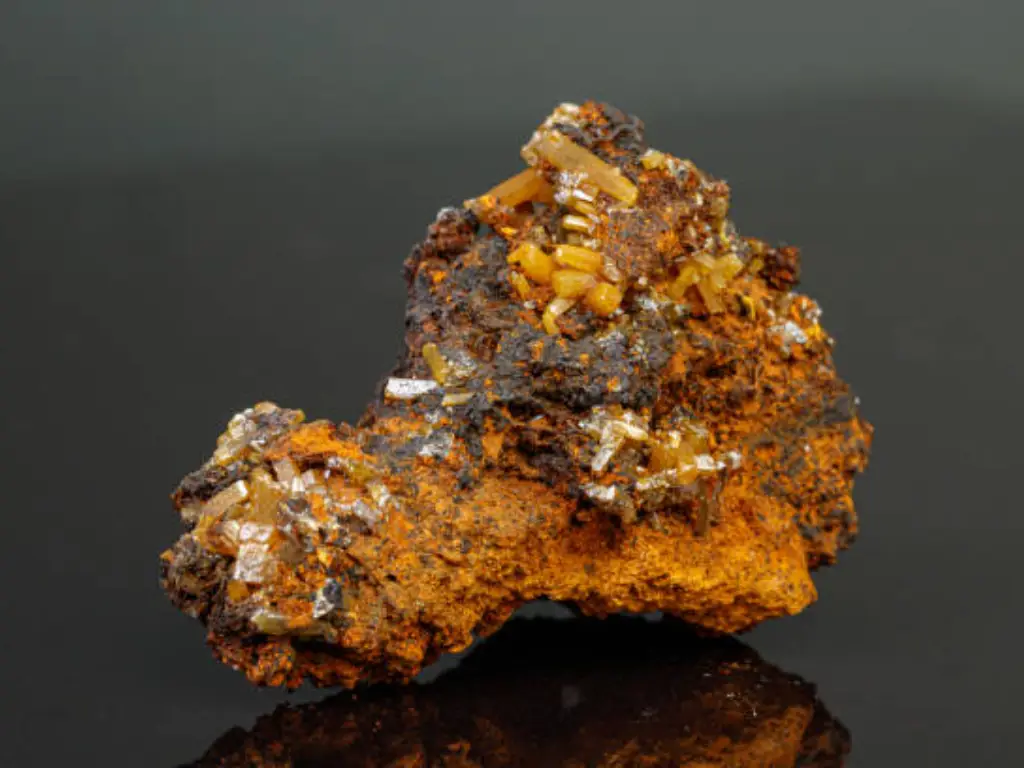
Oxidized gold ore is a kind of gold ore that has been chemically transformed through oxidation, which is the process of reacting with oxygen and water for a long time. This process converts sulfide minerals to oxides and hydroxides and the product is usually porous and friable. Oxidized gold ores are relatively easier to treat using cyanide leaching than the sulfide ores because the oxidation process reduces the size of the sulfide matrix and liberates the gold particles. In addition to cyanide leaching, oxidized gold ores can also be treated using gravity separation methods, view Comprehensive Overview of Gravity Separation Method for Gold Mining to get more information. These ores are usually composed of gold in the native state and also in combination with iron oxides and thus can be processed by different methods of beneficiation and extraction.
Applications of Oxidized Gold Ore
● Jewelry Manufacturing: e. g. , making beautiful jewelry and ornaments.
● Electronics Industry: e. g. , manufacturing high performance electronic parts and connectors.
● Investment Products: e. g. , production of gold coins and bars for investment.
● Medical Devices: e. g. , developing artificial limbs and diagnostic equipment.
● Aerospace Industry: e. g. , fabrication of vital aerospace parts that need high conductivity and resistance to corrosion.
Complete Oxide Gold Ore Processing Process
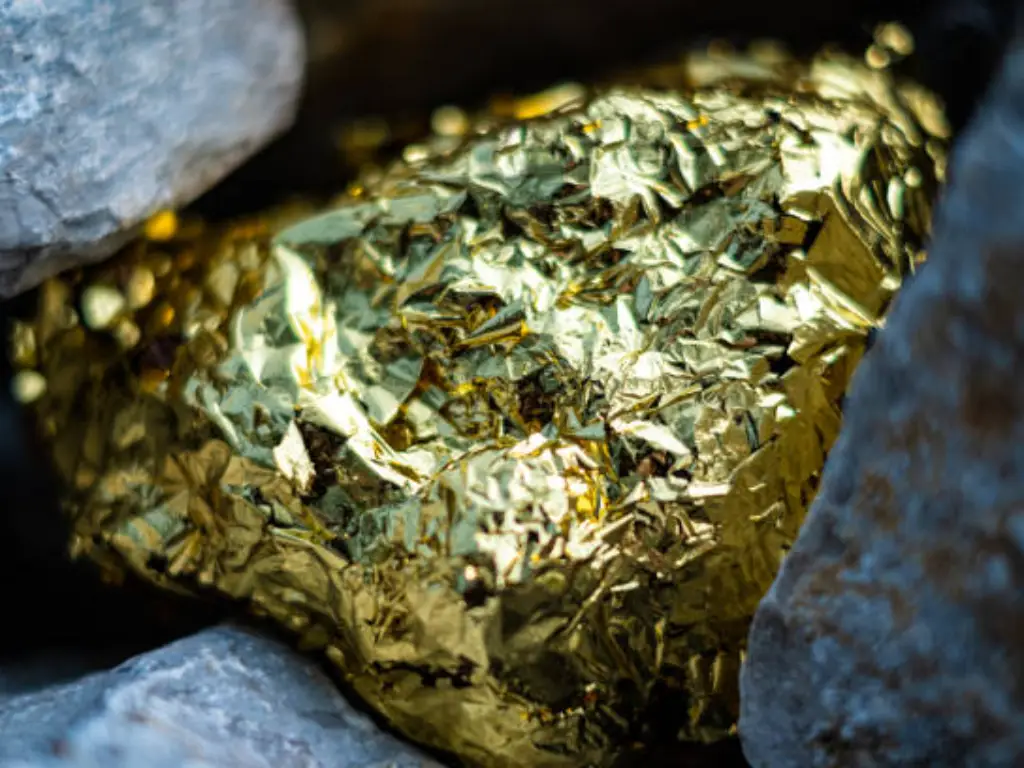
1.Crushing and Grinding
The first step in oxide gold ore processing is the mining of the ore itself, followed by the primary crushing of the gold containing rocks. This step is important because it helps to simplify the material for further processing in other steps. The smaller ore pieces are then transported to a ball mill after the first crushing. In the ball mill, the ore is crushed into fine particles to a size that will allow the gold particles to be easily released from the surrounding material. This fine grinding helps to increase the surface area of the gold ore, thus exposing it to the chemical extraction agents used in the subsequent steps.
2.Screening
After the ore has been crushed and ground to a fine powder, it is conveyed to a vibrating screen. This equipment is used to sort the ore particles by size so that only the right size of particles proceeds to the next step of the process. The vibrating screen effectively sorts the particles and returns the larger ones to the ball mill for further grinding. This helps in making sure that all material is well crushed to the right size that will enhance the recovery of gold. Screening should be done properly to ensure that the next leaching process is efficient and effective.Visit our site to understand how classifying screening machines optimize the gold ore screening process.
3.Cyanide Leaching
In the cyanide leaching stage, the screened ore is taken to large tanks where a cyanide solution is added. This solution leaches the gold out of the finely powdered ore, converting it to a soluble gold-cyanide compound. The leaching tanks are fitted with agitators to enhance the mixing of the cyanide solution with the ore particles to enhance dissolution of gold. This process usually takes several hours, while the cyanide solution leaches gold out of the ore continuously, the aim being to dissolve as much gold as possible into the solution in preparation for concentration and recovery.
4.Thickening
The gold bearing solution from the leaching tanks is then pumped into a thickener where the gold bearing solution is thickened and the solids are allowed to settle at the bottom of the thickener. In this equipment, the solid particles are allowed to settle at the bottom thus making the density of the gold rich solution at the top to be higher. This thickening process is important as it helps to increase the density of the solution in order to ease its handling during the adsorption step. The settled solids or the tailings are also removed and treated at certain intervals of time. The thickener also increases the effectiveness of the entire gold recovery process by concentrating the gold solution.
5.Adsorption
The concentrated gold solution is then treated through activated carbon columns. Activated carbon has a large surface area and a high selectivity for gold, which enables it to selectively adsorb gold from the solution. When the solution passes through the columns, the gold particles stick to the carbon media and thus, are separated from the liquid. This adsorption process is very efficient and can recover a lot of gold from the solution as shown in the following equation. When the carbon is saturated with gold, it is taken out of the columns for other treatments to be made on it.
6.Desorption and Electrowinning
In the desorption stage, the gold adsorbed on the carbon from the adsorption columns is treated to release the gold into a concentrated solution. This is done by heating the carbon and then applying a chemical solution that will release the gold. The gold-rich solution is then taken to electrowinning cells where an electrical current is passed through it. This current deposits the gold onto cathodes and thus recovers it from the solution in the present case. Electrowinning is a very efficient process and the product obtained is very pure gold which can be further purified.
7.Smelting
The gold that is obtained from the electrowinning process is then subjected to smelting process in a smelting furnace. This high-temperature furnace melts the gold, so that it can be easily separated from other impurities and other metals. The molten gold is then cast into molds to make gold bullion bars. Smelting is important because it helps to ensure that the gold is in its pure form and ready for the market. The gold bars produced are weighed and checked for purity before they are forwarded to the last refining process.
8.Refining
The last step of refining is further melting and chemical processing to get the gold as pure as it can be. This process also helps to eliminate any remaining impurities and thus the gold produced is of the required standard. Refining can be done through several processes such as acid treatment, electro refining and other chemical processes. The result is gold that is 99. Concentrations of 99% pure or higher for sale in the market or for industrial use. The purified gold is then poured into bars, ingots or any other shape that is preferred.
9.Tailings Management
During the various processing stages, there is production of waste material referred to as tailings. Tailings management is the process of safely storing or disposing of this material so as to reduce the effects on the environment. This may involve building tailings dams where the tailings are contained in a basin or reprocessing the tailings to recover any remaining minerals. Appropriate handling prevents the tailings from polluting water or soil in the vicinity, complies with the environmental requirements, and minimizes the impact of the mining process on the environment.
Key Equipment for Oxidized Gold Ore Processing
Equipment | Features and Properties | Application in Processing Step |
---|---|---|
Crushers | Durable construction, high capacity, and efficient reduction of ore size | Used in the initial stage to break down large chunks of ore into manageable sizes for further processing. |
Ball Mill | Efficient grinding, adjustable particle size, robust design | Used in the grinding stage to achieve the desired fineness of the ore particles, enabling better liberation of gold. |
Shaking Tables | Precision gravity separation, adjustable settings, durable | Used in the gravity separation stage to concentrate gold particles based on density differences. |
Flotation Machines | High recovery rates, effective reagent distribution, easy to operate | Used in the flotation separation stage to collect gold particles by making them hydrophobic and allowing them to float. |
Magnetic Separators | Strong magnetic fields, selective separation, low energy consumption | Used in the magnetic separation stage to remove magnetic minerals, leaving behind non-magnetic gold-bearing material. |
Autoclaves | High pressure and temperature capabilities, effective oxidation | Used in the pre-treatment stage to break down refractory minerals and make gold more accessible for extraction. |
Thickener Tanks | High capacity, efficient solid-liquid separation, low maintenance . | Used in the concentration and filtration stage to remove excess water from the slurry |
Filter Presses | High-pressure filtration, effective moisture removal, durable design | Used in both concentration and dewatering stages to further remove moisture from the concentrate. |
Activated Carbon Columns | High adsorption capacity, durable, easy regeneration | Used in the adsorption stage to capture gold-cyanide complexes from the solution. |
Smelting Furnaces | High temperatures, precise control, efficient refining | Used in the refining stage to purify the gold concentrate and achieve high purity levels. |
Lorem ipsum dolor sit amet, consectetur adipiscing elit. Ut elit tellus, luctus nec ullamcorper mattis, pulvinar dapibus leo.
How to Select Cutting-Edge Equipment?
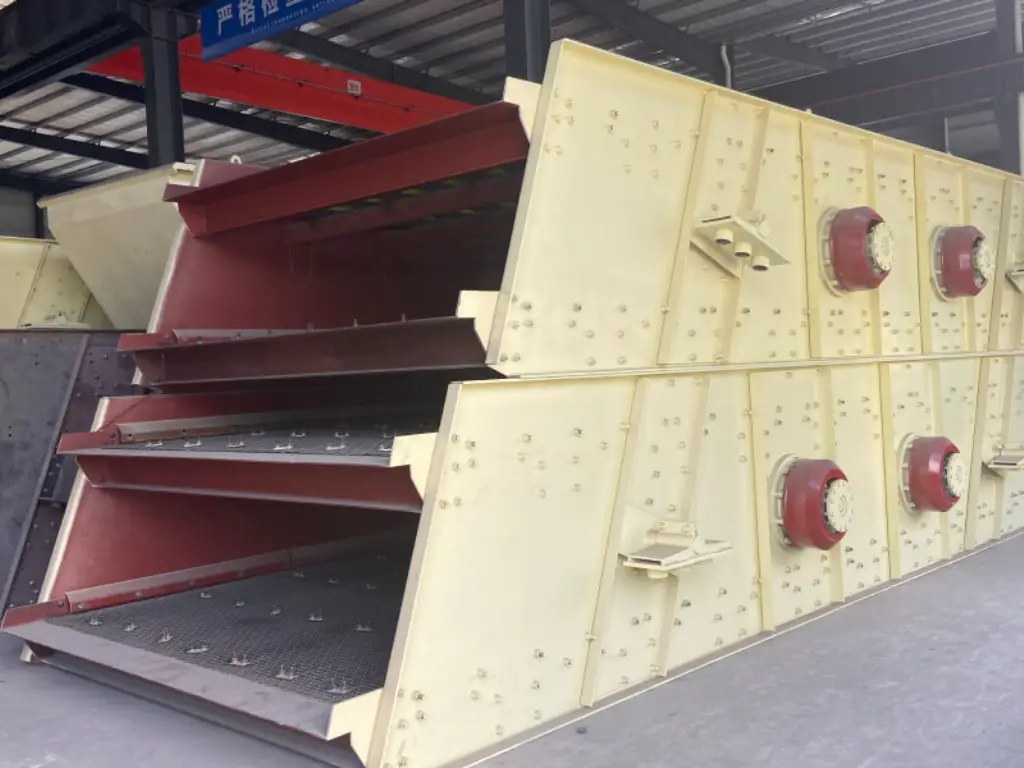
● Evaluate Ore Characteristics: The type of equipment to be used also depends on the mineralogy and particle size distribution of the ore. The specific characteristics of the ore are useful in selecting equipment that will yield the highest efficiency and recovery of the valuable minerals.
● Consider Processing Capacity: Make sure that the equipment will be able to process the required throughput to achieve the set production rate. The matching of the equipment capacity to the processing requirements eliminates the formation of bottlenecks and improves overall efficiency.
● Technology Compatibility: Select equipment that will complement the other systems and technologies used in the processing plant. Compatibility reduces operational interferences and makes it easier to switch from one processing stage to the other.
● Maintenance and Durability: Choose equipment that is durable and does not need frequent repairs and replacement, but will serve you for a very long time. Holding inventories of long-lived equipment decreases the time that is lost to equipment failure and repair, thus increasing productivity.
● Energy Efficiency: Choose equipment that uses less energy to cut on expenses and minimize the effects on the natural environment. Efficient machines are used in mining to ensure that the mining process is sustainable while at the same time achieving the best results.
● Vendor Support and After-sales Service: Another factor to look at is the technical support and after-sales service from the equipment vendor. Availability guarantees the fast solving of problems and uninterrupted work.
To explore how different screen designs influence the sorting process, check out Vibrating Screen Design Demystified: Types and Benefits.
Problems and Solutions for Processing Oxidized Gold Ores
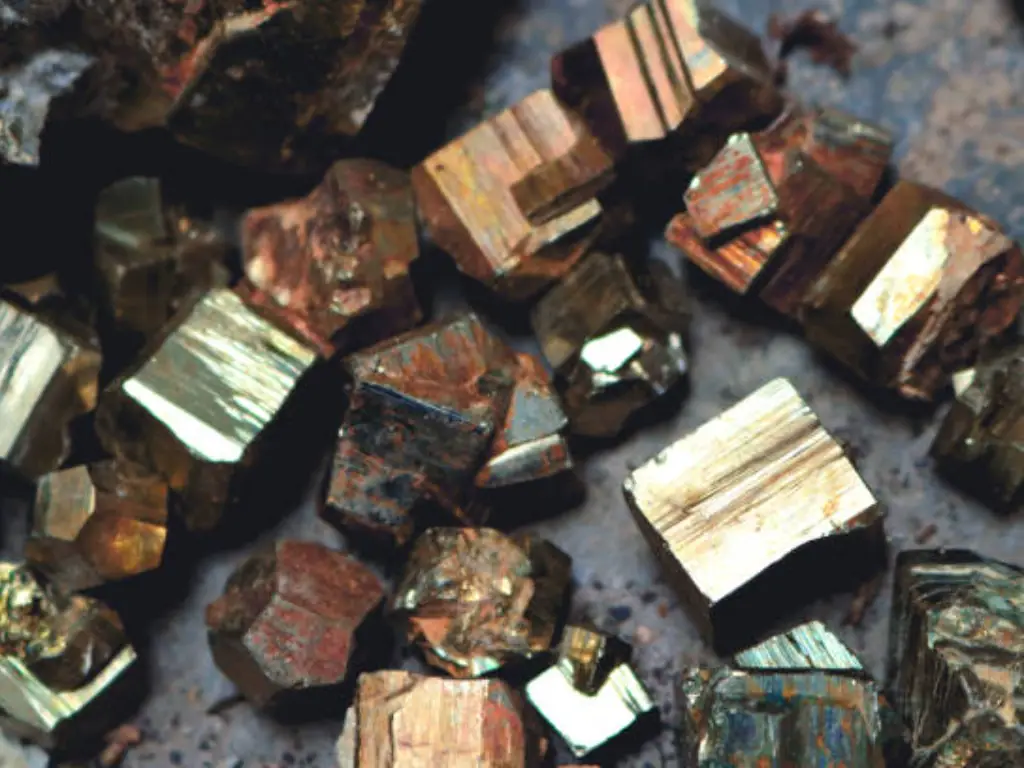
● Low Gold Recovery Rates: Oxidized gold ores have low gold recovery rates as some of the gangue minerals interfere with the cyanide leaching of gold from the ore This can be resolved by using beneficiation equipment such as the centrifugal concentrators to enhance the concentration of the fine gold particles. Also, the improvement of the cyanidation process that is more appropriate for the type of ores available in the gold deposits can increase the recovery rate. The leaching parameters should be frequently monitored and adjusted in order to maximize gold recovery, particularly sodium cyanide concentration. The constant improvement of technology in the beneficiation processes can also lead to increased recovery rates.
● Refractory gold particles : Some oxidized ores have gold particles which are trapped in minerals like iron sulfide and arsenic sulfide and cannot be dissolved by cyanide. To overcome this problem, fine grinding and the use of flotation reagents can help in the liberation of the gold particles. These refractory particles can be well separated by the flotation process with high efficient reagents. In case of very refractory ores, biological oxidation method or pre-treatment with sulfuric acid to break up the mineral structure may be applied. These methods enhance the extraction process so that the gold is more accessible to the other stages of recovery such as heap leaching and carbon leaching.
● Environmental Concerns : The processing of oxidized gold ores is normally carried out with the help of hazardous materials like cyanide which is hazardous to the environment. To minimize such risks, proper waste management should be practiced and enough precaution should be taken to cover cyanide solutions. Another way to decrease the impact is to use less hazardous reagents for leaching, for instance, thiosulfate. The effluent and waste streams are checked regularly and the treatment systems are employed to mitigate the impacts of toxic chemicals on environmental requirements. The application of the best practices in environmental management minimizes the effects of gold processing on the environment while at the same time maximizing economic returns.
● Operational Costs : This is usually the case because of fine grinding and high reagent consumption which leads to high operating costs in the processing of oxidized gold ores. Some of the measures that can be employed to reduce the costs include the incorporation of energy efficient technologies in the grinding operations. More efficient reagents can also lead to lower costs and recycling them within the process is also beneficial. Cost control in the operations is supported by auditing and process improvement activities. Therefore, the efforts to find cheaper ways of processing without compromising the recovery rates can significantly affect the profitability in the case of gold ore beneficiation processes.
● Variations in the Proportion of Ores: Oxidized gold ores can be very diverse in composition and this leads to variation in the processing characteristics. To overcome this, it is required to carry out a mineralogical analysis of the ore before the processing stage. It is possible to increase the recovery and efficiency of the processing method by adapting it to the characteristics of the ore batch. The use of adaptive processing techniques that can be adjusted depending on the fluctuation of the ore will provide consistent results. This makes it possible to adjust the process as soon as possible to achieve high recovery rates regardless of the fluctuations in the ore.
Conclusion
The future of oxidized gold ore processing appears to be bright, as researchers continue to work on refining the process and minimizing the effects on the environment. Chemical methods are also expected to be improved as well as the incorporation of artificial intelligence in mineral processing to improve the accuracy of gold recovery processes. The adoption of cleaner technologies in the extraction process, including bio-leaching and extraction without the use of cyanide, will also define the future of the industry.
Thus, the necessity of the further development of the gold industry and the need to minimize its negative impact on the environment are still relevant. The future trends in oxidized gold ore processing will no doubt present new opportunities and challenges for the industry and will continue to push the industry towards more innovative and efficient solutions.
JXSC: Your Partner in High-Efficiency Gold Ore Processing
JXSC Mine Machinery Factory is one of the most reputable companies in the mining industry that was established in the year 1985. Established in 1985, JXSC has more than 30 years’ experience in mining equipment manufacturing, offering stone crushers, gravity concentration equipment, magnetic separators, etc. It provides full EPC solutions, including engineering consultation and mineral processing experiment, mine design, equipment installation and debugging. This guarantees that the JXSC equipment is durable and has high efficiency and is designed to suit the requirements of various mineral processing companies.
The company’s dedication to technological development and customer service makes JXSC stand out in the market. BV and ISO 9001 certifications are held by them, which ensures the quality of the manufacturing process. The company has established itself in over 60 countries by developing partnerships with mines, which proves its credibility and the global market’s confidence in their products. JXSC’s overseas engineers and installation teams are available to help with installation and commissioning of the equipment to guarantee the best performance. The commitment of the brand to after-sales service guarantees that clients get the best service in the shortest time possible, making JXSC a reliable partner for efficient gold ore processing.
FAQs
How does the mineralogy of oxidized gold ore influence the process of processing the mineral?
The mineralogy of oxidized gold ore defines the type of processing that is to be applied on the ore. Oxidized ores may contain minerals such as iron oxides which are beneficial to the cyanide leaching process since they counter the effect of sulfides on gold extraction. Other factors affecting the leaching process are porosity and permeability of the ore because the cyanide has to get into the ore to dissolve gold. Moreover, the presence of some minerals may affect the choice of extraction methods and the concentration of reagents required, which affects the effectiveness and cost of the process. It is important to know how gold is associated with the ore, for instance, with quartz sand or gangue minerals in order to determine the right beneficiation method.
What are the legal requirements for the processing of oxidized gold ore?
Some of the conditions that should be fulfilled when processing oxidized gold ore include environmental permits and legal requirements of the country, state, and federal laws on mining. Such regulations normally entail the provision of comprehensive environmental impact statements to evaluate the effects on the environment. There should be some measures to regulate wastes and emissions to the acceptable levels of water and air pollution. Other requirements include environmental compliance checks and reporting in addition to occupational health and safety measures for the workers who are engaged in the processing activities. Compliance with these regulations makes it possible to conduct the processing of gold mines in a sustainable and legal manner.
What measures should be taken to maintain the quality of gold extracted from oxidized ore?
There are several measures that are followed to ensure that the quality of gold extracted from oxidized ore is good. The quality control measures must be strictly followed during the entire processing chain from the extraction of the ore to the final refining. The quality of the ore and the processed material is maintained constant by taking samples and analyzing them often. Contamination is eliminated by using high purity reagents and equipment that has been cleaned well. The final stages of refining, smelting and chemical purification should be controlled to achieve the desired level of purity. Compliance with the set industry standards and the legal requirements also assist in determining the quality of the final gold product.