- Home
- Blog
- Equipment Info
- Anatomy of a Ball Mill: A Detailed Ball Mill Diagram
Introduction to Ball Mills
Balls mills are an important part of the gear in the mining and mineral processing industry, where they are utilized in the grinding stage of the crushing process. Comminution involves reducing the size of solid materials, and it consists of two main stages: breaking and grinding. Crushing is the primary phase in which the large particles are reduced into smaller ones that can be introduced into the grinding mills, including ball mills. Grinding, which is the second and final stage, reduces the particle size into even finer particles with the help of impact and attrition forces.
Alongside the mining industry, ball mills are also used in different sectors, such as cement production, for grinding clinker and other raw materials; ceramic manufacturing, for grinding and mixing ceramic powders, and paint production, for dispersing and homogenizing pigments and other ingredients. The multiple uses of ball mills is the main reason why they are so important in many industries. For a detailed explanation of ball mills, click What is a Ball Mill and How Does It Work? An In-Depth Explanation.
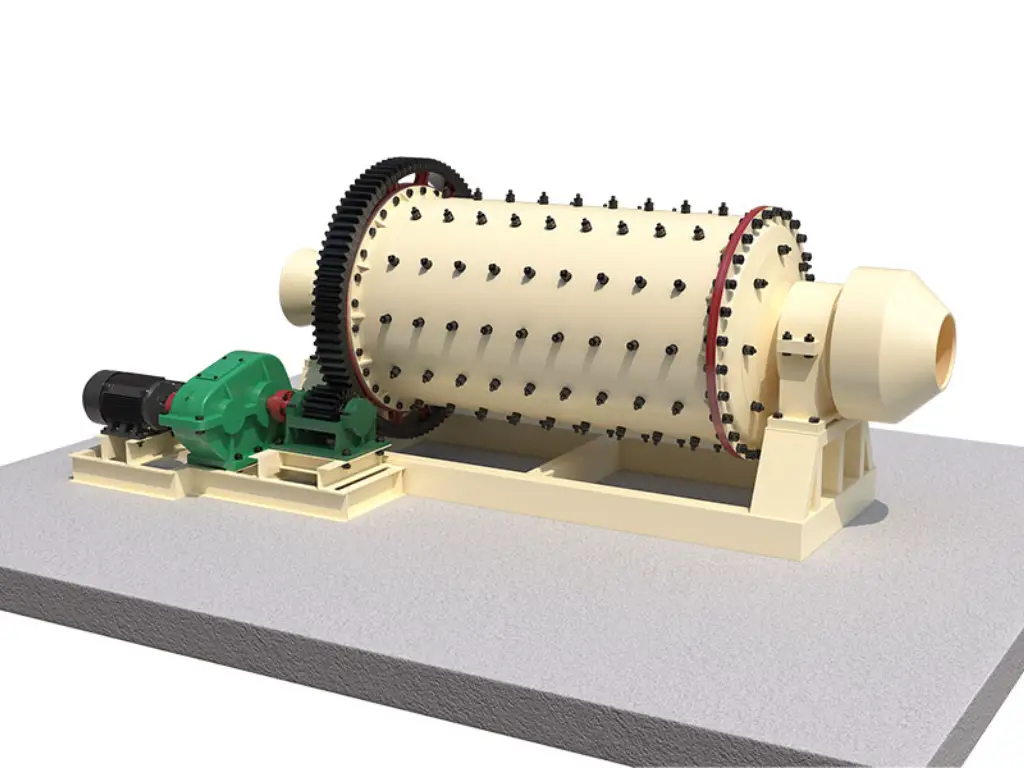
Working Principle of Ball Mills
Fragmentation mechanisms: impact and attrition
The grinding action in a ball mill is achieved through two primary fragmentation mechanisms: attrition and the impact. Impaction happens when the grinding media (balls or hard pebbles) bump into each other and with the material being ground. This leads to the fragmentation of the substance into pieces of smaller size. On the contrary, attrition is a process that results from the rubbing and the shearing of particles against each other as well as the mill’s shell that causes further size reduction.
Energy levels of grinding media
The energy levels of the grinding media is very important in the ball mill’s functioning. During the rotation of the shell, grinding media is lifted up the sides of the mill to a point where they fall back to the bottom of the mill. The higher the media is lifted and the harder that it crashes back down to the material being grounded, the more energy is imparted to the material. There are parameters like the diameter, volume and velocity of the grinding media which affect the energy level.
Rotation of the shell and base plate
Shell rotation of the ball mill is the very important element for grinding process. The shell is commonly mounted on a horizontal axis and rotates at a certain rate called the critical speed. The critical speed is the rotational speed at which the centrifugal force matches the gravitational force, causing the grinding media to stick to the mill’s shell rather than falling. Generally, ball mills are operated at the critical speed of the range 50-90% to attain the best possible grinding results.
Operation in Ball Mills
Cascade operation at different speeds
The operation of a ball mill can be classified into three distinct modes based on the rotational speed:
Low speed: rolling grinding balls without flight
At low speeds, the grinding media rolls along the bottom of the mill without being lifted up by the sides. This mode is characterized by low-impact forces and is ideal for light grinding or mixing applications.
Mixed mode (Cascade mode motion): partial rolling and partial flight
With an increase in rotation speed, the grinding media is lifted up the sides of the mill and then attaining a certain height before falling down. This mode of mixed motion, which is also known as cascade, is the one most commonly used for ball mills, as it gives an equilibrium between impact and attrition forces.
High speed: circular motion of balls with no fall
At very high speeds, the grinding media is carried around the mill’s circumference without falling down. This method, commonly called centrifuging, is not applicable for grinding as there is no impact or attrition going on.
Importance of rotation speed
The speed of ball mill rotation is a critical parameter which determines the grinding efficiency and the end product quality. The optimum speed will differ depending on the mill’s diameter, the size and density of the grinding media, and the material being ground. Operating at the proper speed guarantees that the grinding media will transfer the maximum amount of energy to the material and will not cause the excessive wearing of the mill’s components.
Feed and discharge of material
The ball mills can be operated either in batch or in the continuous mode. In the batch mode, a given amount of material is loaded into the mill and ground for a specific period and then discharged. In a continuous mode, material is fed continuously into one end of the mill and discharged from the other. The feed and discharge mechanisms, which include chutes, hoppers, and grates, are the most important component to have a consistent and controlled flow of the material through the mill.
Optimum speed for maximum size reduction
For the greatest particle size reduction, ball mills should be operated at their optimal speed. This speed is normally between 50-90% of the critical speed, which is dependent on the application and material to be ground. At the optimum speed, the grinding media falls down the shell of the mill at the highest point thereby generating the maximum impact force and the grinding process becomes efficient.
Construction of Ball Mills
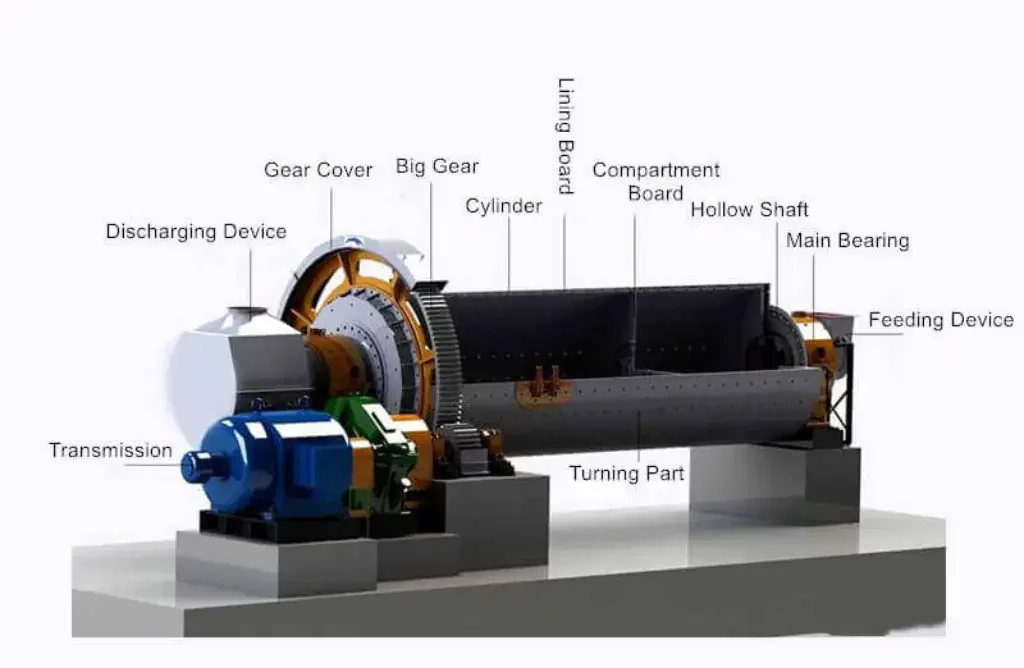
A ball mill consists of three main components: the shell, the grinding media (balls or pebbles), and the engine. The shell is constructed as a metal tube that is hollow inside and it is lined with wear-resistant materials like manganese steel or rubber. The grinding media can be made of high-chrome steel, ceramic, or rubber, but the choice depends on the application. Steel balls are the most common type of grinding media and they can be procured in a variety of sizes from 10 mm to 150 mm in diameter. The size of the balls is based on the size of the raw material and the desired final product size. Ceramic and rubber balls are used in processes where steel balls are unsuitable for contamination, e.g., in the production of ceramic raw materials and paint.
The lining of shell is a necessary part which is responsible for protecting the mill’s shell from the wear and tear induced by the impact and abrasion of the grinding media. Manganese steel, rubber and ceramic are the most commonly used types of lining materials. Manganese steel is famous for its high wear resistance due to its wide application in mining and mineral processing. Rubber Lining is used for wet grinding and is able to reduce the level of noise. Ceramic linings are applied in high-temperature applications or in cases when contamination from metal liners is an issue. The rotation of the mill is driven by the motor, the power of which is determined by the mill’s size and the grinding capacity.
Ball mills can be as small as lab-scale mills or as large as industrial mills with a diameter of up to 8 m. The mill’s capacity is dictated by its volume. The volume depends on both diameter and length. Generally, the length-to-diameter ratio of the mill, known as the L/D ratio, is between 0.5 and 3. Shorter mills are used for crushing coarse materials, while longer mills are utilized for grinding fine materials. The ball mill dimensions and capacity are determined based on the application, and the required throughput.
Discover the workings of these parts at Mastering the Ball Milling Method: Your Comprehensive Guide.
Factors Determining Ball Mill Efficiency
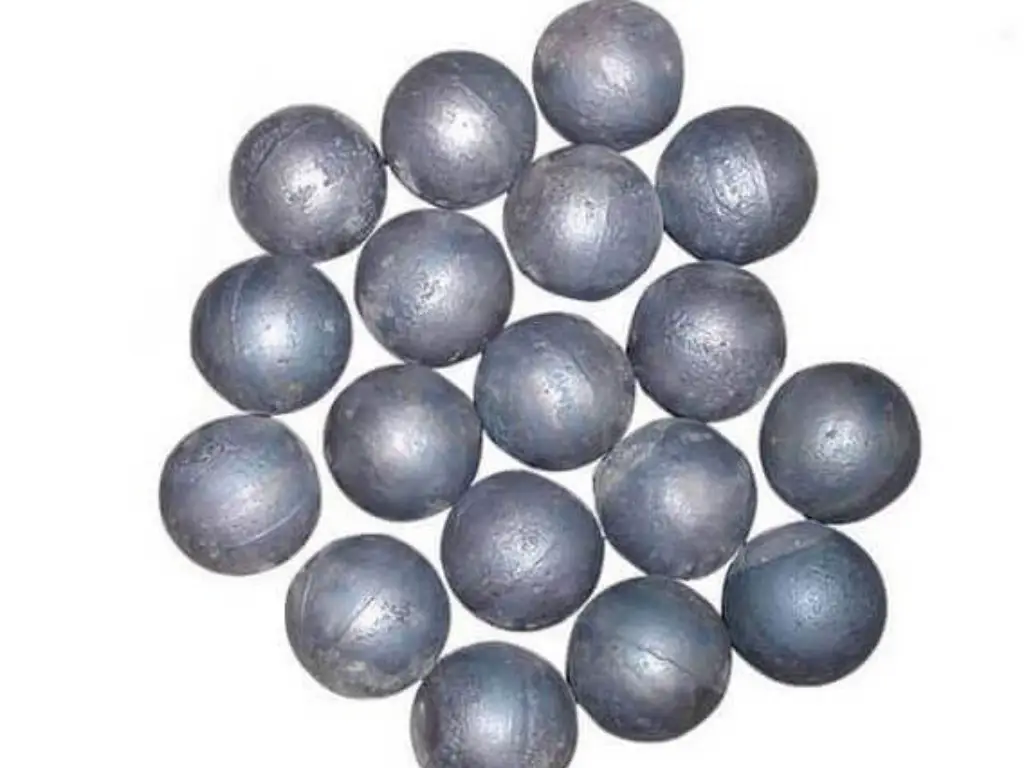
Residence time of the material
The residence time, which is the time period material remains inside the mill, is the main parameter that influences the mill’s efficiency. The longer period of operation allows more interaction between the grinding media and the material, which results in the grinding of the material to finer particles. However, the extended residence time might lead to overgrinding and the reduced capacity as well as extra energy consumption.
Size, density, and number of balls
The grinding efficiency depends on factors such as size, density, and the number of the balls in the mill. The bigger and denser the balls are, the more the energy input will be, and it will lead to quicker grinding. However, employing balls that are way too large might result in a less grind and increased wear of the mill’s inner lining. The number of balls has to be tuned in order to ensure that the balls neither miss the target nor are too dense.
Hardness of balls and material
The selection of the ball mill grinding media hardness, as well as the type of the material being ground, strongly influence the ball mill efficiency. Hardness of the grinding media must be higher than that of the material to be ground for good sizing. Employing balls of the right hardness is the key to regulate mill wear and energy consumption as well as protect the mill’s lining.
Feed rate and feed level
The feed rate, which is the speed at which material is fed into the mill, and feed level, which is the level of material inside the mill, are the two main factors that influence the ball mill’s effectiveness. The feed rate being at the optimum level and under control guarantees that the mill is at its best operation level without being overloaded. The feed level should be kept at around 30-50% of the volume of the ball mill in order to create enough space for the grinding media to move and impact the material.
Rotation speed of the cylinder
As was mentioned above, the rotational speed of the ball mill’s cylinder is a key element in the grinding process efficiency. The mill’s components are subjected to minimum wear as the mill’s speed is optimized to achieve the maximum energy imparted by the grinding media. The optimum speed can vary depending on the mill’s diameter, the size and density of the grinding media, and the material being ground.
Working Process of Ball Mills
Initial stage: particle flattening and shape change
During the initial stage of the grinding process, the particles of the feed material get flattened as well as their shape is changed because of the impact force of the grinding media. This is the stage when most particles of large size are converted into smaller pieces.
Intermediate stage: significant changes compared to the initial stage
The particles are subjected to considerable changes as the grinding process progresses; this is in contrast to the initial stage. The particles get more spherical and uniform in shape, and the rate of size reduction is slower. This stage is brought about by impact and attrition forces, resulting in a finer particle size.
Final stage: particle size reduction and homogeneous microstructure
In the final stage of the grinding process, the particles are reduced to their ultimate size, and a homogenous microstructure is obtained. The particles are now very fine and uniform, with a narrow size distribution. This stage is predominantly made up of attrition forces because the particles are too small to be effectively broken down by impact itself.
Completion stage: extremely deformed metastable structure
The particles have suffered a lot of deformation and have reached a metastable state at the end of the process. This stage is referred to as a high-strain and lattice defects stage in the particles, and it can be associated with enhanced reactivity and unique properties. The last stage is often required in applications such as mechanical alloying where the aim is to obtain unique microstructures and properties of the material.
Advantages of Ball Mills
1. Can deal with difficult materials like hard ores and soft clays.
2. To attain small particle sizes, the milling process can produce particles in the submicron range.
3. This equipment is running continuously, assuring high throughput and low downtimes.
4. The ability to control the final product size by simply adjusting operating parameters is the remarkable feature of this technique.
5. Ensure adequate mixing and homogenization for an evenly dispersed end result.
6. The simple design and minimal maintenance with the worn parts replacement are its advantages.
Disadvantages of Ball Mills
1. High power consumption, with a large amount of heat and noise as the result of energy waste.
2. Milling media and lining materials’ possibility of contamination.
3. The overgrinding risk in the absence of control, which results in undesirable ultrafine particles.
4. Inability to choose to control a single particle size, which leads to a size distribution range.
5. Noisy operation in the crushers, particularly at higher speeds or with larger grinding media.
Conclusion
In closing, the anatomy of an industrial ball mill and its intricate diagram are vital for the optimum performance of the mill and the smooth running of the grinding processes. Through careful assessment of the mill’s working principles, construction, operation, and efficiency determinants, operators and engineers can make well-informed decisions to ensure the maximum grinding efficiency and the output of high-quality products in many fields, such as mining, mineral processing, ceramics, and paints.